In the vast world of industrial applications, selecting the correct valve can make a significant difference in your system’s efficiency and performance. Two commonly used valves in various industries are globe valves and gate valves. Despite their seeming similarities, these two have distinct characteristics making them suitable for diverse scenarios. By understanding their individual traits and differences, you can choose the appropriate valve for your specific needs. Let’s dive into the details!
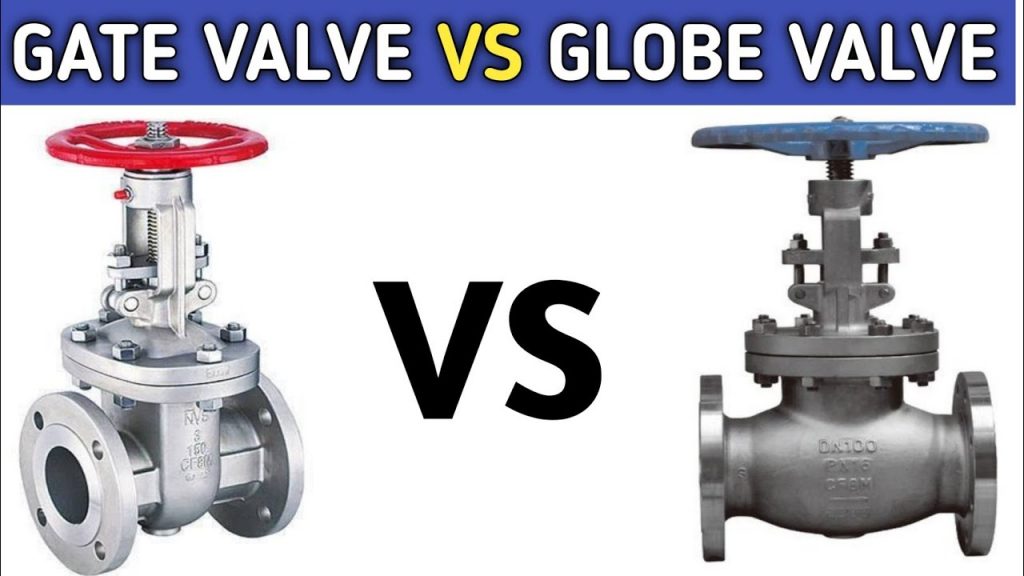
Globe Valve
Definition and Function of a Globe Valve
A globe valve is an integral component in any fluid control system. It gets its name from its spherical body shape which houses a movable disk or plug and a stationary seat. The unique construct allows precise fluid flow regulation by lifting or lowering the disk.
Construction and Design of a Globe Valve
Globe valves boast a more complex design than gate valves – sporting several components such as body, bonnet, disk, stem, seat, and packing. Their bodies come in cylindrical or spherical shapes, with the disk connected to a stem that controls flow regulation.
Applications and Uses of Globe Valves
Given their throttling capabilities and precise flow control attributes, globe valves find extensive usage across industries like water treatment systems, oil pipelines, HVAC systems, chemical processing plants, etc. They’re also well-suited for handling high temperatures and pressures.
Gate Valve
Definition and Function of a Gate Valve
Gate valves are essential in controlling fluid flow using a barrier-like gate disc that lifts up or down as needed. With this movement mechanism, they provide full open or closed positions achieving effective isolation or free-flow conditions.
Construction and Design of a Gate Valve
Gate valves typically feature either wedge-like or parallel gate discs stationed between two seats allowing perpendicular movement to fluid flow direction – offering either full shut-off capability or full flow when lifted.
Applications and Uses of Gate Valves
From oil refineries to sewage treatment plants – gate valves are versatile players effectively regulating fluid flow across industries due to their superior isolation functionality.
Globe Valve vs Gate Valve: What are the Differences Between Them?
Differences in Function & Application
Comparing functionally between globe & gate valves brings out some key contrasts:
- Flow Regulation: While both offer efficient shut-off/optimal-flow control features; globe valves offer a finer level of regulation compared to gate ones.
- Pressure Sealing: Understanding pressure changes within your system is critical while selecting between these two; with globe ones suited better for scenarios where pressure changes aren’t drastic but need throttling capabilities.
Differences in Structure & Design
The structural comparison shows stark differences:
- Body Shape: As names suggest – A ‘globe’ valve mimics the earth’s shape while a ‘gate’ one offers a linear design.
- Disc Movement: Disc movement differs too! In globe types, it’s perpendicular providing effective shut-off whereas it’s parallel in the case of gate types enabling full-flow/shut-off.
Differences in Operation
Operational differences become apparent considering on/off controls & mechanisms:
- On/Off Control: While both achieve this primary aim; only globe ones extend functionality by offering throttling (flow-rate control).
- Mechanisms: Both use different mechanisms – while ‘globe’ employs stem-actioned disc/plug movements for operation; ‘gate’ uses linear stem-action raising/lowering its disc along with media-flow direction.
Advantages & Disadvantages
Every coin has 2 sides! Globes provide tight-seal solutions but suffer higher pressure drops & form complex structures compared to gates which offer simplicity at the cost of lower durability & inability to regulate flows.
When choosing remember – application requirements (pressure changes/flow regulations), material compatibility (with other components), size considerations (valve size required), pressure-rating capacity (to withstand necessary levels) along with budget constraints play key roles!
Conclusion
After examining all aspects we realize – each valve type serves unique purposes! Globes cater better if you require finer controls over rate-of-flows while gates excel at providing complete shut-offs / opens without much resistance! It pays off consulting industry professionals before finalizing your choice based on your specific needs!
FAQs
Use a globe valve when you need precise control over fluid flow rates–they allow for fine adjustments due to their construction design.
Yes! Gate Valves can be regularly used especially when complete isolation/full-fluid flows are required–they perform excellently under such conditions!
A gate valve generally causes a lesser pressure drop compared to a globe one because it doesn’t obstruct the pathway completely like the latter when opened fully.
Typically not advisable! Due to their design, they’re not ideal for achieving precision control over flow rates like globes.
Generally speaking–globes tend toward higher durability than gates due mainly because the latter is more prone to leaks over prolonged usage times.
To sum up–whether you’re leaning towards globes with fantastic throttling capabilities yet greater complexity & high-pressure drops OR gates offering simplicity alongside lower-pressure drops but lacking precision controls; it’s all about finding what fits best within your specific application requirements after balancing benefits against drawbacks wisely! Happy plumbing!