Globe valves may not be the flashiest valves out there. But they play an incredibly important role in regulating flow in industrial pipe systems.
In this comprehensive guide, as a professional globe valve manufacturer, we’ll cover everything you need to know about what is a globe valve used for, including:
- How globe valves work
- Different types of globe valves
- Common globe valve applications
- Advantages and disadvantages of using globe valves
Plus, we’ll look at some pro tips for maintaining your globe valves so they work like champs for years.
Let’s dive in!
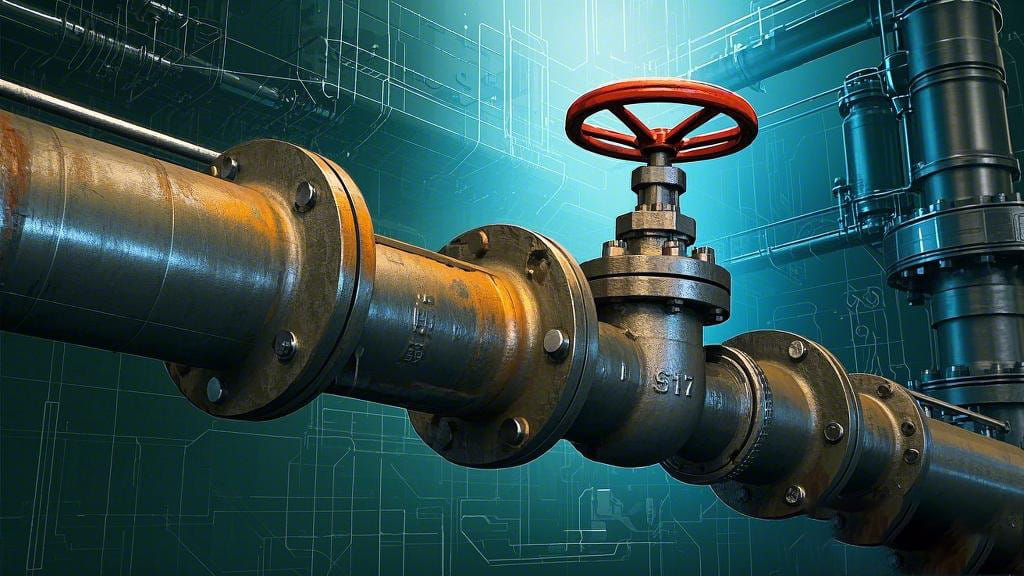
Table of contents
How Do Globe Valves Work?
Simply put, a globe valve controls fluid flow by slowing it down.
Here’s an overview of what’s happening inside a wide open globe valve:
First, the fluid enters the valve and bumps into a baffle that forces it to change directions. Next, it goes up through an opening in the valve seat. Finally, the fluid continues on its way through your pipeline.
When you start closing a globe valve, a plug (also called a disc) lowers down and starts restricting the opening in the seat. This narrows the path that the fluid can flow through, acting like a bottleneck.
Fully closing the valve pushes the disc completely into the seat, sealing it off and stopping flow altogether.
So in summary:
- An open globe valve slows flow down
- A partially closed globe valve restricts flow
- A fully closed globe valve stops flow
This gives globe valves incredibly precise control over flow rates. And it’s the reason they excel at regulating applications.
On top of that, globe valves have excellent sealing capabilities when fully closed. This allows them to completely stop flow, even in high pressure applications.
Now let’s look at a few of the most common configurations of globe valves.
3 Types of Globe Valves
While globe valves come in many different variations, there are 3 main types:
1. Z-Pattern Globe Valves
The Z-pattern (also called T-pattern) is the most common type of globe valve.
Z-pattern globe valves force fluid to follow a zig-zag flow path inside the valve.
This change of direction restricts flow. But it also creates lots of turbulence inside the valve.
So while Z-pattern globe valves excel at regulating flow, the turbulence leads to pressure loss.
2. Y-Pattern Globe Valves
Y-pattern globe valves are a modified version of the standard Z-pattern valve.
The main difference is that the seat opening is slanted at an angle inside the valve body.
The angle that the fluid travels at is less severe. So there’s less turbulence and pressure loss through a Y-pattern valve.
While Y-pattern globe valves are generally more expensive than Z-patterns, they’re ideal for applications where you want precise flow control without restricting overall flow too much.
3. Angle Globe Valves
Angle globe valves have the inlet and outlet at a 90 degree angle from each other. This allows them to serve as both a valve and a pipe elbow.
Since fluid only has to turn 90 degrees (as opposed to a full 180 in Z and Y patterns), these valves cause the least amount of pressure loss.
Angle globe valves are a great choice when minimal loss combined with flow regulation is needed.
Now let’s look at some of the most common globe valve applications.
What is a Globe Valve Used For? 5 Common Applications
Globe valves have certain characteristics that make them well-suited for specific uses.
