When it comes to controlling fluid flow in industrial piping systems, few pieces of equipment are as essential as valves. But with globe valves and ball valves to choose from, how do you know which type of valve is best for your specific application?
In this comprehensive guide, we’ll compare the key differences between these two indispensable flow control devices. We’ll look at how they work, their pros and cons, typical applications, and everything else you need to determine whether a globe valve or ball valve makes more sense for your system.
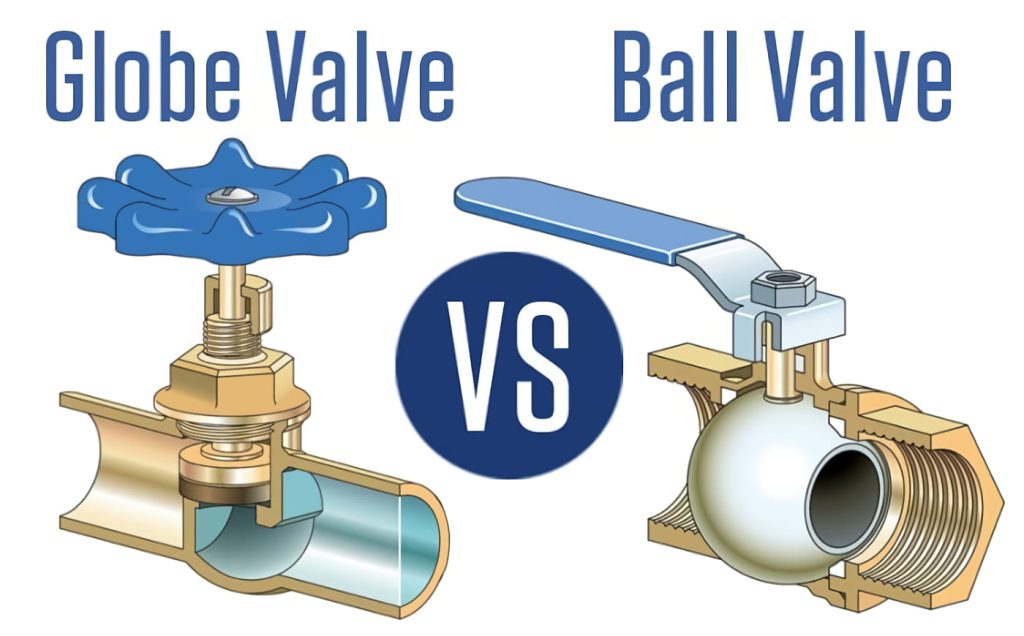
How a Globe Valve Works
A globe valve uses a movable disc or plug attached to a threaded stem to regulate fluid flow. As you turn the handwheel on top, the plug lowers onto the seat, restricting flow more and more until it’s completely closed.
Because the disc sits parallel to the direction of flow, globe valves allow for precise throttling. You get a nice linear flow rate—the farther you lift the disc from the seat, the higher the volume passing through the valve body.
This makes a globe valve perfect for applications like modulating flow to a boiler or accurately controlling flow rate to a piece of equipment.
Globe valves do cause a relatively high pressure drop since fluid must change direction to pass through them. The body is also larger than other valve types. But they make up for these minor drawbacks by providing superior throttling accuracy.
Globe Valve Benefits
There are a number of benefits that make globe valves a staple of industrial piping systems:
- Precise throttling capability – Allows accurate flow control by raising/lowering plug.
- Reliable leak-free closure – Tight mating of plug and seat prevents internal leakage.
- Handles high pressure applications – Up to hundreds of PSI depending on materials and design.
- Variety of configurations – Tee, angle, and wye patterns allow flexibility.
- Bidirectional flow potential – Some globe valve designs allow flow in both directions.
These benefits make globe valves well suited to applications like boilers, heat exchangers, chemical plants, process piping, and other industrial uses requiring accurate flow control.
