A válvula de compuerta es un tipo de válvula que se utiliza para iniciar y detener el flujo de fluidos en tuberías y sistemas de conducción. Esta versátil válvula funciona como una compuerta, cerrándose para detener el flujo y abriéndose para permitirlo.
Pero, ¿qué son exactamente las válvulas de compuerta? ¿Cómo funcionan? ¿Y por qué son una de las válvulas más omnipresentes en diversos sectores?
Esta completa guía sobre válvulas de compuerta responderá a todas esas preguntas y a muchas más. Al final, conocerá a fondo los tipos de válvulas de compuerta, sus componentes, diseño, funcionamiento, aplicaciones y ventajas.
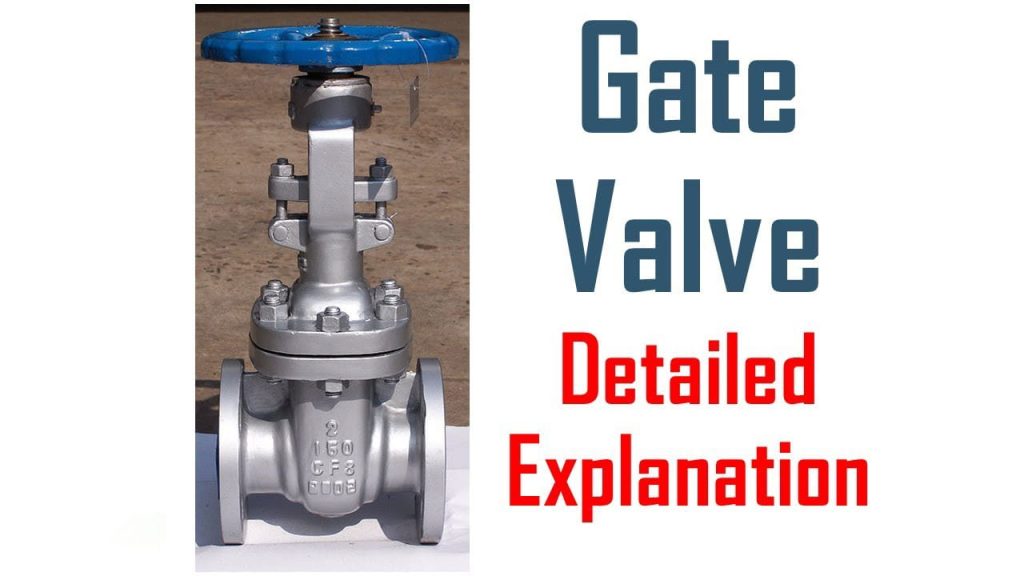
Índice
- ¿Qué es una válvula de compuerta?
- ¿Cómo funciona una válvula de compuerta?
- Tipos de diseño de válvulas de compuerta
- Partes principales de una válvula de compuerta
- ¿Por qué utilizar válvulas de compuerta? Ventajas y aplicaciones
- Ventajas de las válvulas de compuerta
- Desventajas de las válvulas de compuerta
- Indicadores de posición de válvulas de compuerta
- Consideraciones clave al seleccionar válvulas de compuerta
- Dimensionamiento de válvulas de compuerta
- Posición de instalación
- Configuraciones
- Conclusión
¿Qué es una válvula de compuerta?
Una válvula de compuerta es una válvula de movimiento lineal diseñada para iniciar y detener el flujo de fluidos. Se denomina válvula de compuerta porque utiliza una barrera plana en forma de compuerta que se eleva hacia dentro y hacia fuera de la corriente de flujo para cerrar o permitir el paso.
Las válvulas de compuerta se utilizan principalmente como válvulas de aislamiento o válvulas on-off en tuberías para conseguirlo:
- Corte total del flujo durante el mantenimiento
- Procedimientos de desvío de flujos
- Regulación del caudal en ramales
A diferencia de las válvulas de globo y las válvulas de bola, las válvulas de compuerta no están diseñadas para estrangular o funcionar con frecuencia. La ausencia de restricción de caudal permite el flujo total con poca caída de presión.
