When designing or maintaining industrial piping systems, you’ll inevitably need to install valves for controlling fluid flow. The two most common types of valves are globe valves and gate valves. At first glance, they may seem interchangeable. However, there are important differences in how globe valves and gate valves are constructed, as well their advantages and best use cases.
In this comprehensive guide, we’ll compare globe valves vs gate valves across a number of factors. By the end, you’ll know exactly when to choose a globe valve vs a gate valve based on your specific needs.
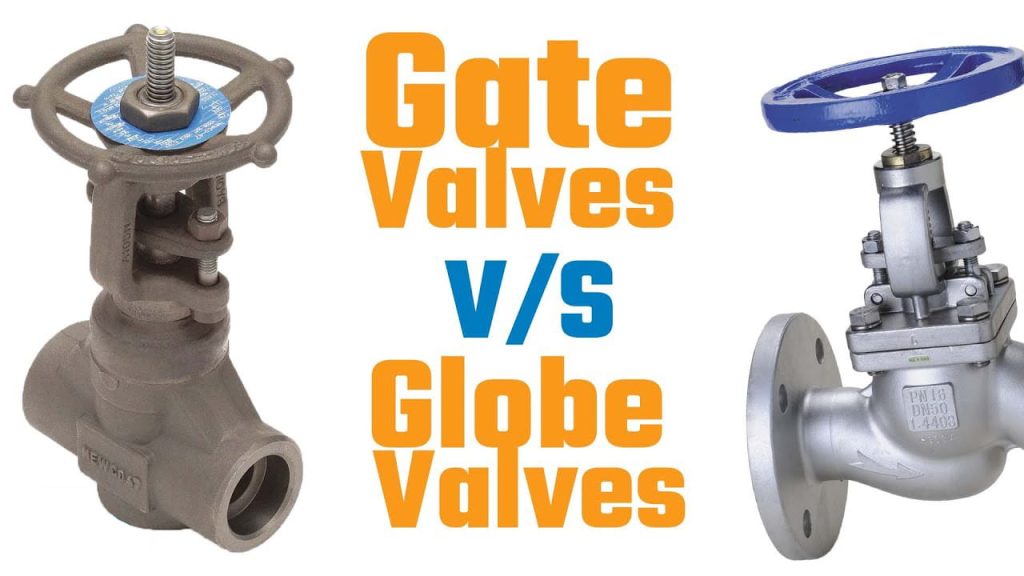
What Is A Globe Valve?
A globe valve uses a spherical body design and a plug-shaped disc connected to a rotating stem to regulate fluid flow. As you turn the valve stem and lift the disc, it allows more fluid to pass through. This makes globe valves excellent for precision flow control.
Globe valves are part of the linear motion valve family – the disc and stem move up and down in a straight line to modulate flow. This is different from quarter-turn valves like ball valves or butterfly valves where the mechanism spins 90 degrees between fully open and closed.
Within the body, globe valves have a baffle that diverts fluid flow sideways before reaching the seat where the plug makes contact. This diversion is what enables globe valves to throttle flow so effectively. However, it also introduces significant pressure drops through the system.
Globe valves really shine where precise regulation of flow is critical. You’ll often find them in applications like:
- Steam systems
- Refineries
- Chemical processing plants
- Water treatment facilities
They also Suit high pressure, extreme temperatures, viscous fluids, and hazardous chemicals where tight shutoff and minimal leakage is vital.
What Is A Gate Valve?
Gate valves operate by lifting/lowering a flat “gate” into the flow stream to start and stop fluid flow. In the fully open position, gate valves offer very little resistance or turbulence since the gate is fully lifted from the flow stream.
Gate valves are also linear motion valves, with the gate/stem oriented horizontally across the pipe diameter. Models with rising stems indicate valve position through stem travel. Non-rising stems use a small sliding indicator threaded onto the upper stem.
Gate valves make excellent on/off valves thanks low pressure drops when open combined with tight shutoff when closed. This makes them well suited for:
- Isolating zones in fluid networks
- Starting/stopping flow to large-bore pipe sections
- Any application where pressure loss must be minimized
They don’t work well for throttling since the partly-open gate can vibrate excessively and lose alignment with the body seats if exposed to high-velocity fluids.
Head-To-Head Globe Valve vs Gate Valve Comparison
Now let’s directly compare some of the key differences between globe and valves valves:
Functionality
- Globe Valves: Designed for flow regulation & control. The plug/seat interface enables reliable throttling without seat erosion.
