La vanne de coulée est coulée dans la vanne, le niveau de pression général de la vanne de coulée est relativement faible (comme PN16, PN25, PN40, mais il y a aussi une haute pression, peut aller jusqu'à 1500LD, 2500LB), la plupart du calibre est supérieur à DN50. Les vannes de forgeage sont forgées. Ils sont généralement utilisés dans les pipelines de haute qualité. Le calibre est petit et ils sont généralement inférieurs au DN50.
Qu’est-ce que le casting ?
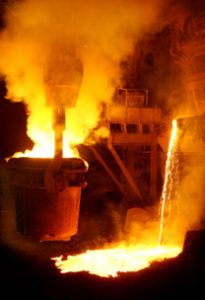
Le cœur du moulage consiste à chauffer le composant métallique jusqu’à l’état fondu et à le verser dans un moule préparé. Bien que le moule soit le plus souvent une matrice, le sable et le moulage à modèle perdu sont souvent utilisés pour des alliages spécifiques ou pour des pièces aux dimensions et à la conception inhabituelles. Une fois le métal refroidi dans la forme de base souhaitée, le métallurgiste termine ensuite la pièce avec les détails demandés par le client, soit à la main, soit par un usinage ultérieur.
Le coût de production par moulage d'ébauches est faible, pour les formes complexes, en particulier avec des pièces à cavité complexes, davantage peut montrer son économie ; En même temps, il présente une grande adaptabilité et de bonnes propriétés mécaniques complètes.
Mais les matériaux nécessaires à la production de pièces moulées (tels que le métal, le bois, le combustible, les matériaux de moulage, etc.) et les équipements (tels que le four métallurgique, le malaxeur de sable, la machine de moulage, la machine de fabrication de noyaux, le shaker, la grenailleuse, la fonte) plaque, etc.) sont plus nombreux et produiront de la poussière, des gaz nocifs et du bruit et pollueront l'environnement.
Histoire du casting
Le moulage est une sorte de technologie de travail à chaud des métaux qui a une histoire d'environ 6 000 ans. En 3200 avant JC, des moulages de grenouilles en bronze sont apparus en Mésopotamie. Entre le 13ème et le 10ème siècle avant JC, la Chine est entrée dans l'apogée des moulages en bronze, le processus a atteint un niveau assez élevé, comme par exemple la dynastie Shang Simuwu carré Ding pesant 875 kg, la dynastie des Royaumes combattants Jinghou Yi Zunpan et la dynastie des Han occidentaux. Les miroirs transparents sont les produits représentatifs de la fonte ancienne. Les premiers moulages ont été fortement influencés par la poterie, et la plupart des moulages étaient des outils ou des ustensiles destinés à la production agricole, à la religion, à la vie et à d'autres aspects, avec une forte couleur artistique. En 513 avant JC, la Chine a produit la première fonte au monde attestée par écrit : la Jin Casting Ding (environ 270 kg). Vers le VIIIe siècle, l’Europe commence à produire de la fonte. Après la révolution industrielle du XVIIIe siècle, la fonderie entre dans une nouvelle période au service des grandes industries. Au 20ème siècle, le développement rapide du moulage a permis de développer la fonte ductile, la fonte malléable, l'acier inoxydable à très faible teneur en carbone et le cuivre aluminium, l'aluminium silicium, l'alliage aluminium magnésium, la base titane, l'alliage base nickel et d'autres matériaux métalliques de coulée, et a inventé un nouveau procédé pour la fonte grise pour réaliser le traitement. Après les années 1950, de nouvelles technologies telles que le moulage à haute pression au sable humide, le moulage au sable à durcissement chimique, la fabrication de noyaux, le moulage à pression négative et d'autres moulages spéciaux et grenaillage ont été introduits.
Types de moulage
Il existe de nombreux types de casting. Selon la méthode de modélisation, il est habituellement divisé en 0 moulage au sable ordinaire, y compris le type de sable humide, le type de sable sec et le sable à durcissement chimique de type 3. (2) moulage spécial, matériaux de moulage par presse et peut être divisé en sable minéral naturel comme le principaux matériaux de moulage spéciaux (par exemple, moulage de précision, moulage en moule, fonderie de moulage en coquille, moulage à pression négative, moulage en moule, moulage en céramique, etc.) et le métal comme matériau principal du moule de moulage spécial (tel que le moulage en moule métallique, coulée sous pression, coulée continue, coulée basse pression, coulée centrifuge, etc.).