Entonces en resumen:
Una válvula de compuerta se utiliza para aislar secciones de un sistema de tuberías deteniendo o abriendo completamente el paso del caudal. El nombre proviene del disco en forma de compuerta que se abre/cierra contra los asientos para controlar el caudal.
Entremos ahora en los intrincados detalles del diseño de las válvulas de compuerta, su mecanismo de funcionamiento y sus aplicaciones.
¿Cómo funciona una válvula de compuerta?
Todas las válvulas de compuerta tienen el mismo mecanismo, sencillo pero eficaz, que consiste en:
- Cuerpo de la válvula
- Capó
- Puerta/borde
- Precinto de embalaje
- Vástago de válvula
El propósito principal de todos estos componentes es bajar y levantar con precisión la compuerta/borde contra los asientos para un cierre positivo.
Cuando la válvula está abierta, la compuerta/cuña se levanta completamente, permitiendo el paso sin restricciones del flujo a través de la válvula. Al cerrar la válvula, la cuña desciende sobre el asiento, bloqueando el flujo en minutos.
El vástago de la válvula conecta la compuerta y el volante. Girando la maneta se gira el vástago, levantando la compuerta del asiento o bajándola sobre la superficie de asiento. El control direccional del fluido la hace adecuada para aislar el flujo en cualquier dirección.
Ahora que ya sabe qué aspecto tiene una válvula de compuerta y cómo controla el caudal, vamos a entrar en algunos fundamentos y terminología clave del diseño de válvulas de compuerta.
Tipos de diseño de válvulas de compuerta
Las válvulas de compuerta vienen en diferentes diseños basados en la orientación de la cuña y el asiento. Los diseños más comunes incluyen:
Válvulas de compuerta corredera paralela
En las válvulas de compuerta de corredera paralela, la compuerta/cuña tiene caras planas y paralelas que encajan entre dos asientos paralelos. No hay efecto cuña en los asientos. Estas válvulas son compactas y, por lo general, se prefieren para manipular lodos.
Las válvulas de compuerta de corredera paralela son las más adecuadas para regular el caudal de medios abrasivos, ya que la compuerta/los asientos son autolimpiantes. Su inconveniente es la elevada turbulencia del fluido que provoca el desgaste del asiento.
Válvulas de compuerta de cuña
Las válvulas de compuerta en cuña son el tipo más común que utiliza una compuerta en forma de cuña. La compuerta cónica encaja con los asientos inclinados para conseguir un cierre hermético incluso a altas presiones.
En función de la flexibilidad de la cuña, las válvulas de compuerta de cuña tienen subtipos:
Válvulas de cuña maciza tienen una compuerta sólida sin piezas móviles. La robusta cuña de una sola pieza proporciona un cierre hermético.
Válvulas de cuña flexibles tienen una compuerta con material flexible alrededor de los orificios del vástago para adaptarse a los asientos. Esta capacidad de autoajuste evita los atascos.
Válvulas de cuña dividida incorporan una compuerta de dos piezas con un muelle entre las caras. La acción independiente asienta ambas piezas de la compuerta uniformemente para un cierre hermético fiable.
Las válvulas de compuerta de cuña ofrecen un cierre bidireccional adecuado incluso para aplicaciones de alta presión. El efecto cuña en los asientos permite un control del fluido de alta resistencia.
Partes principales de una válvula de compuerta
Como se ve en el diagrama anterior, una válvula de compuerta consta de:
Cuerpo de la válvula
El cuerpo constituye la estructura básica que mantiene unidas todas las piezas. Los cuerpos estándar de las válvulas de compuerta se ajustan a la norma MSS SP-70 y están hechos de materiales como bronce, hierro fundido, hierro dúctil o acero.
Los cuerpos de las válvulas de compuerta tienen extremos embridados o roscados para conectar las tuberías. Pueden estar revestidos interna y externamente para evitar la corrosión.
Bonete de válvula
El bonete es la sección superior unida al cuerpo de la válvula mediante pernos. Sujeta la empaquetadura y permite el acceso a las piezas internas para su reparación.
