What is a Globe Valve?
A globe valve is a linear motion valve that stops, starts, and regulates fluid flow. The globe valve disk can be removed entirely from the flow path, or it will completely close the flow path. During the opening and closing of the valve, the disc moves perpendicularly to the seat.
This movement creates the annular space between the disk and seat ring that gradually closes as the valve closes. This characteristic provides the globe valve good throttling ability required for regulating the flow.
Leakage from the globe valve seat is less as compared to the gate valve, mainly due to right-angle contact between the disc and seat ring, which allows a tighter seal between the seat and the disk.
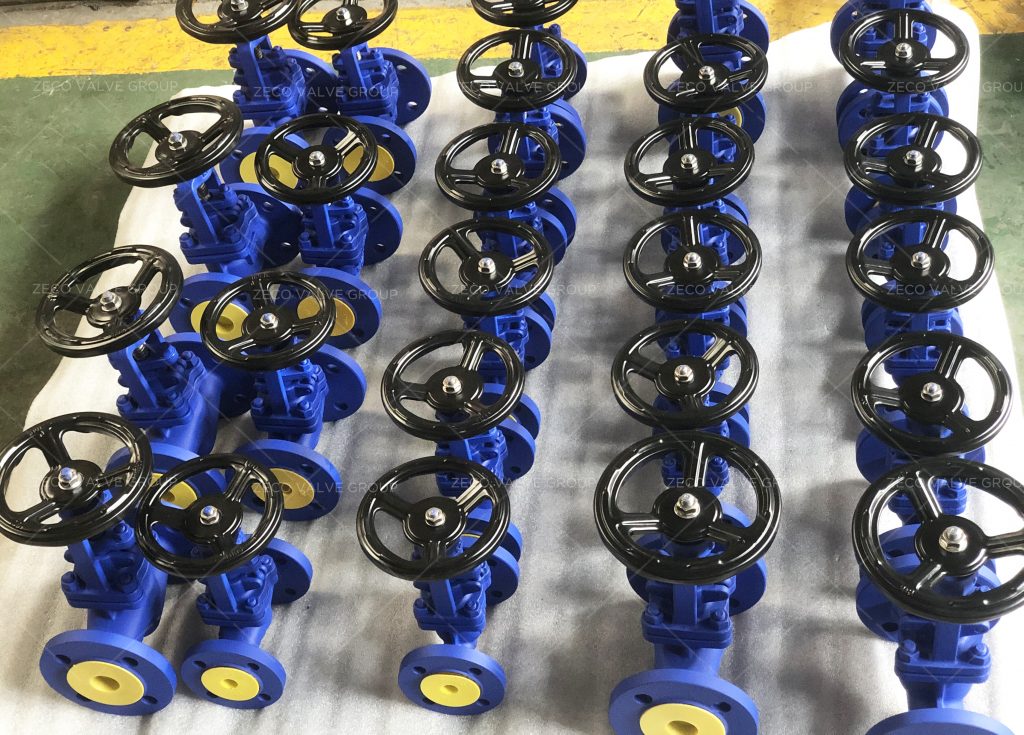
Globa Valve Function
The globe valve is used for throttling flow control. Shut-off is accomplished by moving the disc against the flow stream rather than across it as in the case with a gate valve. The flow pattern through a globe valve involves changes in direction, resulting in greater resistance to flow, causing a high-pressure drop. The globe valve is an excellent valve to use in the high-pressure operation of steam. Our globe valves are factory-made with quality material for long-term use.
Globe Valve Working Principle
A globe valve is primarily designed to stop, start and regulate flow. It is comprised of a movable disk and a stationary ring seat in a generally spherical body. The seat of a globe valve is in the middle of and parallel to the pipe, and the opening in the seat is closed off with the disk. When the handle is turned, manually or through an actuator, a disc is lowered or raised by means of the valve stem. When the disc is fully lowered, the fluid flow is shut off. When the disc is fully raised, the fluid flow is at its maximum rate. When the disc is in raised to less then maximum level, the fluid flow is regulated with proportion to the vertical travel of the disc.
