A Rückschlagventil ist eine mechanische Vorrichtung, durch die Flüssigkeiten nur in eine Richtung fließen können. Rückschlagventile verhindern automatisch jeglichen Rückfluss und spielen daher eine entscheidende Rolle in Fluidsteuerungssystemen in verschiedenen Branchen. Aber was genau sind sie und wie funktionieren sie? Dieser umfassende Leitfaden erklärt Ihnen alles, was Sie wissen müssen.
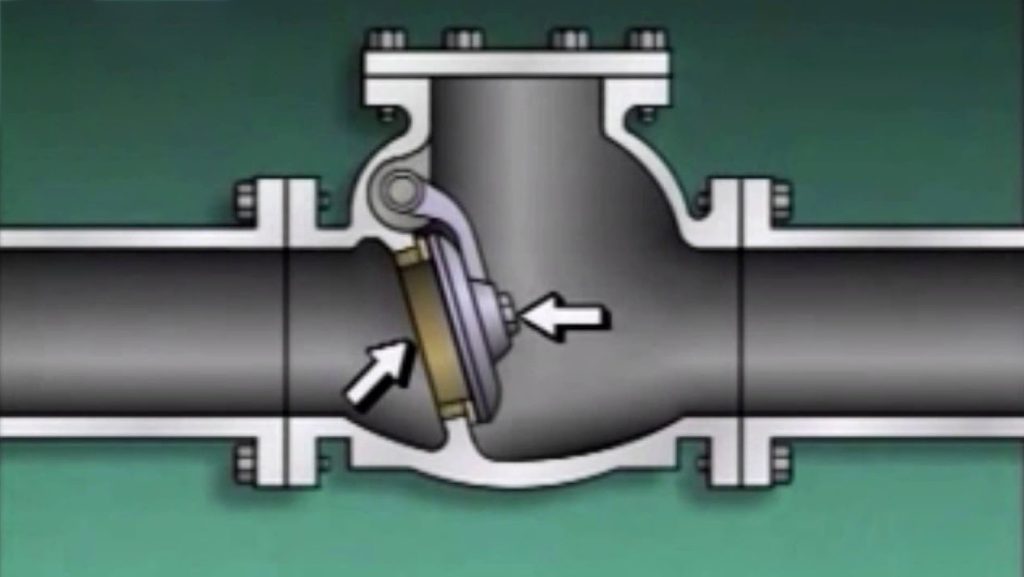
Inhaltsübersicht
Was ist ein Rückschlagventil?
Ein Rückschlagventil, auch bekannt als Rückschlagventil oder Einwegventilist eine mechanische Vorrichtung, die es einem Fluid (Flüssigkeit oder Gas) ermöglicht, nur in eine Richtung zu fließen, und gleichzeitig die Rückströmung in einem System verhindert.
Funktionsweise von Rückschlagventilen
Das Funktionsprinzip von Rückschlagventilen macht sich die Kraft des Flüssigkeitsdrucks zunutze. Wenn die Flüssigkeit in das Ventil eintritt, drückt sie gegen ein internes Bauteil wie eine Kugel, eine Klappe, einen Kolben oder einen Ventilkegel. Wenn sich ein ausreichender Druck aufbaut, hebt sich das Bauteil an oder schwingt aus dem Weg, sodass das Medium zum Auslass fließen kann.
Sobald der Vorwärtsdruck nachlässt, wird das Innenteil durch eine Feder oder die Schwerkraft wieder an den Ventilsitz gedrückt. Dadurch wird der Einlass wasserdicht verschlossen und ein Rückfluss verhindert. Der minimale Vorwärtsdruck, der zum Öffnen des Ventils erforderlich ist, wird als Öffnungsdruck oder Öffnungsdruck bezeichnet.
Zusammenfassend lässt sich also sagen, dass das Rückschlagventil bei Vorwärtsströmung geöffnet und bei Rückwärtsströmung automatisch geschlossen wird. Dank dieser Funktion erfüllen Rückschlagventile ihren Hauptzweck - die Verhinderung von Rückfluss.