Según su construcción, las válvulas de compuerta tienen:
- Capó atornillado
- Bonete de cierre a presión
- Capó atornillado
- Capó de la Unión
Los capós atornillados son preferibles para las válvulas grandes utilizadas en aplicaciones de alta presión.
Compuerta de válvula/cuña
La compuerta/borde es el elemento de cierre que proporciona el control real del caudal. En su posición cerrada, la compuerta presiona contra los asientos para conseguir un cierre hermético.
Las válvulas de compuerta tienen:
- Puerta de cara paralela
- Cuña cónica sólida
- Cuña partida
Los materiales de las compuertas incluyen latón, acero inoxidable o aleaciones de fundición adecuadas para aplicaciones concretas.
Asiento de válvula
El asiento se refiere a la superficie interior del cuerpo contra la que presiona la compuerta para un cierre positivo. Las válvulas de compuerta tienen asientos roscados o fundidos integrales.
Basándose en la resistencia, las válvulas de compuerta tienen:
- Asientos metálicos: Aquí una cuña de compuerta presiona contra los asientos del cuerpo, generalmente de bronce o acero inoxidable.
- Asientos elásticos: Tienen los asientos del cuerpo recubiertos de elastómeros como el caucho de nitrilo. El revestimiento de caucho permite un cierre hermético al tiempo que permite el paso de pequeños sólidos a través de la válvula parcialmente abierta.
Las válvulas de compuerta de asiento elástico suelen preferirse por su excepcional cierre estanco.
Vástago de válvula
El vástago de la válvula conecta el volante o actuador con la compuerta. En función del movimiento del vástago, las válvulas de compuerta son:
Vástago ascendente: El vástago está unido a la compuerta y se eleva fuera del bonete a medida que la válvula se abre. Los vástagos ascendentes tienen indicadores de posición.
Vástago no ascendente: El vástago está fijado al accionamiento. Hace que la puerta/borde suba o baje sin ningún movimiento del vástago. Los vástagos no ascendentes son compactos.
Embalaje
La empaquetadura es la junta que impide la fuga de fluido por donde el vástago entra en el bonete. La empaquetadura de la válvula contiene materiales elásticos que permiten un funcionamiento suave del vástago.
¿Por qué utilizar válvulas de compuerta? Ventajas y aplicaciones
Las válvulas de compuerta proporcionan un control fiable de encendido/apagado adecuado para diversas aplicaciones industriales, especialmente tuberías.
Líneas de agua: Las válvulas de compuerta tienen largos ciclos de vida útil cuando se utilizan para aislar tuberías de agua municipales/industriales para su mantenimiento.
Plantas de proceso: Las válvulas de compuerta aíslan recipientes, equipos o ramales del colector principal en las plantas de proceso.
Líneas de vapor: Las válvulas de compuerta de cuña elástica permiten un control eficaz de encendido/apagado en líneas de vapor a alta temperatura.
Líneas químicas: La estanqueidad bidireccional y los revestimientos resistentes a la corrosión hacen que las válvulas de compuerta sean ideales para líneas de productos químicos corrosivos.
Prevención de incendios: Las válvulas de compuerta se integran fácilmente con los sistemas de rociadores/drenaje para la protección contra incendios.
Líneas de petróleo: Las refinerías de petróleo dependen de las válvulas de compuerta de acero al carbono de alta resistencia para bloquear las tuberías de petróleo de gran diámetro para su limpieza.
Líneas de aguas residuales: Los servicios públicos utilizan válvulas de compuerta de vástago no ascendente subterráneas dispuestas en fosos de hormigón para acceder a las tuberías de aguas residuales.
Líneas ramificadas: Las compuertas compactas no ascendentes regulan cómodamente el caudal en ramales de tuberías y líneas de proceso más pequeñas.
Líneas de servicio enterradas: Válvulas de compuerta anticorrosión aptas para accesos subterráneos enterrados que evitan las excavaciones.
Vaciado del depósito: Las rápidas válvulas de compuerta de paso total vacían rápidamente grandes depósitos en zanjas de drenaje.
