The valves in piping systems control and direct fluid flow. Two of the most widely used types of control valves are plug valves and ball valves. Even though their purpose is similar, there are some key differences in how they function, their design, applications, and more. In this post, we’ll compare plug valves vs. ball valves so you can determine which is the better option depending on your needs.
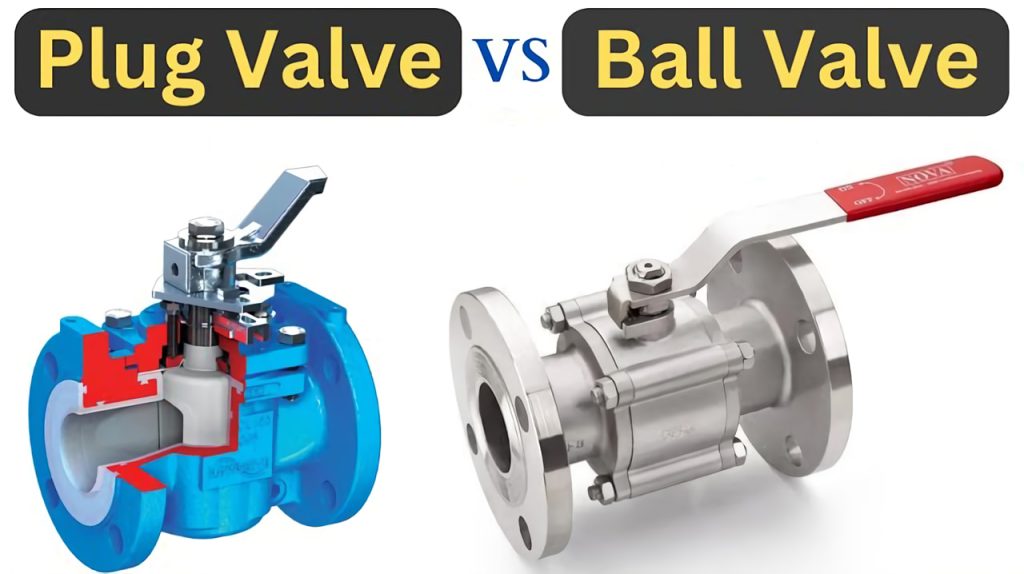
How Plug Valves And Ball Valves Regulate Flow
Both plug valves and ball valves operate with a 90-degree turn to open or close. This makes them “quarter-turn valves.” Their main purpose is for quick on/off flow control and sealing, not for throttling or regulating flow rates.
Plug Valve Design And Operation
A plug valve uses a tapered or cylindrical plug with a bored passageway to control flow. When open, the passageway aligns with the inlet and outlet ports in the valve body, allowing unrestricted flow. When closed, the plug is rotated 90-degrees, blocking the ports with the solid part of the plug to stop flow.
Plug valves come in lubricated or non-lubricated varieties:
- Lubricated: Have an oil chamber to lubricate the plug’s movement. This reduces friction and wear. Used in higher pressure and temperature applications.
- Non-lubricated: Rely on a sleeve lining instead of oil. Typically for lower pressure uses where lubricant contamination is a concern.
Ball Valve Design And Operation
Ball valves also use a bored disc (a ball) to regulate flow, but its operation is slightly different. The spherical ball has a bore through the middle and rotates 90-degrees inside the valve body to align or block the inlet and outlet ports.
Ball valves have a range of configurations depending on factors like bore size, body type, ball mounting, and number of ports. Common varieties include:
- Full port: Oversized ball so flow path matches pipe diameter.
- Reduced port: Smaller ball and flow path.
- Floating ball: Ball floats between inlet and outlet.
- Trunnion: Ball is fixed on a pivot point.
Key Differences Between Plug Valves And Ball Valves
Now that you know the basics of how they work, let’s look at some key differences between plug valves vs. ball valves when it comes to performance, design, cost, maintenance, and applications.