Processus de coulée
Le processus de coulée comprend généralement : (la coulée (conteneurs) rend le métal liquide solide, la coulée selon les matériaux peut être divisée en moule en sable, métal, céramique, boue, graphite, etc., peut être divisée en utilisation jetable, semi-permanente et permanente le type et la qualité de la préparation du moule sont les principaux facteurs influençant la qualité de la coulée ; la fusion et le coulage du métal coulé, le métal coulé (alliage de coulée) comprend principalement la fonte, l'acier moulé et les alliages non ferreux moulés (3) le traitement et l'inspection de la coulée ; traitement de coulée, y compris l'élimination des corps étrangers du noyau et de la surface de coulée, l'élimination des colonnes montantes de coulée, les bavures de meulage à la pelle et autres saillies, le traitement thermique, le façonnage, le traitement antirouille et l'usinage grossier de la vanne de pompe d'entrée.
Qu’est-ce que le forgeage ?
Bien que le chauffage du métal composant soit également essentiel au forgeage, le chauffage pour cette méthode n’est jamais assez intense au point de faire fondre ledit métal. Au lieu de cela, il est simplement rendu suffisamment chaud pour permettre au métallurgiste de procéder au forgeage au marteau ou de le manipuler d'une autre manière dans une matrice préparée. Des presses gigantesques sont utilisées pour les produits plus gros et la méthode de forgeage peut varier en fonction du produit final souhaité ; le forgeage peut être un procédé de forgeage à chaud ou à froid, par exemple, ou peut faire appel à une matrice ouverte ou fermée.
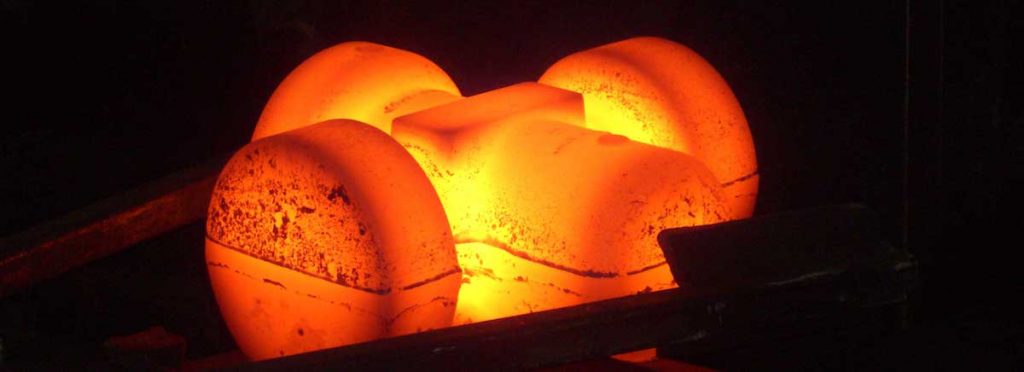
Forgeage : est l'utilisation de machines de forgeage sur la pression des billettes métalliques, la déformation plastique pour obtenir certaines propriétés mécaniques, une certaine forme et taille de la méthode de traitement des pièces forgées.
L'un des deux principaux composants du forgeage. Grâce au forgeage, le métal peut être éliminé sous forme de trous de soudage moulés et les propriétés mécaniques des pièces forgées sont généralement meilleures que celles des pièces moulées du même matériau. Pour les pièces importantes soumises à des charges élevées et à des conditions de travail difficiles dans les machines, les pièces forgées sont principalement utilisées en plus des pièces en tôle, en profilé ou en soudage de forme simple qui peuvent être laminées.
Types de forgeage
Le forgeage selon la méthode de formage peut être divisé en : 0 forgeage ouvert (forgeage libre). L'utilisation de la force ou de la pression pour provoquer une déformation du métal entre les deux blocs supérieur et inférieur (bloc d'enclume) afin d'obtenir les pièces forgées requises, principalement le forgeage manuel et le forgeage mécanique. ② Forgeage en mode fermé. L'ébauche métallique est déformée sous pression dans la chambre de matrice de forgeage d'une certaine forme, et le forgeage peut être divisé en matriçage, forgeage à froid, forgeage rotatif, extrusion, etc. Selon la température de déformation, le forgeage peut être divisé en forgeage à chaud (la température de traitement est supérieure à la température de recristallisation du métal brut), forgeage à chaud (inférieure à la température de recristallisation) et forgeage à froid (température normale).