En esencia, válvulas de compuerta fiables:
- Detienen el flujo de fluidos, incluidas las aguas residuales, los productos químicos y el petróleo
- Separación de equipos, bombas y secciones de recipientes de las líneas principales
- Permiten el acceso a las tuberías cuando es necesario minimizando las perturbaciones del flujo
- Drenaje de medios de depósitos, balsas o puntos bajos de las tuberías
Ventajas de las válvulas de compuerta
Las válvulas de compuerta tienen ventajas inherentes que las convierten en un elemento de control de caudal muy conveniente:
1. Sellado bidireccional
Las válvulas de compuerta aíslan el caudal en ambas direcciones, lo que permite un control flexible del caudal.
2. Restricción mínima del flujo
El paso de caudal sin obstrucciones de la válvula de compuerta provoca escasas caídas de presión, lo que ahorra costes de bombeo.
3. Funcionamiento a bajo par
Las grandes aberturas de las válvulas de compuerta combinadas con piezas de gran acabado permiten un accionamiento sencillo.
4. Sin cavitación del flujo
Las válvulas de compuerta evitan la cavitación del flujo que provoca picaduras y corrosión en las válvulas de globo bajo altas caídas de presión.
5. Pigging capacidad
Las aberturas completas permiten limpiar el interior de las tuberías mediante el paso de un "cerdo", evitando los cortes de flujo.
6. Cierre hermético
La amplificación de la fuerza de contacto compuerta/asiento en las válvulas de compuerta de cuña permite un cierre positivo fiable incluso contra altas presiones Δ.
7. Tamaño más pequeño
Las dimensiones compactas de brida a brida de la válvula de compuerta se adaptan a instalaciones con espacio restringido.
8. Servicio bidireccional sin salida
Las válvulas de compuerta sellan positivamente las líneas con flujo unidireccional o con líquido lleno por un lado durante la reparación.
9. Seguridad contra la sobrepresurización
La robusta unión entre el cuerpo y el bonete soporta los golpes de ariete ocasionales sin fugas.
10. Fácil mantenimiento
La separación del bonete permite acceder y extraer rápidamente las piezas internas sin desmontar la válvula.
Desventajas de las válvulas de compuerta
Las válvulas de compuerta también tienen ciertas limitaciones que deben tenerse en cuenta a la hora de seleccionarlas para aplicaciones concretas:
1. No apto para estrangulamiento
La cuña o compuerta provoca turbulencias y vibraciones cuando está parcialmente abierta, dañando los asientos y la cuña o compuerta.
2. El cierre de golpe puede provocar transitorios
El cierre rápido de las compuertas frente a presiones diferenciales elevadas induce transitorios de golpe de ariete perjudiciales dentro de las tuberías.
3. No es ideal para un uso frecuente
Debido al gran número de componentes móviles que intervienen, las válvulas de compuerta pueden necesitar un mantenimiento temprano cuando se accionan con frecuencia.
4. Más pesadas que otros tipos de válvulas
El cuerpo y el bonete robustos para permitir el servicio a alta presión hacen que las válvulas de compuerta sean más pesadas que otras válvulas.
5. Indicación de posición no estándar
A diferencia de las válvulas de compuerta de vástago ascendente, los indicadores de posición suponen un coste adicional para las válvulas subterráneas de vástago no ascendente.
Indicadores de posición de válvulas de compuerta
Las válvulas de compuerta con vástagos no ascendentes no tienen ninguna indicación visual externa que muestre el estado de abierto/cerrado. Los indicadores de posición solucionan este problema, señalando el estado de la válvula.
Uso de indicadores de válvulas de compuerta:
- Blancos: Los blancos de colores brillantes en los vástagos ascendentes señalan el estado abierto.Los blancos se tiñen, atrapan residuos o los movimientos del vástago fuera de la vista comprometen fácilmente la fiabilidad de la indicación.
- Sensores de proximidad: Detectan electrónicamente la posición de la puerta y transmiten datos en tiempo real. Sin embargo, los componentes electrónicos pueden fallar en entornos difíciles.
- Indicadores mecánicos: Mecanismos sencillos con bandas de colores o flechas muestran la posición de la válvula a través de las penetraciones del capó. Los índices mecánicos visibles desde el exterior en todas las condiciones proporcionan información directa sobre la posición de la compuerta sin electrónica.
