Globe valve is a valve that relies on the pressure of the valve stem so that the sealing surface of the valve flap and the sealing surface of the valve seat are closely fitted to stop the flow of the medium, which belongs to the forced sealing type valve, while the globe valve can also regulate the flow in the pipeline, suitable for the occasions that require frequent throttling, widely used in chemical plant pipelines.
Globe Valve Types
TEE Pattern/Straight Through Globe Valve
The Tee pattern valve design is the most common type of valve body, which has a 180° inlet and outlet flow path in the same direction and a horizontal setting of the valve seat allowing the stem and disc to move perpendicular to the horizontal line. This design has a low flow coefficient and pressure drop. They are used in severe throttling services such as bypass around control valves.T globe valves can also be used where throttling is required without regard to pressure drop.
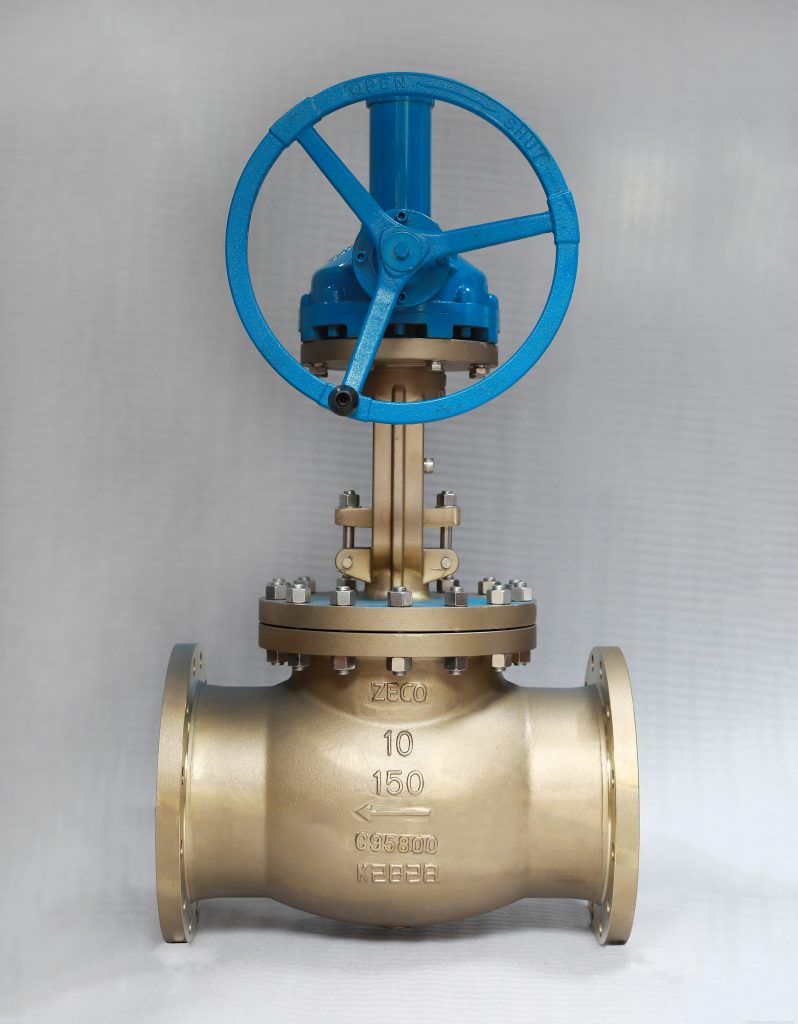
Y Type Globe Valve
The stem of the Y type globe valve forms an angle with the valve seat, about 45 degrees. With a straighter flow path at full opening and minimal resistance to flow, it is the least resistant of the globe valves to flow. The sealing surfaces of the seat and flap can be welded with carbide and can be left open for long periods without serious erosion. When used in drains that are normally closed, they can be passed through a rod to remove debris.
