Ne nous voilons pas la face : le choix des vannes peut faire ou défaire votre système industriel.
Et lorsqu'il s'agit de contrôler le débit dans les canalisations, les vannes papillon sont de véritables outils de travail. À quoi servent les vannes papillon ? Ces dispositifs de contrôle de débit quart de tour régulent tout, de l'eau potable aux boues chimiques, ce qui en fait l'un des types de vannes les plus polyvalents dans le paysage industriel d'aujourd'hui.
J'ai passé d'innombrables heures à étudier la technologie des vannes (un passe-temps étrange, je sais), et j'ai découvert que la compréhension des applications des vannes peut vous épargner de sérieux maux de tête à l'avenir.
Dans ce guide complet, je vais vous indiquer exactement où les vannes papillon shine, leurs principaux avantages et comment choisir celui qui convient le mieux à vos besoins spécifiques.
Plongeons dans le vif du sujet.
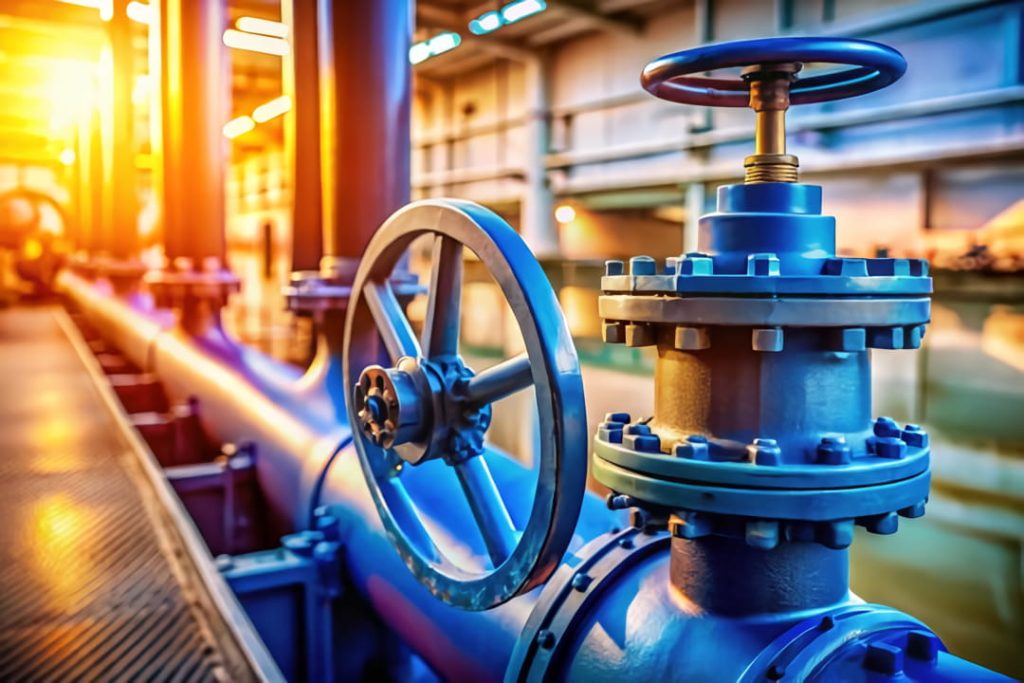
Table des matières
- Qu'est-ce qu'une vanne papillon ?
- Types de vannes papillon à connaître
- À quoi servent les vannes papillon ?
- 1. Systèmes de gestion de l'eau
- 2. CVC et services aux bâtiments
- 3. Industrie du pétrole et du gaz
- 4. Traitement chimique
- 5. Production de denrées alimentaires et de boissons
- 6. Fabrication de produits pharmaceutiques
- 7. Production d'électricité
- 8. Applications marines
- 9. Systèmes de protection contre l'incendie
- 10. Exploitation minière et traitement des boues
- Principaux avantages de l'utilisation des vannes papillon
- Comment choisir la bonne vanne papillon
- Erreurs courantes à éviter lors de l'utilisation de vannes papillon
- Conclusion : À quoi servent les vannes papillon ?
Qu'est-ce qu'une vanne papillon ?
Avant de passer aux applications, examinons rapidement ce qui rend les vannes papillon uniques.
