Olay şu:
Yedek sürgülü vanaların doğru şekilde depolanması ve bakımı sadece yedek parçaları rafta tutmak değildir. Bu, kritik akışkan kontrol sistemlerinizin en çok ihtiyaç duyduğunuz anda asla arızalanmamasını sağlamakla ilgilidir.
Aslında, yanlış vana depolaması endüstriyel tesislerdeki acil durum ekipman arızalarının önde gelen nedenlerinden biridir. Ve inanın bana, kritik bir kapatma sırasında yedek vananın neden tutukluk yaptığını yönetime açıklayan kişi olmak istemezsiniz.
İşte bu yüzden bu kapsamlı kılavuzu bir araya getirdim. Bu makalenin sonunda, yedeklerinizi nasıl saklayacağınızı ve koruyacağınızı tam olarak bileceksiniz sürgülü vana Böylece göreve çağrıldıklarında performans göstermeye hazır olurlar.
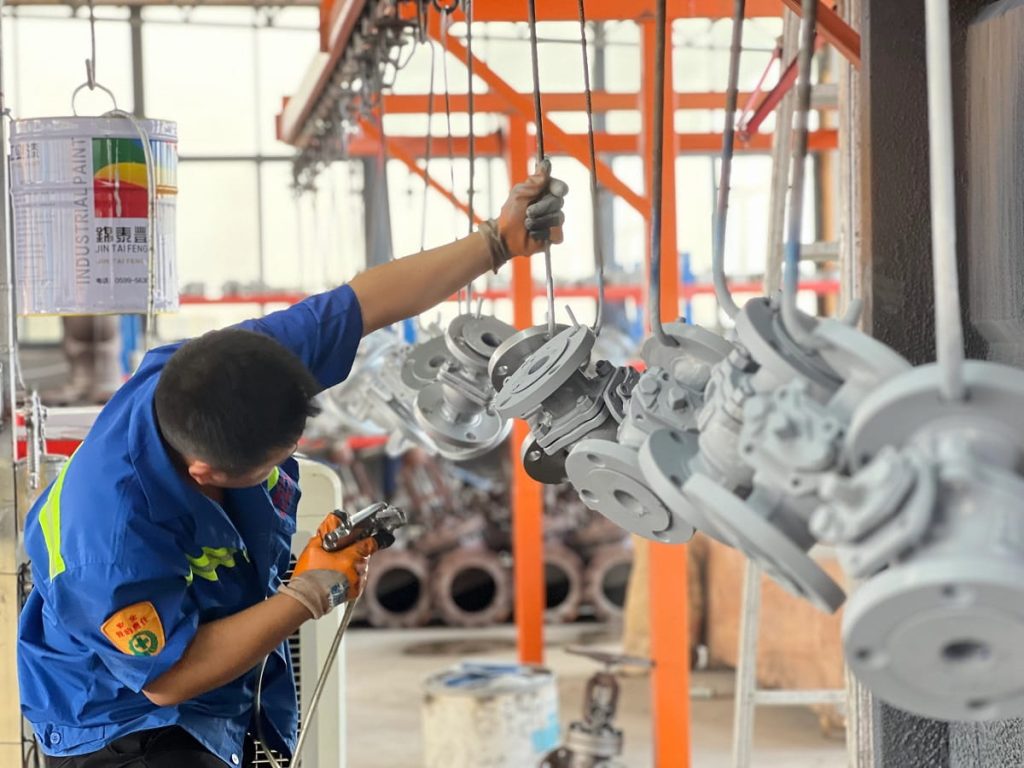
İçindekiler tablosu
- Yedek Sürgülü Vana Depolaması Neden Önemlidir?
