Elegir la válvula adecuada para su sistema de tuberías puede suponer una gran diferencia en cuanto a rendimiento, costes de mantenimiento y fiabilidad general. Pero, como he descubierto trabajando con varias empresas de ingeniería, la mayoría de la gente tiene dificultades para elegir entre dos tipos de válvulas muy populares: las válvulas de bola y las válvulas de compuerta.
Hoy voy a desglosar exactamente cuál es la diferencia entre válvula de bola y válvula de compuerta diseños, funcionamiento y mejores aplicaciones.
Que quede claro: no se trata sólo de conocimientos teóricos. He consultado a ingenieros industriales que toman estas decisiones a diario, y voy a compartir el marco exacto que utilizan para tomar siempre la decisión correcta.
¿Está preparado para convertirse en un experto en selección de válvulas? Sumerjámonos en el tema.
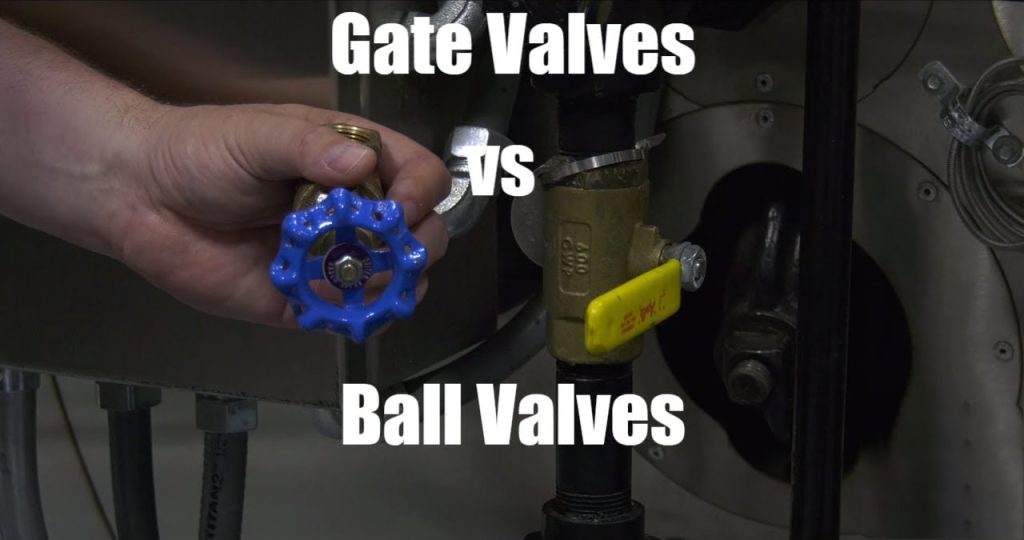
Índice
- Diferencia entre válvula de bola y válvula de compuerta
- La elección correcta para su sistema
- Tendencias del sector y evolución futura
- Conclusión: Tomar la decisión final
Diferencia entre válvula de bola y válvula de compuerta
Las diferencias fundamentales de diseño
En lo que respecta al diseño de las válvulas, las de bola y las de compuerta no podrían ser más diferentes. Estas diferencias fundamentales afectan a todo, desde su vida útil hasta sus aplicaciones.
Explicación del diseño de las válvulas de bola
Las válvulas de bola tienen un diseño bastante ingenioso:
- Una bola esférica con un orificio (puerto) en el centro
- Un vástago conectado a la bola para su rotación
- Asientos que crean juntas alrededor del balón
- Una manivela o actuador que sólo requiere un cuarto de vuelta
La magia reside en su funcionamiento: la bola gira dentro del cuerpo de la válvula y sólo necesita 90 grados de rotación para pasar de totalmente abierta a totalmente cerrada. Esta rápida acción convierte a las válvulas de bola en las campeonas absolutas en situaciones de cierre de emergencia.
Piénsalo así: cuando necesitas detener el flujo inmediatamente, ¿prefieres dar un cuarto de vuelta rápido o hacer girar la rueda varias veces?
