Haben Sie sich jemals gefragt, was ein Absperrklappe Zecke?
Wenn Sie im industriellen Rohrleitungsbau, in der Heizungs-, Lüftungs- und Klimatechnik oder in der Wasseraufbereitung tätig sind, sind Sie diesen Vierteldrehventilen wahrscheinlich schon überall begegnet. Und das aus gutem Grund.
Komponenten von Absperrklappen arbeiten wie eine gut geölte Maschine zusammen und steuern den Flüssigkeitsstrom mit unglaublicher Effizienz. Aber die Sache ist die: Die meisten Menschen verstehen nicht wirklich, was in diesen scheinbar einfachen Geräten vor sich geht.
Das ändert sich heute.
In diesem Leitfaden werde ich jede einzelne Komponente aufschlüsseln, die Absperrklappen so effektiv macht. Sie werden genau erfahren, wie jedes Teil funktioniert, welche Materialien am besten geeignet sind und warum diese Komponenten für Ihre spezielle Anwendung wichtig sind.
Klingt gut? Tauchen wir ein.
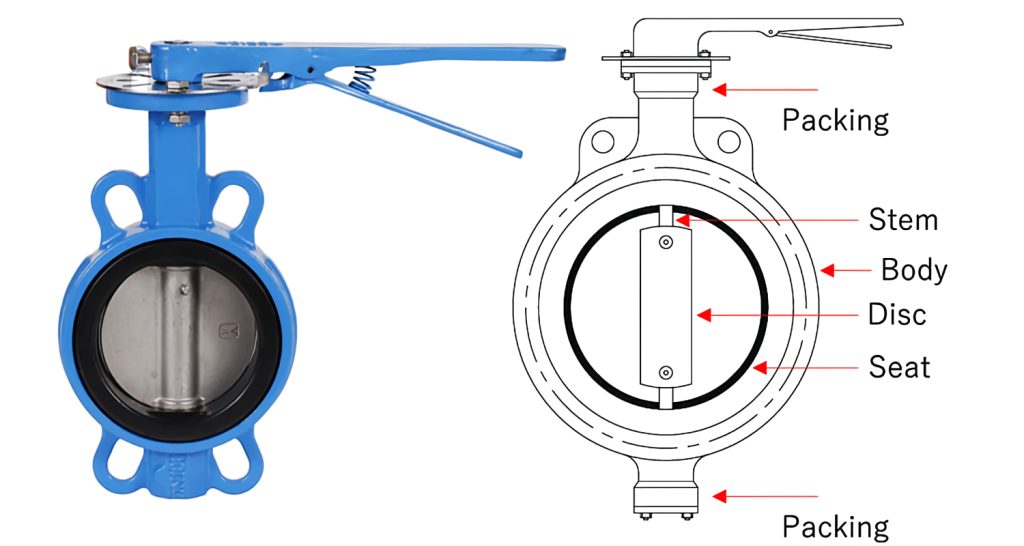
Inhaltsübersicht
- Was sind die Bestandteile von Absperrklappen?
- Analyse der Komponenten von Absperrklappen
- Der Ventilkörper: Das Fundament Ihres Systems
- Die Scheibe: Das Herzstück der Flusskontrolle
- Vorbau-Montage: Das Kraftübertragungssystem
- Sitzsysteme: Wo Dichtung passiert
- Aktuatorische Systeme: Damit alles funktioniert
- Lager und Buchsen: Die unbesungenen Helden
- Dichtungen und O-Ringe: Damit alles dicht bleibt
- Auswahlkriterien, die tatsächlich von Bedeutung sind
- Druck- und Temperaturwerte
- Bewährte Praktiken bei der Installation
- Wartung, die Probleme vermeidet
- Gemeinsame Anwendungen nach Branchen
- Die Quintessenz
Was sind die Bestandteile von Absperrklappen?
So sieht es aus:
Eine Absperrklappe sieht von außen vielleicht einfach aus, ist aber in Wirklichkeit ein ausgeklügeltes Stück Technik, bei dem mehrere wichtige Komponenten harmonisch zusammenarbeiten.
Stellen Sie sich das wie einen Automotor vor. Sie sehen die Motorhaube, aber darunter arbeiten Dutzende von Teilen zusammen, damit alles reibungslos funktioniert.
