Ever wondered why ball valves are not used in steam service? You’re not alone.
Here’s the deal: Steam might seem simple on the surface, but it creates some of the most demanding conditions any valve can face. And while ball valves are rockstars in many applications, they often fall flat when it comes to handling steam.
In this comprehensive guide, I’m going to break down exactly why engineers and maintenance professionals think twice before installing ball valves in steam systems. I’ll cover everything from material limitations to performance issues that make these valves problematic in steam applications.
Let’s dive right in.
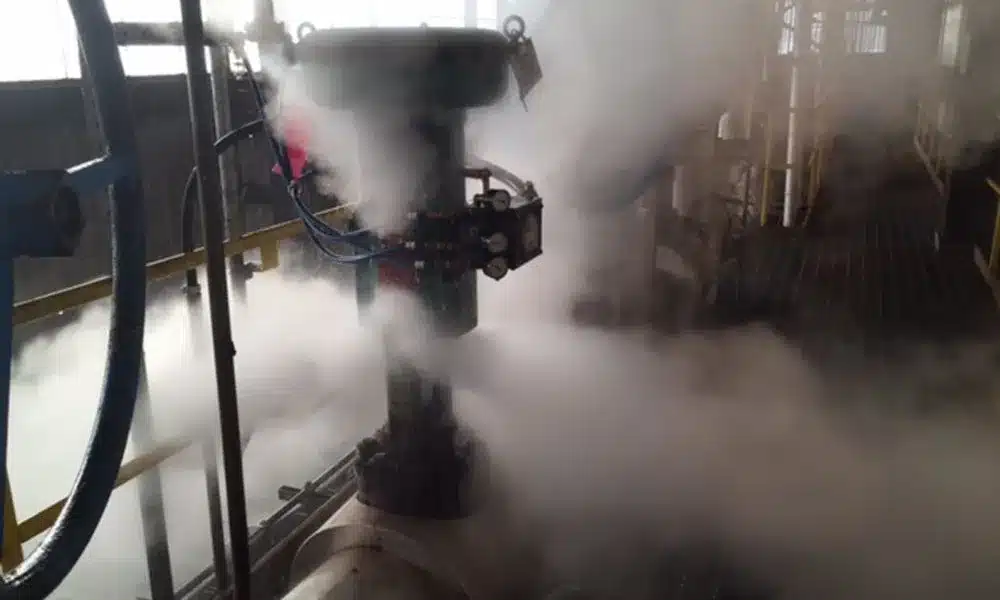
Table of contents
- The Extreme Conditions in Steam Systems
- Why Ball Valves Are Not Used in Steam Service?
- Steam Valve Alternatives That Actually Work
- Understanding Valve Materials for Steam Service
- Real-World Consequences of Using Ball Valves in Steam
- Best Practices for Steam Valve Selection
- The Bottom Line: Choose the Right Tool for the Job
- Conclusion
The Extreme Conditions in Steam Systems
Before we get into the nitty-gritty of valve selection, we need to understand what makes steam such a challenging medium.
Steam systems aren’t playing around. They operate under conditions that push materials and components to their absolute limits:
- High Temperatures: Steam temperatures frequently exceed 250°C (482°F), with superheated steam getting significantly hotter
- High Pressures: We’re talking pressures up to 4 MPa (580 psi) or even higher
- Thermal Cycling: Systems constantly heat up and cool down, causing materials to expand and contract
- Phase Changes: Steam condenses into water under various conditions, especially during startup and shutdown
Think about it like this: a valve in a steam system is basically working inside a pressure cooker that’s constantly being turned on and off.
Why Ball Valves Are Not Used in Steam Service?
Now let’s get to the heart of the question: why ball valves are not used in steam service. There are several technical reasons that make ball valves problematic for steam applications:
1. Material Limitations Under High Temperatures
Standard ball valves typically use soft seat materials like PTFE (Teflon) or various elastomers. Here’s the problem: these materials don’t hold up well in extreme heat.
When exposed to steam temperatures:
- Soft seats deform and lose their shape
- Sealing capabilities deteriorate rapidly
- Material degradation accelerates dramatically
Let me put this in perspective. Most PTFE seats have a practical temperature limit around 180°C (356°F). But as we’ve seen, steam systems often operate well above 250°C (482°F). That’s like using plastic cookware in an industrial oven – it’s simply not designed for those conditions.
2. Thermal Expansion Issues
Ball valves contain multiple components made from different materials, each with their own thermal expansion rates. This creates some serious problems in steam service:
- Uneven Expansion: The ball (typically metal) expands at a different rate than the seats (typically polymers)
- Thermal Binding: The valve can become difficult to operate after thermal cycling
- Loosening Connections: Repeated expansion and contraction can loosen threaded connections
When a steam system heats up, these different expansion rates can cause the ball to bind against the seats. And when it cools down? You might get leakage as components contract unevenly.
3. Poor Throttling Performance
Here’s something many people don’t realize: ball valves are designed primarily for on/off service, not for throttling flow.
When you partially open a ball valve in a steam system:
- High-velocity steam creates erosion on sealing surfaces
- Flow characteristics are poor and unpredictable
- Pressure drops can cause localized flashing and cavitation
- Valve seats wear quickly, leading to leakage
In contrast, globe valves are specifically designed with throttling in mind. Their flow path and construction make them much more suitable for controlling steam flow rates.