Une vanne papillon est une vanne rotative quart de tour qui utilise un disque (le "papillon") monté sur une tige pour contrôler le débit. Lorsque vous tournez la poignée de 90 degrés, le disque tourne soit parallèlement à l'écoulement (complètement ouvert), soit perpendiculairement à l'écoulement (complètement fermé).
Voici la composition d'une vanne papillon typique :
- Corps de soupape: La structure extérieure qui se connecte à votre tuyauterie
- Disque: La plaque circulaire qui tourne pour contrôler le débit
- Tige: La tige qui transmet la force de rotation au disque
- Siège: La surface d'étanchéité qui assure la fermeture hermétique
- Actionneur: Le mécanisme qui actionne la vanne (poignée, engrenage, électrique ou pneumatique).
Contrairement aux robinets-vannes qui se soulèvent complètement hors de la voie d'écoulement, le disque du robinet à papillon reste dans le flux d'écoulement même lorsqu'il est complètement ouvert. Cela crée une légère perte de charge, mais offre des avantages significatifs en termes d'espace et de poids.
Types de vannes papillon à connaître
Toutes les vannes papillon ne sont pas égales. La conception que vous choisissez a un impact considérable sur les performances, en particulier dans les applications exigeantes.
Vannes papillon concentriques (décalage zéro)
Il s'agit de robinets à papillon d'entrée de gamme dont le disque est centré sur l'axe de la tige. Elles présentent les caractéristiques suivantes
- Sièges en caoutchouc résilient pour une étanchéité positive
- Pression et température nominales inférieures
- Une construction rentable
- Parfait pour les applications générales
Vannes papillon à double excentration (haute performance)
Ces vannes décalent le disque par rapport à l'axe central du tuyau et à l'axe de la tige :
- Réduit l'usure des joints pendant le fonctionnement
- Améliore la capacité d'étanchéité
- Gère des pressions plus élevées (jusqu'à 740 psi)
- Fonctionne à des températures comprises entre -100°F et 500°F
Vannes papillon à triple excentration
Option haut de gamme dans le monde des vannes papillon, ces dernières sont dotées d'un troisième décalage géométrique :
- Crée un mécanisme d'étanchéité métal contre métal
- Élimine les frottements pendant le fonctionnement
- Gère les températures extrêmes (jusqu'à 1000°F)
- Assure une fermeture étanche aux bulles dans les applications critiques
- Gère des pressions allant jusqu'à 1480 psi
Configurations du corps de vanne
Au-delà de la conception interne, les vannes papillon se déclinent en différents styles de corps :
- Style Wafer: Pris en sandwich entre des brides de tuyaux, léger et économique
- Style d'oreille: Les inserts filetés permettent une installation d'un seul côté.
- A brides: Bride intégrée pour des raccordements plus sûrs
- Double bride: Les deux extrémités sont munies de brides pour une stabilité maximale
À quoi servent les vannes papillon ?
Voici maintenant le cœur de ce guide - les domaines dans lesquels les vannes papillon excellent vraiment. J'ai organisé ces applications en fonction de l'industrie et de la fonctionnalité pour vous donner une vue d'ensemble.
1. Systèmes de gestion de l'eau
Les compagnies des eaux apprécient les vannes papillon pour leur fiabilité et leur rentabilité. Elles sont utilisées dans :
- Stations d'épuration municipales: Contrôle du flux entre les étapes de traitement
- Réseaux de distribution d'eau: Isolation sectionnelle dans les grandes canalisations
- Barrages et réservoirs: Régulation des taux de libération de l'eau
- Systèmes d'irrigation: Gestion de la distribution de l'eau aux champs
- Usines de dessalement: Contrôle des flux d'eau de mer et d'eau douce
Par exemple, les vannes papillon de grand diamètre (souvent de 24″ à 96″) contrôlent le débit d'eau dans les conduites principales des villes avec une perte de pression minimale par rapport à d'autres types de vannes.