Zu den wichtigsten Komponenten der Absperrklappe gehören:
- Ventilkörper
- Scheibe (der "Schmetterling")
- Spindel oder Welle
- Sitz und Dichtungssystem
- Lager und Buchsen
- Aktuatorischer Mechanismus
Jede Komponente spielt eine bestimmte Rolle bei der Steuerung des Flüssigkeitsstroms. Wenn Sie ein Detail übersehen, kann Ihr gesamtes System ausfallen.
(Glauben Sie mir, ich habe es selbst erlebt.)
Analyse der Komponenten von Absperrklappen
Der Ventilkörper: Das Fundament Ihres Systems
Das Ventilgehäuse ist der Ausgangspunkt für alles.
Dies ist das Hauptgehäuse, das an Ihr Rohrleitungssystem angeschlossen wird und alle internen Komponenten enthält. Aber nicht alle Ventilgehäuse sind gleich.
Wafer vs. Lug Body Styles
Sie haben hier zwei Möglichkeiten:
Wafer-Style-Gehäuse sind die budgetfreundliche Wahl. Sie sitzen zwischen Rohrflanschen und verwenden lange Bolzen, die durch die gesamte Baugruppe gehen. Perfekt zur Verhinderung des Rückflusses bei Standardanwendungen.
Lug-Style-Körper sind die Premium-Option. Sie verfügen über Gewindeeinsätze, die mit separaten Schraubensätzen direkt an Rohrflansche geschraubt werden können. Das bedeutet, dass Sie eine Seite abnehmen können, ohne die andere zu beeinträchtigen.
Profi-Tipp: Entscheiden Sie sich für die Ösenvariante, wenn Sie in einer Sackgasse arbeiten oder einen einfachen Wartungszugang benötigen.
Materialien für den Körper, die wirklich wichtig sind
Das ist der Punkt, an dem die meisten Menschen etwas falsch machen:
Sie wählen die Materialien nach dem Preis und nicht nach der Leistung aus.
Gängige Ventilkörperwerkstoffe sind:
- Gusseisen: Ideal für einfache Wasseranwendungen
- Sphäroguss: Hervorragendes Verhältnis zwischen Stärke und Gewicht
- Kohlenstoffstahl: Standard für Öl und Gas
- Edelstahl: Ihre Anlaufstelle für korrosive Umgebungen
Die Quintessenz? Stimmen Sie Ihr Material auf Ihre Flüssigkeitseigenschaften, Druck- und Temperaturanforderungen ab. Alles andere würde nur zu Problemen führen.
Die Scheibe: Das Herzstück der Flusskontrolle
Jetzt kommen wir zu den guten Dingen.
Die Scheibe (auch "Schmetterling" genannt) ist das, was den Flüssigkeitsstrom steuert. Wenn sie senkrecht zur Strömung steht, ist sie verschlossen. Wenn sie parallel ist, sind Sie weit offen.
Interessant ist aber Folgendes:
Nicht alle Disc-Designs funktionieren auf die gleiche Weise.
Konzentrische vs. exzentrische Designs
Konzentrische Scheiben bei denen der Schaft durch die Mittellinie verläuft. Einfach, kostengünstig, perfekt für einfache Anwendungen.
Exzentrische Entwürfe sind der Punkt, an dem es spannend wird:
- Doppelt exzentrisch: Zwei Offsets reduzieren den Verschleiß und verbessern die Abdichtung
- Dreifach exzentrisch: Drei Offsets schaffen Metall-auf-Metall-Dichtungen für extreme Bedingungen
Ich persönlich empfehle exzentrische Konstruktionen für Hochleistungsanwendungen. Die Mehrkosten machen sich durch geringeren Wartungsaufwand bezahlt.
Scheibenmaterialien für verschiedene Anwendungen
Die Wahl des Plattenmaterials kann über den Erfolg Ihres Systems entscheiden:
- Edelstahl: Bewältigt korrosive Flüssigkeiten wie ein Champion
- Sphäroguss: Solide Wahl für Wassersysteme
- Kohlenstoffstahl: Standard für den allgemeinen industriellen Gebrauch
- PTFE-ausgekleidet: Perfekt für die chemische Verarbeitung
Vorbau-Montage: Das Kraftübertragungssystem
Der Stiel verbindet Ihre Bandscheibe mit der Außenwelt.