- Valf Depolama Arızasının Arkasındaki Bilim
- Gerçekten İşe Yarayan Çevresel Depolama Gereksinimleri
- Uzun Süreli Depolama için Adım Adım Vana Hazırlığı
- Arızaları Önleyen Denetim Programları
- Farklı Vana Tipleri için Bakım Protokolleri
- Yaygın Depolama Hataları (Ve Bunlardan Nasıl Kaçınılır)
- Maliyet-Fayda Analizi: Doğru Depolama Neden Öder?
- Kritik Uygulamalar için Gelişmiş Depolama Stratejileri
- Yaygın Depolama Sorunlarını Giderme
- Valf Depolama Teknolojisinin Geleceği
- Dokümantasyon ve Kayıt Tutma En İyi Uygulamalar
- Depolama Programınızı Oluşturun: Başlarken
- Çözüm
Yedek Sürgülü Vana Depolaması Neden Önemlidir?
İşin özüne inmeden önce, size bir resim çizmeme izin verin.
Teksas'taki büyük bir su arıtma tesisi kurşun geçirmez bir yedekleme sistemine sahip olduğunu düşünüyordu. Depolarında iki yıldan uzun süredir yedek sürgülü vanalar saklıyorlardı. Yoğun yaz talebi sırasında birincil vanaları arızalandığında, aceleyle yedeği kurdular.
Sonuç mu?
Yedek valf düzgün kapanmıyordu. Depolama sırasında korozyon oturma yüzeylerine zarar vermişti. Tesis 18 saatlik kesinti ve $200.000'in üzerinde gelir kaybıyla karşı karşıya kaldı.
Sonuç: Doğru depolama isteğe bağlı değildir, kritik öneme sahiptir.
İşte bu kılavuzda ele alacaklarımız:
- Valf bozulmasını önleyen çevresel depolama gereksinimleri
- Uzun süreli depolama için adım adım hazırlık prosedürleri
- Sorunları arızaya dönüşmeden önce yakalayan denetim programları
- Sektör liderleri tarafından kullanılan gerçek dünya bakım protokolleri
Valf Depolama Arızasının Arkasındaki Bilim
Sizinle bazı ufuk açıcı verileri paylaşmama izin verin.
2024 yılında yapılan bir sektör araştırmasına göre, acil durumlarda meydana gelen yedek vana arızalarının 67%'si doğrudan uygunsuz depolama koşullarından kaynaklanmaktadır. En yaygın suçlular?
- Atmosferik korozyon (43% arıza)
- Conta bozulması (31% arıza)
- Mekanik bağlama (18% arıza)
- Kirlenme (8% arıza)
İyi haber ne mi? Tüm bu sorunlar doğru depolama yaklaşımı ile 100% önlenebilir.
Gerçekten İşe Yarayan Çevresel Depolama Gereksinimleri
Sıcaklık Kontrolü: Valf Korumanın Temeli
İşte çoğu tesisin sıcaklık kontrolü konusunda yanlış yaptığı noktalar:
Aşırı sıcaklıklardan kaçınmaya odaklanırlar ancak sıcaklık dalgalanmalarını göz ardı ederler.
Tatlı nokta: Depolama sıcaklıklarını günlük minimum değişimle 50°F ile 80°F (10°C ile 27°C) arasında tutun.
Bu neden önemli?
Sıcaklık döngüsü metal bileşenlerin farklı oranlarda genleşmesine ve büzülmesine neden olur. Bu da zaman içinde mikro çatlaklara ve sızdırmazlık deformasyonuna yol açabilecek gerilim konsantrasyonları yaratır.
Profesyonel İpucu: İklim kontrollü deponuz yoksa yalıtım bariyerleri kullanın ve günlük sıcaklık değişimlerini izleyin. Günde 20°F'nin üzerindeki değişimler sorun yaratır.
Nem Yönetimi: Korozyona Karşı İlk Savunma Hattınız
Bunu ne kadar vurgulasam azdır: Nem, depolanan vanaların sessiz katilidir.
Sihirli sayı? Bağıl nemi 50%'nin altında tutun.