Sealing Ability
Plug valves generally seal better than ball valves. The plug’s larger surface area enables a tighter seal, but requires higher torque to operate. Ball valves compensate through materials and injection seals.
Ease Of Operation
Ball valves are easier to operate. Their balls are lighter weight compared to plug valves and don’t need as much torque to rotate and seal. This allows smoother opening and closing.
Durability And Longevity
Ball valves tend to last longer. The high torque wear on plug valves leads to shorter average lifespan. Ball valves also have less contact with fluids thanks to protective seats and seals.
Size And Scalability
Ball valves come in a wider range of sizes, with large scale ball valves easier to produce than large plug valves. It’s common to find ball valves over 24 inches, whereas large plug valves are rare.
Customization
Ball valves enable more customization, like adding Sloven ports, multi-port configurations, and special linings or ball materials. Complex custom plug valves aren’t really an option.
Cost
Plug valves are generally cheaper than ball valves. Their simple single-piece bodies reduce manufacturing complexity compared to some ball valve types.
Ball Valve Vs. Plug Valve Applications
Let’s look at where plug and ball valves are best used based on their traits:
Where To Use Plug Valves
Corrosive fluids – Can be fitted with protective sleeve linings for chemical resistance. The tight seal also prevents seepage damage.
Higher sealing demands – The large sealing surface makes them well-suited for applications that require a bubble-tight shutoff. For example, natural gas pipelines.
Abrasive media – Can effectively cut off the uncontrolled flow of abrasives like slurries. The smooth contours prevent buildup.
Frequent on/off operation – Repeated cycling doesn’t affect sealing as rapidly as ball valves thanks to the simpler single-piece body and absence of ball injection mechanisms.
Cost-conscious applications – Affordable price point makes them appealing for commercial applications where extreme pressures/temperatures aren’t a factor.
Where To Use Ball Valves
Higher & lower pressure extremes – Available in class ratings up to 4500 psi and pressure-assisted seat designs for effective sealing at high and low pressures. Can handle cryogenic temperatures or superheated steam lines.
Frequent throttling – The spherical shape of ball valve ports causes less wire draw damage from velocity changes compared to plug valves during throttling.
Higher flow capacity – Full port ball valves match pipe diameter to avoid constriction. This enables them to handle higher flow rates than same size plug valves.
Easy maintenance – Ball valves like three-piece or top entry models allow servicing without removing from the pipeline. Their rebuildable seats simplify maintenance. Plugs require full valve replacement.
Automation – Compact shape, light operation, and range of actuation methods make ball valves perfect for automated on/off control.
How To Choose Between Ball Valves & Plug Valves
Here are a few key points that can help guide your decision when choosing either a plug valve vs. ball valve:
- Sealing & regulation – If bubble-tight shutoff is critical, plug valves are the way to go. For throttling applications, opt for ball valves.
- Frequency of operation – Plug valves handle more frequent cycling. Use ball valves for simpler on/off tasks.
- Operating conditions – Select lubricated plug valves for high temp needs. Lean towards ball valves for extreme low and high pressures.
- Fluid properties – Plug valves suit corrosive, polymerizing, or solid-laden fluids. Ball valves work for clean services.
- Maintenance factors – Plug valves permit fast seal replacements. Ball valves simplify in-line strainer cleaning.
- Budget – Plug valves win for cost-effectiveness. Spend more upfront on better built ball valves to save over the long-run.
Carefully evaluating the fluid, pressure parameters, flow control needs, longevity expectations, and budget for your application allows for the optimal plug vs ball valve selection. And consulting an application engineer never hurts!
I hope this plug valve vs. ball valve comparison has given you the details needed to determine which type of valve better suits your specific needs. Both plug and ball valves play vital roles across an array of industrial uses, with their relative advantages and disadvantages coming into play depending on the situation. If you have any other valve questions, let me know in the comments!