Check valve is also called a clack valve, one-way valve, or non-valve valve because it only allows fluid to flow in one direction. These industrial valves are automatically activated by the force generated by the flow of the medium in the pipeline and can be classified as automatic valves.
What is a Check Valve?
Check valves are usually installed in the pipeline to prevent backflow. A check valve is basically a one-way valve in which the flow can flow freely in one direction, but if the flow turns, the valve will be closed to protect the piping, other valves, pumps, etc. If the flow is diverted without a check valve installed, a water hammer may occur. Water hammer often occurs with extreme force and can easily damage pipes or components.
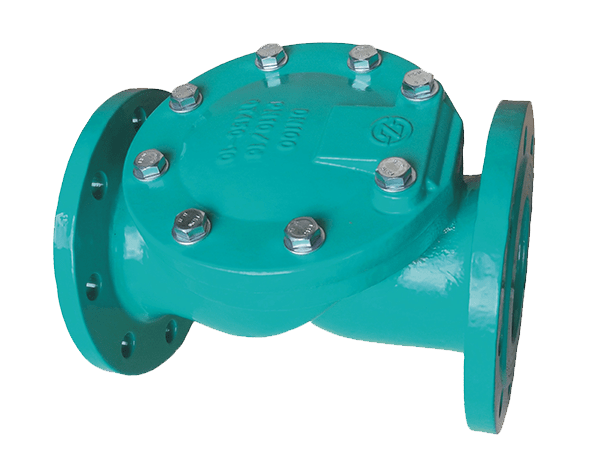
What is the Function of Check Valve?
The function of the check valve is to only allow the medium to flow in one direction and prevent the flow in multiple directions. Normally, the check valve works automatically. Under the action of the fluid pressure flowing in one direction, the disc opens; when the fluid flows in the opposite direction, the disc acts on the valve seat due to the self-coincidence of the fluid pressure and the disc, thereby cutting off the flow.
Applications of Check Valve
All check valves are suitable for various applications such as gas and liquid pipelines, water and steam systems, cooling towers, water treatment, gas export facilities, product tank farms, gas storage, and Mining dehydration.
Check valves can be used in many different applications. For example, they are usually placed on the outlet side of the pump to protect the pump from backflow. The centrifugal pump is the most common type of water pump. It is not self-priming, so a check valve is essential to keep the water in the pipeline. In addition, check valves are often used in HVAC systems (heating, ventilation, and air conditioning systems). For example, HVAC systems are used in large buildings, where the coolant is pumped many stories up. The check valve is installed here to make sure that the coolant will not be flushed back.
- Protection of upstream equipment
- Backflow can easily damage meters, compressors, filters, pumps, and other devices built for unidirectional flow. Water hammer is another potentially dangerous phenomenon. Check valves can help reduce the effect of water hammers, especially when the valve is equipped with an end-stage damper.
- Preventing media contamination or mixing
- By preventing reverse flow, check valves prevent the mixing of different media between two reservoirs. For example, in a water treatment plant, check valves prevent treated water from flowing back into the untreated water reservoir.
- Preventing drainage
- When media is being pumped from a suction reservoir to a discharge reservoir, reverse flow is highly likely to occur when the pump is stopped. Check valves are used to prevent this. The valve type commonly used for this is the foot valve.
Precautions when choosing a check valve
When selecting a check valve, it is important to conduct a cost-benefit analysis of the specific system. Usually, the focus is on reducing costs while obtaining the lowest possible pressure loss, but for check valves, higher safety equals higher pressure loss. Therefore, in order to ensure the check valve protection system, each system needs to be evaluated separately, and factors such as the risk of water hammer, acceptable pressure loss, and the financial consequences of installing a check valve must be considered.
We are check valve suppliers. Please feel free to contact us if you are interested in our check valves or other products.
Related Tags :
Ten articles before and after
Why Use a Ball Valve Instead of a Gate Valve?
The Working Principle And Features Of Cast Iron Gate Valve Manufacturer China
Classification And Working Principle Of Stainless Steel Ball Valve
How To Maintain Butterfly Valve
Use, Installation, and Maintenance Of The Ball Valve
Difference Between Gate Valve And Butterfly Valve