The ceramic-lined valve has very good performance on abrasion erosion, corrosion resistance, excellent heat-shielding, and electric insulation. Mainly used in electric power, petroleum, chemical, metallurgy, mining, sewage treatment, and other industries where the metal valve cannot be applicable.
What is a Ceramic Ball Valve?
A ceramic ball valve is a type of ball valve which has internal components made of ceramic materials. Such ceramic components include ball, seat, and lining. A ceramic ball valve has its body made of a metallic material such as stainless steel or carbon steel. The metallic body is used to protect the ceramic trim from damage by sudden mechanical or thermal shock. A ceramic ball valve uses a ball with a hole at its center where fluid flows through when the handle is rotated. Ceramic ball valves can also be automatic by using actuators like pneumatic, electric, or hydraulic actuators. Benefits of using a ceramic ball valve over other materials like steel include lower mass and high resistance to wear. Ceramic ball valves have excellent resistance to corrosion and abrasion. Such properties of ceramic ball valves are used in severe applications prone to abrasion and corrosion. Ceramic ball valves are used in various industries such as petroleum, chemical engineering, and manufacturing plants.
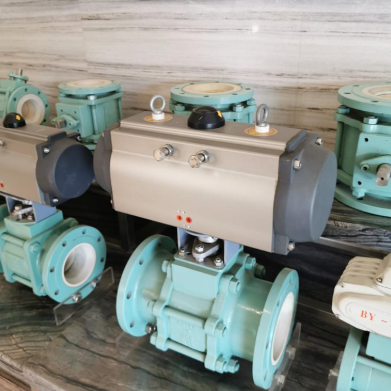
Design of Ceramic Ball Valves
- Several flanges and body size combinations are available to meet specific application requirements
- A wide range of Cv values are available to meet various control applications
- Simplified spare parts allow for easy on-site valve maintenance
- Floating and trunnion ball versions
- High-temperature versions
- Various body and ceramic liner/ball material options
- Low emission shaft sealing available for strict environmental requirements
The ceramic ball valve adopts a new high-tech type structural ceramic material as sealing and wearing parts, which can improve abrasion and corrosion resistance, and sealing performance, prolonging lifespan, 2-4 times of lifespan than Titanium Alloy and Monel valve. Using ceramic ball valves can reduce repair or replacement costs and improve the safety, and stability of the operating system.
Components of Ceramic Ball Valves
Trim components of ceramic ball valves adopt Alumina or zirconia ceramic with high chemical stability and hardness (HRC88), only inferior to diamond. The ceramic-lined valve has very good performance on abrasion erosion, corrosion resistance, excellent heat-shielding, and electric insulation. Mainly used in electric power, petroleum, chemical, metallurgy, mining, sewage treatment, and other industries where the metal valve cannot be applicable.
The ball is made with advanced grinding equipment and advanced process technology that can ensure high precision ball roundness, a good surface. The self-lubricating capability of ceramic ensures good sealing after polishing, which radically changed the defects that metal hard sealing valve has such as big torque, and non-corrosion-resistant sealing surface.
The ball and seat adopt alumina or zirconia ceramic with high chemical stability and hardness (HRC88). The ceramic-lined valve has very high abrasion resistance, corrosion resistance, erosion resistance, and good insulation. The wetted body is fully lined with PFA that also has good performance on corrosion resistance. Compared to the fully lined ceramic valve, PFA lined one lower the whole weight and is also more economic.
Specifications of Ceramic Control Valves
- Size: 1/2” – 8” (DN15-DN200) Full Bore Construction
- 1-1/2” – 10” (DN15-DN200) Reduced Bore Construction
- Pressure: Clas150-Class300 (PN10-PN40)
- Available Manufacturing Standards: ASME, JIS, DIN, GOST, etc.
- Available Liner Ceramic Materials: Al2O3, ZrO2, Si3N4, SiC
- Available Ball Port type: Round type or V type.
Features of Ceramic Ball Valve
- Completely ceramic flow path, no metallic components
- Material designed to withstand thermal shocks
- Robust backlash-free ball to stem connection, stainless steel stem
- Lug and wafer body type options
- One piece body
- Low Cv trim options for small capacity applications
- Live loaded packing
Applications of Ceramic Ball Valves
- Coal Fired Power Plants
- Flue gas desulphurization (FGD), lime/gypsum slurry process water with high chlorides and solids content
- Iron & Steel
- Injection of coal powder (PCI), injection of carbon powder in electric arc furnaces (EAF), raw iron desulphurization (supply of additives: CaC, Mg02…)
- Polysilicon
- Si3CI4, TCS, raw silicon, splitting of silicon with acids, conveying of silicon powder
- Waste Incineration Plants
- HCI-prewashes, limestone suspension for pH regeneration, corrosive washing water (HF loaded)
- Pulp & Paper
- Kaolin, bentonite, fillers, dyes, bleachers, talcum, pulp residue, lime suspension, Mg02, green liquor, wood particles in suspension
- Mining
- Splitting of ore with H2SO4, copper residues in suspension, concentrated copper slurries (“floatation”) to the filter, pneumatic conveying of copper powder to the smelter, air bleed valve on the pneumatic conveying container
- Pneumatic Conveying
- All types of dry bulk material (quartz, silicon, lime, coal, glass, cement, PP pellets …)
- Petrochemical
- FCC aluminum oxide powder as the catalyst, catalyst slurry
- Fertilizer
- Ammonium nitrate slurry, phosphoric acid with solids (lime), dolomite, washing water with hydrofluoric acid content
- Chemical
- TiO2 suspension, Ti3C14, H2SO4 + Ti02, FeCl2
Related Tags :
Ten articles before and after
More About our Knife Gate Valves | Professional valve manufacturer | Quality valve supplier
RB Series Trunnion Mounted Ball Valve | Professional valve manufacturer | Quality valve supplier
Zeco Valve Range | Professional valve manufacturer | Quality valve supplier
Happy Festive Season | Professional valve manufacturer | Quality valve supplier
News – How Can LNG Filling Station Equipment Reduce Gas Loss Manually | Cryogenic valve manufacturer
News – How To Reduce BOG Emission Of LNG Filling Station Equipment | Cryogenic valve manufacturer