What is a Parallel Slide Gate Valve?
Slide Gate valves are linear motion valves used for full bore fluid flow without any change in direction. They are designed to provide an efficient method for controlling the flow of free-flowing dry bulk materials. It is an ideal valve for transmission and interruption of fluid movement which is mainly suitable for crude, gas pipes, petrochemical oil depots, and other pipelines in the industrial process. The face of this type of valve is mostly parallel and hence they are often referred to as Parallel Slide Gate valves. They are generally either fully open or fully closed and are not normally used to regulate flow. However, slide gate valves can also be installed at the outlet of an oil pump to regulate and control the flow of liquid. A typical slide gate valve is shown in the figure below:
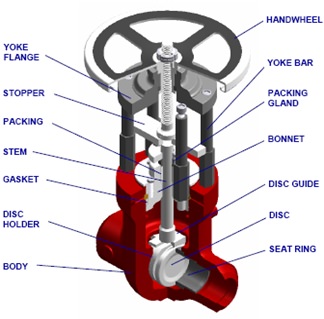
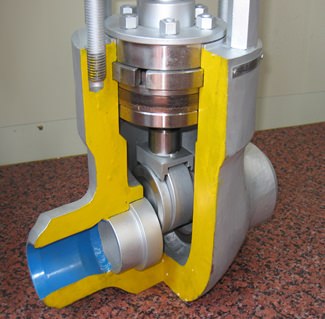
How does Parallel Slide Gate Valve work?
The parallel gate consists of the valve body, bonnet, disc assembly, stem, and top works, each side of the valve can withstand full differential pressure. A replaceable double-disc seal with double bleeding and blocking (DBB) is created by a combination of internal pressure and spring force. The floating seat can automatically relieve pressure when the middle chamber is under pressure. When the pressure in the cavity is greater than that in the channel, the cavity pressure will be released to the channel. When the upstream pressure of the channel is greater than that of the downstream (the valve is closed), the pressure in the middle chamber will be discharged to the upstream side channel. When the upstream pressure of the channel is equal to the downstream (the valve is fully open), the pressure in the middle chamber can realize the discharge of bilateral channels. The valve seat automatically resets after pressure relief.
- When the pressure inside the valve (cavity, inlet and outlet) is equal or no pressure, the disc is closed and the PTFE sealing ring on the seat surface forms the initial seal. The seat ring can automatically clean the sealing surface on both sides of the disc every time the valve is opened or closed.
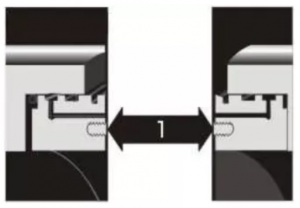
- Medium pressure acting on the inlet side disc, forcing the disc moves toward the exit seat PTFE ring, compress until it compaction in the metal valve seat sealing surface, formed the hard and soft double seal, namely PTFE to metal seal, metal to metal seal, export seat also is pushed to the body seat hole on the end face of the O-ring seat ring and valve sealing.
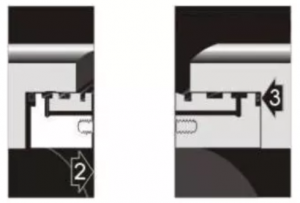
- The inlet seal forms after the pressure in the cavity relief, and the medium pressure forces the inlet seat to move to the disc. At this time, the inlet seat produces soft PTFE to metal seal and metal-to-metal seal, the O-ring guarantees the sealing of the seat outer ring with the valve body.
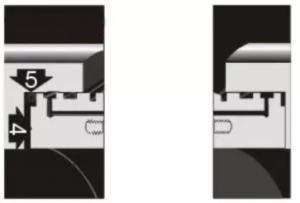
- Automatic pressure relief of the valve. When the pressure in the cavity of the valve body is greater than the pipe pressure, the inlet seat is pushed to the disc end of the upstream seat hole under the pressure difference, and the excess pressure between the upstream seat and the sealing surface of the disc of the valve body is discharged into the upstream pipe.
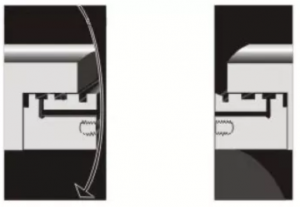
Features and Benefits of Parallel Slide Gate Valve
- 1. The parallel slide gate valve closes with a sliding action instead of the usual compression, so there is no tendency, notch, or indent on the sealing surfaces. The result of this action can bring better tightness to the disc on the seat-ring, and a longer lifetime for the discs and seat sealing surfaces.
- 2. parallel-slide gate valve has a cleaning function with intimate contact on the seats during the closing action. So if any impurities appear or tendency on the seats and discs, they are eliminated and the sealing contact is free from undesirable particles. It also reduces seat-bearing stress and guarantees long life. The wide flat seating can minimize the effect of minor damages on the surface as sealing occurs over the entire surface.
- 3. No additional power and a final surge of torque are required to make the seating leak-tight because sealing is obtained by sliding, not by compression. Furthermore, the valve operates with low energy because there is no need for high energy when opening the valves.
- 4. Actuator size of the parallel slide gate valve can be much smaller than the wedge type. Hammering or impacting hand wheels are not usually necessary on this valve.
- 5. The low torque operation brings less stress and fatigue to the trim. This gives a longer lifetime and greater leak-tight reliability.
- 6. When the valve is closed, the exact position of the stem does not play a great role. As a result, there is no problem with the differences in the thermal expansion coefficient of the materials. Also, the actuators can be stopped with general position switches.
- 7. The possible jam found in wedge gate valves as a result of body contraction will never occur in parallel slide gate valves.
