Ever walked through an industrial facility and wondered how they control all that fluid flowing through those massive pipes?
Here’s the deal: What is a robinet à soupape is one of the most common questions I get from people new to industrial systems. And for good reason.
Globe valves are everywhere. From your local water treatment plant to massive oil refineries, these workhorses are quietly doing their job 24/7.
Mais voilà...
Most people think all valves are created equal. They’re not.
Globe valves have some unique characteristics that make them perfect for certain applications (and terrible for others).
In this guide, I’m going to break down everything you need to know about globe valves. By the end, you’ll understand exactly when to use them, how they work, and why they’re so popular in industrial applications.
Ça vous dit quelque chose ? Entrons dans le vif du sujet.
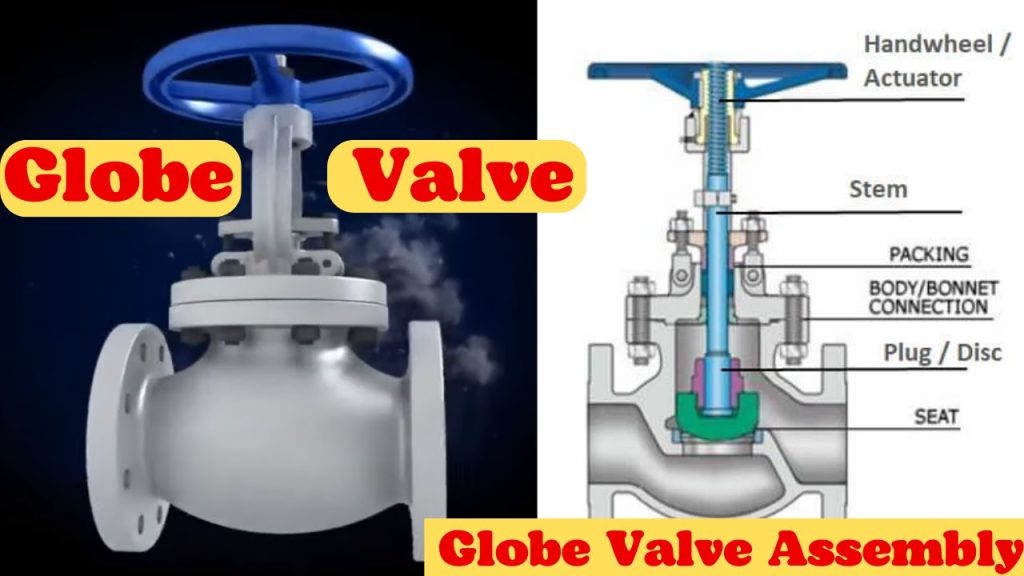
Table des matières
- What is a Globe Valve
- How Globe Valves Actually Work
- Types de robinets à soupape (et quand les utiliser)
- Key Components That Make It Work
- Where You’ll Find Globe Valves in Action
- The Good, The Bad, and The Trade-offs
- Installation and Maintenance Best Practices
- Globe Valve vs. The Competition
- Sizing and Selection Criteria
- Future Trends in Globe Valve Technology
- Conclusion
What is a Globe Valve
A globe valve is a type of industrial valve used to control the flow of fluids (liquids or gases) in a pipeline. Its name comes from its round shape, but many modern globe valves don’t look perfectly round on the outside.
How Globe Valves Actually Work
Let me explain this in simple terms.
A globe valve operates using linear motion. That means the disc (the part that controls flow) moves straight up and down – not sideways like some other valve types.
Here’s what happens inside:
When Opening:
- You turn the handwheel (or actuator kicks in)
- The stem lifts the disc away from the seat
- Fluid starts flowing through the valve
When Closing:
- The disc moves down toward the seat
- Flow area gets smaller and smaller
- Complete closure stops all flow
But here’s where it gets interesting…
Unlike gate valves that lift completely out of the flow path, globe valve discs stay right in the middle of the action. This creates what we call a “tortuous flow path” – basically, the fluid has to change direction multiple times.
Pourquoi cela est-il important ?