- Gate Valves: Either fully open or fully closed. Cannot accurately regulate flow since the gate vibrates readily in partially open states.
Pressure Drop
- Globe Valves: Much higher pressure drop since fluid is diverted within the body. Avoid where pressure loss is critical.
- Gate Valves: Very low pressure loss thanks to unobstructed, straight-through flow path.
Sealing Reliability
- Globe Valves: Extremely effective sealing and isolation thanks to rugged body/plug interface and linear contact.
- Gate Valves: Prone to leakage over time as body seats erode. Gate can lose alignment and fail to fully isolate.
Maintenance Requirements
- Globe Valves: More intricate internal construction with small clearances leads to higher maintenance workload.
- Gate Valves: Larger internal voids simplify maintenance. However, higher seat wear means more teardowns for seat replacement.
Installation Considerations
- Globe Valves: Require allowance for vertical space due to lifted stem/actuator. Orient so flow matches arrow on body.
- Gate Valves: Rising stem variants need more overhead clearance than non-rising designs. Suitable for horizontal or vertical installation.
Typical Cost
- Globe Valves: Often 30-50% higher cost than equivalent gate valves.
- Gate Valves: Greater simplicity equates to lower production costs.
Below is a comparison table summarizing the key differences:
Factor | Globe Valve | Gate Valve |
---|---|---|
Primary function | Flow control & throttling | Isolation & on/off control |
Pressure drop | High | Low |
Sealing reliability | Extremely good | Moderate |
Maintainability | Difficult | Easy |
Installation | Vertical orientation. Flow direction fixed | Any orientation. Bidirectional |
Unit cost | Expensive | Cheap |
When Should You Choose A Globe Valve Over A Gate Valve?
With an understanding of their respective strengths and weaknesses, we can recommend the best applications suited to globe and gate valves.
Choose Globe Valves When:
Precision flow control is needed
The globe valve’s throttling ability makes it the go-to choice for accurately regulating fluid flow. Applications like metering chemical additives, managing steam, or maintaining process temperatures rely on globe valves fine control.
Minimal leakage is critical
Globe valves achieve superb isolation by fully surrounding the plug disc with metal. This makes an excellent pressure seal to prevent drips or leaks. If you absolutely cannot tolerate spills or emissions, install globe valves.
The system involves hazardous fluids
Corrosive chemicals, flammable liquids, extreme temperatures/pressures – globe valves are right at home. Their rugged construction stands up to practically any media with reliable containment and utter dependability.
Installing on vertical lines
Globe valves must be mounted with the flow matching the molded arrow on the body. This requirement matches nicely with vertical pipe. Orient so flow moves upwards through the valve.
Frequent operation is needed
The globe valve’s linear plug action provides smooth movement with little wear. Their rugged construction handles constant cycling far better than the sliding gate motion of gate valves.
Choose Gate Valves When:
Pressure loss must be minimized
Gate valves fully withdraw from the flow path when open, leaving an unrestricted, full-bore passage. This characteristic makes them perfect for allowing maximum flow volumes.
Occasional isolation is needed
Most gate valve applications involve relatively infrequent on/off operation. Their tight shutoff when closed makes reliable isolation valves for maintenance bypass duties or equipment isolation.
Installing on large-bore pipes
The gate valve’s straight-through flow path and absence of internal obstructions allows larges pipes to realize full flow potential. They also seal reliably despite the greater forces exerted by high-volume flow.
The process involves slurries
Gate valves better accommodate liquids with suspended solids like wastewater or chemical slurries. Their straight-through bores allow particles through without clogging nor eroding the seats prematurely.
The application is bidirectional
Gate valves suit bidirectional flow well thanks to their symmetrical body and flow path. Check that your specific model allows bidirectional flow before installing.
Cost is a major concern
If sticking to a tight budget, gate valves shave a good 30% off the price tag associated with globe valves. Just be prepared to sacrifice precision flow control capability.
Conclusion
Globe and gate valves both serve important duties handling flow control, isolation, and containment across a vast array of industrial processes. Understanding their fine differences in controlling characteristics, maintenance needs, pressure handling, and cost profile allows engineers to select either with confidence.
Reach for globe valves when accuracy, safety, and reliability outweigh budgets. Utilize economical gate valves for easier flow tasks not demanding precision.
Through careful globe vs gate valve selection, you can build fluid systems with the exacting performance your application requires!