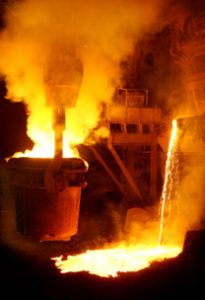
Valve Casting
The valve is used to change the passage section and the flow direction of the medium. It has the functions of diversion, cutoff, regulation, throttling, check, split or overflow relief. Valve castings are control components in pipeline fluid delivery systems. They come in a wide variety of sizes and sizes.
Valve castings are widely used in chemical, petrochemical, petroleum, paper, mining, electric power, liquefied petroleum gas, food, pharmaceutical, water supply, and drainage, municipal, mechanical equipment, electronics industry, urban construction, and other fields.
Types of Valve Casting
Lost Wax Casting: Is able to make cast steel valve components, like carbon steel, stainless steel, and other cast steel alloys. Lost wax casting is a precision casting method for valve components, so we can achieve good dimensions and tolerances, smoother surface. Stainless steel valve casting parts are widely used in silical sol casting process, which is another lost wax method. We can use this casting process for butterfly valves, ball valves, ect.
Lost Foam Casting: This casting method is more suitable for making precison cast iron valve parts, which can also get good surface finish and sizes, such net shape or near net shape valve castings will need no machining or just little machining allowance.
Sand Casting: Also a casting process for valve casting parts. Sand casting is suitable for both steel and iron valve castings. Compare with lost foam and lost wax castings, it is more suitable to make larger valve components, so normally, we will need to leave more machining allowance for further machining operation. The max weight we can cast is around 2 tons per piece.
Valve Sand Casting Process
Valve Investment Casting Process
Each of our valve body casting process is executed in strict accordance with the Standard Operation Procedure (SOP). The main valve body casting process of valve body casting manufacturing is as the following: Pouring simulation, Mold development, Raw material inspection, Wax pattern, Shell preparation, Metal pouring, Cleaning and Heat treatment, Inspection, Warehouse packaging, and Shipping.
- Mold Development
- The technical department develops the mold, and the quality department uses the three coordinates to carry out the dimensional inspection.
- Wax Pattern
- The workshop uses automatic waxing machines to set the waxing pressure, holding time, etc. and to produce high quality was patterns.
- Shell Preparation
- The workshop has 4 automatic production lines, able to produce 1800 sets of shells. We use hygrothermograph, aerometer, and PH to monitor humidity, temperature, and concentration of liquor aluminum chloride.
- Metal Pouring
- 4 sets of 500KG furnaces are in production, and 3 sets of 500KG spare furnaces are ready when capacity increases. The operators conduct rigorous tests to fulfill material requirements.
- Clean And Heat Treat
- The workshop is fully equipped with 8 heat treatment furnaces, 3 quenching furnaces, 1 central shot blasting machine and 11 large shot blasting machines.
- Inspection
- All blank dimensions are checked using a CMM. We have rockwell hardness machine, dynamic balance instrument, roundness meter, etc. The company’s quality department has certified employees to do UT, PT, MT testing.
Valve Sand Casting Process
Each of our valve body casting process is executed in strict accordance with the Standard Operation Procedure (SOP). The main valve body casting process of valve body casting is as the following: Pouring simulation, Mold development, Raw material inspection, Modeling (Core-Making), Melting, Metal pouring, Cleaning and Heat treatment, Inspection, Warehouse packaging, and Shipping
- Mold Development
- Design and produce molds according to the requirements of the drawings. Generally, wood molds can be used for single-piece production, plastic molds and metal molds are made for mass production, and templates can be made for mass castings. Our mold is mainly made of aluminum.
- Modeling (Core-Making)
- Includes modeling (forming the cavity of the casting with molding sand), core-making (forming the inner shape of the casting), and mold matching (putting the core into the cavity and closing the upper and lower flasks). Modeling is a key process in valve body casting process.
- Melting
- According to the required metal composition, the chemical composition is matched, and the appropriate melting furnace is selected to melt the alloy material to form a qualified liquid metal liquid (including qualified composition and qualified temperature)
- Metal Pouring
- Pour qualified molten metal into the sand box equipped with the mold. The pouring stage has high safety requirement, and we have rigorous process control to protect the safety of our employees.
- Clean And Heat Treat
- After the molten metal is poured and solidified, the molding sand is removed, and the gate and other attachments are knocked out to form the required casting.
- Inspection
- All blank dimensions are checked using a CMM. We have rockwell hardness machine, dynamic balance instrument, roundness meter, etc. The company’s quality department has certified employees to do UT, PT, MT testing.
Materials of Valve Casting Parts are as following:
Carbon Steel (mainy for high pressure valve castings): WCA, WCB, ZG25, ZG200-350, ASTM A216 WCA/WCB/WCC, GS25.
