When it comes to regulating flow in industrial pipe systems, ball valves and butterfly valves are two of the most common options.
Both valve types have their advantages and disadvantages when compared to each other. Knowing how they differ allows you to select the best valve for your particular application.
In this post, I’ll compare ball valves and butterfly valves in depth so you can make an informed decision between the two.
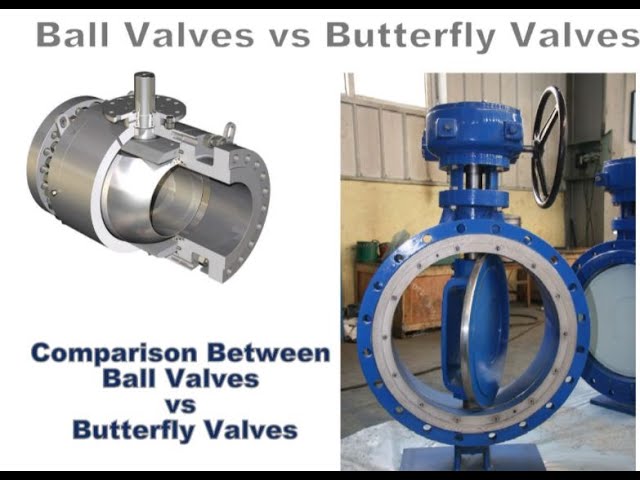
An Overview of Ball Valves
A ball valve uses a perforated, spherical disc to control liquid or gas flow. When open, the ball’s bore is in line with the valve body’s inlet and outlet. When closed, the bore is perpendicular, blocking flow.
Ball valves are rotary valves requiring a 90 degree turn to go from fully open to fully closed. This makes them relatively fast-acting compared to other valve types.
They can handle high pressure applications up to 1,000+ PSI depending on the model and are capable of regulating flow to a certain extent with precise positioning.
Applications Where Ball Valves Excel
Ball valves really shine for on/off applications rather than throttling flow control. Their tight sealing and ability to withstand high pressures also suit them well for:
- Gas lines
- Chemical/petroleum transport
- High temperature liquids
- Corrosive media
- Vacuum lines
Certain ball valve variants like V-port or characterised control trim enable reasonable flow regulation. But you’ll get better modulation from globe or butterfly valves overall.
An Overview of Butterfly Valves
Butterfly valves also use a rotary disc design. But instead of a spherical ball, a thin disc pivots from the center of the valve body.
When open, flow passes around the disc unimpeded. In the closed position, the disc seats against the perimeter of the valve body, blocking flow similar to a ball valve.
Applications Where Butterfly Valves Stand Out
Butterfly valves are built for large diameter applications where other valve styles would be impractical or cost-prohibitive.
You’ll typically find them in roles like:
- Cooling water intake/outflow
- Fire suppression lines
- Municipal water transport
- Hydroelectric penstocks
- Stormwater overflow
- Sewage lines
They also suit throttling applications better than ball valves in some cases. The disc doesn’t fully exit the flow stream when open, enabling reasonable control.
Ball Valve vs Butterfly Valve Comparison
Now that you know the basic characteristics of ball and butterfly valves, let’s compare them across some key categories:
Cost
For small pipe diameters under 12 inches, ball and butterfly valves cost about the same.
But past 12 inches, butterfly valves become much more affordable than an equivalent ball valve. At the high end reaching 48 inches, butterfly valves are around 1/4th the price of a ball valve.
The lightweight single-piece disc is cheaper to produce at scale than a massive one-piece ball needing extensive machining.
Winner: Butterfly Valve
Pressure Ratings
When it comes to handling pressure, ball valves are the undisputed champions. Many can handle at least 800 PSI without issue and specialty models reach far beyond that.
The main downside of a butterfly valve is its inability to deal with high pressure applications. Anything over 300 PSI risks leaking and potential valve damage. The seating depends on a thin edge mating perfectly with the perimeter seal.
High pressures make it difficult to close the valve and necessitate a bypass to balance line pressure.
Winner: Ball Valve
Flow Control
Both valve types easily handle on/off control. And both can modulate flow to some degree although ball valves will do this better in most cases.
The disc of a butterfly valve always remains in the flow stream at an angle except when fully open or fully closed. At high flow velocities, this angled disc causes significant turbulence and pressure drops.
So a butterfly valve’s flow control capabilities diminish rapidly as pressures and velocities rise. They end up acting as more of an on/off component.
Ball valves on the other hand can take on a legitimate control valve function in certain scenarios. Configurations like V-port, contour port, and characterised control trim enable smooth flow regulation without pressure drops.
Winner: Ball Valve
Size and Weight
Earlier we mentioned cost scaling better for butterfly valves at large sizes. Weight also becomes a differentiating factor around the 12 inch diameter mark.
A 48 inch butterfly valve weighs in under 1,500 lbs. Whereas an equivalent ball valve tips the scales over 15,000 lbs!
The compact single-piece disc carries far lower loads than a massive spherical chunk of steel. This gives butterfly valves a huge advantage in large water or wastewater systems where weight matters.
Winner: Butterfly Valve
Cycle Life
Both valve types should deliver acceptable lifespans in excess of 10,000 cycles if sized and specified correctly. However their longevity differs across factors like pressure and flow velocity.
A butterfly valve’s Achilles heel is high differential pressure as discussed earlier. The seating contact point sees rapid wear leading to leakage over time.
Ball valves can withstand far greater pressures for far longer. In fact high velocities and pressure drops across a valve shorten its lifespan considerably. And those are effects butterfly valves suffer from but not ball valves.
Winner: Ball Valve
Picking the Right Valve for Your Application
We’ve covered a lot of factors on how ball valves and butterfly valves differ. Now let’s boil things down to a simple decision process.
Here are two questions to quickly narrow down whether a ball or butterfly valve makes sense:
- Is line pressure under 300 PSI? If yes, consider a butterfly. If no or it approaches/exceeds 1,000 PSI, choose a ball valve.
- Does pipe diameter exceed 12 inches? If yes, default to a butterfly valve for cost savings. If no, evaluate both valves.
Beyond those rules of thumb, also factor in:
- Flow Control Needs – Tight regulation suits a ball valve better. Simple on/off duties can use either.
- Maintenance Access – Ball valves allow in-line maintenance. Butterfly valves often require adjacent spool pieces.
- Weight Restrictions – Lightweight butterfly valves accommodate size/weight limited systems.
- Media Properties – Ball valves withstand difficult liquids and gases better than butterfly typically.
There are always exceptions based on the nuances of your system. But this decision process hits the critical points for an informed valve choice.
An experienced supplier can make specific recommendations based on all your operating conditions and requirements too.
Summary: How to Choose Between Ball Valves and Butterfly Valves
Both ball and butterfly valves serve an important role in regulating flow across a breadth of industrial systems.
Their main differences come down to:
- Cost – Ball valves cost more at large sizes
- Pressure – Ball valves outperform at high pressures
- Flow Control – Ball valves provide smoother regulation
- Weight – Butterfly valves are lighter at big diameters
Factor in size, pressure, flow, weight limits, maintenance access, and media compatibility. Then leverage the guidance here to pick the best valve technology for your application.