Construcción de válvulas de compuerta
Las válvulas de compuerta funcionan según un principio completamente distinto:
- Una compuerta plana o en forma de cuña (disco) que se mueve perpendicularmente al flujo
- Un vástago roscado que convierte la rotación en movimiento lineal
- Un volante que requiere varias vueltas para funcionar
- Un bonete que aloja el conjunto del vástago
- Los asientos del cuerpo crean juntas contra la compuerta
A diferencia del rápido cuarto de vuelta de las válvulas de bola, las válvulas de compuerta requieren múltiples rotaciones del volante para abrirse o cerrarse completamente. Este funcionamiento gradual ayuda a reducir los golpes de ariete en sistemas de gran caudal, pero es definitivamente más lento en situaciones de emergencia.
Diferencias operativas que importan
Hablemos ahora de cómo se traducen estas diferencias de diseño en el rendimiento en el mundo real.
Funcionamiento de las válvulas de bola
He aquí lo que hace especiales a las válvulas de bola en funcionamiento:
- Velocidad: El funcionamiento rápido de un cuarto de vuelta permite el cierre instantáneo
- Estanqueidad: El diseño crea un sellado excelente incluso después de años de uso
- Control de flujo: Aunque están destinadas principalmente al servicio de encendido/apagado, las válvulas de bola especializadas pueden proporcionar cierta estrangulación
- Durabilidad: Menos piezas móviles significa menos puntos de fallo
- Eficiencia espacial: Diseño compacto para espacios reducidos
He visto plantas de fabricación que han optado por las válvulas de bola para aplicaciones sin estrangulamiento por su fiabilidad y rapidez de funcionamiento. Cuando cada segundo cuenta durante una parada de emergencia, ese cuarto de vuelta puede salvar literalmente el equipo y evitar desastres.
Funcionamiento de las válvulas de compuerta
Las válvulas de compuerta funcionan de forma diferente en varios aspectos clave:
- Funcionamiento gradual: Los giros múltiples evitan los cambios bruscos de presión
- Flujo sin obstáculos: Cuando está completamente abierto, la restricción de caudal es mínima.
- Movimiento lineal: La compuerta se levanta completamente fuera del paso del caudal
- Espacio necesario: Necesita más holgura debido a la extensión del vástago cuando está abierto
- Limitaciones de estrangulamiento: No es ideal para el estrangulamiento (posiciones parcialmente abiertas)
Una planta de procesamiento químico con la que trabajé utilizaba específicamente válvulas de compuerta para sus líneas de proceso principales, ya que el paso de caudal sin obstrucciones era fundamental para sus materiales de alta viscosidad.
Comparación de rendimiento: ¿Qué válvula gana?
Comparemos estos tipos de válvulas directamente en las métricas de rendimiento más importantes.
Capacidad de estanqueidad y fuga
Las válvulas de bola suelen ofrecer una estanqueidad superior a la de las válvulas de compuerta. ¿Por qué? El diseño permite una compresión constante del asiento contra la bola, creando un cierre hermético incluso después de miles de ciclos.
Las válvulas de compuerta pueden desarrollar vías de fuga con mayor facilidad a medida que la compuerta y los asientos se desgastan con el tiempo. La acción de deslizamiento acaba creando patrones de desgaste desiguales que comprometen la estanqueidad.
Características del flujo
Aquí es donde las cosas se ponen interesantes:
- Válvulas de compuerta: Proporcionan un flujo laminar sin obstrucciones cuando están totalmente abiertos - ideal para lodos y fluidos viscosos.
- Válvulas de bola: Crean una ligera turbulencia alrededor de la bola, pero los diseños estándar de puerto completo minimizan esto.
Para aplicaciones en las que es fundamental evitar la caída de presión, una válvula de compuerta totalmente abierta aventaja ligeramente a las válvulas de bola. Sin embargo, los avances en el diseño de válvulas de bola de paso total han eliminado en gran medida esta ventaja, excepto en las aplicaciones más sensibles.