Stainless Steel: SS304, SS316, PH17-4, ASTM A351 CF8/CF8M/CF3/CF3M, ZG0Cr18Ni9, zg0Cr18Ni12Mo2, ZG00Cr18Ni10.
Gray Iron: HT200, HT250, HT300, HT350,GG15, GG20, GG30, FC200, FC250, FC300, ASTM A48 CLASS NO.20,NO.25,NO.30, NO.35.
Ductile Iron: QT400-18, QT500-7, QT600-3,GGG40, GGG50,GGG60, FCD450-70, FCD400-15, FCD500-7, FCD600-3, ASTM A536 ( 60-40-18,65-45-12, 80-55-06).
NO. | Materials | Pressure | Temperature | Medium | Grades |
1 | Gray cast iron | ≤1.0MPa | -10 °C ~ 200 °C | water, steam, air, gas, and oil | HT200, HT250, HT300, HT350 |
2 | Forgeable cast iron | ≤ 2.5MPa | -30 ~ 300 °C | water, steam, air and oil | KTH300-06, KTH330-08, KTH350-10 |
3 | Ductile iron | ≤4.0MPa | -30~350°C | water, steam, air and oil | QT400—15, QT450—10, QT500—7 |
4 | Acid-resistant high silicon ductile iron | ≤ 0.25MPa | below 120 °C | – | – |
5 | Carbon steel | ≤32.0MPa | -30~425°C | water, steam, air, hydrogen, ammonia, nitrogen and petroleum products | WC1, WCB, ZG25 and high quality steel 20, 25, 30 and low alloy structural steel 16Mn. |
6 | Copper alloy | ≤ 2.5MPa | -40 ~ 250 °C | water, seawater, oxygen, air, oil and other media | ZGnSn10Zn2 (tin bronze), H62, Hpb59-1 (brass), QAZ19-2, QA19-4 (aluminum bronze). |
7 | High-temperature copper | ≤17.0MPA | ≤570°C | steam and petroleum products | ZGCr5Mo, 1Cr5M0, ZG20CrMoV, ZG15Gr1Mo1V, 12CrMoV, WC6, WC9 and other grades. |
8 | Low-temperature steel | ≤ 6.4Mpa | ≥ -196 ° C | ethylene, propylene, liquid natural gas, liquid nitrogen and other media | ZG1Cr18Ni9 0Cr18Ni9 1Cr18Ni9Ti ZG0Cr18Ni9 |
9 | Stainless acid-resistant steel | ≤ 6.4Mpa | ≤ 200 ° C | Nitrite acid, acetic acid and other media | ZG0Cr18Ni9Ti ZG0Cr18Ni10 ZG0Cr18Ni12Mo2Ti ZG1Cr18Ni12Mo2Ti |
In recent years, the China Casting Valve Manufacturers realized the valve unattended strong automatic control, so the quality of the valve manufacturers to choose the valve to pay attention to which point?
I. parameters and specifications
So-called the parameters of the valve specifications can also be in short calls it the types of products, the principle of the valve consistent but the details are different, so is applicable to different places, such as the valve manufacturer of fire dampers in the mainstream of 3 c contains smoke fire damper and automatic smoke fire damper and so on all sorts of types, main control parameters and specification is the basis of choosing fire damper.
Ii. Applicable place and operating temperature
Cost-effective Cast Iron Gate Valve Manufacturer product identification will be clearly marked in the product operating temperature, it will directly determine its application, some inexpensive valve has certain versatility and generality, but as far as possible choose to install it in the main area, such as public buildings action temperature of fire dampers in exhaust system is relatively high, and the ordinary residential or commercial air conditioning system of action temperature of fire dampers in the 3 c is relatively low.
Iii. Functional requirements
For valve factory valves in the same product in different places have different requirements, so you choose 3 c before either from above or below the line of fire dampers in the choose and buy depends on its basic function and the applicable scope, such as fire damper, for example, still depends on whether you need 3 c fire valve has the function of automatic open and close, whether can meet the needs of normally open, if there is a remote control and signal output, and other functions.
Related Tags :
Ten articles before and after
Causes Of Failure And Damage Of Stainless Steel Globe Valves
China Casting Valve Manufacturers
Cast Iron Check Valve Supplier
How does the cryogenic Cast Iron Gate valve work?
Pressure Relief Valve Can Not Be Installed In Reverse
Cast Steel Ball Valve, Cast Steel Ball Valves Supplier
Precautions for The Use of Cast Iron Valves
China Industrial Valves Brand, DIN angle type Globe Valve Supplier
China Valve Manufacturers Teach You How to Maintain The Valve