According to ASME B16.5, the steel flange has seven pressure ratings: Class 150-300-400-600-900-1500-2500, which is very clear. The Class 300 flange can withstand more pressure than the Class 150, because the Class 300 flange needs to be made of more material to withstand greater pressure. However, the pressure capacity of the flange depends on many factors. The pressure rating of the flange is expressed in pounds, and a pressure rating has a different representation. For example, 150Lb, 150Lbs, 150# and Class 150 mean the same.
Examples of Pressure Rating
The bearing capacity of flanges varies with temperature. As the temperature increases, the bearing capacity of the flange decreases. For example, the Class 150 flange has a pressure capacity of 270 PSIG at room temperature; has a pressure capacity of 180 PSIG at 400℉; has a pressure capacity of 150 PSIG at 600℉; has a pressure capacity of 75 PSIG at 800℉.
In other words, when pressure falls, temperature rises, and vice versa. Valve Flanges can be made of a variety of materials, such as stainless steel, cast iron, ductile iron, carbon steel, and so on, each with a different pressure rating. The following figure shows an example of a flange in NPS12. As you can see, the diameter of the flange inner hole and face is the same. However, the flange outside diameter, bolt hole center circle diameter, and bolt hole diameter increase with the increase of the pressure level. The number and diameter of bolt holes are: CL150 – 12 x 25.4 CL300 – 16 x 28.6 CL400 – 16 x 34.9 CL600 – 20 x 34.9 CL900 – 20 x 38.1 CL1500 – 16 x 54 CL2500 – 12 x 73
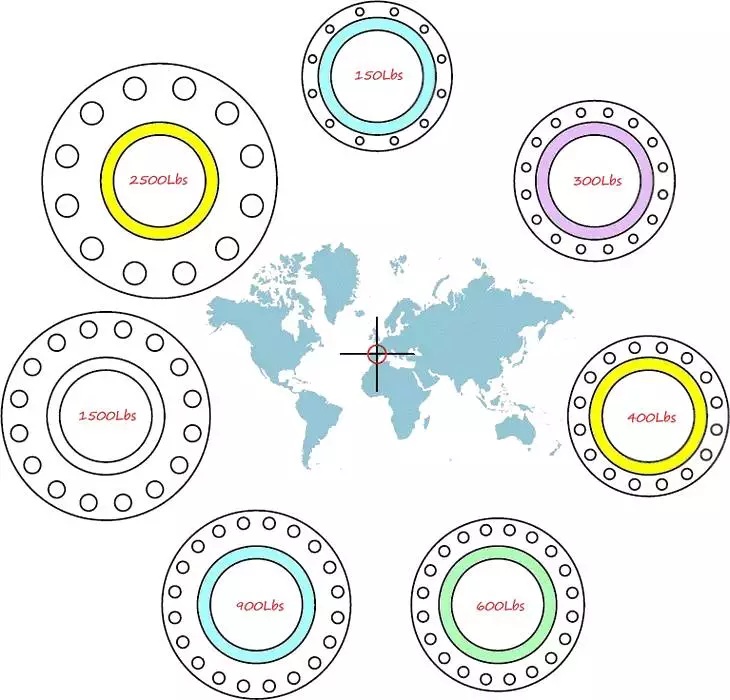
Examples of Pressure Temperature Rating
The pressure-temperature rating means the maximum allowable working gauge pressure (pressure in Bar) of the material and class at the rated temperature (Celsius). The linear insertion method can be used to determine the intermediate temperature, but insertion between flange levels is not allowed. Flange joints can be suitable for pressure-temperature ratings if the bolts and gaskets of the flange joints meet the relevant limitations and the alignment and assembly of the flange joints are in accordance with standards.
The rated temperature corresponding to the rated pressure is the case temperature of the pressure vessel of the flange and the flange pipe. In general, this temperature is the same as the temperature of the stored fluid. When the temperature is – 29 ℃ (- 20 ℉), the following rating, shall be no greater than – 29 ℃ (- 20 ℉) rating.
