Why water doesn’t flow back into your house from the sewer line? Or how fuel stays in your car’s engine instead of flowing back to the tank?
That’s all thanks to check valves—the unsung heroes of fluid systems everywhere.
What is the purpose of a check valve? In simple terms, check valves are designed to allow fluid to flow in one direction only while preventing backflow in the opposite direction. This one-way traffic control is crucial for everything from your home’s plumbing system to massive industrial operations.
But there’s a lot more to these seemingly simple devices than you might think.
In this definitive guide, I’ll break down exactly what check valves do, how they work, and why they’re so important across countless applications.
Let’s dive in.
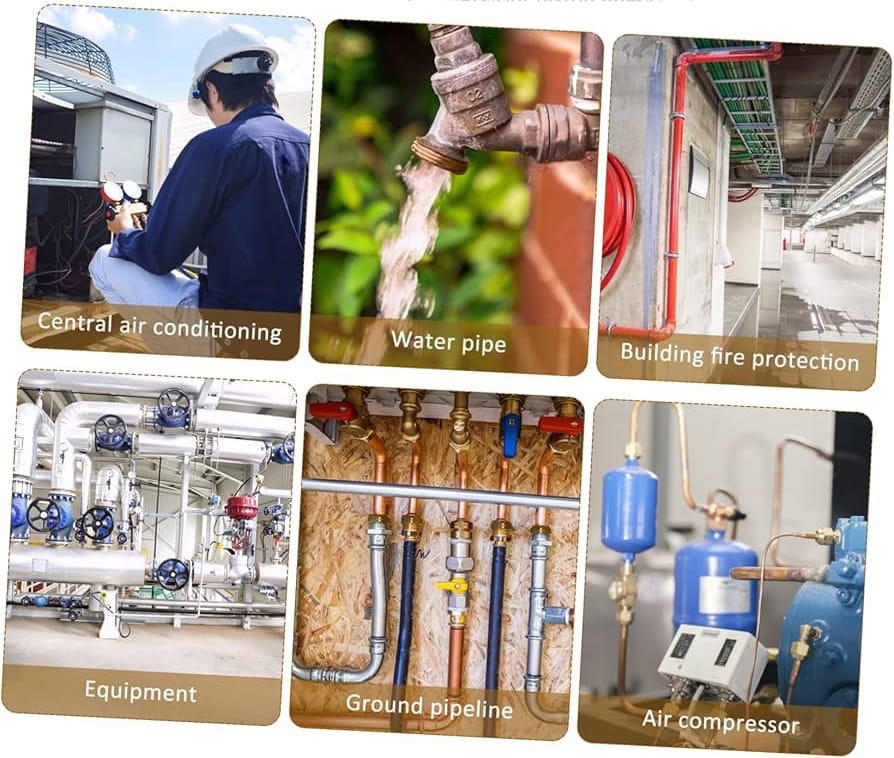
Table of contents
How Check Valves Work: The Basics
Before we go deeper into their purpose, you need to understand how check valves actually work.
Think of a check valve as a one-way door for liquids and gases. It opens automatically when fluid pushes in the “right” direction and slams shut when fluid tries to go the “wrong” way.
Here’s the cool part: check valves do this automatically, with zero electricity or manual intervention required.
Most check valves have these basic components:
- A valve body (the housing)
- An inlet and outlet
- A movable mechanism (like a disc, ball, or flapper)
- A seat (where the mechanism rests when closed)
When fluid pressure on the inlet side exceeds the outlet pressure, the valve opens. When pressures reverse or flow stops, the valve closes—often with the help of gravity, a spring, or reverse flow pressure.
The beauty is in the simplicity. No motors. No computers. Just physics.
The 5 Key Purposes of Check Valves
Now that you understand the basics, let’s explore why these valves are so important.
1. Preventing Backflow (Their Primary Job)
The number one purpose of a check valve is backflow prevention.
But why is backflow such a big deal?