Ancak çoğu insanın gözden kaçırdığı şey şudur: Bu sadece ortalama nemle ilgili değildir. Bu, yoğuşma döngülerini önlemekle ilgilidir.
Üç aşamalı nem kontrol yaklaşımı:
- Birincil kontrol: Nem alma sistemleri veya kurutucu malzemeler
- İkincil koruma: Buhar bariyerli ambalajlar
- İzleme: Alarm özellikli dijital higrometreler
Örneğin, birlikte çalıştığım bir kimyasal işleme tesisi, sadece uygun nem kontrolleri uygulayarak valf depolama arızalarını 89% azalttı. Yılda 15-20 depolanmış valf değiştirirken bunu sadece 2-3'e indirdiler.
Atmosferik Kirletici Koruması
Endüstriyel ortamlar depolanan ekipmanlar için zorludur. Düşük korozif gaz konsantrasyonları bile aylar veya yıllar içinde vana bileşenlerini tahrip edebilir.
Yaygın atmosferik tehditler:
- Tuzlu hava (kıyı tesisleri)
- Hidrojen sülfür
- Sülfür dioksit
- Yakındaki proseslerden kaynaklanan kimyasal buharlar
Çözüm: Gerektiğinde filtreleme sistemleri ile izole edilmiş depolama alanları.
Uzun Süreli Depolama için Adım Adım Vana Hazırlığı
Burası lastiğin yolla buluştuğu yerdir. Tam olarak bu prosedürü uyguladığınızda yedek valfleriniz yıllar sonra bile çalışmaya hazır olacaktır.
Aşama 1: İç Temizlik ve Koruma
Adım 1: Uygun temizlik solüsyonları kullanarak tüm proses kalıntılarını giderin
- İnorganik birikintiler için su bazlı çözümler
- Organik kalıntılar veya hidrokarbon kontaminasyonu için solvent temizliği
Adım 2: İç yüzeylere koruma bileşikleri uygulayın
- Karbon çelik bileşenler için buhar fazı inhibitörleri
- Paslanmaz çelik veya egzotik alaşımlar için özel pas önleyiciler
Kritik not: Koruma bileşikleri ve vana malzemeleri arasında tam uyumluluk sağlayın. Bazı işlemler hassas alaşımlarda gerilme korozyonu çatlamasına neden olabilir.
2. Aşama: Dış Koruma Önlemleri
Adım 3: Dış kaplamaları inceleyin ve onarın
- Depolamadan önce boya hasarlarını giderin
- Astar ve son kat boya uyumluluğu için üretici spesifikasyonlarını takip edin
Adım 4: Dişli bağlantıları koruyun
- Diş macunları veya koruyucu kapaklar uygulayın
- Uzun depolama süreleri için bant sarma sistemleri kullanın
3. Aşama: Konumlandırma ve Ambalajlama
Adım 5: Valf konumunu ayarlayın
- Sürgülü vanaları 25-50% açık konumda depolayın
- Bu, kirlenmeyi önlerken sızdırmazlık yüzeyleri üzerindeki baskıyı azaltır
Adım 6: Paketleme sistemlerinin uygulanması
- Kontrollü iç atmosfer için buhar bariyeri filmleri
- Mekanik koruma için rijit konteynerler
- Depolama süresine göre boyutlandırılmış kurutucu malzemeler
Arızaları Önleyen Denetim Programları
İşte benim gerçek endüstriyel deneyimlerime dayanarak önerdiğim denetim çerçevesi:
Aylık Görsel Denetimler (vana başına 15 dakika)
Kontrol Listesi:
- Dış kaplama durumu
- Ambalaj bütünlüğü
- Çevresel izleme sistemleri
- Kurutucu doygunluk göstergeleri
Üç Aylık Detaylı Değerlendirmeler (vana başına 45 dakika)
Faaliyetler:
- Kaputun çıkarılması ve iç denetim
- Kök çalışma doğrulaması
- Ambalaj durumu değerlendirmesi
- Sızdırmazlık yüzey değerlendirmesi
Danışmanlığını yaptığım bir tesis, üç aylık denetimler sırasında, acil durum konuşlandırması sırasında tamamen arızaya neden olabilecek potansiyel gövde bağlama sorunlarını keşfetti.
