Ever wondered why engineers get so specific about valve types?
It’s not just technical jargon. The right valve can make or break an entire system.
Today, I’m breaking down everything about globe valves – what they do, why they matter, and when you should use them.
What is the purpose of a globe valve? Globe valves primarily control flow with precision in fluid systems. Their design allows for excellent throttling capabilities, reliable shut-off functionality, and adaptability across various industrial applications requiring accurate flow regulation.
But that’s just scratching the surface.
Let’s dive deeper…
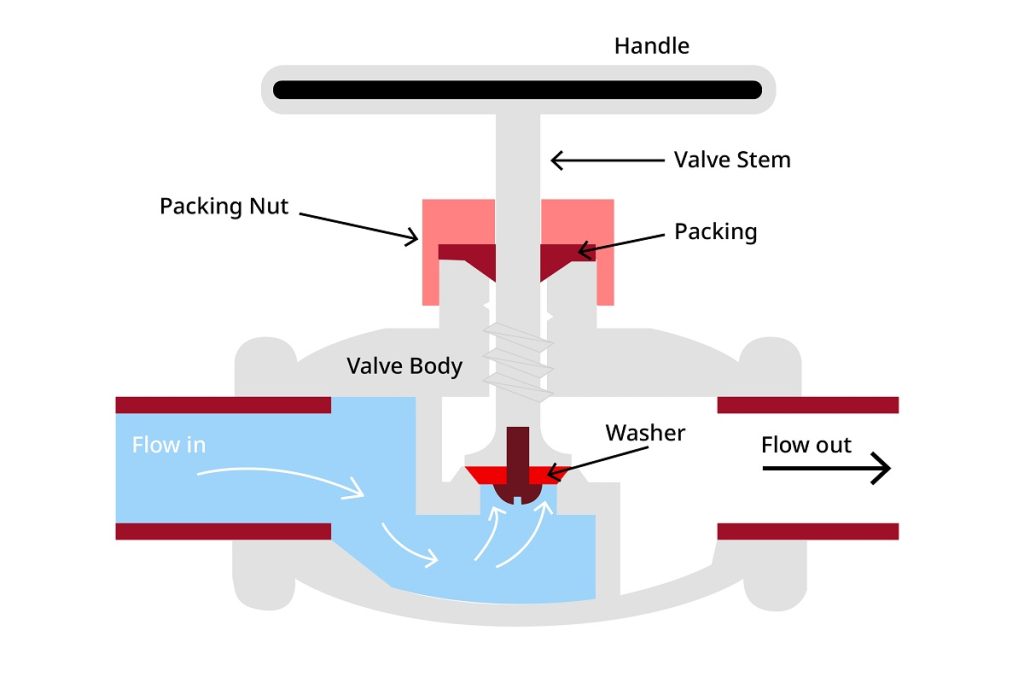
Table of contents
- What Exactly Is a Globe Valve?
- The 5 Primary Purposes of Globe Valves
- Types of Globe Valves (And When to Use Each)
- Industries That Rely on Globe Valves
- How to Select the Right Globe Valve
- Common Problems and Troubleshooting
- Maintenance Best Practices
- Globe Valves vs. Other Valve Types
- The Future of Globe Valve Technology
- Final Thoughts: Choosing Wisely
What Exactly Is a Globe Valve?
Before we jump into purposes, let’s get clear on what we’re talking about.
Globe valves get their name from their spherical body shape (though modern versions don’t always look like perfect globes).
Inside, they have a movable disk-type element and a stationary ring seat. When you operate the valve, the disk moves toward or away from the seat, controlling how much fluid passes through.
What makes them special? The flow path.
Here’s the key difference: In globe valves, fluid must change direction to flow through the valve. This creates resistance that’s perfect for controlling flow rates.
The 5 Primary Purposes of Globe Valves
Let’s get straight to the point. Globe valves aren’t just random components – they serve specific purposes in fluid systems.
1. Precise Flow Regulation
This is where globe valves truly shine.
Need to adjust flow to exactly 37% capacity? A globe valve can do that.
Their design allows for incremental adjustments, making them ideal for applications where you need to dial in exact flow rates. Think of them as the dimmer switch of the valve world, not just an on/off toggle.
2. Effective Throttling
Throttling means partially restricting flow through a valve – and globe valves are the kings of throttling.
The disk-to-seat design creates a variable restriction that remains stable even with pressure fluctuations. This makes them perfect for:
- Controlling system pressure
- Preventing water hammer
- Maintaining specific flow conditions
3. Reliable Shut-Off Capability
While not always the first choice for pure on/off applications (that’s ball valves’ territory), quality globe valves provide excellent sealing when closed.
The disk presses directly against the seat with significant force, creating a tight seal that prevents leakage – crucial in systems handling dangerous or expensive fluids.
4. Handling High Pressure Differentials
Here’s something interesting:
Many valves struggle when there’s a huge pressure difference across them. Not globe valves.
Their design naturally accommodates high pressure differentials, making them suitable for challenging environments like pressure reducing stations.
5. Bidirectional Flow Control
Depending on the specific design, many globe valves can control flow in either direction – a versatility that’s incredibly valuable in complex systems.
Types of Globe Valves (And When to Use Each)
Not all globe valves are created equal. The design variations directly impact their performance characteristics.
T-Pattern Globe Valves
These are what most people picture when thinking of globe valves. The stem and seat are arranged in a T shape relative to the pipe.
Best for: Throttling applications where precision control matters more than minimizing pressure drop.
Y-Pattern Globe Valves
In these valves, the stem is angled (typically 45°) relative to the pipe. This creates a more streamlined flow path.
