What is the secret behind high functioning valves? What makes them better in performance? Is it the materials? Do the calibration machines matter that much? The truth is, all of these matters. Before even understanding the minute details of the industrial valve, one needs to know more about how valves are made.
This article will discuss the manufacturing of industrial valves from beginning to end. This would provide readers information about valve manufacturing
To Purchase Raw Materials
When our drawing, datasheet, and commercial offer get customers approved, we will send the Proforma Invoice for our customers, and waiting for them to sign back or release the contract for us. After the advance payment/deposit kicks into our account, we will start the procurement of raw materials for this case.
For industrial valves of raw materials, it has to consider various grades of steel casting body, forging steel body, or special alloy steel, duplex steel material.
Things to Note in Valve Manufacturing
The manufacture and inspection technology of valve rough is very complicated. The valve’s casting blank is a thin-walled shell with complicated structure. Casting requires a smooth surface, casting characters clear, especially to have a dense structure, and do not allow the occurrence of pores, shrinkage, cracks, sand and other defects. In order to meet the above requirements, a series of technological measures should be taken during casting, such as selecting molding materials with high fire resistance and controlling moisture of molding sand, and layer-by-layer compaction during molding to ensure the hardness of molding sand, adopt reasonable gating and riser system and strictly control pouring speed and temperature. Due to the high technical requirements, the casting process of valve rough is much more complicated than that of common castings.
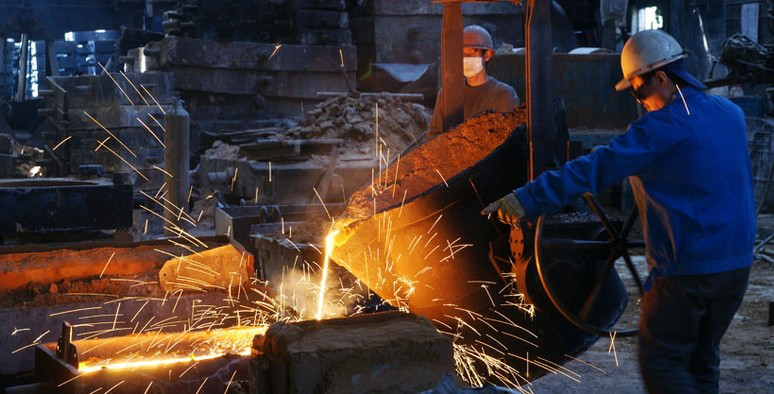
In addition, besides inspecting the size, position accuracy and appearance, some valves need to be inspected for metallographic structure, mechanical properties, corrosion resistance and non-destructive testing, etc. .
Machining
All the raw materials are inspected by our quality control department before the materials into the manufacturing process.
Through the issued the manufacturing procedure card to apply the raw materials from the warehouse supervisor for machining workshop. Body, bonnet, seat, and plug, etc are machined on CNC machines. after being machined our QA inspects and measures the dimensions again.
Things to Note in Valve Manufacturing
It’s very difficult to machine. Due to the variety of valve materials, except various cast iron, carbon steel, most of its high-strength, corrosion-resistant and high-hard material cutting performance is very poor, it is difficult to make parts meet the requirements of the machining precision and Surface roughness. The valve sealing surface of the geometry of the precision and Surface roughness requirements are very high, which increases the difficulty of machining the valve.
At the same time, the poor cutting performance of valve material brings many new problems to the machining method, tool angle and geometry shape, tool material, cutting parameters, process equipment and so on.
Valve parts are difficult to install on machine tools. Valve main parts of the structure, shape more complex, some parts are thin-walled, slender parts, poor rigidity. When machining on the machine tool, it is very difficult to locate and fix the fixture, so a complicated special fixture is often needed.
For some valve parts, the positioning accuracy of the base plane is lower and the Surface roughness is higher, sometimes even using non-machined surface positioning. The sealing surface and other parts of the processing accuracy and Surface roughness requirements are very high, it is difficult to ensure the quality of processing. Therefore, in order to meet the needs of technology, it is often necessary to improve the accuracy of positioning base surface and reduce the Surface roughness, or machining the positioning base surface on the non-machining surface, which increases the complexity of the valve manufacturing process.
Assembly
Assembly is the phase where technicians attach all the valve components to one another. Often times, the assembly is done by hand. It is at this point that technicians assign the valves production numbers as well as designation according to the regulations it follows such as DIN or API and the likes.
Pressure Test
After the complete assembly, we are going to transfer the valve to the hydrostatic bench for shell test, low-pressure test, seat leakage test. Witness by QA colleague, in accordance with drawing to see if the result meets relevant standards. If qualified then transfer to the painting area.
Inspection and Quality Control
After test & inspection, painting, functional test, the customers informed the third party to arrange the witness and inspect. And our quality assurance department records project name, tag number, model, process quality checks, furnace number, and all the details into our system.
We also supply various Ball Valve, Gate Valve, Check Valve, Globe Valves, Butterfly Valves, if you are interested in industrial valves, follow us quickly, our website: www.zecovalve.com
Related Tags :
Ten articles before and after
9 Ways to Extend the Service Life of Industrial Valves – Zeco Valve
What is an axial flow silent check valve?
How Does Resilient Seated Butterfly Valve Work? – Zeco Valve
What is the difference between a knife gate valve and slide gate valve?
How Does Flanged Gate Control Valve Work – Zeco Valve
What is the difference between globe valve and stop check valve?
Ball Valve vs. Gate Valve: Which is Better? – Zeco Valve