Description
ZECO Valve is an API 600 approved Gate Valve Manufacturer.
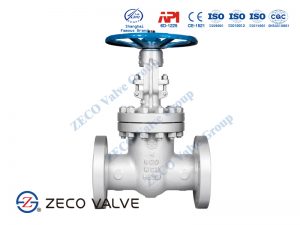
What are Industrial Valves?
In industrial applications, valves play a vital role in controlling or regulating media movement in piping systems. The wide scope of industrial applications allows more varieties in valve design.
While most are for the stop-start mechanism, certain valves also have throttling capabilities. Additionally, valves are either manually operated or with the use of a gear that moves the actuator.
Any person engaging in the piping business should understand the importance of valves. Knowing the operation and maintenance of valves ensures that these can last longer. It also ensures that the entire piping process is without delays.
This article discusses everything you need to know about industrial valves. Included in this article are the different valve functions and the general valve parts. This article also discusses the commonly used valves in industrial applications.
What is Industrial Gate Valve?
Industrial Gate Valves or “Block Valves” are the most commonly used valve type in the oil & gas industry. Gate valves are intended for on-off flow control. When fully open, fluid flows through the valve in a straight line, resulting in minimum pressure drop across the valve.
Industrial gate valves are suitable for both above-ground and underground installation and are designed for fully open or fully closed service. They are installed in pipelines as isolating valves and should not be used as control or regulating valve.
These valves can be divided into two main types, namely parallel and wedge-shaped. Parallel industrial gate valves use a flat gate between two parallel seats. The knife gate valve is a popular valve designed this way, with a sharp edge on the bottom of the gate. Wedge-shaped industrial gate valves use two inclined seats and a slightly mismatched inclined gate.
Industrial gate valves used to be a metal seated wedge with the conical wedge design and angular sealing devices needing a depression in the valve bottom to ensure a tight closure. These days resilient seated gate valves have a plain valve bottom that allows for the free passage of sand and pebbles in the valve.
Rising stems are fixed to industrial gate valves and raise or lower as the gate is operated. This is a visual indication of the industrial gate valve’s position and this makes it easier to grease the stem. This type of industrial gate valve is usually only suited to above-ground installations.
Non-rising stems are threaded into the gate itself and take up less vertical space. These valves are suitable for both above-ground and underground installations.
Industrial gate valves are long-lasting and durable and don’t require much maintenance.
Specifications of Industrial Gate Valve
SIZE RANGE | Size Range From 1/4” – 60” |
PRESSURE RANGE | Size Range Pressure Range ANSI 150# to ANSI 1500# pressure rating |
MATERIAL GRADES | WCB, A105N, LF2, LCC, CF8M, 316, 316L, A20, Hastelloy C, Other exotic materials |
TRIM MATERIALS | 13Cr, SS 316, A20, Monel, Hastelloy C stem and wedge |
PACKAGING & GASKET MATERIAL | Graphite or Teflon |
END CONFIGURATIONS | Raised Face, RTJ, Threaded, Socket Weld, Threaded X Socket |
STANDARDS | Low Emissions, NACE certified |
Industrial Gate Valve Parts And Components
The industrial valve is a collective set of smaller parts. There are internal and external parts. While specific valve types contain certain components definitive to that design, all industrial valves share major valve components. This section will discuss the different valve parts.
Body
The body houses the internal parts of the valve, including the trim. This is also the passageway for the fluid. Industrial valve manufacturers produce this as either of the three: cast, forged, or fabricated. The body also connects the valve on both ends to the pipe system.
Bonnet
The two functions of the bonnet are:
It houses the internal parts of the valves.
It supports the stem since it is in the of the bonnet in many valve types.
Valve Trim
The valve trim refers to the collective valve parts that come in contact with the flow media. These are the disc, the valve seat, and the stem. Take note, some valves may have additional parts, but generally speaking, these three are always present in most valves.
The type of seat and disc, along with the placement of the disc in relation to the seat, determine the valve trim performance. It is also the combination of the disc, seat, and stem that determines the movement and control of the valve.
- Disc
- The disc has alternative names depending on the type of valve. Ball and gate are two other names for the disc. This part can function as a throttle or to stop/permit the flow of media into the valve to the pipes.