Best for: Applications requiring lower pressure drop while still maintaining good throttling capability.
Angle Globe Valves
These combine the functions of a globe valve and an elbow fitting. The inlet and outlet meet at a 90° angle.
Best for: Systems where flow needs to change direction anyway, saving space and reducing the number of joints.
Needle Valves
Technically a subset of globe valves, needle valves use a long, tapered point (the “needle”) for extremely precise control of small flows.
Best for: Very fine flow adjustment in instrumentation, sampling, or laboratory applications.
Industries That Rely on Globe Valves
Globe valves aren’t just theoretical – they’re workhorses across major industries.
Oil and Gas
In refineries and processing facilities, globe valves control everything from crude oil flow to precise chemical injection rates.
The robust construction and precise control capabilities make them ideal for the demanding conditions in this industry.
Power Generation
Whether it’s a nuclear plant, coal-fired facility, or modern combined cycle plant, power generation requires exact control of steam, water, and various working fluids.
Globe valves handle the high temperatures and pressures while providing the control necessary for efficient and safe operation.
Water Management
Municipal water systems use globe valves for pressure regulation, flow control, and system isolation.
Their reliability and longevity make them ideal for infrastructure that needs to operate for decades with minimal maintenance.
Chemical Processing
When handling dangerous, corrosive, or valuable chemicals, precise control isn’t just about efficiency – it’s about safety.
Globe valves provide the necessary precision and can be constructed from materials compatible with aggressive media.
How to Select the Right Globe Valve
Choosing the right globe valve involves considering several crucial factors:
Flow Requirements
This is fundamental. What are you trying to accomplish?
- Need precise throttling? T-pattern valves excel here.
- Want to minimize pressure loss? Y-pattern designs are your friend.
Material Compatibility
The valve materials must be compatible with the process fluid. For example:
- Stainless steel trim works well for corrosive or high-temperature applications
- Bronze or brass for standard water service
- Exotic alloys for especially challenging environments
Pressure and Temperature Ratings
Your valve must be rated for the maximum pressure and temperature it will encounter. This is non-negotiable for safety and performance.
Matching the valve’s pressure class to your system requirements prevents leaks and failures.
Actuation Method
How will the valve be operated?
- Manual handwheels for infrequent adjustment
- Electric actuators for remote or automated operation
- Pneumatic actuators for faster cycling or intrinsically safe requirements
Common Problems and Troubleshooting
Even the best globe valves can experience issues. Here’s what to watch for:
Leakage Through the Seat
This typically indicates:
- Debris caught between disk and seat
- Worn seat or disk
- Improper closing torque
Solution: Cycle the valve fully open and closed to flush debris, or inspect and replace worn components.
Stem Packing Leaks
When you see leakage around the stem, it usually means:
- Packing is worn or compressed
- Improper packing installation
- Stem damage
Solution: Tighten packing gland bolts incrementally, or replace packing if tightening doesn’t resolve the issue.
Difficult Operation
Valves that are hard to operate might have:
- Damaged stem threads
- Insufficient lubrication
- Excessive process pressure
- Corroded components
Solution: Apply appropriate lubricant, check for mechanical damage, and ensure the valve is properly sized for the application.
Maintenance Best Practices
Want your globe valves to last? Follow these maintenance tips:
- Regular Cycling – Periodically operate valves that are normally fully open or closed to prevent seizing.
- Lubrication – Apply appropriate lubricant to stems and other moving parts according to manufacturer recommendations.
- Packing Adjustment – Check and adjust packing gland tension to prevent both leakage and excessive stem friction.
- Visual Inspection – Look for signs of corrosion, leakage, or damage during routine walkthroughs.
- Documented Maintenance – Keep records of all service to identify recurring issues and predict replacement needs.
Globe Valves vs. Other Valve Types
Globe valves aren’t always the right choice. Here’s how they compare:
Globe vs. Ball Valves
Ball valves offer:
- Quarter-turn operation (faster)
- Lower pressure drop when fully open
- Excellent sealing
But they can’t match globe valves for throttling precision.
Globe vs. Gate Valves
Gate valves provide:
- Minimal flow restriction when open
- Bidirectional sealing
- Simple design
However, they’re poor at throttling and typically larger/heavier than equivalent globe valves.
Globe vs. Butterfly Valves
Butterfly valves feature:
- Compact design
- Lower cost
- Quarter-turn operation
But they generally can’t handle the pressure differentials that globe valves can.
The Future of Globe Valve Technology
Valve technology isn’t standing still. Here’s what I’m seeing in the globe valve space for 2025 and beyond:
- Smart Valve Integration – Globe valves with built-in sensors and connectivity for real-time monitoring and predictive maintenance.
- Advanced Materials – New alloys and composites that extend service life in extreme conditions.
- Efficiency Improvements – Redesigned flow paths that maintain control capability while reducing energy losses.
- Environmental Focus – Zero-emission stem sealing and sustainable manufacturing processes to meet increasingly strict regulations.
Final Thoughts: Choosing Wisely
Globe valves are precision instruments that serve as the backbone of fluid control in countless industrial systems.
Their ability to regulate flow with precision, provide reliable isolation, and adapt to diverse operational conditions makes them indispensable across industries.
When selecting globe valves, remember to match the valve design to your specific application requirements. Consider flow characteristics, material compatibility, and pressure ratings to ensure optimal performance.
So, what is the purpose of a globe valve? It’s to give engineers precise control over fluid systems, enabling the safe, efficient operation of everything from oil refineries to water distribution networks, and countless processes in between.
Is there a specific application you’re considering a globe valve for? Let me know in the comments below!