Manipulación de presión y temperatura
Ambos tipos de válvulas pueden soportar una amplia gama de presiones y temperaturas, pero su rendimiento difiere:
- Válvulas de bola: Excelentes en aplicaciones de presión/temperatura moderadas, especialmente con asientos blandos.
- Válvulas de compuerta: A menudo se prefieren para aplicaciones a temperaturas extremas en las que se requiere un asiento metal-metal.
He visto sistemas de vapor de alta temperatura que utilizan válvulas de compuerta especializadas específicamente porque los componentes de asiento metálicos mantienen la integridad a temperaturas que dañarían los materiales de asiento de las válvulas de bola estándar.
Consideraciones específicas de la aplicación
La industria de las válvulas no es de talla única. Las distintas aplicaciones exigen diferentes características de las válvulas.
Cuando las válvulas de bola brillan más
Elija válvulas de bola cuando:
- El funcionamiento rápido es esencial (cierre de emergencia)
- La estanqueidad es fundamental
- Plazas limitadas
- Se requiere ciclismo frecuente
- Se prevé la automatización (requiere menos par)
- El medio es limpio o moderadamente abrasivo
Hace poco trabajé con una empresa farmacéutica que cambió totalmente a válvulas de bola para sus sistemas de vapor limpio porque la reducción de hendiduras y las excelentes propiedades de sellado respaldaban sus requisitos sanitarios.
Cuando las válvulas de compuerta son la mejor opción
Las válvulas de compuerta siguen siendo la opción preferida cuando:
- Es necesario un funcionamiento gradual para evitar el golpe de ariete
- Se requiere un flujo absolutamente sin obstrucciones
- El sistema requiere tuberías de gran diámetro
- Se transportan lodos o fluidos muy viscosos.
- Las temperaturas extremas superan los materiales de los asientos de las válvulas de bola
Los sistemas municipales de abastecimiento de agua siguen utilizando predominantemente válvulas de compuerta para las líneas principales de transmisión debido a sus características de flujo sin obstrucciones y a su fiabilidad en grandes diámetros.
Tamaño y espacio necesarios
Las dimensiones físicas de estas válvulas pueden marcar la diferencia en el diseño de sus tuberías.
Válvula de bola Huella
Las válvulas de bola ofrecen un diseño compacto con:
- Espacio lateral mínimo necesario para la rotación de la empuñadura
- Dimensiones frontales reducidas en comparación con las válvulas de compuerta equivalentes
- No se necesita espacio para prolongar el vástago
Este tamaño compacto hace que las válvulas de bola sean ideales para salas de equipos abarrotadas y sistemas de patines modulares en los que el espacio es escaso.
Válvula de compuerta Espacio necesario
Las válvulas de compuerta requieren más espacio de instalación:
- Espacio vertical considerable para la extensión del vástago cuando está abierto
- Más espacio operativo para la rotación del volante
- Mayores dimensiones del cara a cara en muchos casos
He visto proyectos de modernización en los que la sustitución de válvulas de compuerta por válvulas de bola ha resuelto problemas de espacio que limitaban el acceso y el mantenimiento.
Análisis de costes: Gasto inicial frente a gasto vitalicio
Hablemos de dinero: tanto los costes iniciales como a largo plazo son importantes.
Comparación de la inversión inicial
En general:
- Las válvulas de bola suelen costar inicialmente 10-30% más que las válvulas de compuerta equivalentes
- Esta diferencia de precio se reduce a medida que aumenta el tamaño
- Los costes de automatización suelen ser inferiores en el caso de las válvulas de bola
Costes de mantenimiento y vida útil
La verdadera comparación de costes procede del ciclo de vida total:
- Las válvulas de bola suelen requerir menos mantenimiento
- Las válvulas de compuerta suelen necesitar un ajuste de la empaquetadura del vástago y, en su caso, un reacondicionamiento del asiento.
