Casting valve is cast into the valve, the general casting valve pressure grade is relatively low (such as PN16, PN25, PN40, but there is also high pressure, can be to 1500LD, 2500LB), most of the caliber is more than DN50. Forging valves are forged out. They are generally used in high grade pipelines. The caliber is small, and they are generally below DN50.
What is Casting?
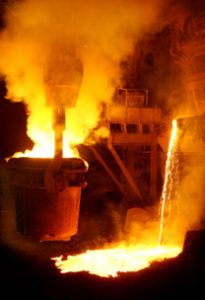
The core of casting is in heating the component metal to a molten state and pouring it into a prepared mold. Though the mold is most often a die, sand and investment casting are often used for specific alloys or for parts with unusual dimensions and design. Once the metal cools into the basic desired shape, the metalworker then finishes the part with the details requested by the client either by hand or through further machining.
Casting production of blank cost is low, for complex shape, especially with complex cavity parts, more can show its economy; At the same time, it has wide adaptability and good comprehensive mechanical properties.
But the materials needed for casting production (such as metal, wood, fuel, molding materials, etc.) and equipment (such as metallurgical furnace, sand mixing machine, molding machine, core-making machine, shaker, shot blasting machine, cast iron plate, etc.) are more, and will produce dust, harmful gas and noise and pollute the environment.
History of Casting
Casting is a kind of metal hot working technology that has a history of about 6000 years. In 3200 BC, castings of bronze frogs appeared in Mesopotamia. Between 13 BC and 10 BC century, China has entered the heyday of bronze castings, the process has reached a fairly high level, such as the Shang Dynasty Simuwu square Ding weighing 875 kg, the Warring States Dynasty Jinghou Yi Zunpan and the Western Han Dynasty transparent mirror are the representative products of ancient casting. Early casting was greatly influenced by pottery, and most of the castings were tools or utensils for agricultural production, religion, life and other aspects, with strong artistic color. In 513 BC, China produced the first cast iron in written records in the world – the Jin Casting Ding (about 270 kg). Around the 8th century, Europe began to produce cast iron. After the industrial revolution in the 18th century, castings entered a new period of serving large industries. In the 20th century, the rapid development of casting, has developed the ductile iron, malleable cast iron, ultra-low carbon stainless steel and aluminum copper, aluminum silicon, aluminum magnesium alloy, titanium base, nickel base alloy and other casting metal materials, and invented a new process for gray cast iron to carry out the treatment. After the 1950s, new technologies such as wet sand high pressure molding, chemical hardening sand molding, core making, negative pressure molding, and other special casting and shot blasting were introduced.
Types of Casting
There are many kinds of casting. According to the modeling method, it is customarily divided into 0 ordinary sand casting, including wet sand type, dry sand type and chemical hardening sand type 3. (2) special casting, press molding materials and can be divided into natural mineral sand as the main special casting molding materials (e.g., investment casting, mold casting, shell mold casting foundry, negative pressure casting, mold casting, ceramic mold casting, etc.) and metal as the main mold material of special casting (such as metal mold casting, pressure casting, continuous casting, low pressure casting, centrifugal casting, etc.).
Casting Process
Casting process usually includes: (casting (containers) makes liquid metal solid casting, casting according to the materials can be divided into sand mold, metal, ceramic, mud, graphite, etc., can be divided by use disposable, semi permanent and permanent type, mold preparation quality are the main factors influencing the casting quality; The melting and pouring of casting metal, casting metal (casting alloy) mainly includes cast iron, cast steel and cast non-ferrous alloy; (3) casting treatment and inspection, casting treatment, including the removal of core and casting surface foreign bodies, casting riser removal, shovel grinding burr and other protrusion, heat treatment, shaping, antirust treatment and rough machining. Inlet pump valve
What is Forging?
Though the heating of the component metal is also essential to forging, heating for this method never gets so intense as to make said metal melt. Instead, it’s merely made hot enough to make it possible for the metalworker to conduct hammer forging or otherwise manipulate it into a prepared die. Gigantic presses are used for larger products and the method of forging can vary depending on the desired final product; forging may be a hot or cold forging process, for example, or may make use of an open or closed die.
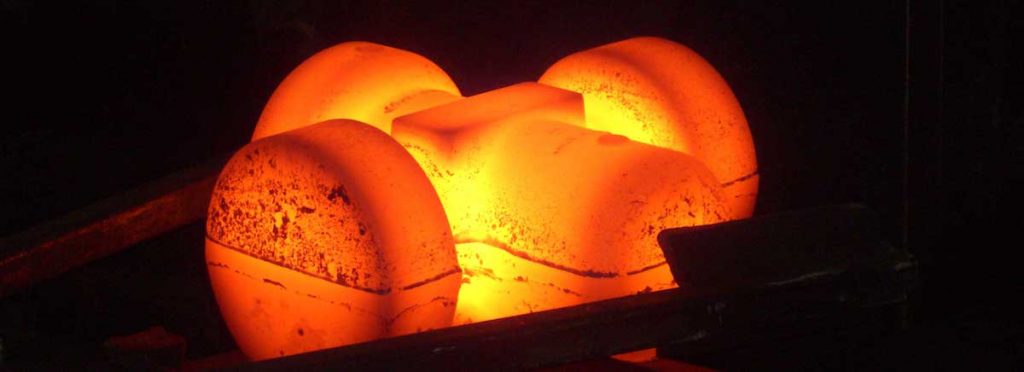
Forging: is the use of forging machinery on the metal billet pressure, plastic deformation to obtain a certain mechanical properties, a certain shape and size of forgings processing method.
