316 stainless steel has better corrosion resistance than 304 stainless steel and has good corrosion resistance in the production of pulp and paper. Moreover, 316 stainless steel is also resistant to erosion by marine and aggressive industrial atmospheres
In general, 304 stainless steel and 316 stainless steel have little difference in chemical resistance but differ in certain media.
The stainless steel originally developed was 304. In certain cases, this material is sensitive to pitting corrosion. An additional 2-3% increase in molybdenum reduces this sensitivity, which gives birth to 316. In addition, the additional molybdenum can also reduce the corrosion of certain hot organic acids.
316 stainless steel has almost become the standard material for the food and beverage industry. Due to the shortage of molybdenum in the world and the high nickel content in 316 stainless steel, the price of 316 stainless steel is higher than that of 304 stainless steel.
Pitting corrosion is a phenomenon mainly caused by deposition corrosion on stainless steel surfaces due to the lack of oxygen to form a chromium oxide protective layer.
Especially in small valves, the possibility of deposits on the valve plate is small, so pitting corrosion is rare.
In all types of aqueous media (distilled water, drinking water, river water, boiler water, sea water, etc.), 304 stainless steel and 316 stainless steel have almost the same corrosion resistance, unless the content of chloride ion in the medium is very high, then 316 stainless steel is more suitable.
In most cases, the corrosion resistance of 304 stainless steel and 316 stainless steel is not much different, but in some cases, it may vary widely, and specific analysis is required. In general, valve users should be aware of the fact that they should select the material of the container and the pipe according to the condition of the medium. We do not recommend materials to the user.
SS316 & SS316L Heat resistance:
316 stainless steel has good oxidation resistance in intermittent use below 1600 °C and continuous use below 1700 °C. In the temperature range of 800-1575 degrees, it is preferable not to continuously apply 316 stainless steel, but when 316 stainless steel is continuously used outside this temperature range, the stainless steel has good heat resistance. 316L stainless steel has better carbide precipitation resistance than 316 stainless steel and can be used in the above temperature range.
Heat treatment:
Annealing is carried out at a temperature ranging from 1850 to 2050 degrees, followed by rapid annealing and rapid cooling. 316 stainless steel cannot be hardened by heat treatment.
SS316 & SS316L Welding:
316 stainless steel has good welding properties. All standard welding methods can be used for 316 stainless steel welding. When welding, 316Cb, 316L, or 309Cb stainless steel filler rods or welding rods can be used according to the application. For best corrosion resistance, the welded section of 316 stainless steel requires post-weld annealing. If 316L stainless steel is used, post-weld annealing is not required.
SS304, SS304L, SS316, SS316L Mechanical properties:
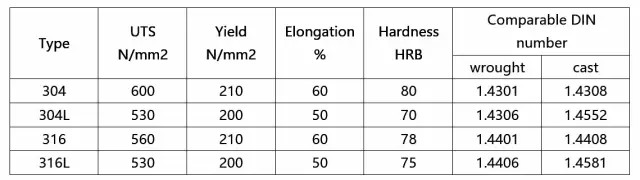
Among all steels, austenitic stainless steel has the lowest yield point. Therefore, from the viewpoint of mechanical properties, austenitic stainless steel is not the best material for the valve stem. To ensure certain strength, the diameter of the valve stem will increase. The yield point cannot be increased by heat treatment but can be improved by cold forming.
Magnetic property:
Due to the wide application of austenitic stainless steel, it gives people the wrong impression that all stainless steels are not magnetic. Austenitic stainless steel can be understood as non-magnetic, as is the case with quenched forged steel. However, 304 stainless steel processed by cold forming will be somewhat magnetic. For cast steel, if it is 100% austenitic stainless steel, it is not magnetic.
Low carbon type of stainless steel:
The corrosion resistance of austenitic stainless steel comes from the chromium oxide protective layer formed on the metal surface. If the material is heated to a temperature between 450 ° C and 900 ° C, the structure of the material changes, and chromium carbide forms along the edges of the crystal. Thus, a chromium oxide protective layer cannot be formed at the edge of the crystal, resulting in a decrease in corrosion resistance. This type of corrosion is called “intergranular corrosion.”
Thus, 304L stainless steel and 316L stainless steel are developed to resist this kind of corrosion. Both 304L stainless steel and 316L stainless steel have lower carbon content. Because of the reduced carbon content, chromium carbide is not produced and no intergranular corrosion occurs.
It should be noted that higher intergranular corrosion sensitivity does not mean that non-low carbon materials are more susceptible to corrosion. This sensitivity is also higher in high chlorine environments.