- Las piezas de reparación de las válvulas de bola suelen ser más sencillas y menos numerosas
- Los costes de mano de obra para el mantenimiento suelen ser más elevados en el caso de las válvulas de compuerta
Una planta industrial con la que trabajé calculó un ahorro de 40% a lo largo de su vida útil tras cambiar las válvulas de compuerta por las de bola, a pesar de la mayor inversión inicial.
Compatibilidad de automatización
Los sistemas industriales modernos dependen cada vez más del accionamiento automatizado de válvulas.
Automatización de válvulas de bola
Las válvulas de bola favorecen la automatización porque:
- El cuarto de vuelta requiere actuadores menos potentes
- Los requisitos de par son coherentes y predecibles
- Los indicadores de posición son más sencillos (sólo 0° y 90°)
- Las opciones a prueba de fallos son más fáciles de aplicar
Automatización de válvulas de compuerta
La automatización de válvulas de compuerta presenta más retos:
- El funcionamiento multivuelta requiere actuadores más complejos
- Los mayores requisitos de par aumentan los costes de los actuadores
- La información sobre la posición es más complicada
- La lubricación del vástago se vuelve más crítica
La industria petroquímica ha ido migrando hacia las válvulas de bola automatizadas en aplicaciones sin estrangulamiento precisamente por estas ventajas de automatización.
La elección correcta para su sistema
Este es mi marco de selección entre válvulas de bola y de compuerta:
- Definir los requisitos críticos: Velocidad, estanqueidad, características del caudal
- Evaluar las limitaciones de espacio: Espacio libre disponible para el funcionamiento y el mantenimiento
- Tenga en cuenta las propiedades de los medios de comunicación: Viscosidad, abrasividad, temperatura
- Analizar la frecuencia de funcionamiento: Frecuencia de ciclo de la válvula
- Calcular los costes de por vida: Compra inicial más mantenimiento previsto
- Evaluar las necesidades de automatización: Requisitos de control actuales o futuros
- Compruebe las normas del sector: Algunas aplicaciones tienen requisitos específicos
Este enfoque sistemático le permitirá elegir la válvula óptima para su aplicación específica.
Tendencias del sector y evolución futura
El sector de las válvulas sigue evolucionando, con varias tendencias notables:
- Mayor adopción de válvulas de bola en aplicaciones tradicionales de válvulas de compuerta
- Desarrollo de asientos de válvulas de bola de alto rendimiento para temperaturas extremas
- Introducción de tecnologías de válvulas "inteligentes" para la supervisión de su estado
- Creciente énfasis en la reducción de las emisiones fugitivas en los diseños de válvulas
Para 2025, las previsiones del sector sugieren que las válvulas de bola seguirán ganando cuota de mercado, mientras que las válvulas de compuerta especializadas mantendrán su posición en aplicaciones específicas en las que sus ventajas de diseño son insustituibles.
Conclusión: Tomar la decisión final
A la hora de decidir ¿cuál es la diferencia entre válvula de bola y válvula de compuerta? diseños para su aplicación específica, recuerde que ambos tipos de válvulas tienen su lugar en los sistemas de tuberías modernos.
Las válvulas de bola destacan en aplicaciones que requieren un funcionamiento rápido, estanqueidad y ciclos frecuentes. Su diseño de cuarto de vuelta las hace ideales para el cierre de emergencia y la automatización.
Las válvulas de compuerta siguen siendo valiosas para aplicaciones que requieren un caudal sin obstrucciones, un funcionamiento gradual y un rendimiento en condiciones extremas o tamaños muy grandes.
La clave está en adaptar las características de las válvulas a sus necesidades específicas en lugar de aplicar un enfoque único.
Ahora que entiende exactamente ¿cuál es la diferencia entre válvula de bola y válvula de compuerta? estará preparado para seleccionar válvulas más inteligentes que optimizarán el rendimiento, la fiabilidad y los costes de mantenimiento de su sistema.