Globe Valve Types
Body Designs of Globe valves
There are three primary body designs for Globe valves, namely. Tee Pattern or Z-body, Angle Pattern, and Wye Pattern or Y-body body.
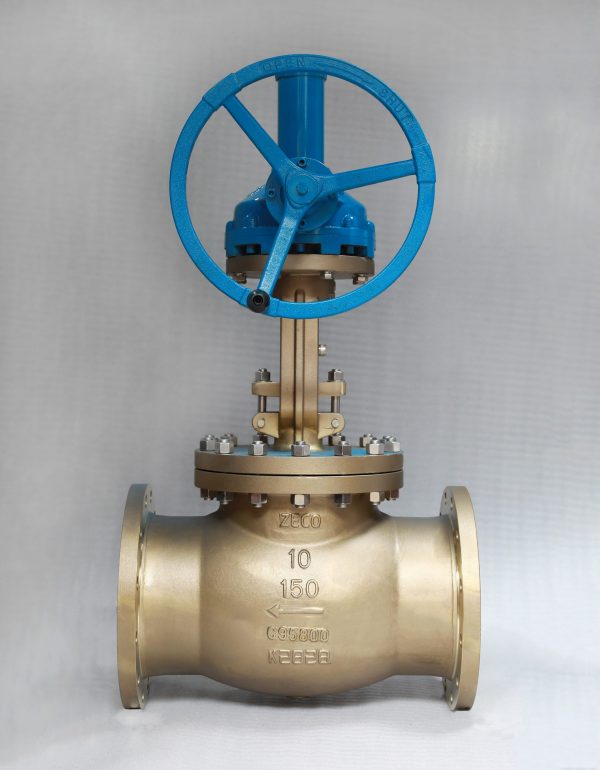
- Tee Pattern Globe Valve
- Tee Pattern Globe valve(T pattern globe valve) design is the most common body type, with a Z-shaped diaphragm. The horizontal setting of the seat allows the stem and disk to travel perpendicular to the horizontal line. This design has the lowest coefficient of flow and higher pressure drop. They are used in severe throttling services, such as in bypass lines around a control valve. Tee-pattern Globe valves may also be used in applications where pressure drop is not a concern and throttling are required.
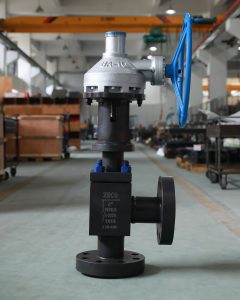
- Angle Globe Valve
- The angle Pattern Globe valves(Angle globe valve) design is a modification of the basic Tee Pattern Globe valve. The ends of this Globe valve are at an angle of 90 degrees, and fluid flow occurs with a single 90 degrees turn. They have a slightly lower coefficient of flow than wye-pattern Globe valves. They are used in applications that have periods of pulsating flow because of their capability to handle the slugging effect of this type of flow.
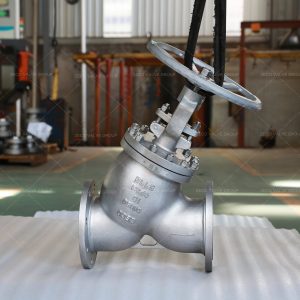
- Wye Pattern Globe Valve (Y Type Globe Valve)
- Wye Pattern Globe valves(Y-type globe valve) design, is an alternative for the high-pressure drop, inherent in Globe valves. The seat and stem are angled at approximately 45 degrees, which gives a straighter flow path at full opening and offers the least resistance to flow. They can be cracked open for long periods without severe erosion. They are extensively used for throttling during seasonal or startup operations. They can be rod through to remove debris when used in drain lines that are normally closed.
Bonnet Design of Globe Valves
There are three primary bonnet designs for Globe valves, namely.. screwed bonnet, bolted bonnet, welded bonnet, or pressure seal bonnet.
- Screwed Bonnet Globe Valve
- Screwed bonnet: This is the most basic design possible, and it is utilized for low-cost valves.