Please note that this phenomenon arises at high temperatures (450 ° C – 900 ° C). Usually, soldering is the direct cause of reaching this temperature. For common soft seat butterfly valves, the use of low carbon stainless steel does not make much sense since we do not weld on the valve plate, but most specifications require 304L stainless steel or 316L stainless steel.
What is 316 Stainless Steel?
316 stainless steel or grade 316 as it is popularly called is a common alloy of stainless steel which has an austenite property. It contains a maximum carbon content of 0.08% and 2-3% of molybdenum content. The additional molybdenum is responsible for its corrosion resistance property, acidic condition use, and resistance to pitting and increased temperature.
316 Stainless Steel Properties
The 316 stainless steel is applicable in different rapid prototyping operations for different functions based on its properties. Below are some of its important properties:
- It has high strength so you can mold it into different shapes without cracking
- It has a high resistance to corrosion and pitting; hence it can be used to fabricate materials that will be exposed to chemicals and acids.
- It has a good form and weld property
- The elastic modulus is about 193GPa
- The melting point ranges from 13710C – 13990C
- The minimum rate of its tensile strength is 515MPa
- Its density is 7.98g/cm3
Applications of 316 Stainless Steel
316 stainless steel materials are used to fabricate products employed in areas where corrosive resistance is necessary. Examples of such uses are in making heat exchangers, pieces of pharmaceutical and photographic equipment, pumps, and parts constantly exposed to the marine environment. This alloy is also suitable for evaporators and apparatus for chemical processes.
What is 316L Stainless Steel?
316l stainless steel or officially known as Grade 316l has a lower carbon content compared to 316 stainless steel. It contains 0.03 maximum carbon content and molybdenum in its composition. This low carbon content reduces the effect of carbide precipitation during sheet metal fabrication processes such as welding.
316L Stainless Steel Properties
The 316l stainless steel is also applicable in different rapid prototyping operations for different functions based on its properties. Below are some of its important properties:
- It has a large resistance to creep
- It has an excellent ability to take different forms
- At an elevated temperature, 316L ruptures and has a good tensile strength
- The most significant property of 316L stainless steel is that it has less carbon and molybdenum than 316 steel. Hence, it has better corrosive resistance compared to 316.
Applications of 316L Stainless Steel
The 316l stainless steel is a common material used in the fabrication of equipment and materials by various industries including:
- Food processing and chemical industries
- Marine
- Jewelry
- Water treatment companies
- power generation
316 vs 316L Stainless Steel: What’s the Difference?
Stainless steel is a broad category of steel alloys that have some proportion of chromium that protects the metal from corrosion and related damage. The amount of chromium in the alloy — as well as the amounts of other metallic elements — differs depending on which variation of stainless steel you’re working with.
316 stainless steel is a popular alloy that possesses molybdenum. Unlike 304 steel, the most common form of stainless steel, it possesses enhanced resistance to corrosion from chloride and other acids. This makes it ideal for outdoor applications in marine environments or applications that risk potential exposure to chloride.
316 steel comes in different varieties, including 316L. 316L stainless steel possesses less carbon and molybdenum than typical 316 steel, which gives the two alloys different characteristics. This article will explore the fundamental differences between the alloys so you can choose the best fit for your application.
Even though 316 and 316L have high similarities, their prices are approximately the same, we can also differentiate them in their composition, mechanical properties, and other aspects.
1. Composition
The key difference between standard 316 stainless steel and SS316L is the composition, 316 contains more molybdenum than 316L, which results in increased resistance to pitting and crevice corrosion and better protection when exposed to high-chloride chemicals and acids. In addition, 316L is the low-carbon variation of 316 because it has a lower carbon content than 316, in contrast, grade 316H is the higher carbon version. Type 316 stainless steel contains up to 0.08% carbon while the maximum carbon content of type 316L is 0.03%. The 316L will also be softer than 316 due to the lower carbon. For the percentages of other elements, 316 and 316 have almost no difference.
2. Mechanical Properties
Compare stainless steel 316 and 316L in mechanical properties, including yield strength, tensile strength, elongation, and hardness as below.
3. Application
316L is a better choice for the application or the fabrication process that needs a lot of welding because the lower carbon content minimizes deleterious carbide precipitation. But 316 can be annealed to resist weld decay. And, 316L is the main choice for medical implants, rather than SS316.
Related Tags :
Ten articles before and after
Thread selection and application for forged steel valves – Zeco | API 602 forged valve manufacturer
Working principle of forged steel check valves – Zeco | API 602 forged valve manufacturer
Selection of valve materials for several acidic media – Zeco | API 602 forged valve manufacturer
Factors affecting quenching crack or heat treatment crack – Zeco | API 602 forged valve manufacturer
Brief analysis on forging crack and heat treatment crack – Zeco | API 602 forged valve manufacturer