Because reverse flow can cause serious problems:
- Contamination: In water systems, backflow could mean sewage or chemicals flowing back into clean water supplies
- Efficiency loss: In heating systems, backflow wastes energy by sending hot water where it’s not needed
- Equipment damage: In pumping systems, backflow can cause pumps to spin backwards, potentially damaging motors
In fact, preventing backflow is so important that many building codes and regulations specifically require check valves in certain applications.
2. Protecting Expensive Equipment
Think about a pump system pushing water uphill. When that pump shuts off, all that water wants to come rushing back down due to gravity.
Without a check valve, that water would spin your pump backward—potentially damaging bearings, seals, and the motor itself.
This protection extends to countless types of equipment:
- Pumps (all types)
- Compressors
- Boilers
- Pressure vessels
- Filters and strainers
A $100 check valve can easily save you from a $10,000 equipment repair. That’s what I call good ROI.
3. Maintaining System Pressure
Many systems need to maintain pressure even when pumps or compressors aren’t running.
For example, in a domestic water pressure tank system, the check valve keeps pressurized water from flowing back into the well when the pump shuts off.
This pressure maintenance is crucial for:
- Consistent water delivery
- Reducing pump cycling (which extends equipment life)
- Preventing water hammer effects
- Keeping gases compressed in storage
Bottom line? Check valves help systems stay pressurized without wasting energy.
4. Preventing Contamination
In certain applications, keeping fluids separated isn’t just about efficiency—it’s about safety.
This is especially important in:
- Municipal water systems: Preventing contaminated groundwater from entering clean water supplies
- Medical applications: Keeping medications flowing in the right direction
- Food processing: Ensuring product integrity and preventing cross-contamination
- Chemical processing: Keeping reactive chemicals separated until intended mixing
The one-way flow that check valves provide serves as a critical safety barrier in these sensitive applications.
5. Enabling Complex Fluid Circuits
Check valves are the “diodes” of the fluid world—they direct flow in specific pathways, enabling complex fluid circuits.
This is particularly important in:
- Hydraulic systems
- Pneumatic control systems
- Cooling circuits
- Multi-pump arrangements
- Filter bypass systems
Without check valves, many of these systems would be impossible to design effectively.
Types of Check Valves and Their Specific Purposes
Not all check valves are created equal. Different designs serve different purposes, and choosing the right one matters.
Swing Check Valves
How they work: A hinged disc swings open with forward flow and closes with reverse flow.
Best for:
- Clean liquid applications
- Horizontal pipe installations
- Low-pressure applications
- Minimal pressure drop requirements
Swing check valves are probably what you picture when thinking of a check valve. They’re the most common type you’ll find in residential plumbing.
Ball Check Valves
How they work: A ball (usually made of metal or plastic) moves forward with flow and seals against a seat when flow reverses.
Best for:
- Vertical pipe installations
- Slurry applications (since the ball can rotate, preventing buildup)
- Simple, cost-effective applications
- Applications with minimal space
Ball check valves are the workhorses of many industrial applications because of their simplicity and reliability.
Spring-Loaded Check Valves
How they work: A spring holds a disc or piston against a seat until forward pressure overcomes the spring tension.
Best for:
- Any orientation (horizontal, vertical, or angled pipes)
- Applications requiring fast closure
- Preventing water hammer
- Systems with backpressure
The spring component makes these valves more responsive than gravity-dependent types, reducing the risk of water hammer.
Diaphragm Check Valves
How they work: A flexible diaphragm deforms with forward flow and seals against a seat with reverse flow.
Best for:
- Sanitary applications
- Chemical handling
- Low-pressure systems
- Applications requiring zero leakage
The diaphragm provides an excellent seal, making these valves ideal for applications where even small leakage is unacceptable.
Lift Check Valves
How they work: A disc moves up and down in line with the flow path.
Best for:
- High-pressure applications
- Steam systems
- Small line sizes
- Vertical flow (upward direction)
Lift check valves work well in constrained spaces where a compact valve is needed.
Pro Tip: When selecting a check valve, always consider the specific requirements of your system. The wrong valve type can lead to water hammer, excessive pressure drop, or premature failure.
Real-World Applications of Check Valves
To truly understand the purpose of check valves, let’s look at how they’re used across different industries.