Stellen Sie es sich als das Übertragungssystem vor, das die Drehung des Stellantriebs in die Bewegung der Klappenscheibe umwandelt. Wenn Sie hier etwas falsch machen, wird Ihr Ventil nicht richtig funktionieren.
Einteilige vs. zweiteilige Vorbauten
Einteilige Vorbauten sind die erste Wahl. Einzeln bearbeitete Komponenten, keine Schwachstellen, hervorragende Ausrichtung. Aber wenn etwas kaputt geht, muss man das ganze Ding ersetzen.
Zweiteilige Vorbauten bieten eine einfachere Wartung. Sie können zwar einzelne Abschnitte ersetzen, aber es gibt potenzielle Verbindungspunkte, die ausfallen könnten.
Benetzte vs. nicht-benetzte Konfigurationen
Das ist etwas, was die meisten Leute nicht bedenken:
Benetzte Stängel wenden Sie sich direkt an Ihre Prozessmedien. Sie benötigen Materialien, die für die von Ihnen durchströmten Medien geeignet sind.
Nicht benetzte Stängel Verwendung von Dichtungen, um den Schaft von den Medien zu isolieren. Das ist zwar komplizierter, aber dafür können Sie kostengünstige Materialien verwenden.
Sitzsysteme: Wo Dichtung passiert
Ihr Sitz verhindert ein Auslaufen, wenn das Ventil geschlossen ist.
Und genau hier versagen viele Systeme.
Weiche Sitzmaterialien
Elastomer-Sitze verformen, um eine blasendichte Abdichtung zu erreichen:
- EPDM: Perfekt für Wasseraufbereitungsanwendungen
- NBR: Geeignet für Öl- und Kraftstoffanwendungen
- PTFE: Meister der chemischen Verträglichkeit
Metallsitze für extremen Einsatz
Bei extremen Temperaturen oder abrasiven Medien sind Metallsitze die einzige Option.
Sitze aus rostfreiem Stahl Sie sind feuersicher und halten hohen Temperaturen stand, die Elastomere zerstören würden.
Profi-Tipp: Sparen Sie nicht an den Sitzmaterialien. Ein $50-Sitzfehler kann einen millionenschweren Prozess zum Erliegen bringen.
Aktuatorische Systeme: Damit alles funktioniert
Der Aktuator ist der eigentliche Antrieb des Ventils.
Und Sie haben mehrere Möglichkeiten, jede mit spezifischen Vorteilen.
Manuelle Stellantriebe
Handhebel eignen sich hervorragend für kleinere Ventile. Sie lassen sich schnell bedienen, sicher positionieren und können in jeder Position arretiert werden.
Getriebe bieten Ihnen die Drehmomentvervielfachung, die Sie für größere Ventile benötigen. Die Bedienung ist zeitaufwändiger, aber Sie können viel höhere Drehmomente bewältigen.
Automatische Stellantriebe
Wenn Sie eine Fernsteuerung oder eine automatische Steuerung benötigen:
Elektrische Stellantriebe Verwendung von Motoren mit Endschaltern für präzise Positionierung. Perfekt für abgelegene Standorte.
Pneumatische Antriebe Verwenden Sie Druckluft für einen schnellen Betrieb. Ideal, wenn Sie eine schnelle Notabschaltung benötigen.
Hydraulische Stellantriebe bieten ein gewaltiges Drehmoment für die größten Ventile. Ein Overkill für die meisten Anwendungen.
Lager und Buchsen: Die unbesungenen Helden
Was die meisten Menschen nicht wissen, ist Folgendes:
Ihre Lager und Buchsen ermöglichen einen reibungslosen Betrieb während der gesamten Lebensdauer des Ventils.
Diese Komponenten verringern die Reibung und den Verschleiß während des Betriebs. Sie bestehen oft aus Bronze oder PTFE-Materialien, die für Selbstschmierung sorgen.
Wenn Sie bei der Qualität der Lager sparen, müssen Sie die Ventile ständig erneuern.
Dichtungen und O-Ringe: Damit alles dicht bleibt
Dichtungen verhindern Leckagen an beweglichen Teilen.
PTFE-Dichtungen mit Chemikalien und extremen Temperaturen umgehen.
Gummidichtungen funktionieren gut für normale Wasseranwendungen.
Graphit-Dichtungen sind die erste Wahl für den Einsatz bei hohen Temperaturen.
Der Schlüssel liegt in der Anpassung der Dichtungswerkstoffe an Ihre spezifischen Betriebsbedingungen.