- Seat
- The seat provides a cushion for the disc. Seal rings are its other name. Some types of valves have one seat while others have two or more. The higher the number of seats, the better sealing. Multiport valves have more seats since these have more than one exit. Some seats are integrated into the valve structure. Others are replaceable.
- The quality of the valve seat directly affects the effectiveness of leakage prevention. Depending on the requirements like the type of flow media, temperature and pressure gauges, and the like, valves are either elastomer like Teflon or metal.
- Stem
- The stem is the shaft that connects the disc to the actuator. This part supplies the motion needed to open or close the disc. The opening and closing movements are either linear like the gate or globe valves, or rotational like the butterfly and ball valves.
- Bolts
- Bolts hold one valve part to another, for example, the bonnet to the body. The bolts make the seal tighter.
- Actuator
- The actuator goes by many names such as wheels, levers, and handles. More often than not, the names follow the design of the actuator. Gate and globe valves have manual handwheels as actuators. On the other hand, ball, plug, and butterfly valves have levers that act as actuators. While manual actuators are common, there are circumstances that automation or power is the ideal way to actuate. There are issues with valve location such as being remote. Time does not allow the valves to open quickly via manual methods.
- The valve is large and the pressure is too high; manual opening becomes risky.
- Packing
- This is also called the gasket. Packing functions as a seal between the stem and the bonnet. This plays an important role as the proper installation of the packing increases the life service of the valve.
- Installed too loose, the valve leaks. If installed too tight, the valve cannot move. Packing, in other words, reduces damage and increases the sealing capability of the valve. It has five components, namely the gland follower, the gland, the stuffing box, and the backseat.
- Yoke
- The yoke is the arm that connects the body and bonnet to the actuator. Made as a one-piece with the bonnet, the yoke should withstand the force applied to the actuator. The yoke contains the nuts and bushing that act as connectors to other parts of the valve.
Features of Industrial Gate Valves
- ZECO industrial gate valve is designed with a seal, which can meet the needs of replacing packing with pressure in the maintenance field, and ensure no leakage when replacing packing. Compared with the original replacement process of disassembling the valve, it accelerates the speed greatly, saves the time of personnel, and optimizes the operation time of the pipeline;
- Long thread stem nut prolongs tread life and permits the removal of the hand wheel in the fully open position;
- Flexible graphite gasket used for 150 Class gate valve, spiral wound gasket for Class 300 & 600 valves, and metal ring gasket for gate valves of 900 or greater Class(600 Class is obtainable if customer requires);
- During the opening and closing of the valve, the integral guide in the valve body keeps the wedge from the center. Without the integral guide, the gate seal will be offset, and the structure of the ZECO industrial gate valve stabilizes the sealing performance.
Applications of Industrial Gate Valves
- Cost and Energy efficient
- Simple body design and easy to operate
- Dual flow direction, depending on the medium
- Minimum erosion experienced
- Minimum pressure involved, due to streamlining the flow
Product Overview of Industrial Gate Valves
SIZE RANGE | Size Range From 1/4” – 60” |
PRESSURE RANGE | Size Range Pressure Range ANSI 150# to ANSI 1500# pressure rating |
MATERIAL GRADES | WCB, A105N, LF2, LCC, CF8M, 316, 316L, A20, Hastelloy C, Other exotic materials |
TRIM MATERIALS | 13Cr, SS 316, A20, Monel, Hastelloy C stem and wedge |
PACKAGING & GASKET MATERIAL | Graphite or Teflon |
END CONFIGURATIONS | Raised Face, RTJ, Threaded, Socket Weld, Threaded X Socket |
STANDARDS | Low Emissions, NACE certified |
Industrial Valve Manufacturer
ZECO Valve is an industrial valve manufacturer of ball valves, gate valves, globe valves, check valves, butterfly valves, plug valves, and strainers. Our valve factory in China adheres to ANSI, API, DIN, GOST, BS, JIS, China GB standards, and customer-specific requirements. Our products have been sold worldwide for a wide range of applications in natural gas, oil, oil refining, chemical, marine, power generation, and pipeline transportation industries.