- 8. In wedge gate valves, the wedge must have positioning guides on its slides to keep it in line while closing under full flow conditions. These guides are not usually made of any hard materials and tend to wear, and eventually may cause jamming.
Comparison Parallel Slide Gate Valve vs Wedge Gate Valve
Our Parallel Slide Gate Valve design offers many advantages over double disc wedge gate valves in providing tight reliable
shut-off in water and steam service.
One of these advantages comes from the seating method used by these valves. Our Parallel Slide Gate Valve uses position seating allowing the line force in the system to assist in the sealing of the valve seat by holding the downstream disc firmly against the downstream seat. By comparison, a double-disc wedge gate valve relies upon torque force to wedge the disc into the valve body to provide shut-off. This requires the valve seat in a double disc wedge gate to actually deform to provide seating. Over a short period of time, this can lead to permanent deformation of the seat allowing a leak path to occur. Position seating also requires less torque to open and close than torque seating. This allows for use of a smaller actuator to operate our valve, thereby reducing operational costs.
Also, the wide flat seating surface of our valve offers an advantage in sealing surface area. Our valve has a seating surface width of up to two inches. This prevents minor scratches or seat deformation from becoming a leak path. Since a double disc wedge gate valve relies upon a line contact seating surface, it has a very thin seating surface area. A line contact seat increases the probability that a minor seat inconsistency will become a leak path. Also, the greater seating surface of our valve provides for the distribution of bearing stresses over a large area thus reducing seat wear caused by everyday operation. Due to its wide flat seats and position-seated design, a parallel slide gate does not require reseating of the disc after a valve closed hot cools down. A double disc wedge gate, due to its torque seated design, may require that you reseat it after cooling due to contraction which may loosen a previously adequate seal.
In addition to the above advantages, our Parallel Slide Gate Valve also offers protection against thermally locking a valve in the closed position. This can occur when a hot valve in the closed position begins to cool. The larger valve body may cool faster than the disc causing the body to contract quicker trapping the discs between the body seats. This will then require increased torque to break the disc away from its seat. The two independent discs of the Parallel Slide Gate Valve, along with the position-seated design, allow for compensation for varying rates of thermal contraction, thereby preventing thermal binding from occurring. However, since a double disc wedge gate’s seating principle calls for wedging the disc into the body it cannot compensate for varying rates of contraction, and the valve can become jammed closed, requiring more torque than available to open the valve.
The seating principle of the Parallel Slide Gate Valve makes it far superior to the double disc wedge gate valve; with a more forgiving seating method that compensates for minor seat variations and uses internal forces to provide reliable tight sealing
The problems of solid wedge gate valves:
- 1. Malfunction of disc opening due to Thermal Binding In wedge-type valves, thermal binding is caused by dimensional interference between wedge and seat, due to temperature differences and thermal expansion. Valves are commonly used at high.
- 2. Leakage problems due to thermal deformation Since the sealing of the valve is obtained by compression, enough surface pressure between discs and seats is necessary. The bodies should be designed to be thick and strong in order to stand against.
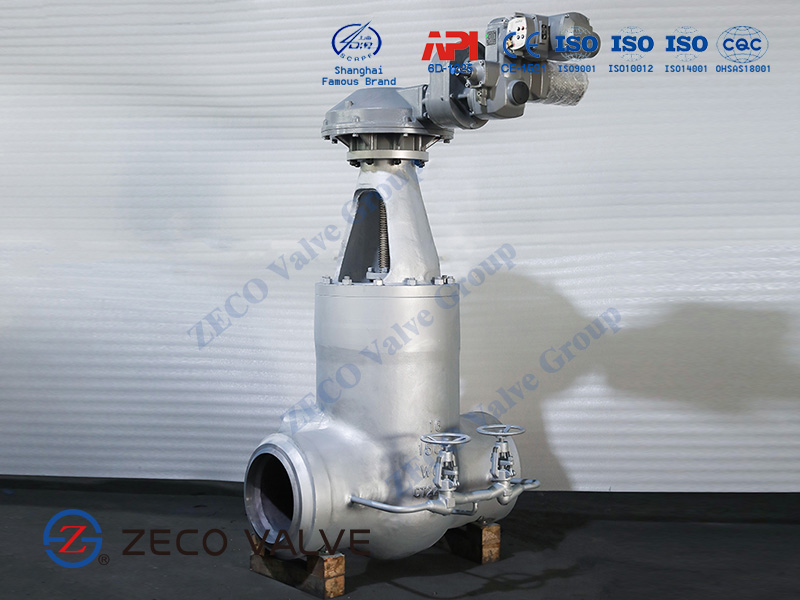
MAIN MATERIAL | Carbon, Alloy or Stainless Steel Titanium & Nickel Alloy(Hastelloy) Incoloy, Inconel, Monel, Super, Duplex, etc. |
---|---|
SIZES FROM | 1/2″ – 24″ (15mm – 600mm) |
CLASSES | ASME 900 / 1500 / 2500 / 3500 / 4500 |
SIZES FROM | Pneumatic, Electrical, Hydraulic Power Operated Parallel |
Related Tags :
Ten articles before and after
BELLOWS SEAL GLOBE VALVE (OS & Y , FLANGED TYPE)
The world young scientists (Wenzhou) summit 2019: Yongjia pump valve industry summit forum
New excellent valve product – Semi-ball valve
Promoting Green Casting is the Development Trend of Valve Casting Industry in the Future
API 6D Stainless steel/Carbon steel Spring Return Deadman Lever Operated Ball Valve
Concentric Butterfly Valve Stock/fast delivery Available-Europe Wareshouse