2. CVC et services aux bâtiments
Grâce à leur conception compacte, les vannes papillon sont idéales pour les salles mécaniques des bâtiments où l'espace est limité :
- Systèmes d'eau réfrigérée: Contrôle du débit vers les serpentins de refroidissement
- Circuits d'eau de chauffage: Régulation de la distribution d'eau chaude
- Boucles d'eau du condenseur: Gestion du débit d'eau de la tour de refroidissement
- Unités de traitement d'air: Contrôle du débit d'air dans les grands conduits
- Isolation des zones: Sectionnement des zones de bâtiments pour l'entretien
La plupart des applications HVAC utilisent des vannes concentriques à siège résilient qui assurent un service fiable avec un minimum de maintenance.
3. Industrie du pétrole et du gaz
Dans les applications pétrolières, les vannes papillon à triple excentration et à haute performance répondent à des conditions exigeantes :
- Raffineries: Contrôle des flux d'hydrocarbures entre les unités de traitement
- Systèmes de canalisations: Isolation des sections pour l'entretien
- Parcs de stockage: Gestion des opérations de transfert de produits
- Plates-formes offshore: Contrôle de divers fluides de processus
- Installations de GNL: Gestion des flux de liquides cryogéniques
L'industrie pétrolière exige des conceptions résistantes au feu qui conservent leur fonctionnalité même en cas de températures extrêmes, ce que les vannes à triple excentration excellent à faire.
4. Traitement chimique
La compatibilité chimique est cruciale dans les applications de traitement :
- Fabrication de produits chimiques: Manipulation d'acides, de bases et de solvants
- Traitement par lots: Diriger les réactifs et les produits
- Exploitation de parcs de stockage: Transfert de produits chimiques entre cuves de stockage
- Traitement des effluents: Contrôle des flux de déchets
- Systèmes d'épuration: Gestion des flux de gaz dans la lutte contre la pollution
Ces applications font souvent appel à des matériaux spécialisés tels que des vannes revêtues de PTFE, de PFA ou d'alliages métalliques exotiques pour résister à la corrosion.
5. Production de denrées alimentaires et de boissons
Les exigences sanitaires déterminent le choix des vannes dans l'industrie alimentaire :
- Transformation laitière: Contrôle des flux de lait et de produits
- Production de boissons: Gestion des ingrédients liquides
- Opérations de brassage: Contrôle du transfert de l'eau, du moût et de la bière
- Systèmes de nettoyage en place (CIP): Orienter les solutions de nettoyage
- Mise en lots des ingrédients: Mesure de quantités précises de liquides
Les vannes papillon de qualité alimentaire présentent des surfaces polies, des élastomères approuvés par la FDA et des conceptions qui empêchent la formation de pièges à bactéries.
6. Fabrication de produits pharmaceutiques
Les applications ultra-pures exigent des conceptions spécialisées :
- Systèmes d'eau pour injection (WFI): Contrôle de l'eau purifiée
- Distribution de vapeur: Gestion des milieux de stérilisation
- Isolation du processus: Séparation des étapes de fabrication
- Des services publics propres: Gestion de la vapeur et des gaz purs
- Formulation par lots: Contrôle de l'ajout d'ingrédients
Les vannes papillon pharmaceutiques présentent souvent des surfaces électropolies et une documentation de validation pour répondre aux exigences réglementaires strictes.
7. Production d'électricité
La fiabilité est primordiale dans les applications de production d'énergie :
- Systèmes d'eau de refroidissement: Contrôle du refroidissement du condenseur
- Eau d'alimentation de la chaudière: Gestion de l'approvisionnement en eau des générateurs de vapeur
- Eau de service: Refroidissement des équipements auxiliaires
- Systèmes de manutention des cendres: Contrôle des flux de boues dans les usines de charbon
- Contrôle des émissions: Gestion des flux de gaz dans les systèmes de lavage
Les centrales électriques utilisent généralement des conceptions robustes à double ou triple excentration, conçues pour un fonctionnement continu et une maintenance minimale.
8. Applications marines
La résistance à la corrosion domine la sélection des vannes pour les applications marines :
- Systèmes de ballastage: La gestion de l'eau de mer pour la stabilité des navires
- Systèmes principaux d'incendie: Distribution d'eau pour la lutte contre les incendies
- Systèmes de refroidissement: Contrôle de l'eau de refroidissement du moteur
- Transfert de marchandises: Chargement et déchargement de cargaisons liquides
- Systèmes de cale: Gestion de la collecte des eaux usées
Les vannes papillon marines sont souvent fabriquées en bronze, en acier inoxydable super-duplex ou en nickel-aluminium-bronze pour résister à la corrosion de l'eau de mer.
