What is Explosive Decompression?
Many manufacturers and operators in the oil and gas industry have leakage problems with elastomer seals, especially when a drop in pressure takes place. This primarily occurs in sealings which create a barrier against gaseous media if highly pressurized gas falls to a very low-pressure level within a very short period of time. The result of this process is often damage to the Viton o-rings. The elastomer material is either torn in various places or blistering on the surface. This phenomenon is called explosive decompression.
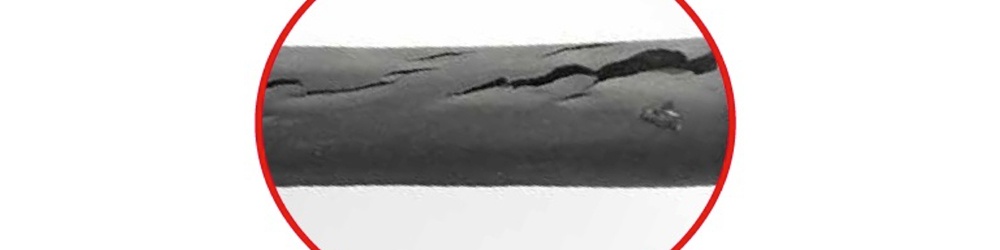
For the high demands on elastomer seals against explosive decompression (AED / Anti Explosive Decompression), all trunnion ball valves supplied by ZECO Valve are fitted with Viton AED o-rings. Most brands stocked are fitted with NORSOK standard M-710 certified o-rings (the leading international standard for this field).
What is Explosive Decompression O-Ring?
Standard elastomer o-rings do provide FE Class A performance by temperature, pressure, and fluids. Water, aromatics, amines, CO2, glycol, methanol, etc, can either swell the matrix to bursting point in the confinement of the o-ring groove or chemically attack the polymer itself. Low temperature (blowdown situations) require special ED-resistant o-rings as standard elastomers become hard and can no longer follow stem lateral movement.
The component in valves that leads to the most limited “operating window” are elastomer o-rings. Such o-rings are mostly found in trunnion-mounted ball valves. At low temperatures, elastomers become harder, less resilient, and lose their memory. For static seals, low-temperature tolerance is somewhat better, as there is no strong reliance on resilience needed. Under -29c service, lip seals are recommended (consequently, specifying ‘AED’).
It should be noted that in Australia Viton AED o-rings are being specified carte blanche in all sizes and classes even in standard sweet service at standard temperature and even for floating balls. Even Shell Oil company only specifies AED o-rings for class 600 and above in their trunnion valves. Class 150 and 300, especially in standard service at normal temperatures the phenomenon does not occur nor does it occur even in 900, 1500 class valves, floating ball valves at normal temperatures in smaller sizes up to 100NB.
Also, floating ball valves often contain only one static backup stem seal that is less affected, and floating ball valves don’t normally have dynamic seat o-rings.
Constituents requiring detailed attention are water, methanol, glycol, amines, ammonia CO2 and H2S. When relatively small and/or molecules migrate into the open polymer structure or elastomer, swelling occurs. Numerous other elastomer ED resistant grades are available such as Aflas®, East-O-Lion 985® (HBNR), etc., depending on service, temperature, etc.
A serious high-pressure constraint exists in gaseous, or volatile services when light components in the fluid diffuse into the elastomer over time and expand in the matrix upon rapid decompression before they can diffuse out again. The effect is called Explosive Decompression (ED) and it appears at particularly low pressures when CO2 or H2O is present.
Anti-Explosive Decompression (AED) Seals
AED seals and AED O-rings are available from PPE in a range of elastomer material types including HNBR, FEPM (Aflas®), FKM, and FFKM under the brand names EnDura®, Perlast®, and Perlast® ICE.
In addition to Viton, another accepted o-ring material is HNBR, (which is inherently AED resistant). In 1500 class and above much more expensive lip seals are generally specified by major companies like Shell. However, as a minimum in larger sizes in trunnion valves nylon or PEEK backup rings are required immediately behind the Viton o-ring (a practice that Chinese design with Western badges don’t do).
Carbon dioxide service for example is an example of a service condition where ED-resistant o-rings are required for trunnion ball valves. Apart from the need to avoid liquid carbon dioxide becoming trapped in the hole in the ball, the designer should be careful in the choice of materials for the rest of the components from which a valve is made up.
Elastomers contain voids and rigid inclusions that are produced during manufacture. Fluids in contact with the material are absorbed and diffuse throughout the material. At high pressure the fluid remains as a liquid; when the pressure drops the fluid will expand to a gas which can cause mechanical damage such as extrusion and blistering and undergo rapid gas decompression, (RGD), often referred to as explosive decomposition, consequently ED resistant o-rings are required.
The problem with some gasket or seal materials is that of RGD (explosive decompression). For multiple decompression applications, where pressure is cycled up and down, cracks can form and grow at stresses much lower than the breakpoints. If the number of cycles is higher than the number of fatigue cycles to failure, then cracks will grow, and eventually, the material will fail.
Explosive Decompression Testing
PPE is a leading manufacturer and developer of anti-explosive decompression (AED) sealing solutions. PPE’s materials development laboratories, located in UK and Houston, house modern ED testing facilities for rubber in the industry.
The high-pressure test rigs are capable of pressurizing various seal geometries up to 13.8 MPa or 20,000 psi over any time period, any number of depressurization cycles, and at any temperature up to 250°C (482°F). The rigs can be used to test materials against various industry standards or perform custom testing to simulate actual field operations.
The test rigs at PPE are capable of testing to standards such as TOTAL GS PVV 142, NORSOK M710, NACE TM0297, and ISO 23936-2. The O-ring carrier inserts are interchangeable to accommodate various squeeze levels in face and piston geometries.
Related Tags :
Ten articles before and after
Spring Return Deadman Handle for Quarter Turn Valves – ex stock! | Zeco
Updated API Trim Chart & Applications | Zeco
AGA Approved, Firesafe Certified Ball Valves & Actuators ex stock | Zeco
Differencies between ISO 15848 and TA-Luft | Zeco
API6D, Testing Procedure & Double Block & Bleed versus Double Isolation & Bleed | Zeco
Australian Pipeline Valve – We’re certified! | Zeco
Large Trunnion Ball Valve History | Zeco
Tip of the day – 90 degree orientated Gate Valves | Zeco