- Bolted Bonnet Globe Valve
- Bolted-bonnet: This is the most common design and is seen in the majority of globe valves. A gasket is required to seal the junction between the body and the bonnet.
- Welded Bonnet Globe Valve
- Welded-Bonnet: This is a common design that does not need disassembly. They weigh less than their bolted-bonnet equivalents.
- Pressure Seal Bonnet Globe Valve
- Pressure-Seal Bonnet: This kind is commonly employed in high-pressure, high-temperature applications. The greater the pressure in the body cavity, the greater the strain on the gasket of a pressure-seal valve
Globe Valve Parts
A globe valve has several key parts:
- Bonnet:
- The bonnet is the outer part of the valve, which encompasses these other parts.
- Cage:
- The cage surrounds the stem within the valve.
- Stem:
- The stem connects the disk to the valve actuator or handwheel, transmitting the force.
- Disk (Plug):
- The part of the globe valve that moves perpendicular to the seat. It’s the moveable physical barrier that blocks (or frees) the flow. When closed, the disk sits against the seat, plugging the flow. When opened, the disk sits above the seat, allowing liquid to pass.
- Types of Disc
- Ball Disc – suitable for low temperatures and low pressures. Ideal for starting and stopping operations. Ill-suited for flow regulation.
- Composition Disc – composites by definition consist of several components. The disc is almost always manufactured from metal whilst a non-metallic ring is mounted onto the disc to form the seating area. The non-metallic ring material is chosen to have good corrosion and erosion characteristics and may be custom-made to ensure it is fit for purpose. If the non-metallic ring is chosen correctly, it should allow for better sealing. Composite discs are often employed for steam system applications.
- Plug Disc – plug discs have a long and tapered shape. The shape of the plug disc makes it much more suitable to throttling than the composite and ball disc-type designs.
- Seat (Seat ring):
- This part of the valve provides the seal between the stem/disk and bonnet when the disk is tightly pressed against it. It’s either integrated or screwed into the valve itself.
Globe Valve Symbol
The symbol for a globe valve is two sideways triangles on the same linear line with
the points touching in the middle. Where the points touch, there’s a black circle. You
can see a picture of it here.
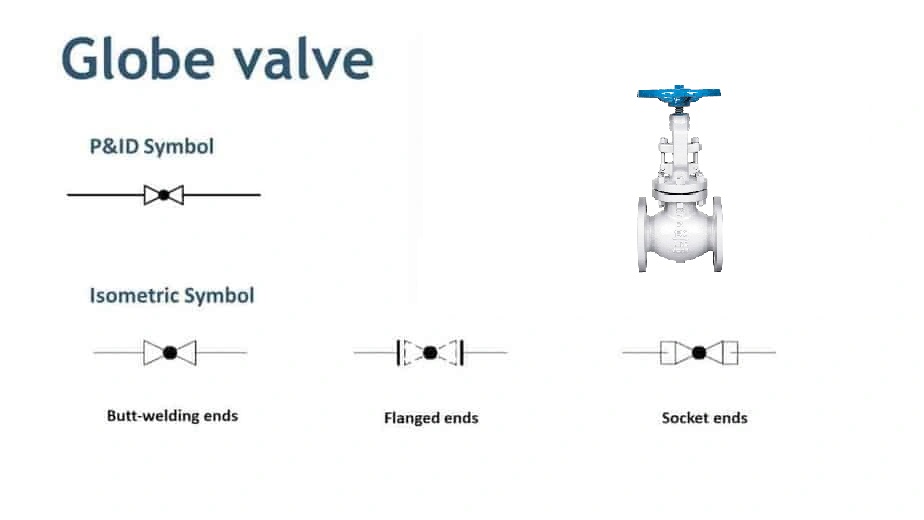
For applications with low temperatures, Globe valves are normally installed so that the pressure is under the disc. This contributes to an easy operation and helps protect the packing.
For applications with high-temperature steam service, Globe valves are installed so that the pressure is above the disk. Otherwise, the stem will contract upon cooling and tend to lift the disk off the seat.