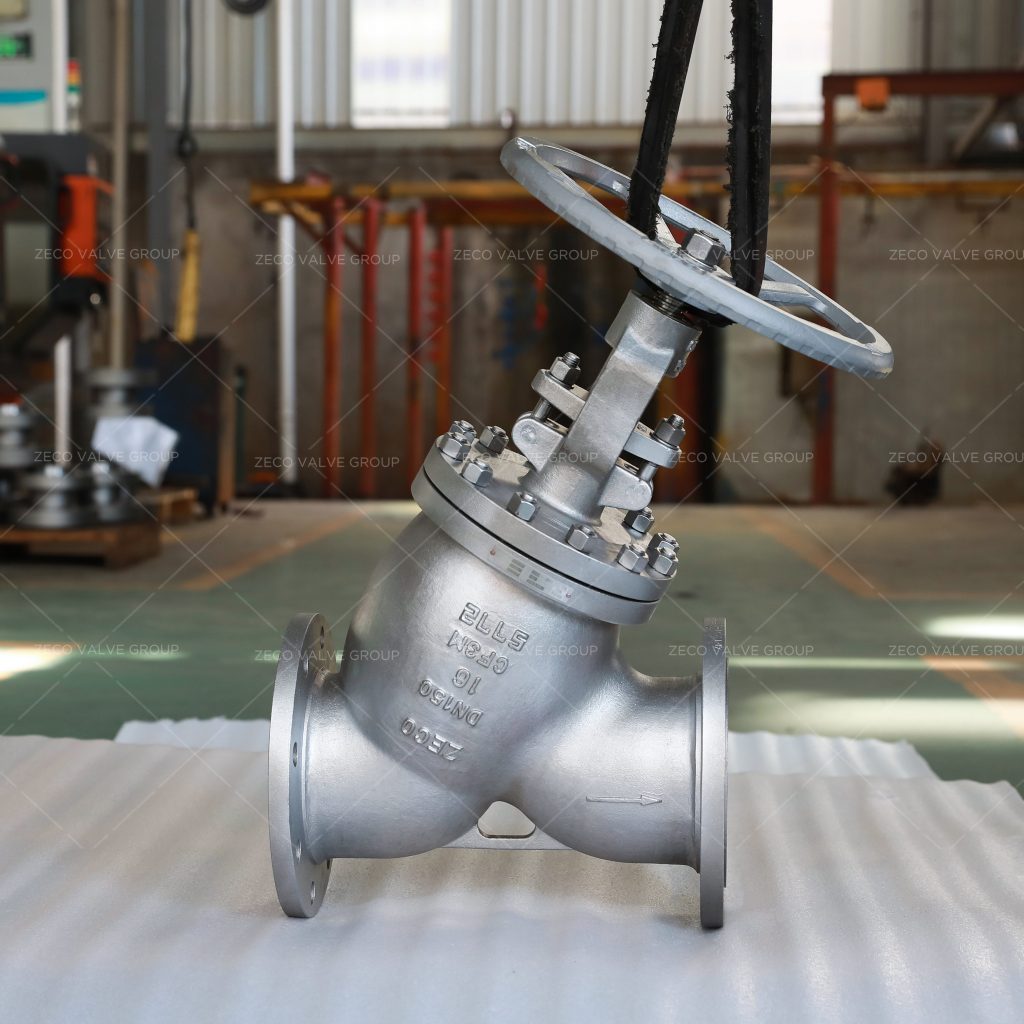
Angle Globe Valve
The angle globe valve design is a modification of the basic 3-way shut-off valve. These globe valves have 90-degree angles at both ends and the flow of fluid is only one 90-degree turn, allowing them to be installed at right angles to the piping system, saving the need for 90° elbows. They are used in applications with the pulsating flow as they have the ability to handle the sludging effect of this type of flow. This type of valve is best suited for ammonia production systems and for refrigeration systems in fertilizer plants.
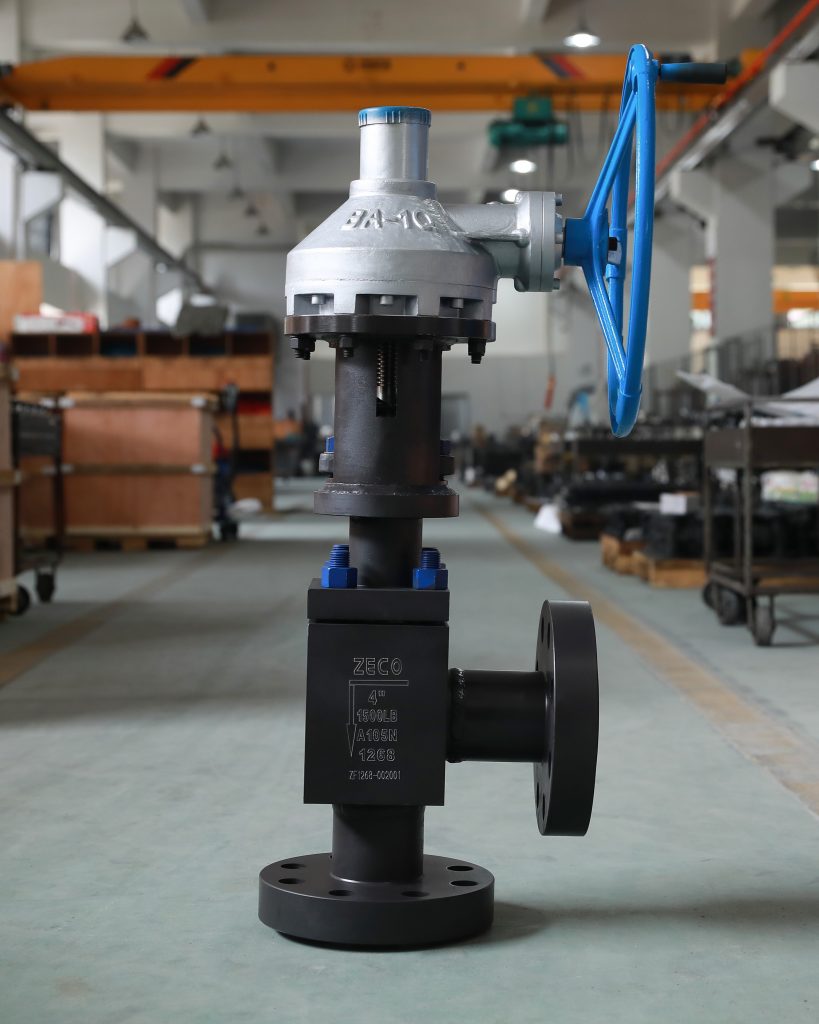
Construction of Globe valves
Globe valves are made up of a valve body, valve disc, valve bonnet, and valve stem. The opening and closing part of the globe valve is a plug-shaped valve disc with a flat or conical sealing surface, which moves linearly along the center line of the fluid. The stem is operated in lift type (the stem is rotated up and down by the handwheel, which remains in its position) and rotary lift type (the handwheel and stem rotate and move up and down together, the lock nut is located on the valve body).
How do globe valves work?
Globe valve is a forced seal valve where pressure must be applied to the disc/plug to establish a tight seal when the valve is closed. When the medium enters the valve from below the valve flap, the resistance to be overcome by the operating force is the friction of the stem and packing and the force generated by the pressure of the medium. When the force to close the valve is greater than the force to open the valve, the diameter of the stem should be increased to avoid distortion and bending of the stem.
With the introduction of the pressure seal globe valve, the direction of media flow in the globe valve is changed from above the valve flap to the valve cavity. In this case, the pressure of the medium will reduce the force of closing the valve and increase the force of opening the valve, so that the diameter of the stem can be reduced accordingly. At the same time, this type of valve is relatively sealed under the action of the medium.