This winding path is exactly what gives globe valves their superpower: incredible throttling control.
You can crack open a globe valve just a tiny bit and get precise flow control. Try that with a gate valve and you’ll get unpredictable results (plus you’ll probably damage the valve).
The Internal Flow Pattern
Picture this: fluid enters the valve, hits the internal baffle, gets forced up and around the disc, then changes direction again to exit.
It’s like a NASCAR race with multiple sharp turns instead of a straight highway.
This tortuous path has two major effects:
- Excellent flow control (the good news)
- Higher pressure drop (the trade-off you need to consider)
Types de robinets à soupape (et quand les utiliser)
Not all globe valves are created equal. Here are the main types you’ll encounter:
Z-Type Globe Valves
This is the most common type you’ll see.
The seat is horizontal, and the stem moves perpendicular to the pipeline. Creates that classic Z-shaped flow path I mentioned earlier.
Meilleur pour :
- General throttling applications
- Systems where pressure drop isn’t critical
- Budget-conscious projects (they’re typically the cheapest option)
Y-Type Globe Valves
Here’s where things get interesting.
Y-type valves position the seat and stem at about 45 degrees to the pipe axis. This creates a more streamlined flow path.
Le résultat ?
- 10-15% lower pressure drop compared to Z-type
- Better for high-pressure applications
- Can handle higher flow velocities
Conseil de pro : If you’re dealing with high-pressure steam or other demanding applications, Y-type is usually worth the extra cost.
Robinets à soupape d'équerre
These change the flow direction by 90 degrees.
Instead of needing a separate elbow fitting, the valve does double duty – controlling flow AND changing direction.
Parfait pour :
- Tight spaces where you need to change pipe direction anyway
- Reducing the number of joints (fewer potential leak points)
- Systems with fluctuating flow conditions
Bellows-Sealed Globe Valves
The premium option for demanding applications.
These incorporate a bellows system to prevent any leakage along the stem. Zero tolerance for fugitive emissions.
Essential for:
- Hazardous chemicals
- High-purity pharmaceutical processes
- Nuclear applications
- Anywhere environmental compliance is critical
Key Components That Make It Work
Let me break down the anatomy of a globe valve:
Corps de vanne
The main pressure vessel that houses everything. Usually made from:
- Acier Carbone (most common, good for general service)
- Acier inoxydable (corrosion resistance)
- Fonte (lower pressure, water applications)
- Specialized alloys (extreme conditions)
Disc and Seat Assembly
This is where the magic happens.
Les disque is the movable part that controls flow. The siège is the stationary ring that the disc seals against.
Common disc types:
- Ball discs: General purpose, good sealing
- Needle discs: Ultra-precise control for small lines
- Composition discs: Soft materials for tight shut-off
Stem and Bonnet
Les tige connects your handwheel to the disc. The bonnet is like the lid that keeps everything contained while allowing the stem to move.
Critical point: The packing around the stem is what prevents leakage. This is usually the first thing to wear out, so keep an eye on it.
Where You’ll Find Globe Valves in Action
Globe valves show up everywhere precise flow regulation is needed. Here are the most common applications:
Industrie du pétrole et du gaz
- Pipeline flow control
- Refinery processing units
- Wellhead operations
- Natural gas distribution
The ability to throttle flow makes them perfect for maintaining steady flow rates despite pressure fluctuations.
Production d'électricité
- Systèmes d'eau de refroidissement
- Steam line control
- Feedwater regulation
- Boiler vents and drains
In power plants, you need rock-solid reliability. Globe valves deliver.
Traitement de l'eau
Municipal water plants use globe valves for:
- Flow rate control
- Chemical feed systems
- Backwash operations
- Pressure regulation
Systèmes CVC
Building automation systems rely on globe valves for:
- Chilled water control
- Heating fluid regulation
- Temperature zone control
Le résultat ? Anywhere you need to adjust flow rates frequently, globe valves are usually your best bet.