Una indicación fiable evita el accionamiento de compuertas cerradas que pueden romper el vástago o las compuertas. La retroalimentación de posición también evita dejar las compuertas ligeramente abiertas, lo que puede dejar pasar residuos que provoquen fugas en el asiento.
Consideraciones clave al seleccionar válvulas de compuerta
La elección de las válvulas de compuerta adecuadas requiere una evaluación:
- Presión nominal
- Temperatura nominal
- Dirección del flujo
- Requisitos de cierre
- Necesidades de resistencia a la corrosión
- Accesibilidad
- Necesidades de estrangulamiento
- Requisitos de automatización
- Costes iniciales y de mantenimiento
A la hora de elegir las válvulas, tenga en cuenta las condiciones de funcionamiento, las propiedades del medio y el lugar de instalación. Consultar a especialistas en válvulas también ayuda a seleccionar las configuraciones óptimas de válvulas de compuerta.
Las válvulas de compuerta correctamente dimensionadas con clases de presión adecuadas a las presiones máximas proporcionan una larga vida útil. Los revestimientos adecuados para resistir la corrosión evitan el fallo prematuro de la válvula.
Dimensionamiento de válvulas de compuerta
Durante el dimensionamiento, el diámetro del paso de caudal de la válvula de compuerta debe coincidir con el de la tubería para evitar cuellos de botella en el caudal.
Las válvulas sobredimensionadas pueden depositar residuos alrededor de las compuertas y provocar fugas. Las válvulas subdimensionadas provocan erosión, fugas y pérdidas de caudal por altas velocidades.
El tipo de extremo de conexión de la válvula también necesita tuberías adecuadas. Los extremos con bridas se adaptan a las necesidades de desmontaje frecuente, mientras que los extremos roscados se adaptan fácilmente a las aplicaciones de media presión.
Posición de instalación
Idealmente, las válvulas de compuerta deben estar en posición vertical, permitiendo la caída libre de la compuerta para reducir la fricción por deslizamiento. Esto prolonga la vida útil de la junta en aplicaciones de ciclo alto o de estrangulación.
Las posiciones horizontales necesitan abrirse y cerrarse de vez en cuando para evitar que la puerta se pegue a los asientos.
Configuraciones
Las válvulas de compuerta presentan diferentes juntas de bonete, diseños de vástago (ascendente/no ascendente), tipos de asiento (metálico/resiliente) y conexiones finales (embridadas, soldadas por encastre, soldadas a tope, etc.) para adaptarse a las necesidades particulares de instalación. Conseguir configuraciones adecuadas evita fallos prematuros.
La elección de la configuración correcta de la válvula de compuerta, junto con un dimensionamiento inteligente, da como resultado un rendimiento fiable de la aplicación. Esto minimiza las paradas imprevistas y permite aumentar el tiempo de actividad y la productividad operativa.
Conclusión
A partir de este análisis detallado, ya conoce el significado, el funcionamiento, los diseños, las aplicaciones y las ventajas de las válvulas de compuerta.
Para recapitular rápidamente:
- Las válvulas de compuerta proporcionan un control de apertura y cierre mediante un elemento de compuerta/disco que se mueve de forma normal al flujo.
- La compuerta presiona contra los anillos del asiento para conseguir un cierre hermético en ambas direcciones del flujo.
- Las válvulas de compuerta se utilizan principalmente como válvulas de aislamiento que detienen o abren completamente el flujo
Hay disponibles múltiples configuraciones de diseño con compuertas de cuña, de deslizamiento paralelo o expansibles. Esto permite una aplicación fiable en diversos escenarios industriales, como líneas químicas, plantas de proceso, líneas de vapor, etc., donde es necesario un aislamiento frecuente.
Espero que le haya gustado esta guía definitiva que explica todo sobre las válvulas de compuerta. Compártala si le ha resultado útil. Si tiene alguna otra pregunta sobre las válvulas de compuerta, hágamelo saber en la sección de comentarios a continuación.