Water Gate Valve
The resilient seated water isolation gate valve of ZECO from China is widely used and reliable in the water supply and drainage system of water supply company, sewage company, and various industries in big cities of China. Established in 1991, at that time we are the only gate valve manufacturers in China, and it is the Chinese market to introduce and the earliest development and production of cast iron gate valve manufacturers, and already known in the field of water gate valve production for more than decades, although the market of other China gate valves are very common and the price is low, but the durability and reliability, we believe that our deep research and development and rich production experience are the foundations why we are trusted gate valve supplier of our customers.
Types of Gate Valve
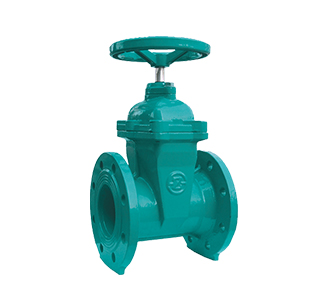
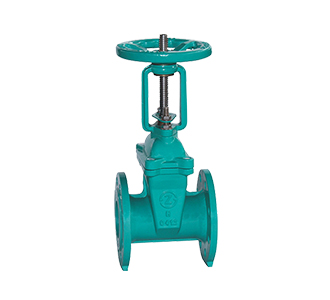
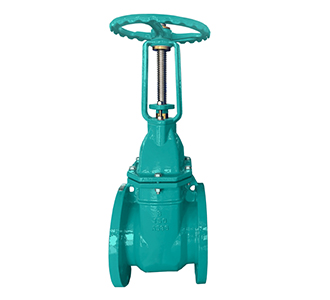
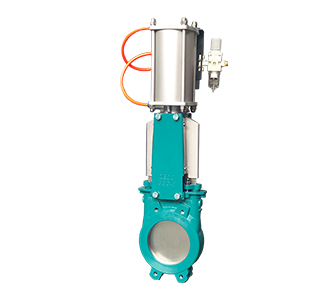
How Does a Gate Valve Work?
A gate valve is the most common valve for water supply systems. It represents a linear-motion isolation valve and has a function to stop or allow the flow. Gate valves got their name from the closure element sliding into the flow stream to provide shutoff and, therefore, acting like a gate. Gate valves are used to isolate specific areas of the water supply network during maintenance, repair works, new installations, as well as to reroute water flow throughout the pipeline.
Gate valves are normally operated by a handwheel, a valve T-key (wrench), or an actuator. The wheel is attached to a valve stem and transfers rotational energy to it. During the gate valve opening, the rotation of the handwheel turns the threads of the gate stem into the gate and vice versa for closing. This energy moves the gate valve wedge downwards or upwards. In underground gate valve installations, an extension spindle is attached, which allows operation without direct access to the valve itself.
Generally, gate valves are installed in the areas of a pipeline where they will longer remain open or closed, as they generally require some time to switch between these two positions. However, when the valve needs to be operated quite often or even remotely, motorized gate valves are used (i.e. equipped with an electric actuator).
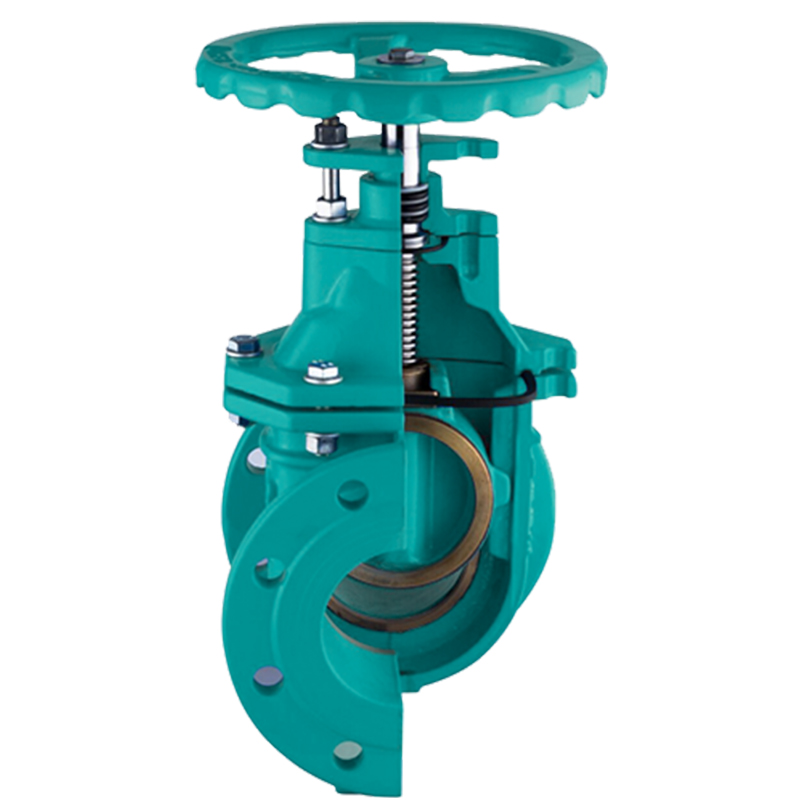
How to Choose the Right Gate Valve?