Yıllık Kapsamlı Değerlendirme (vana başına 2-3 saat)
Tam kapsam:
- Komple demontaj ve bileşen kontrolü
- Basınç testi (hidrostatik ve pnömatik)
- Üretici spesifikasyonlarına göre boyutsal doğrulama
- Simüle edilmiş çalışma koşulları altında performans testi
Farklı Vana Tipleri için Bakım Protokolleri
Karbon Çelik Vanalar
Bunlar en agresif korozyon korumasını gerektirir.
Temel gereksinimler:
- Her 12-18 ayda bir buhar fazı inhibitörü uygulaması
- Aylık nem izleme
- Herhangi bir kaplama hasarına anında müdahale
Paslanmaz Çelik Vanalar
Adının sizi yanıltmasına izin vermeyin; paslanmaz çelik valfler yine de uygun bakıma ihtiyaç duyar.
Odak alanları:
- Klorür kontaminasyonunu önleyin (stres korozyon çatlamasının ana nedeni)
- Conta arayüzlerinde çatlak korozyonu olup olmadığını izleyin
- Uyumlu koruma bileşikleri kullanın
Egzotik Alaşımlı Vanalar
Özel hususlar:
- Malzemeye özgü koruma gereklilikleri
- Geliştirilmiş dokümantasyon ve izlenebilirlik
- Özel taşıma prosedürleri
Yaygın Depolama Hataları (Ve Bunlardan Nasıl Kaçınılır)
Düzinelerce endüstriyel tesise danışmanlık yaptıktan sonra, aynı hataları tekrar tekrar gördüm:
Hata #1: Vanaların tam kapalı konumda depolanması
- Problem: Sızdırmazlık yüzeylerinde gerilim konsantrasyonları oluşturur
- Çözüm: Her zaman kısmen açık konumda saklayın
Hata #2: Çevresel izlemenin göz ardı edilmesi
- Problem: Kademeli bozulma fark edilmiyor
- Çözüm: Alarm sistemleri ile otomatik izlemenin uygulanması
Hata #3: "Ayarla ve unut" zihniyeti
- Problem: Depolama koşulları zaman içinde değişir
- Çözüm: Düzenli denetim ve bakım programları
Maliyet-Fayda Analizi: Doğru Depolama Neden Öder?
Bunu gerçek rakamlarla ortaya koymama izin verin.
6 inçlik bir sürgülü vana için tipik maliyetler:
- Yeni valf: $15,000-$25,000
- Uygun depolama programı: Vana başına yılda $500-$1,000
- Arıza süresi boyunca acil durum değişimi: $50,000-$100,000+ (üretim kaybı dahil)
Matematik basittir: Uygun depolama programları kendilerini defalarca amorti eder.