How a Ball Valve Works
Rather than using a rising plug, a ball valve utilizes a bored-out ball that rotates on its axis inside the valve body to regulate flow. When the lever is parallel with the pipe, the hole lines up with flow and the valve is open. At 90 degrees, flow is blocked.
Ball valves operate almost exponentially—flow increases drastically once the tiniest part of the hole is revealed. So while they make for quick, easy on/off control, they don’t allow the fine throttling that globe valves provide.
The compact package does come with very low pressure drop since there’s nothing obstructing flow when it’s fully open. For relatively low cost, you also get exceptional cycle life and the ability to handle high temperatures.
When to Use a Ball Valve
There are certain applications where a ball valve really shines:
- Frequent on/off operation – 90 degree operation allows for rapid cycling.
- Low-pressure drop required – Unobstructed straight-through flow when open.
- Chemically aggressive fluids – Can be specified with exotic alloys.
- High temperature applications – Rated for hundreds of degrees with proper materials.
- Quick isolation required – Fast 1/4 turn operation stops flow immediately.
This makes ball valves well suited for uses like steam systems, chemical plants, air lines, tank drain service, and other on/off applications.
Globe Valve vs. Ball Valve Comparison
Now that you know the basics of how they operate, let’s take a closer look at some specific areas of comparison between globe and ball valves:
Throttling Ability
Since globe valves operate by raising and lowering a plug, they allow excellent throttling rangeability from 100% open down to almost closed. Ball valves can’t provide the same accuracy due to their exponential flow characteristic.
Winner: Globe valve
Pressure Drop
The straight through-flow of an open ball valve results in very little loss. Globe valves require fluid to change direction so have higher drops.
Winner: Ball valve
Cost
Ball valves are generally less expensive than comparably sized globe valves thanks to their simple, compact components.
Winner: Ball valve
Reliability & Durability
A ball valve’s simplicity generally equals exceptional cycle life with little maintenance. More complex globe internals may require occasional work.
Winner: Ball valve
Size
Compact ball valve designs take up far less space than bulky globe valve bodies.
Winner: Ball valve
Bidirectional vs. Unidirectional
Many globe valves can only flow in one direction. Ball valves handle bidirectional flow without issue.
Winner: Ball valve
Areas of Comparison Between Globe and Ball Valves
- Throttling ability
- Pressure drop
- Cost
- Reliability and durability
- Size/space requirements
- Bidirectional vs. unidirectional flow
When you weigh all factors, globe valves are the best choice when accurate flow control is needed since nothing can match their throttling accuracy.
Ball valves excel when an economical on/off valve is required thanks to fast cycling, low pressure drop, and compact form factor.
Typical Globe Valve Applications
Thanks to their precise throttling capabilities, you’ll often find globe valves installed in applications like these:
- Hot water or steam boilers – Precisely match boiler firing rate to load.
- Chillers – Modulate refrigerant flow to tune cooling capacity.
- Chemical injection systems – Control additive rate.
- Custody transfer processes – Ensure accurate flow measurement.
- High-pressure fluid transport – Reliable shutoff and low leakage.
Typical Ball Valve Applications
With their rapid on/off operation, exceptional cycle life, and low pressure drop, ball valves excel in these types of installations:
- Steam tracing lines – Quickly cut off flow without water hammer.
- Chemical plants – Economical, long lasting valves even with exotic alloys.
- Batch processing – Rapidly switch flows from tank to tank.
- Air systems – Fast, reliable isolation of branches and mains.
- Fuel supply lines – Immediate safety shutoff if needed.
Choosing Between a Globe or Ball Valve
When deciding between a globe or ball valve for your application, the most important factor is whether you need accurate throttling capability or just a basic on/off valve.
If precision flow control is critical – like in a boiler or mixing operation – a globe valve is by far the best choice.
For simple shutoff applications, an economical ball valve likely makes more sense.
Beyond that, also consider pressure drops, reliability requirements, operating temperatures, frequency of cycling, and installation space restrictions.
Weighing all these areas of comparison will lead you to the right flow control solution!