CARBON STEEL FLANGE RATING CHART
ANSI FLANGE ASTM A105, A350 Gr. LF2/LF6 Class 1
The flange rating table shows the maximum pressure for flanges of classes 150/300/400/600/900/1500/2500 at increasing temperatures (Celsius or Fahrenheit) – in PSI
Temperature (in F°) | 150# | 300# | 400# | 600# | 900# | 1500# | 2500# |
< 100 | 285 | 740 | 985 | 1480 | 2220 | 3705 | 6170 |
200 | 260 | 680 | 905 | 1360 | 2035 | 3395 | 5655 |
300 | 230 | 655 | 870 | 1310 | 1965 | 3270 | 5450 |
400 | 200 | 635 | 845 | 1265 | 1900 | 3170 | 5280 |
500 | 170 | 605 | 805 | 1205 | 1810 | 3015 | 5025 |
600 | 140 | 570 | 755 | 1135 | 1705 | 2840 | 4730 |
650 | 125 | 550 | 730 | 1100 | 1650 | 2745 | 4575 |
700 | 110 | 530 | 710 | 1060 | 1590 | 2655 | 4425 |
750 | 95 | 505 | 675 | 1015 | 1520 | 2535 | 4230 |
800 | 80 | 410 | 550 | 825 | 1235 | 2055 | 3430 |
850 | 65 | 320 | 425 | 640 | 955 | 1595 | 2655 |
900 | 50 | 230 | 305 | 460 | 690 | 1150 | 1915 |
950 | 35 | 135 | 185 | 275 | 410 | 685 | 1145 |
1000 | 20 | 85 | 115 | 170 | 255 | 430 | 715 |
Hydrostatic Test Pressure (in Psig) | 450 | 1125 | 1500 | 2225 | 3350 | 5575 | 9275 |
The flange rating table shows the maximum pressure for flanges of classes 150/300/400/600/900/1500/2500 at increasing temperatures (Celsius or Fahrenheit) – in bars
Temperature in C° | 150# | 300# | 400# | 600# | 900# | 1500# | 2500# |
-29 / 38 | 19.6 | 51.1 | 68.1 | 102.1 | 153.2 | 255.3 | 425.5 |
50 | 19.2 | 50.1 | 66.8 | 100.2 | 150.4 | 250.6 | 417.7 |
100 | 17.7 | 46.6 | 62.1 | 93.2 | 139.8 | 233 | 388.3 |
150 | 15.8 | 45.1 | 60.1 | 90.2 | 135.2 | 225.4 | 375.6 |
200 | 13.8 | 43.8 | 58.4 | 87.6 | 131.4 | 219 | 365 |
250 | 12.1 | 41.9 | 55.9 | 83.9 | 125.8 | 209.7 | 349.5 |
300 | 10.2 | 39.8 | 53.1 | 79.6 | 119.5 | 199.1 | 331.8 |
325 | 9.3 | 38.7 | 51.6 | 77.4 | 116.1 | 193.6 | 322.6 |
350 | 8.4 | 37.6 | 50.1 | 75.1 | 112.7 | 187.8 | 313 |
375 | 7.4 | 36.4 | 48.5 | 72.7 | 109.1 | 181.8 | 303.1 |
400 | 6.5 | 34.7 | 46.3 | 69.4 | 104.2 | 173.6 | 289.3 |
425 | 5.5 | 28.8 | 38.4 | 57.5 | 86.3 | 143.8 | 239.7 |
450 | 4.6 | 23 | 30.7 | 46 | 69 | 115 | 191.7 |
475 | 3.7 | 17.4 | 23.2 | 34.9 | 52.3 | 87.2 | 145.3 |
500 | 2.8 | 11.8 | 15.7 | 23.5 | 35.3 | 58.8 | 97.9 |
Notes:
- ASTM A105: An extended exposure to temperatures above 425°C, converts the carbide phase of steel to graphite (therefore this material is not recommended for constant temperatures above this value.