Die wichtigsten Vorteile von Rückschlagventilen
Rückschlagventile bieten erhebliche Vorteile bei der Handhabung von Flüssigkeiten:
Rückwärtsfluss verhindern
Da Rückschlagventile nur eine Bewegung in eine Richtung zulassen, verhindern sie, dass Medien in die falsche Richtung fließen. Dies schützt die Geräte vor Leistungsproblemen, Verschmutzungsrisiken und physischen Schäden durch Gegendruck.
Druck regulieren
Da Rückschlagventile den Durchfluss in Vorwärtsrichtung aufrechterhalten und Druckverluste durch Rückfluss verhindern, sorgen sie dafür, dass Flüssigkeitssysteme ein konstantes Druckniveau halten. Dies ist entscheidend für die Effizienz von Industrieanlagen, Gebäuden und Bewässerungssystemen.
Wasserschlag reduzieren
Ein schnelles Schließen des Ventils führt häufig zu Druckstößen, die auf die kinetische Energie der sich bewegenden Flüssigkeit zurückzuführen sind und als Wasserschlag bezeichnet werden. Rückschlagventile mildern solche harten hydraulischen Stöße durch kontrolliertes Abbremsen im Gegensatz zu einem abrupten Stopp.
Automatisierter Betrieb
Die ausschließliche Verwendung mechanischer Komponenten ermöglicht das automatische Öffnen und Schließen der Rückschlagventile in Abhängigkeit von den Druckverhältnissen. Es sind keine manuellen Eingriffe oder externe Energieversorgung erforderlich.
Geringere Wartung
Das einfache Innenleben minimiert den Wartungsbedarf. Rückschlagventile enthalten nur wenige bewegliche Teile, die robust und sehr zuverlässig sind, wenn sie für die jeweilige Anwendung angemessen dimensioniert sind.
Haupttypen von Rückschlagventilen
Während alle Rückschlagventile die gleiche Grundfunktion erfüllen, gibt es verschiedene Ausführungen für unterschiedliche Flüssigkeitsbedingungen, Rohrgrößen und Installationskonfigurationen.
Kugelrückschlagventile
Eine kugelförmige Kugel im Inneren des Ventilgehäuses dient bei dieser Konstruktion als Verschlussteil. Wenn sich der Druck am Einlass aufbaut, wird die Kugel zur Seite geschoben und gibt den Weg vorübergehend frei. Diese Ventile können leicht pulsierende Durchflüsse gut bewältigen.
Rückschlagventile
Hier schwenkt eine klappbare Scheibe bei ausreichendem Zufluss von der Einlassseite aus dem Weg. Rückschlagklappen zeichnen sich durch einen geringen Durchflusswiderstand und eine große Bohrungsöffnung für den Einsatz in Rohren mit großem Durchmesser aus.
Rückschlagventile anheben
Ein spindelgeführter Kolben, auf den der Eingangsdruck einwirkt, bildet den Schließmechanismus in Hubrückschlagventilen. Der Kolben hebt sich vertikal vom Sitz, wenn der Druck den Feder- oder Schwerkrafteinfluss übersteigt. Diese Bauart eignet sich für Flüssigkeiten mit hohen Strömungsgeschwindigkeiten und häufigen Strömungsumkehrungen.
Membran-Rückschlagventile
Anstelle einer schwingenden oder aufsteigenden Barriere enthalten Membranrückschlagventile eine elastische Membran, die sich durchbiegt, um den Durchfluss zu ermöglichen. Die entspannte Membrane dichtet dann den Einlass ab. Diese Ventile eignen sich für aggressive Flüssigkeiten und Hochtemperaturanwendungen.
Schlüsselfaktoren bei der Spezifikation von Rückschlagventilen
Mehrere wichtige Aspekte entscheiden darüber, ob ein Rückschlagventilmodell für eine bestimmte Anwendung geeignet ist:
- Druckstufe: Rückschlagventile sind für einen breiten Druckbereich erhältlich, von Hochvakuum bis zu 15.000+ psi für extreme industrielle Anwendungen. Berücksichtigen Sie sowohl Arbeits- als auch Gegendruck.