The Good, The Bad, and The Trade-offs
Let’s be honest about the pros and cons:
Avantages
Excellent Throttling Control
This is the big one. Globe valves can be positioned anywhere from fully closed to fully open with predictable flow characteristics.
Reliable Shut-off
When properly maintained, they provide tight sealing with minimal leakage.
Durable Design
The robust construction handles frequent operation without excessive wear.
Maintenance-Friendly
Many designs allow you to replace the seat and disc without removing the entire valve from the pipeline.
Désavantages
Higher Pressure Drop
That tortuous flow path comes with a price – typically 2-4 times the pressure drop of a gate valve.
Higher Cost
More complex internal design means higher manufacturing costs.
Not Great for Slurries
The internal geometry can trap particles, leading to erosion or sticking.
Slower Operation
Linear motion means more turns to go from closed to open compared to quarter-turn valves.
Installation and Maintenance Best Practices
Here’s what I’ve learned from years of working with these valves:
Installation Tips
Check Flow Direction
Most globe valves are unidirectional. Look for the arrow on the valve body and install accordingly.
Provide Adequate Support
Globe valves are heavier than gate valves. Make sure your piping support can handle the weight.
Leave Access Space
You’ll need room above the valve for maintenance. Don’t install it right under a ceiling or other obstruction.
Maintenance Schedule
Monthly Checks:
- Visual inspection for leaks
- Verify smooth operation
- Check packing condition
Annual Maintenance:
- Lubricate stem threads
- Inspect seat and disc condition
- Replace packing if needed
- Test shut-off performance
Conseil de pro : Keep spare packing material on hand. It’s the most common maintenance item and relatively cheap insurance.
Globe Valve vs. The Competition
Here’s how globe valves stack up against other common valve types:
Robinets à soupape et robinets-vannes
- Gate valves: Better for on/off service, lower pressure drop
- Globe valves: Superior throttling, more frequent operation capability
Robinets à soupape et robinets à tournant sphérique
- Ball valves: Faster operation, lower pressure drop
- Globe valves: Much better flow control precision
Robinets à soupape et robinets à papillon
- Butterfly valves: Lighter, cheaper for large sizes
- Globe valves: Better sealing, more precise control
Le résultat ? Choose based on your primary need: on/off control (gate/ball) or flow regulation (globe).
Sizing and Selection Criteria
Getting the right size globe valve is crucial. Here’s what to consider:
Flow Coefficient (Cv)
This tells you how much water (in GPM) will flow through the valve at a 1 PSI pressure drop.
Rule of thumb: Size for about 70-80% of maximum Cv to allow for future capacity.
Pression et température nominales
Standard pressure classes include:
- 150 PSI (low pressure)
- 300 PSI (medium pressure)
- 600+ PSI (high pressure applications)
Sélection des matériaux
Consider:
- Process fluid compatibility
- Temperature extremes
- Corrosion potential
- Regulatory requirements
Future Trends in Globe Valve Technology
The valve industry is evolving. Here’s what I’m seeing in 2025:
Technologie des vannes intelligentes
More globe valves now come with:
- Built-in position feedback
- Wireless monitoring capabilities
- Predictive maintenance sensors
Matériaux avancés
New alloys and coatings are extending service life in harsh conditions.
Improved Sealing
Better elastomer compounds and metal-to-metal sealing technologies are reducing fugitive emissions.
Conclusion
So qu'est-ce qu'un robinet à soupape?
It’s your go-to solution when you need precise flow control in industrial applications. Sure, they create higher pressure drops than some alternatives, but that tortuous flow path is exactly what gives them their incredible throttling capability.
Here’s my recommendation:
Use globe valves when:
- You need frequent flow adjustments
- Precise control is more important than minimal pressure drop
- Reliable shut-off is critical
- You’re dealing with steam, hot water, or other fluids that benefit from gradual flow changes
Skip them when:
- You just need simple on/off control
- Pressure drop is a major concern
- You’re handling slurries or dirty fluids
- Quick operation is essential
The key is matching the valve type to your specific application needs. Get that right, and globe valves will serve you reliably for decades.