Choosing a sturdy and durable gate valve can reduce the cost of expensive replacement in the future. Here are some selection criteria:
Wedge design
The wedge is the sealing part of the gate valve, so it is very important.
Wedge nut: The wedge nut connects the wedge to the valve stem. There are two basic wedge nut designs; a loose wedge nut design in which the brass nut slides in a groove in the wedge core; and a fixed wedge nut design in which the nut expands in the wedge core. With the fixed wedge nut design, the number of movable parts is reduced, thus eliminating the risk of corrosion due to the damage of the rubber surface of the wedge core by the moving parts. Therefore, it is recommended to use a fixed wedge nut design.
Wedge guide plate and sliding shoe: When opening and closing the valve during pipeline operation, the wedge plate bears friction and pressure. The guide device on the wedge joint cooperates with the corresponding groove in the main body to help stabilize the wedge position during operation and ensure that the valve stem will not bend downstream due to the flow rate. The wedge-shaped track shoes help ensure that the rubber on the wedge-shaped surface does not wear out due to friction between the wedge and the internal rails. Make sure to fix the wedge on the wedge and make sure that the rubber layer under it is sufficient to prevent the wedge core from corroding.
Rubber: The wedge must be fully vulcanized with rubber, and the amount of rubber in the sealing area of the wedge is sufficient to absorb impurities in the valve seat, which is very important for the sealing of the valve. The strong bond between the rubber and the wedge core is important to ensure proper sealing even when the rubber is compressed and to prevent creep corrosion even if sharp objects penetrate the rubber during closing of the valve.
Rubber quality
Rubber quality is critical to durability and valve function. Rubber must be able to withstand the continuous impact of impurities and chemicals without being damaged, and must be able to absorb small impurities in the valve seat to make it tightly sealed.
External corrosion protection
External corrosion protection is critical to the service life of the valve. It is recommended to use in accordance with DIN 3476 Part 1, EN 14901 and GSK
Tight structure
There are two important design issues:
Stem seal: The seal on the bonnet around the stem can maintain the pressure inside the valve/pipe. Stem seals should always be designed to be maintenance-free and should provide the service life of the valve or at least meet the service life requirements of EN 1074-2. The main seal that maintains the internal pressure is best designed as a hydraulic seal, so as to achieve a tighter seal while increasing the internal pressure. The spare seal should be placed around the valve stem. In order to protect the seal from external contamination, a seal should be placed around the top stem. For safety and health reasons, high-quality EPDM rubber compounds approved for drinking water must be used in places in direct contact with drinking water.
Bonnet/body seal: The tightness between the bonnet and the valve body can be achieved by using a gasket embedded in the valve recess. This design ensures that the gasket remains in the correct position and will not be blown out due to pressure fluctuations. In order to protect the bonnet bolts from corrosion, the bonnet gasket should surround the bolts, and the bolts should be embedded in the valve in such a way that no threads are exposed.
General performance
When operating the gate valve through the handwheel or electric actuator, be sure to pay attention to the operating and closing torque.
Full bore: In order to be able to use pipeline cleaning equipment, the inner diameter of the valve should be consistent with the nominal size of the valve.