- Durchflusskapazität: Sorgen Sie für einen angemessenen Lebenslauf (Durchflusskoeffizient) auf die Durchflussmenge des Systems abstimmen. Eine Überdimensionierung des Ventils kann zu Fehlfunktionen führen.
- Ausrichtung der Installation: Bestimmte Rückschlagventile müssen horizontal oder vertikal eingebaut werden, damit sie mit Hilfe der Schwerkraft ordnungsgemäß funktionieren.
- Druck knacken: Der zum Öffnen des Ventils erforderliche Mindestdruckunterschied sollte mit den normalen Betriebsbedingungen übereinstimmen. Der typische Bereich liegt bei 2-5 psi.
- Temperatur-Bewertung: Der Betrieb in Heiz-/Kühlsystemen oder Prozessleitungen kann mit erheblichen Temperaturschwankungen verbunden sein. Rückschlagventile müssen daher hohen oder niedrigen Temperaturen standhalten.
- Anschluss der Rohrleitung: Abmessungen wie Rohrdurchmesser, Flanschgröße und Anschlussart (Gewinde, Schweißmuffe usw.) müssen eine geeignete Anpassung der Armatur an die Rohrleitung ermöglichen.
- Medieneigenschaften: Aspekte wie Viskosität, Verschmutzungsgrad, Korrosivität und Neigung zu Ablagerungen helfen bei der Entscheidung über geeignete Ventilwerkstoffe und funktionale Designaspekte.
Unter Berücksichtigung dieser Schlüsselfaktoren können Konstrukteure von Flüssigkeitssystemen und Wartungsteams die am besten geeigneten, langlebigen und zuverlässigen Rückschlagventile für ihre spezifischen Anwendungsanforderungen auswählen und gleichzeitig den Betrieb sicherstellen. Wenn sie richtig dimensioniert und installiert sind, werden Rückschlagventile über Jahre hinweg mit minimalem Aufwand einwandfrei funktionieren.
Allgemeine Rückschlagventilanwendungen
Von privaten Sanitärsystemen bis hin zu großen Industrieanlagen spielen Rückschlagventile eine wichtige Rolle, wenn es darum geht, einen Durchfluss in eine Richtung zu ermöglichen und den Druck zu regulieren.
HVAC-Systeme
Heizungs-, Lüftungs- und Klimaanlagen sind auf Rückschlagventile angewiesen, um den Rückfluss von erwärmter oder gekühlter Luft bzw. Wasser zu verhindern und die Wärmeregulierung in Gebäuden zu ermöglichen.
Industrielle Verarbeitung
Rückschlagventile schützen Rohrleitungen, Pumpen und Steuergeräte vor Verunreinigungen und Schäden und ermöglichen gleichzeitig einen effizienten Flüssigkeitstransport. Sie sind in Produktionsanlagen und Prozessindustrien, die mit extrem hohen/niedrigen Temperaturen und Drücken arbeiten, unverzichtbar.
Bewässerung
Rückschlagventile in Bewässerungsleitungen verhindern das Zurücksaugen von behandeltem Wasser und verhindern, dass externe Verunreinigungen in die Versorgungsleitung gelangen.
Brandbekämpfungssysteme
Die Aufrechterhaltung eines angemessenen Drucks und eines gleichmäßigen Wasserflusses zu Sprinklern und Pumpen wird durch Rückschlagventile erreicht. Diese Anwendung erfordert eine hohe Widerstandsfähigkeit gegenüber stark verschmutztem Wasser.
Erdölförderung
Von Offshore-Plattformen bis hin zu Lagertanks sorgen Rückschlagventile für einen unidirektionalen Durchfluss durch kilometerlange Öl- und Gaspipelines, während sie gleichzeitig einen reibungslosen Pumpvorgang gewährleisten und durch Wasserschlag verursachte Brüche verhindern.
Durch die Verhinderung von Rückströmungen bei so unterschiedlichen Anwendungen beweisen Rückschlagventile weiterhin ihre Notwendigkeit bei der Handhabung von Flüssigkeiten, Gasen, Dampf und mehr in privaten, gewerblichen und industriellen Flüssigkeitsnetzen.