Auswahlkriterien, die tatsächlich von Bedeutung sind
Nun, da Sie die Komponenten kennen, wie wählen Sie die richtige Kombination?
Hier ist mein systematischer Ansatz:
Funktion Anforderungen
Wollen Sie ein- und ausschalten oder drosseln? Drosselungsanwendungen erfordern präzise Durchflusseigenschaften und einen geringen Druckabfall.
Medienkompatibilität
Für ätzende Flüssigkeiten: Komponenten aus rostfreiem Stahl mit PTFE-Dichtungen
Für abrasive Medien: Gehärtete Scheibenmaterialien und Metallsitze
Für hohe Temperaturen: Metallsitze und Graphit Verpackung
Druck- und Temperaturwerte
Passen Sie Ihre Ventilkennwerte an die Systembedingungen an. Dreifach exzentrische Ausführungen bewältigen die extremsten Bedingungen.
Berechnungen des Durchflusskoeffizienten
Berechnen Sie Ihre Cv-Anforderungen, um das Ventil richtig zu dimensionieren. Verwenden Sie die Herstellerangaben, um sicherzustellen, dass Sie die maximalen Durchflussanforderungen erfüllen.
Bewährte Praktiken bei der Installation
Selbst perfekte Komponenten funktionieren nicht, wenn man sie falsch einbaut.
Ich empfehle Folgendes:
- Überprüfung der Spezifikationen gegen Systemanforderungen
- Alle Oberflächen reinigen zur Vermeidung von Trümmerschäden
- Flanschausrichtung prüfen (Fehlausrichtung verursacht Bandscheibenbindung)
- Stützen Sie das Ventil die Belastung der Rohrleitungen zu verringern
- Schrauben schrittweise anziehen in der richtigen Reihenfolge
Profi-Tipp: Ziehen Sie das Ventil vor dem endgültigen Festziehen immer wieder an, um einen reibungslosen Betrieb zu gewährleisten.
Wartung, die Probleme vermeidet
Regelmäßige Wartung verlängert die Lebensdauer der Komponenten und verhindert teure Ausfälle.
Monatliche Aufgaben:
- Schalten Sie das Ventil aus, wenn es nicht regelmäßig benutzt wird.
- Kontrolle auf externe Leckagen
- Prüfen Sie den Betrieb des Stellantriebs
Jährliche Aufgaben:
- Spindeldichtungen und Scheibe schmieren
- Sitze auf Verschleiß prüfen
- Zustand der Lager prüfen
Wann müssen Komponenten ersetzt werden?
- Sitzleckage außerhalb der zulässigen Grenzen
- Leckage der Spindeldichtung
- Bindung während des Betriebs
Gemeinsame Anwendungen nach Branchen
Unterschiedliche Branchen setzen unterschiedliche Komponenten voraus:
Wasserversorgung legt den Schwerpunkt auf Korrosionsbeständigkeit und NSF-Konformität.
Chemische Verarbeitung verlangt Materialverträglichkeit und brandsichere Konstruktionen.
Öl und Gas erfordert hohe Druckfähigkeit und zuverlässige Abdichtung.
HVAC-Systeme betonen den schnellen Betrieb und den geringen Druckabfall.
Die Quintessenz
Verstehen Komponenten von Absperrklappen ist nicht nur technisches Wissen - es ist der Schlüssel zur Auswahl, Installation und Wartung von Systemen, die tatsächlich funktionieren.
Das müssen Sie sich merken:
- Abstimmung der Materialien auf Ihre spezifische Anwendung
- Knausern Sie nicht bei kritischen Komponenten wie Sitzen und Lagern
- Eine ordnungsgemäße Installation verhindert die meisten Betriebsprobleme
- Regelmäßige Wartung verlängert die Lebensdauer der Komponenten drastisch
Die Ventilindustrie entwickelt sich ständig weiter, wobei neue Materialien und Konstruktionen die Leistung jedes Jahr verbessern. Aber die Grundlagen, die ich hier behandelt habe, bleiben konstant.
Wenn Sie verstehen, wie Komponenten von Absperrklappen zusammenarbeiten, können Sie fundierte Entscheidungen treffen, die Geld sparen und Ausfallzeiten verhindern.
Das ist der Unterschied zwischen der Hoffnung, dass Ihr System funktioniert, und dem Wissen, dass es funktioniert.