Globe Valve Application
The following are some of the typical applications of Globe valves:
- Cooling water systems where flow needs to be regulated
- Fuel oil system where flow is regulated and leak tightness is of importance
- High-point vents and low-point drains when leak tightness and safety are major considerations
- Feedwater, chemical feed, condenser air extraction, and extraction drain systems
- Boiler vents and drains, main steam vents and drains, and heater drains
- Turbine seals and drains
- Turbine lube oil system and others
Advantages and Disadvantages of Globe Valve
- Advantages
- Good shutoff capability
- Moderate to good throttling capability
- Shorter stroke (compared to a gate valve)
- Available in tee, wye, and angle patterns, each offering unique capabilities
- Easy to machine or resurface the seats
- With the disc not attached to the stem, the valve can be used as a stop-check valve
- Disadvantages
- Higher pressure drop (compared to a gate valve)
- Requires greater force or a larger actuator to seat the valve (with pressure under the seat)
- Throttling flow under the seat and shutoff flow over the seat
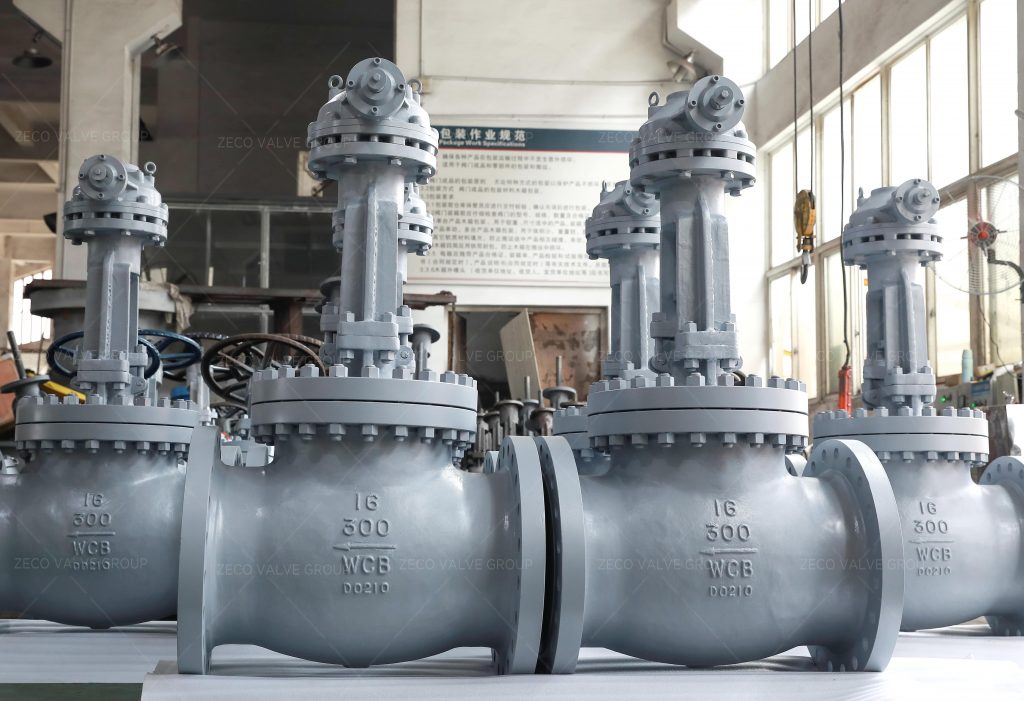
ZECO Valve is a proessional globe valve manufacturer in China, if any inquiries, please be free to contact us.
Related Tags :
Ten articles before and after
Valve part-Rubber factory-Visit
Is Valve quality the reason of China chemical EXPLOSION: Yancheng chemical factory In March 21th
Technical Specifications for Valve Selection and Configuration
The market competitiveness of cast iron valves is further reduced?
Advantages and Disadvantages of Butterfly Valves
Advantages and Disadvantages of Ball Valves
Advantages and Disadvantages of Gate Valves
Shanxi discovered 2.437 billion tons of coal resources last year
Thermal insulation valves: ball valves feature, principal, installation,advantageous