One of the two main components of forging. Through forging can eliminate the metal as cast loose, welding holes, the mechanical properties of forgings is generally better than the same material castings. For the important parts with high load and severe working conditions in machinery, forgings are mostly used in addition to the plate, profile or welding parts with simple shape that can be rolled.
Types of Forging
Forging according to the forming method can be divided into: 0 open forging (free forging). The use of force or pressure to make the metal between the upper and lower two anti-iron (anvil block) deformation to obtain the required forgings, mainly manual forging and mechanical forging. ② Closed mode forging. The metal blank is deformed under pressure in the forging die chamber of a certain shape, and the forging can be divided into die forging, cold forging, rotary forging, extrusion and so on. According to the deformation temperature forging can be divided into hot forging (the processing temperature is higher than the recrystallization temperature of the blank metal), warm forging (lower than the recrystallization temperature) and cold forging (normal temperature).
The forging material is mainly a variety of components of carbon steel and alloy steel, followed by aluminum, magnesium, titanium, copper and its alloy. The original state of the material includes rods, casting chains, metal powders and liquid metals. The ratio of the cross sectional area of the metal before deformation to the die sectional area after deformation is called the forging ratio. Correct choice of forging than to improve product quality, reduce the cost has a great relationship.
Forging Process
The basic process of forging consists of a few traditional steps:
- the raw material (steel blocks, ingots, billets) is cut into smaller parts if needed
- the raw material is heated to reach the required forging temperature (the application of heat is necessary to make the material ductile and malleable); the forging temperature depends on the type of metal and is achieved by positioning the material into a furnace/oven;
- the heated metal is shaped into the required form by applying mechanical forces (pressure).
- the semifinished part undergoes machining, finishing and heat treatment
At the end of the process, the resulting product features extreme strength, impact toughness and wear resistance thanks to the metallurgical recrystallization and grain refinement resulting from the applied thermal and mechanical treatment.
Why use Castings?
The main benefit of casting is to create components that are too large, complex, or otherwise unsuitable for the forging. We can forge part sizes up to 18” in length and weights up to 100 pounds. But if you are in need of an end product weighing 5000 pounds, casting would be a more suitable option. So use casting when:
- Your part is too large to forge.
- The part is complicated (contact us for advice on this)
- Part requires custom alloys added
Why use Forging?
If your end piece is able to be forged, it should be forged. This will give your part better strength, more consistency, a tighter grain structure, and longer lifetime. Reach out to our engineers to see if forging is right for your project.
Is Cast or Forged better?
All in all, casting tends to be the less expensive, more versatile option, however; forging offers superior strength and wear resistance. The question of which is better depends on the top priorities for your project. If low cost, exotic alloys, and complex geometries are a priority, casting would probably be the way to go. However, if strength and structural integrity are concerned, forging may be the better option.
Forged vs Cast
Forging | Casting | |
Structural Integrity | Far superior in strength compared to castings. High level of material predictability | Products tend to be more porous and more susceptible to breakage compared to forgings |
Tolerance | Not well suited to highly complex geometries | Allows for a high level of detail. Able to adhere to tight tolerances |
Product Size | Limited in terms of the size and thickness of the metal (larger = more difficult) | Compatible with a wide range of sizes |
Material Selection | Selection of alloys is limited | Compatible with nearly all types of metal |
Secondary Operations | Usually requires secondary operations to refine and finish product to exact specifications | Provides primary product that will usually require very few secondary operations |
Cost | Tends to be most cost effective for medium to large production runs | Generally, less expensive compared to forging, but it depends on the specific casting method used. |
Related Tags :
Ten articles before and after
News – metal seat dual plate check valves ready for shipment | Industrial valve manufacturer
News – floating ball valve | Industrial valve manufacturer
News – Check Valve | Industrial valve manufacturer
News – Check valve function and classification | Industrial valve manufacturer
News – What are the advantages and disadvantages of the globe valve | Industrial valve manufacturer
News – The characteristics of ball valves and butterfly valves | Industrial valve manufacturer
News – Iron Ore and Steel Prices Climb to Record Highs | Industrial valve manufacturer
News – Electric and pneumatic actuators | Industrial valve manufacturer
News – Check Valve The New Developing Direction | Industrial valve manufacturer