4. Condensate Handling Challenges
Steam systems deal with condensate – the liquid that forms when steam cools. Ball valves aren’t great at handling this aspect:
- Water Hammer Risk: Ball valves close quickly, which can trap steam and cause dangerous water hammer effects
- Condensate Drainage: Their design doesn’t allow for proper condensate drainage
- Thermal Shock: When cool condensate hits hot valve components, it creates thermal shock that can damage the valve
Steam Valve Alternatives That Actually Work
If ball valves aren’t ideal for steam, what should you use instead? Let’s look at the alternatives that steam system experts actually recommend:
Globe Valves: The Steam System Champions
Globe valves have been the gold standard for steam service for decades, and for good reason:
- Superior Throttling: Their design provides excellent flow control characteristics
- Renewable Seats: Metal seats can be refurbished or replaced
- Better Heat Resistance: Can be made entirely of metals suitable for high temperatures
- Self-Draining Design: Helps prevent condensate buildup
The flow path in a globe valve forces the steam to change direction, reducing erosion while providing precise control – exactly what you need in a steam system.
Gate Valves for Full-Flow Applications
When you need minimal pressure drop in a full-open/full-closed steam application, gate valves offer significant advantages:
- Straight-Through Flow: Minimal pressure loss when fully open
- Metal-to-Metal Seats: No soft components to degrade
- Thermal Stability: Better handling of temperature fluctuations
- Positive Shutoff: Can provide tight closure when needed
Gate valves open slowly by design, which helps prevent water hammer – a serious safety concern in steam systems.
Specialized Ball Valves for Limited Steam Applications
Now, I should mention that specially designed ball valves can be used in certain steam applications, but they need specific features:
- Metal seats instead of soft seats
- Reinforced stem designs
- Special blow-out proof stems
- Anti-static features
- Live-loaded packing
These specialized steam ball valves cost significantly more than standard ball valves and still have limitations regarding throttling and service life.
Understanding Valve Materials for Steam Service
The materials used in steam valves play a crucial role in their performance and longevity. Let’s break down what works and what doesn’t:
Body Materials
For steam valve bodies, these materials stand up to the challenge:
- Forged steel
- Cast steel
- Stainless steel
- Ductile iron (for lower pressures)
Brass and bronze can work for low-pressure steam but aren’t recommended for industrial applications due to their reduced strength at high temperatures.
Seat Materials
This is where standard ball valves really fall short:
- PTFE/Teflon Seats: Begin to deform around 180°C
- Elastomer Seats: Generally fail below 150°C
- Metal Seats: Required for reliable steam service
Remember, steam temperatures commonly exceed 250°C. Standard ball valve seats simply can’t handle those conditions.
Stem and Packing Considerations
Steam valves require:
- Graphite-based or specialized high-temperature packing
- Corrosion-resistant stem materials
- Proper stem designs to handle thermal expansion
Standard ball valve stems and packing are rarely designed with these requirements in mind.
Real-World Consequences of Using Ball Valves in Steam
Let’s talk about what actually happens when standard ball valves are installed in steam systems:
Rapid Failure and Leakage
The most common outcome is premature failure:
- Seats deform and leak within weeks or months
- External leakage through packing occurs as materials degrade
- Valves become difficult or impossible to operate
Safety Concerns
Steam leaks are not just inefficient – they’re dangerous:
- High-pressure steam can cause severe burns
- Failed valves can create water hammer conditions
- Sudden releases of steam create hazardous environments
Maintenance Nightmares
Using the wrong valve type creates ongoing problems:
- Frequent replacement requirements
- Unplanned system shutdowns
- Increasing maintenance costs
- Lost productivity
Best Practices for Steam Valve Selection
If you’re designing or maintaining a steam system, follow these guidelines:
- Choose Valve Types Wisely:
- Use globe valves for throttling and control
- Consider gate valves for on/off service
- Only use specialized steam-rated ball valves when absolutely necessary
- Select Appropriate Materials:
- Verify temperature ratings of all components
- Ensure body materials can handle thermal cycling
- Confirm seat materials are suitable for steam temperatures
- Consider System Requirements:
- Properly size valves for the application
- Account for condensate handling
- Plan for thermal expansion in piping design
- Implement Proper Installation Practices:
- Install valves with stems in recommended orientation
- Use appropriate gaskets and bolting materials
- Provide adequate support to prevent piping stress
The Bottom Line: Choose the Right Tool for the Job
Selecting valves for steam service isn’t about brand preferences or initial cost – it’s about safety, reliability, and total cost of ownership.
Standard ball valves might be less expensive upfront and work wonderfully in many applications, but steam service demands specialized solutions. The consequences of choosing the wrong valve type include:
- Shortened valve life
- Frequent maintenance
- Safety hazards
- System inefficiency
- Higher long-term costs
In the world of steam systems, using the right valve is not just good engineering – it’s essential for safety and reliability.
Conclusion
So there you have it – a comprehensive look at why ball valves are not used in steam service. While specialized high-temperature ball valves do exist for specific steam applications, standard ball valves simply cannot handle the extreme conditions, thermal cycling, and flow control requirements of typical steam systems.
Globe valves and gate valves remain the preferred choices for steam applications due to their superior material compatibility, better flow characteristics, and longer service life under extreme conditions.
The next time you’re designing or maintaining a steam system, remember that valve selection is crucial. Choosing the right valve type isn’t just about following best practices – it’s about ensuring system efficiency, minimizing maintenance costs, and most importantly, maintaining safety.
Now I’d love to hear from you: Have you experienced issues with ball valves in steam systems? Or do you have questions about valve selection for specific steam applications? Let me know in the comments below!