Forging and casting are two very different manufacturing methods. When something is cast, the material is heated above its melting temperature and poured into a mold where it solidifies. When something is forged it is physically forced into shape while remaining in a solid state – although it is frequently heated.
Forging is Stronger than Casting.
One of the main reasons we choose to provide forging services is that it provides a stronger end product for our partners. According to a study performed by the Industrial & Manufacturing Engineering Department at the University of Toledo:
- Forged parts had a 26% higher tensile strength than the same cast parts.
- Forged parts had a 37% higher fatigue strength resulting in a much longer lifespan than cast parts.
- Cast iron only had 66% of the yield strength of forged steel, a measurement that indicates the load amount metal can hold before deforming.
- The forged parts had a 58% reduction in the area when pulled to failure, compared to 6% reduction for cast parts. That means forge parts allow for much greater deformation before failure than cast parts.
Forged Steel vs Cast Steel
The casting process is preferred for:
- parts and components that would be too complex or expensive to manufacture by steel forging (example: large valve bodies);
- parts that have internal cavities;
- large sized parts (there are virtually no size limits in terms of the weight of the parts that can be produced with the casting process);
- parts in special alloys (some specific alloys are more difficult to forge than cast, for example, those with a high content of Nickel and Moly, which have considerable resistance to mechanical forces);
- parts requiring mass production and small lots.
The forging process is preferred for:
- parts requiring extremely high strength, toughness, and resistance (indeed, during the forging process the steel grain structure gets modified to conform to the shape of the final product – with high uniformity of composition and metallurgical recrystallization);
- parts that have to withstand stronger impacts and mechanical forces;
- parts where porosity, the risk of a gas void, pockets, and the possible formation of cavities (even micro-granular) are not acceptable;
- production of mechanically strong parts without using expensive alloys;
- parts that require high wear resistance;
- parts subject to high loads and stress;
- high-end applications when the integrity and the quality of the part are the main objectives in the production process, rather than time and cost.
Forged Steel Ball Valve vs Cast Steel Ball Valve
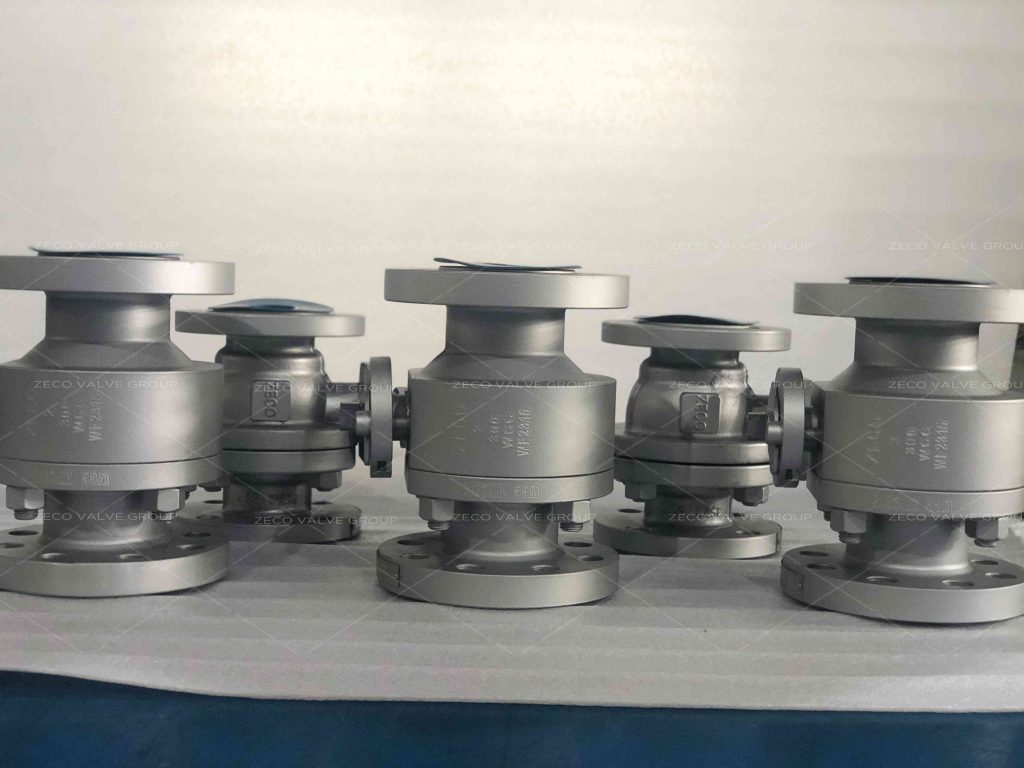
Cast steel ball valves are ball valves formed by pouring liquid into a mold and allowing it to solidify. Alloy steel is the most common casting material. Cast steel is divided into cast carbon steel, cast low alloy steel, and cast special steel. Cast steel refers to steel castings produced by casting methods. Cast steel is mainly used to make parts with complex shapes that are difficult to forge or cut and require high strength and plasticity.
Forged steel ball valves are made of forged steel and forgings by the forging process. Forged steel ball valves are stronger than cast steel ball valves and can withstand larger impact forces. Its plasticity, toughness, and other mechanical properties are also higher than castings, so for some important mechanical parts, should use forged steel parts.
Casting is liquid forming while forging is a plastic deformation process. The internal structure of the forged workpiece is improved, the mechanical property is good, the grain is uniform, and it is the best choice for important heavy-duty parts. Casting may cause structural segregation and defects, but casting has its own advantages. The forming of complex parts is not easily accomplished by forging, in which case the casting process is more advantageous.
Related Tags :
Ten articles before and after
How Does a Butterfly Valve Work – Zeco Valve
Difference Between Double Offset and Triple Offset Butterfly Valve – Zeco Valve
Introduction of V-type Ball Valves
Top 5 Butterfly Valve Manufacturers in the USA – Zeco Valve
Difference Between Ball Valve and Butterfly Valve – Zeco Valve