9. Systèmes de protection contre l'incendie
La rapidité de réaction est essentielle dans les applications de sécurité :
- Elévateurs principaux: Contrôle de l'alimentation en eau des systèmes d'arrosage
- Contrôle sectionnel: Isoler des parties de grandes installations
- Configurations d'essai et de vidange: Vérification du fonctionnement du système
- Contrôle de la pompe à incendie: Gestion du refoulement de la pompe
- Systèmes de déluge: Contrôler le débit d'eau pour ouvrir les sprinklers
Les vannes papillon homologuées UL/FM offrent la fiabilité nécessaire aux systèmes de sécurité des personnes.
10. Exploitation minière et traitement des boues
La résistance à l'abrasion est essentielle dans ces applications exigeantes :
- Traitement des minéraux: Contrôle des boues de minerai
- Gestion des résidus: Diriger les flux de déchets
- Eau de traitement: Gestion de la recirculation de l'eau
- Circuits de flottation: Contrôle de l'addition de produits chimiques
- Opérations de lixiviation: Gestion des flux de solutions
Les vannes papillon à haute performance avec des composants trempés ou des revêtements spécialisés gèrent ces services abrasifs.
Principaux avantages de l'utilisation des vannes papillon
Maintenant que nous avons vu où elles sont utilisées, voyons pourquoi les vannes papillon sont souvent le meilleur choix :
1. Efficacité spatiale
Les dimensions compactes face à face font des vannes papillon la solution idéale pour les espaces restreints. Par rapport aux robinets-vannes de taille similaire, ils nécessitent généralement :
- 60-80% moins de longueur de face-à-face
- Dégagement vertical considérablement réduit pour le fonctionnement
- Moins de soutien structurel en raison d'un poids plus léger
2. Le rapport coût-efficacité
Les vannes papillon permettent de réaliser des économies substantielles :
- Coût d'achat initial inférieur (souvent 50-60% de moins que les robinets-vannes comparables)
- Frais d'installation réduits grâce à un poids plus léger
- Actionneurs moins coûteux grâce à des exigences de couple plus faibles
- Besoins d'entretien minimes pendant toute la durée de vie du produit
3. Fonctionnement rapide
La conception quart de tour permet :
- Ouverture et fermeture rapides (90° contre plusieurs tours pour les portails)
- Indication visuelle claire de la position (ouvert/fermé)
- Automatisation aisée avec des actionneurs quart de tour
- Capacité de réaction plus rapide en cas d'urgence
4. Excellent contrôle du débit
La plupart des conceptions de vannes papillon fournissent :
- Contrôle proportionnel du débit tout au long de la rotation
- Faible perte de charge en cas d'ouverture complète
- Etranglement stable dans les positions partiellement ouvertes
- Capacités d'étanchéité bidirectionnelle
5. Polyvalence des applications
La large gamme de configurations disponibles permet :
- Gammes de températures allant de la cryogénie à 1000°F+.
- Pression nominale du vide à plus de 1480 psi
- La taille varie de 2″ à 120″+.
- Compatible avec presque tous les supports fluides
Comment choisir la bonne vanne papillon
Permettez-moi de vous présenter un processus simple de sélection de la vanne papillon idéale :
Étape 1 : Définir les conditions de service
Commencez par documenter ces paramètres critiques :
- Type de média (eau, vapeur, produits chimiques, etc.)
- Plage de température (minimum et maximum)
- Pression requise (opérationnelle et maximale)
- Débit et vitesse
- Fréquence de fonctionnement (constante, occasionnelle, d'urgence uniquement)
Étape 2 : Sélectionner le type de dessin ou modèle approprié
En fonction de vos conditions de service :
- Concentrique: Usage général, conditions modérées
- Double compensation: Pression/température plus élevée
- Triple compensation: Conditions extrêmes, exigences en matière de fuite nulle
Étape 3 : Choisir le style de carrosserie
Tenez compte de vos exigences en matière d'installation :
- Tranche: Le plus économique, nécessite du matériel externe
- Patte: Permet un service en cul-de-sac, un renvoi unilatéral
- A brides: Connexion la plus robuste, pression la plus élevée
Étape 4 : Spécifier les matériaux de construction
Faites correspondre les documents à votre demande :
- Corps: Fonte, fonte ductile, acier au carbone, acier inoxydable ou alliages exotiques.