Kritik Uygulamalar için Gelişmiş Depolama Stratejileri
Otomatik İzleme Sistemleri
Modern tesisler sürekli izleme için IoT sensörleri kullanıyor:
- Sıcaklık ve nem kaydı
- Menzil dışı koşullar için otomatik uyarılar
- Tesis bakım yönetim sistemleri ile entegrasyon
Rotasyon Programları
Bazı tesisler, çalışabilirliği sağlamak için depolanan vanaları geçici olarak hizmete alır:
- Uzun süreli statik depolama sorunlarını önler
- Gerçek dünya performans doğrulaması sağlar
- Personelin ekipmana aşinalığını korur
Yaygın Depolama Sorunlarını Giderme
Korozyon Sorunları
Erken evre korozyon:
- Etkilenen alanları derhal temizleyin
- Çevresel kontrolleri iyileştirin
- Muhafaza yöntemlerini yeniden değerlendirin
Gelişmiş korozyon:
- Profesyonel değerlendirme gerekli
- Bileşen değişimi gerektirebilir
- Tüm depolama programını gözden geçirin
Mekanik Ciltleme
Kök bağlama:
- Genellikle kirlenme veya korozyon ürünlerinden kaynaklanır
- Üretici spesifikasyonlarına göre temizleyin ve yağlayın
- Çevresel kontrolleri kontrol edin
Conta Bozulması
Yaşa bağlı sertleşme:
- Uzun depolama süreleri için normal
- Servis öncesinde conta değişimi için plan yapın
- Depolama sıcaklığı optimizasyonunu göz önünde bulundurun
Valf Depolama Teknolojisinin Geleceği
2025 ve sonrasına baktığımızda, ortaya çıkan birkaç teknoloji vana depolama ortamını değiştiriyor:
Tahmine dayalı analitik: Depolama parametrelerine dayalı olarak vana durumunu tahmin eden yapay zeka destekli sistemler
Gelişmiş koruma bileşikleri: Daha uzun süreli koruma sağlayan yeni formülasyonlar
Akıllı paketleme: İç koşulları takip eden kendi kendini izleyen konteynerler
Dokümantasyon ve Kayıt Tutma En İyi Uygulamalar
Depolama programının başarısı için doğru dokümantasyon çok önemlidir:
Temel kayıtlar:
- Depolama hazırlama prosedürleri ve tarihleri
- Denetim bulguları ve eğilimler
- Çevresel izleme verileri
- Bakım faaliyetleri ve parça değişimi
Dijital sistemlerin avantajları:
- Otomatik hatırlatma sistemleri
- Trend analizi yetenekleri
- Tesis varlık yönetimi ile entegrasyon
Profesyonel ipucu: Zaman içinde vana durumunu belgelemek için dijital fotoğrafçılık kullanın. Görsel eğilimler genellikle ölçümlerde ortaya çıkmadan önce sorunları ortaya çıkarır.
Depolama Programınızı Oluşturun: Başlarken
Eğer sıfırdan başlıyorsanız, işte benim önerdiğim yaklaşım:
1. Aşama (1. Ay): Değerlendirme ve planlama
- Mevcut yedek vanaların envanteri
- Mevcut depolama koşullarını değerlendirin
- İyileştirme planı geliştirin
2. Aşama (2-3. Aylar): Çevresel kontroller
- Nem ve sıcaklık kontrolleri uygulayın
- İzleme sistemleri kurun
- Uygun paketleme prosedürlerine başlayın
3. Aşama (4-6 Aylar): Denetim ve bakım protokolleri
- Personeli prosedürler konusunda eğitin
- Dokümantasyon sistemleri kurun
- Düzenli denetim programlarına başlayın
Çözüm
Yedek sürgülü vanaların doğru şekilde depolanması ve bakımı üç temel ilkeye dayanır: çevre kontrolü, düzenli denetim ve proaktif bakım.
Bunu doğru yapan tesislerde 95%'nin üzerinde yedek vana güvenilirlik oranları görülmektedir. Bunu yapmayanlar ise genellikle en az göze alabilecekleri zamanlarda maliyetli acil durum arızalarıyla karşılaşırlar.
Unutmayın: Yedekleme valfleriniz kritik sistemleriniz için sigorta poliçeleridir. Ve her sigorta gibi, yalnızca en çok ihtiyaç duyduğunuzda çalışırlarsa değerlidirler.
Bu depolama ve bakım uygulamalarını bugün uygulamaya başlayın ve yedekleme sistemlerinizin gerçekten harekete hazır olduğunu bilerek daha rahat uyuyun.
Valf depolama programlarıyla ilgili deneyiminiz nedir? Bu stratejilerden herhangi birini tesisinizde uyguladınız mı? Aşağıdaki yorumlarda bana bildirin.