The Function of globe valves in the pipeline system
Conventional globe valves can act as isolators and throttling valves. Although globe valves have a slightly higher pressure drop than straight-through valves (such as gate, plug, and ball valves), they can be used where the pressure drop through the valve is not a controlling factor.
Globe valves are widely used to control flow. The range of flow control, and the pressure drop, must be considered when designing the valve to avoid failure and to ensure satisfactory service. Valves for high differential pressure throttling services require specially designed spools.
In general, the maximum differential pressure across the valve flap should not exceed 20% of the maximum upstream pressure or 200 psi (1380 kPa), whichever is lower. For applications exceeding these differential pressure limits, valves can be designed with special trims.
Performance of Globe Valve
Advantages of Globe Valve
- Good shut-off capability
- Moderate to good throttling capacity
- Shorter stroke (compared to gate valves)
- Available in T, Y and angle patterns, each offering unique features
- Easily machined or resurfaced seats
- Stem not attached to the valve plate, valve can be used as a shut-off check valve
Disadvantages of Globe Valve
- Higher pressure drop (compared to gate valves)
- Greater force or larger actuator is required to seat the valve (pressure below the seat)
- The throttled flow below the valve seat and shut-off flow above the valve seat
Related Tags :
Zeco Valve is a professional globe valve manufacturer.
Ten articles before and after
Principle and Operation Method of Globe Valve
What Is a Butterfly Valve Used For?
What Is the Function of the Globe Valve?
Advantages and Disadvantages of Gate, Butterfly, Globe, Ball, and Plug Valves(Part 1)
Advantages and Disadvantages of Gate, Butterfly, Globe, Ball, and Plug Valves(Part 2)
Maintenance of Pneumatic Ball Valves
Cause and Effect of Corrosion of Pneumatic Ball Valves (Part 3)
Cause and Effect of Corrosion of Pneumatic Ball Valves (Part 2)
Cause and Effect of Corrosion of Pneumatic Ball Valves (Part 1)
What Should be Pay Attention to When Installing a Pneumatic Ball Valve?