- ASTM A350 LF6: shall not be used for temperatures above 260 C°
ANSI FLANGE ASTM A350 Gr. LF3, A350 LF6, Class 2
The flange rating chart shows the maximum pressure for flanges of classes 150/300/400/600/900/1500/2500 at increasing temperatures (Celsius or Fahrenheit) – in PSI
Temperature in °F | 150# | 300# | 400# | 600# | 900# | 1500# | 2500# |
-20 to 100 | 290 | 750 | 1000 | 1500 | 2250 | 3750 | 6250 |
200 | 260 | 750 | 1000 | 1500 | 2250 | 3750 | 6250 |
300 | 230 | 730 | 970 | 1455 | 2185 | 3640 | 6070 |
400 | 200 | 705 | 940 | 1410 | 2115 | 3530 | 5880 |
500 | 170 | 665 | 885 | 1330 | 1995 | 3325 | 5540 |
600 | 140 | 605 | 805 | 1210 | 1815 | 3025 | 5040 |
650 | 125 | 590 | 785 | 1175 | 1765 | 2940 | 4905 |
700 | 110 | 570 | 755 | 1135 | 1705 | 2840 | 4730 |
750 | 95 | 505 | 670 | 1010 | 1510 | 2520 | 4200 |
800 | 80 | 410 | 550 | 825 | 1235 | 2060 | 3430 |
850 | 65 | 270 | 355 | 535 | 805 | 1340 | 2230 |
900 | 50 | 170 | 230 | 345 | 515 | 860 | 1430 |
950 | 35 | 105 | 140 | 205 | 310 | 515 | 860 |
1000 | 20 | 50 | 70 | 105 | 155 | 260 | 430 |
ANSI FLANGE ASTM A350 Gr. LF1
The flange rating table shows the maximum pressure for flanges of classes 150/300/400/600/900/1500/2500 at increasing temperatures (Celsius or Fahrenheit) — in PSI
Temperature °F | 150# | 300# | 400# | 600# | 900# | 1500# | 2500# |
-20 to 100 | 235 | 620 | 825 | 1235 | 1850 | 3085 | 1545 |
200 | 215 | 560 | 750 | 1125 | 1685 | 2810 | 4680 |
300 | 210 | 550 | 730 | 1095 | 1640 | 2735 | 4560 |
400 | 200 | 530 | 705 | 1060 | 1585 | 2645 | 4405 |
500 | 170 | 500 | 665 | 995 | 1495 | 2490 | 4150 |
600 | 140 | 455 | 610 | 915 | 1370 | 2285 | 3805 |
650 | 125 | 450 | 600 | 895 | 1345 | 2245 | 3740 |
700 | 110 | 450 | 600 | 895 | 1345 | 2245 | 3740 |
750 | 95 | 445 | 590 | 885 | 1325 | 2210 | 3685 |
800 | 80 | 370 | 495 | 740 | 1110 | 1850 | 3085 |
850 | 65 | 270 | 355 | 535 | 805 | 1340 | 2230 |
900 | 50 | 170 | 230 | 345 | 515 | 860 | 1430 |
950 | 35 | 105 | 140 | 205 | 310 | 515 | 860 |
1000 | 20 | 50 | 70 | 105 | 155 | 260 | 430 |
Related Tags :
Ten articles before and after
Monel alloy for anti-corrosion forged valves – Zeco | API 602 forged valve manufacturer
Do You Know the Types of Valve Flange Sealing Surfaces? – Zeco | API 602 forged valve manufacturer
Flash evaporation and cavitation of forged steel valves – Zeco | API 602 forged valve manufacturer
Silicone rubber sealing materials for forged steel valve – Zeco | API 602 forged valve manufacturer