Pressure-control valves are found in practically every pneumatic and hydraulic system. They help in a variety of functions, from keeping system pressures below a desired limit to maintaining a set pressure level in the part of a circuit. Different types of pressure control valves include relief, reducing, sequence, counterbalance, safety, and unloading. All of them are typically closed valves, except for reducing valves, which are usually open. For most of these valves, a restriction is necessary to produce the required pressure control. One exception is the externally piloted unloading valve, which depends on an external signal for its actuation, which normally comes from a digital pressure regulator. In certain applications, like ventilators and anesthesia machines, the flow must be consistent at all times. Variations in the flow of gases can lead to serious injury or death. That’s why control valves are so important.
Typesof Pressure Control Valve
Pressure control valve, short for pressure valve sometimes, refers to the valve which can be used to control the pressure and it is mainly used to meet the force or torque of actuators. Pressure control valve can be divided into safety valve, relief valve, pressure reducing valve, and sequence valve.
Pressure Relief Valve
Most pneumatic and hydraulic power systems are designed to operate within a defined pressure range. This range is a function of the forces the actuators in the system must generate to do the required work. Without controlling these forces, the power components and expensive equipment could get damaged. Relief valves make it possible to avoid this hazard. They are the safeguards that limit maximum pressure in a system by diverting excess gases when the pressure gets too high. The pressure at which a relief valve first opens to allow fluid to flow through is known as cracking pressure. When the valve is bypassing its full rated flow, it is in a state of full-flow pressure. The difference between full-flow and cracking pressure is sometimes known as the pressure differential or the pressure override.
In some cases, this pressure override is not objectionable. It can be a disadvantage if it wastes power via gas lost through the valve prior to reaching the maximum setting. This can allow maximum system pressure to exceed the ratings of the other components.
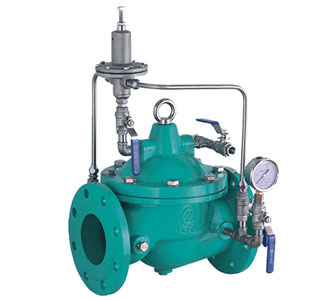
Pressure Reducing Valve
The function of pressure reducing valve is to adjust the oil pressure. This kind of valve consists of two parts: the pilot valve and the main valve. After entering from the oil mouth and flowing through the spool and orifices, the high-pressure oil will de-pressure into low-pressure oil and outflow the mouth of pressure reducing valve.
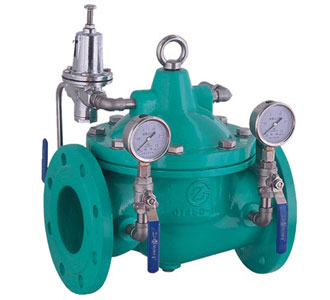
Sequence Valve
Due to the pressure change in the hydraulic system, the sequence valve can control the sequence of actuators. The structure and working principle of the sequence valve are basically the same as the relief valve, and the only difference is that the exit of the sequence valve is no longer used to connect tanks. Therefore, the internal leaking oil can not channel directly to the oil chamber with a pipeline but uses a special pipeline instead.
Although pressure control valve has different functions and features because of their wide varieties, the fundamental role is still focused on pressure control. After years of development and reform, China has got rapid development in all walks of life. So how to seek common progress and development for these industries matching equipment is a difficult problem for researchers and businesses.
Balance Valves
These valves are typically closed and are often used to maintain a set pressure in a portion of a circuit, usually to counterbalance a weight. The style of valve is ideal for counterbalancing an external force or to counteract a weight like in a press to keep it from free-falling. The valve’s primary port is connected to the rod end of a cylinder, and the secondary port is connected to the directional control valve. The pressure is set slightly higher than what’s required to keep the load from free-falling. When pressurized fluid flows to the cylinder’s cap end, the cylinder extends and increases pressure in the rod end and shifts the main spool in the valve. This creates a path that allows fluid to flow through the secondary port to the directional control valve and reservoir. As the load is raised, the integral check valve opens to allow the cylinder to retract freely. If it is necessary to relieve back pressure at the cylinder and increase the force at the bottom of the stroke, the counterbalance valve can be operated remotely. When the cylinder extends, the valve must open and its secondary port is connected to the reservoir. When the cylinder retracts, it doesn’t matter that load pressure is felt in the drain passage because the check valve bypasses the valve’s spool.
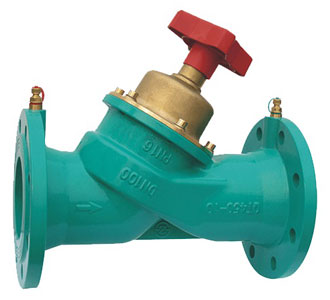
Related Tags :
Ten articles before and after
Introduction and Features of Flow Control Valves – Zeco |API Approved Valve Supplier
Advantages of DIN Standard Safety Valves – Zeco |API Approved Valve Supplier
The Raise of Solenoid Valves is the Future Trend – Zeco |API Approved Valve Supplier
Classification and Application of Vacuum Valves – Zeco |API Approved Valve Supplier
The Importance of Maintenance and Repair on Valves – Zeco |API Approved Valve Supplier
Features and Advantages of Buried Full Welded Ball Valves – Zeco |API Approved Valve Supplier
Some Knowledge of Butterfly Valve and Butterfly Handles – Zeco |API Approved Valve Supplier
The Layout of Safety Valves – Zeco |API Approved Valve Supplier
Difference between elec butterfly valve and elec gate valve – Zeco |API Approved Valve Supplier
Knowledge of Pneumatic Cut-off Ball Valve – Zeco |API Approved Valve Supplier