Here are 5 of the most common globe valve applications:
1. Regulating Flow in Water Systems
Because of their excellent throttling abilities, globe valves frequently regulate cooling water flow on the water-side of HVAC and refrigeration systems.
You’ll also find them controlling flow to fixtures in commercial plumbing systems.
For example, globe valves under bathroom sinks, toilets, urinals, etc. make it easy to shut off water to a specific fixture for maintenance, without affecting the rest of the system.
2. Steam Systems
Globe valves have the precision and pressure handling capabilities for steam system service.
You’ll often see them at heat exchangers, regulating steam flow to precisely meet heating demands. For example, at a shell and tube heat exchanger in a commercial building.
Many steam boilers have specialized globe valves called stop checks installed at the boiler outlet too.
Stop checks combine a globe valve and check valve into one component. This gives operators the ability to regulate steam flow from the boiler. But the built-in check valve stops dangerous steam backflow into the boiler.
3. Mixing Fluids
Blending two fluids together is commonplace in industries like food processing, pharmaceutical manufacturing, and chemical processing.
Globe valves meter the flow of each individual fluid. Then the streams mix in precise concentrations downstream of the valves.
4. Pressure Reducing Valves (PRVs)
Anytime you need to lower upstream pressure down to a controlled downstream pressure, you need a PRV.
There are many styles, but globe valves are one of the most popular thanks to their excellent throttling capabilities.
PRVs take advantage of the pressure differentials between the high and low pressure sides to operate. No external power source required!
Some common examples where you might encounter PRV globe valves:
- Reducing city water pressure entering factories and buildings
- Lowering steam header pressure for process use
- Industrial compressed air systems
5. Surge Control
Whenever you quickly stop flowing liquid (like with a pump shutoff), flow momentum causes a pressure spike called a “surge”.
At a minimum, surges accelerate wear and tear. But severe ones can destroy entire pump systems!
By quickly opening during the pressure spike event, surge control globe valves release pressure and prevent catastrophe. The globe valve’s fast-acting capabilities suit them perfectly for this.
Advantages of Globe Valves
Now that we’ve covered globe valve internals and some applications, let’s summarize some of the main advantages they offer:
Precise Throttling Capabilities – The tiered seat design provides far superior control over intermediate flow compared to other valve designs.
Minimal Leakage – The linear seat design enables excellent shutoff capabilities under pressure, keeping fluids where they belong.
Low Maintenance – Globes are very tolerant of debris and rarely require more than basic servicing over years of use.
Customization – With all the trim, body, bonnet, and disc options available, you can spec a globe valve for practically any combination of pressure, temperature, fluids, and required performance specifications.
When you need accuracy, reliability, and versatility, few valve designs check all the boxes like a globe valve.
But globe valves aren’t without some downsides…
Disadvantages of Globe Valves
The very characteristics that make globe valves good at what they do, also create some inherent disadvantages.
Chief among them is flow restriction and pressure loss.
Remember the zig-zag flow path inside globe valves? That’s some intense turbulence!
All the direction changes restrict flow compared to other valves. While not an issue for regulators, it makes globe valves less suited for isolation applications where you want absolutely no flow restrictions when open.
The intense turbulence also leads to pressure loss. So while globe valves suit lower pressure applications just fine, they’re less than ideal for high flow, high pressure systems where pressure loss is unacceptable.
Other potential globe valve disadvantages include:
Higher initial cost – More moving parts drives up their price.
Complex internal geometry – Not the easiest valves to maintain in severe service conditions.
Potential clogging – The tight passages leave them susceptible to fouling in extremely dirty services.
So while globe valves excel at flow control, they come up short when it comes to isolation duties and handling high pressure flow.
Pick another valve type if those characteristics are critical!
Now let’s close things out with some key maintenance tips for globe valves.
Globe Valve Maintenance Tips
To keep your globe valves in tip-top shape for years to come:
Inspect annually – Check for external leakage and smooth handwheel operation. Catch issues early!
Detail disassemble every 3-5 years – Clean seats, plugs, and stems of debris and deposits for smooth functioning.
Lubricate stems and seals – Keep things sliding smoothly using manufacturer approved lubricants.
Consider linings and coatings – Protect critical valve internals from corrosion and erosion with special overlays in harsh services.
Automate bigger valves – Manual operation of large valves is cumbersome. Actuators make operation consistent and hands-free.
Monitor automation health – Check diagnostic data and have specialists verify health of actuators and positioners regularly.
And with that, you’ve reached the end of this globe valves extravaganza!
You now know key details on:
- Internal workings
- Different configurations
- 5 useful applications
- Pros and cons
- Critical maintenance needs
I hope you’ve achieved globe valve zen! If any questions pop up, ask away in the comments section.