- Disque: Similaire au matériau du corps ou amélioré pour la résistance à l'usure
- Siège: EPDM, NBR, PTFE, métal, en fonction de la compatibilité chimique
- Tige: Généralement en acier inoxydable ou en alliage supérieur
Étape 5 : Sélection de la méthode d'actionnement
En fonction des besoins opérationnels :
- Poignée manuelle: Le plus simple, pour une utilisation accessible et peu fréquente
- Opérateur d'engrenages: Pour les tailles plus importantes nécessitant un couple plus élevé
- Actionneur électrique: Commande à distance, positionnement précis
- Actionneur pneumatique: Fonctionnement rapide, zones à sécurité intrinsèque
- Actionneur hydraulique: Applications à couple élevé
Étape 6 : Prendre en compte les exigences particulières
N'oubliez pas ces facteurs souvent négligés :
- Exigences en matière de certification de la sécurité incendie
- Conformité aux normes sur les émissions fugitives
- Limitations du bruit
- Préoccupations liées aux vibrations
- Indemnités de corrosion
Erreurs courantes à éviter lors de l'utilisation de vannes papillon
Après avoir examiné des centaines de demandes de vannes, j'ai remarqué ces erreurs fréquentes :
1. Ignorer les limites de pression
Les vannes papillon ont des pressions nominales définies qui diminuent avec la taille. Ne pensez pas qu'une vanne de 2″ et une vanne de 24″ de la même série ont des capacités de pression identiques.
2. Inadéquation entre la vanne et l'actionneur
Un actionneur sous-dimensionné ne fournira pas un couple suffisant pour faire fonctionner la vanne, en particulier dans des conditions de haute pression ou d'urgence.
3. Négliger les limites de vitesse
Une vitesse d'écoulement excessive peut provoquer des vibrations du disque, entraînant une usure prématurée du siège ou une défaillance de la tige.
4. Mauvaise position d'installation
L'installation d'une vanne papillon trop près de coudes, de pompes ou d'autres vannes peut créer des turbulences qui endommagent la vanne.
5. Ignorer la compatibilité chimique
Toujours vérifier la compatibilité du matériau du siège avec les fluides du procédé, y compris les produits chimiques de nettoyage susceptibles d'entrer en contact avec la soupape.
Conclusion : À quoi servent les vannes papillon ?
Les vannes papillon ont gagné leur place en tant que composants essentiels des systèmes modernes de contrôle des fluides dans de nombreuses industries. Leur polyvalence, leur rentabilité et leur conception compacte les rendent idéales pour des applications allant de la simple distribution d'eau au traitement chimique complexe.
Récapitulons les points essentiels :
- Les vannes papillon excellent dans les scénarios nécessitant un contrôle efficace du débit dans un espace limité.
- Leur fonctionnement par quart de tour permet un déclenchement rapide pour les systèmes manuels et automatisés.
- Diverses conceptions (concentrique, à double décalage, à triple décalage) permettent d'adapter les performances aux exigences de l'application.
- Les versions spécifiques à l'industrie répondent aux exigences particulières des secteurs alimentaire, pharmaceutique et d'autres secteurs spécialisés.
- Une sélection appropriée nécessite un examen minutieux des conditions de service, des matériaux et des besoins opérationnels.
La prochaine fois que vous évaluerez les options de vannes pour votre système, pensez aux nombreux avantages qu'offrent les vannes papillon. Leur combinaison unique de performance et de valeur en fait souvent le choix optimal pour les applications modernes de contrôle des fluides.
À quoi servent les vannes papillon ? Comme nous l'avons vu, la réponse couvre pratiquement toutes les industries qui font circuler des liquides ou des gaz dans des tuyaux. Avec une sélection et une installation appropriées, ces vannes polyvalentes fourniront des années de service fiable dans vos applications les plus exigeantes.