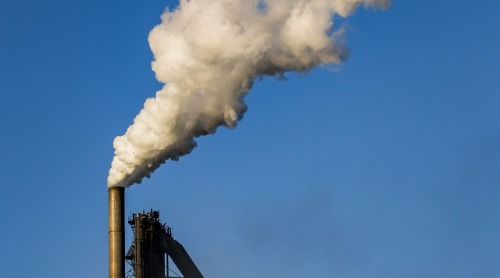
Compressed air has been utilized as a safe and reliable power source for over 100 years. In fact, approximately 90% of all industrial manufacturing companies rely on compressed air at various stages of operation.
Many manufacturers have turned to compressed air as an economical utility. Unlike gas, water, and electricity, compressed air does not need to be supplied by an outside source—it can easily be generated on-site by the user. While this makes power generation easier, it also puts the responsibility of air purity and contamination in the hands of manufacturers.
The three main types of contaminants in compressed air
Water content in compressed air
Then there is the moisture contained in our ambient air. It enters the compressed air piping system through the intake in the form of water vapor. This water vapor is the most prominent contaminant in compressed air in total volume terms and it forms most of the liquid contamination that can be found in the air system.
The water content is measured in terms of the dewpoint. It is the temperature at which the compressed air is still able to handle its water vapor content before the moisture forms condensate.
If the moisture is not removed, it can reduce the service lives of pneumatic equipment through corrosion. In addition, it could lead to bacterial growth, which could adversely impact the quality of final products. This is especially problematic in applications in the food and beverage and pharmaceutical sectors.
While air quality is not as important for some processes, it is crucial to applications in the food & beverage and pharmaceutical sectors, where bacterial growth would be particularly harmful.
Oil in compressed air
The quantity of oil in compressed air depends on several factors, including the type of machine, design, age and condition. There are two main types of compressor design in this respect: those that function with lubricant in the compression chamber and those that function without lubricant. In lubricated compressors, oil is involved in the compression process and also is included in the (fully or partially) compressed air. However, in modern, lubricated piston and screw compressors the quantity of oil is very limited.
In this case, it is known as a compression contaminant.
Dust particles in compressed air
It all starts with the ambient air that has to be compressed. In a typical industrial environment, it can contain more than 140 million dirt particles per cubic meter. When it is compressed, these contaminants are concentrated in line with the air pressure increase.
That means that compressed air can contain many times as many dirt particles. Unfortunately, most of them are so small (under two microns) that an inlet filter only removes 20% of them.
The four most common sources of compressed air contamination and what causes them.
Ambient Air
Ambient air is the air found outside of the compressor. When an air compressor is in use, it acts as a large vacuum that pulls in the surrounding air. This air often contains water vapor, microorganisms, atmospheric particulate, and oil vapor that can be harmful to the compressor system. To avoid contamination, make sure proper filtration methods are set in place.
Air Compressor
Contaminants are often unavoidable in compressor systems because certain materials are required for the system to function properly. Liquid oil, liquid water, oil aerosols, and water aerosols are often used in air compression and ultimately find pathways into the air chamber. It’s important to be aware of these potential contaminants and limit exposure when possible.
Air Receiver
Air receivers are installed to increase the efficiency and reliability of the compressor. However, they also serve as a source of contamination that can lead to chemical reactions and oxidation if not properly maintained. Be sure to provide regular cleanings and preventative maintenance to avoid rust, pipe scale, and bacteria from forming.
Distribution Piping
Distribution piping transports air from the compressor to various locations around the facility. Similarly to air receivers, distribution pipes can be a major source of contamination that can lead to rust, pipe scale, and the growth of bacteria if not properly maintained.
To protect your compressed air systems from contamination, be sure to provide regular preventative maintenance and filtration systems that eliminate harmful contaminants and keep your air safe.
2 ways to prevent contaminated air in your food facility
Keep the air as dry as possible
Before pumping the air through your plant, remove as much moisture as possible. The ideal dew point is -40℉. Most facilities have a large dryer that can achieve this level of dryness. Monitor your dryer’s performance regularly to ensure that it can reach this temperature specification.
Use at least a two-stage filtration system
Ensure your facility is using proper filters to prevent microorganisms from appearing in the air and traveling through your plant. Food Safety recommends installing a two-stage filter system as close as possible to the point of use. For some plants, a three-stage filter system may be necessary.
What is an Air Valve?
Air Valves perform two important functions in a piping system. They maintain system design efficiency and provide system protection. System efficiency is maintained by venting air via the air valves from the system which can restrict flow and increase pumping costs.
Protection is provided by exhausting and admitting air through the air valves during system operations including start-up, shutdown, and critical conditions such as power failures or line breaks. The exhausting and admitting of air during these conditions will reduce the potential for destructive surges and water hammer normally associated with uncontrolled air or a vacuum condition within the piping system.
Related Tags :
Ten articles before and after
3 WAYS THAT PPE WILL KEEP YOU SAFE IN THE WORKPLACE | Zeco Valve
HOW TO PREVENT CORROSION IN OIL AND GAS APPLICATIONS | Zeco Valve
Valve Master First Choice For Engineering
Brand Notability Improves Unceasingly
API standard gate valve,globe and check valves,high pressure gate valves
HOW TO STAY SAFE IN INDUSTRIAL HEATING APPLICATIONS | Zeco Valve
THE EIGHT WASTES OF LEAN MANUFACTURING AND HOW TO TACKLE THEM | Zeco Valve
WHAT YOU NEED TO KNOW ABOUT FILTRATION IN THE FOOD AND BEVERAGE INDUSTRY | Zeco Valve
WHAT YOU NEED TO KNOW WHEN SELECTING THE RIGHT INSTRUMENTATION TUBING | Zeco Valve
EVERYTHING YOU NEED TO KNOW ABOUT THE HEAT TREATING PROCESS | Zeco Valve