Residential Plumbing
In your home, check valves serve critical functions:
- Backwater valves prevent sewage backflow during floods
- Sump pump discharge lines use check valves to keep water from flowing back into the sump pit
- Hot water recirculation systems use check valves to ensure water flows in the proper direction
- Well water systems use check valves to maintain pressure and prevent well contamination
Without these valves, your home’s plumbing would be far less reliable and potentially unsafe.
Industrial Processes
In industrial settings, check valves are absolutely vital:
- Chemical processing relies on check valves to keep chemicals flowing in the right direction
- Boiler feed systems use check valves to prevent hot water or steam from flowing back to pumps
- Cooling water systems use check valves to ensure proper circulation through heat exchangers
- Compressed air systems use check valves to isolate compressors and maintain pressure
The right check valve can make or break an industrial process’s efficiency and safety.
HVAC Systems
Modern heating, ventilation, and air conditioning systems incorporate numerous check valves:
- Chilled water systems use check valves to prevent backflow through inactive pumps
- Heat pumps use check valves to direct refrigerant flow correctly
- Boiler systems use check valves to prevent backflow of hot water
- Solar thermal systems use check valves to prevent reverse circulation at night
These applications help maintain comfort in buildings while maximizing energy efficiency.
Oil and Gas Industry
Check valves are particularly crucial in the high-stakes world of oil and gas:
- Pipeline systems use check valves to prevent flow reversal during pump failures
- Refinery processes use specialized check valves for high-temperature applications
- Offshore platforms use check valves to prevent backflow in case of emergency shutdowns
- Natural gas compression relies on check valves to maintain pressure and prevent backflow
The reliability of these valves can have major safety and environmental implications.
Water Treatment
Clean water depends on properly functioning check valves:
- Water intake systems use check valves to prevent backflow during pump stoppages
- Chemical injection points use check valves to prevent water from backing up into chemical tanks
- Distribution systems use check valves to maintain pressure zones
- Backflow preventers (specialized check valves) protect potable water supplies
These applications directly protect public health by maintaining water quality.
How to Choose the Right Check Valve
With so many types available, selecting the right check valve can feel overwhelming. Here’s a simplified approach:
Step 1: Define Your Flow Requirements
- What’s the minimum and maximum flow rate?
- Is the flow continuous or intermittent?
- Is there a risk of water hammer?
Step 2: Consider Your Fluid
- What are you flowing? (water, oil, gas, slurry, etc.)
- Is it corrosive or abrasive?
- What’s the temperature range?
- Is it sanitary or hazardous?
Step 3: Evaluate Installation Constraints
- What’s the pipe orientation? (horizontal, vertical, angled)
- How much space is available?
- Are there pressure limitations?
- Are there noise concerns?
Step 4: Think About Maintenance
- How accessible does the valve need to be?
- How critical is the application?
- What’s the expected service life?
- Is easy replacement important?
By answering these questions, you’ll narrow down your options significantly.
Conclusion
So, what is the purpose of a check valve? As we’ve seen, it’s far more than just preventing backflow—though that remains their primary function.
Check valves protect equipment, maintain system pressure, prevent contamination, enable complex fluid systems, and ultimately save money by preventing costly failures and inefficiencies.
From the simplest residential plumbing application to the most complex industrial process, check valves play a vital role in keeping fluids flowing in the right direction.
Whether you’re a homeowner trying to understand your plumbing system or an engineer designing complex industrial processes, understanding check valves is essential for creating safe, efficient, and reliable fluid systems.
Remember: The right check valve for your application depends on numerous factors, including flow characteristics, fluid properties, installation constraints, and maintenance requirements. Taking the time to select the proper valve will pay dividends in system performance and reliability.
Bottom line? Check valves may not be the most exciting component in a system, but they’re often among the most important. Their purpose—ensuring one-way flow—is fundamental to countless applications that we rely on every day.
Now I’d like to hear from you: Have you ever encountered issues with check valves in your systems? Or do you have questions about what is the purpose of a check valve in a specific application? Let me know in the comments below!