Le matériau de forgeage est principalement constitué d'une variété de composants d'acier au carbone et d'acier allié, suivis de l'aluminium, du magnésium, du titane, du cuivre et de ses alliages. L'état d'origine du matériau comprend les tiges, les chaînes de coulée, les poudres métalliques et les métaux liquides. Le rapport entre la surface de la section transversale du métal avant déformation et la surface de la section de la matrice après déformation est appelé taux de forgeage. Le choix correct du forgeage plutôt que l'amélioration de la qualité du produit et la réduction des coûts ont une excellente relation.
Processus de forgeage
Le processus de base du forgeage comprend quelques étapes traditionnelles :
- la matière première (blocs d'acier, lingots, billettes) est découpée en morceaux plus petits si nécessaire
- la matière première est chauffée pour atteindre la température de forgeage requise (l'application de chaleur est nécessaire pour rendre la matière ductile et malléable) ; la température de forgeage dépend du type de métal et est obtenue en plaçant le matériau dans un four ;
- le métal chauffé est façonné selon la forme requise en appliquant des forces mécaniques (pression).
- la pièce semi-finie subit un usinage, une finition et un traitement thermique
À la fin du processus, le produit obtenu présente une résistance extrême, une résistance aux chocs et à l'usure grâce à la recristallisation métallurgique et à l'affinement du grain résultant du traitement thermique et mécanique appliqué.
Pourquoi utiliser Castings ?
Le principal avantage du moulage est de créer des composants trop grands, complexes ou inappropriés pour le forgeage. Nous pouvons forger des pièces allant jusqu’à 18 pouces de longueur et pesant jusqu’à 100 livres. Mais si vous avez besoin d’un produit final pesant 5 000 livres, le moulage serait une option plus appropriée. Utilisez donc le casting lorsque :
- Votre rôle est trop important pour être falsifié.
- La pièce est compliquée (contactez-nous pour obtenir des conseils à ce sujet)
- La pièce nécessite l'ajout d'alliages personnalisés
Pourquoi utiliser le forgeage ?
Si votre embout est forgé, il doit l’être. Cela donnera à votre pièce une meilleure résistance, plus de cohérence, une structure de grain plus serrée et une durée de vie plus longue. Contactez nos ingénieurs pour voir si le forgeage convient à votre projet.
Est-ce que Cast ou Forged est meilleur ?
Dans l’ensemble, le casting a tendance à être l’option la moins chère et la plus polyvalente ; le forgeage offre une solidité et une résistance à l’usure supérieures. La question de savoir lequel est le meilleur dépend des principales priorités de votre projet. Si les alliages exotiques et les géométries complexes sont une priorité, le moulage serait probablement la voie à suivre. Cependant, si la résistance et l’intégrité structurelle sont concernées, le forgeage peut être la meilleure option.
Forgé vs Casté
Forgeage | Fonderie | |
Intégrité structurelle | Résistance bien supérieure à celle des pièces moulées. Haut niveau de prévisibilité matérielle | Les produits ont tendance à être plus poreux et plus susceptibles de se briser par rapport aux pièces forgées. |
Tolérance | Peu adapté aux géométries très complexes | Permet un haut niveau de détail. Capable de respecter des tolérances strictes |
Taille du produit | Limité au niveau de la taille et de l'épaisseur du métal (plus gros = plus difficile) | Compatible avec une large gamme de tailles |
Sélection des matériaux | La sélection d'alliages est limitée | Compatible avec presque tous les types de métaux |
Opérations secondaires | Nécessite généralement des opérations secondaires pour affiner et finir le produit selon des spécifications exactes | Fournit un produit primaire qui nécessitera généralement très peu d’opérations secondaires |
Coût | A tendance à être plus rentable pour les séries de production moyennes à grandes | Généralement moins cher que le forgeage, mais cela dépend de la méthode de coulée spécifique utilisée. |
Balises associées :
Dix articles avant et après
Actualités – vanne à bille flottante | Fabricant de vannes industrielles
Actualités – Clapet anti-retour | Fabricant de vannes industrielles
Actualités – Actionneurs électriques et pneumatiques | Fabricant de vannes industrielles
Actualités – Qu'est-ce qu'un robinet à tournant sphérique | Fabricant de vannes industrielles