Check valves are found in almost every industrial application acting as one-way or non-return valves. Check valves are simple devices that perform a vital function by preventing reverse flows, preventing damage, and ensuring efficient operations. Different types of check valves are designed for a specific application.
Working Principle of Check Valves
As already stated, a check valve operates on the principle of differential pressure. For a check valve to open, it must attain a minimum upstream pressure known as cracking pressure. Depending on the check valve design and size, the cracking pressure changes. When the upstream pressure reaches the cracking pressure, the valve opens, allowing the fluid to enter. Back pressure is generated when the upstream pressure falls below the cracking pressure and the flow attempts to move from the outlet to the inlet. At this point, the check valve closes, and the flow halts. The closing mechanism of a check valve varies depending on the design and type of the valve. Spring or Gravity pressure normally assist the closing process.
As the check valve works only in one direction, manufacturers provide an arrow on the valve body indicating the flow direction.
Types of Check Valves
ZECO Check Valve types can be divided into the following designs:
Swing Check Valves
A basic swing Check valve consists of a valve body, a bonnet, and a disk connected to a hinge. The disk swings away from the valve seat to allow flow in the forward direction and returns to the valve seat when the upstream flow is stopped to prevent backflow.
The disc in a swing type Check valve is unguided as it fully opens or closes. Many disk and seat designs are available to meet the requirements of different applications. The valve allows full, unobstructed flow and automatically closes as pressure decreases. These valves are fully closed when the flow reaches zero to prevent backflow. Turbulence and pressure drop in the valve is very low.
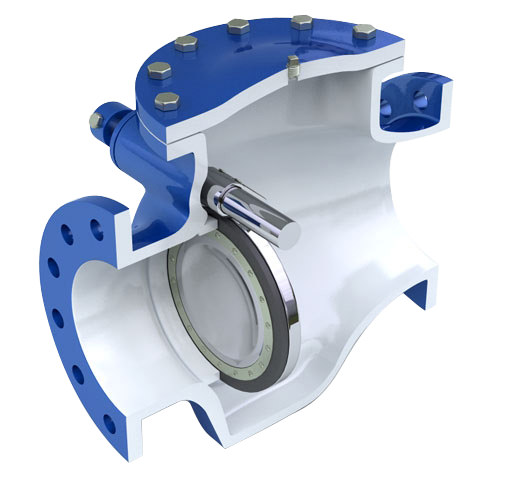
Industry Codes and Standards
- Valve Design: BS 1868 / API 6D
- Pressure Testing: BS 6755-I
- Face To Face: ANSI B 16.10
- Flange Drilling : ANSI B 16.5 / BS 10 Table / DIN / IS / JIS Std.
- Butt Weld End: ANSI B 16.25
- Face to Face: ANSI B 16.10
- Socket Weld End: ANSI B 16.11
- Screwed End: ANSI B 1.20.1(BSP/NPT)
Wafer Check Valves
Wafer Type Check Valve has short face-to-face dimensions and low weight allowing a simple space-saving installation between the companion flanges.
The valves are suitable for mounting between weld neck or slip-on type companion flanges of different standards.
They are specially developed for applications where a low-pressure loss is essential. Opening and closing of the valve will take place at an extremely low-pressure difference over the valve disc.
The eccentric disc shaft combination with the disc seat guarantees a positive shut-off returning media. Wafer check valves are becoming the preferred type of check valve for most applications due to their compact design and relatively low cost.

Lift Check Valve / Piston Check Valve
The seat design of a lift-Check valve is similar to a Globe valve. The disc is usually in the form of a piston or a ball.
Lift Check valves are particularly suitable for high-pressure service with high flow velocity. In lift Check valves, the disc is precisely guided and fits perfectly into the dashpot. Lift Check valves are suitable for installation in horizontal or vertical pipelines with upward flow.
Flow to lift Check valves must always enter below the seat. As the flow enters, the piston or ball is raised within guides from the seat by the pressure of the upward flow. When the flow stops or reverses, the piston or ball is forced onto the valve’s seat by both the backflow and gravity.
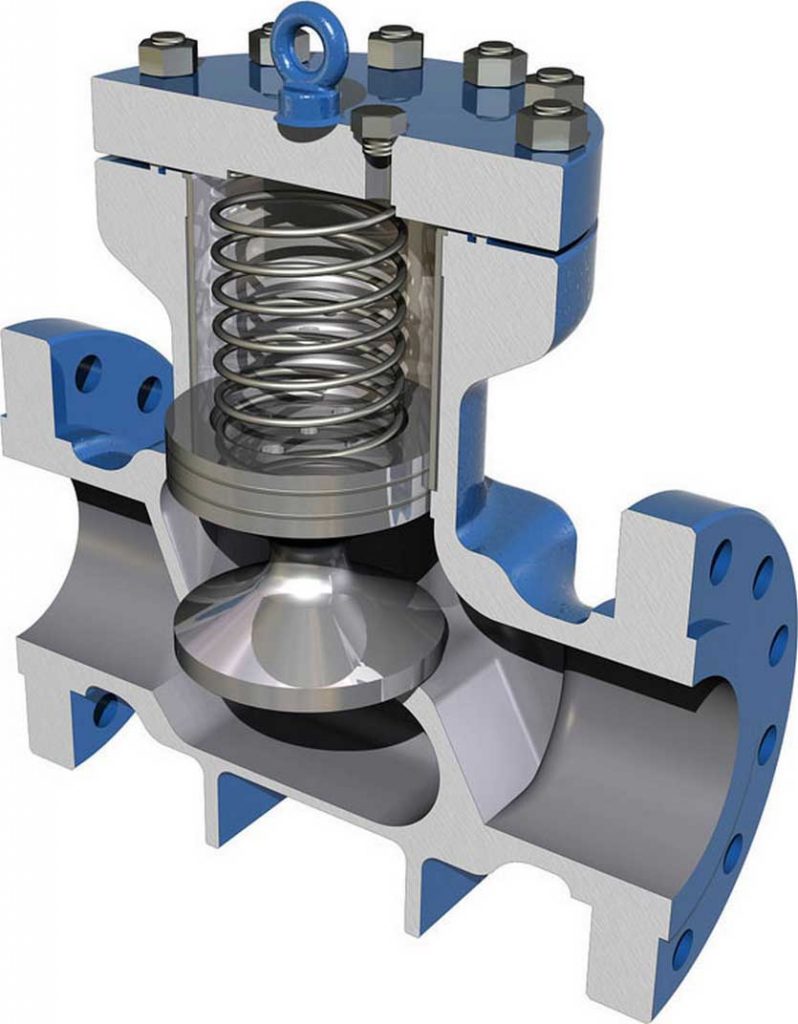
Ball Check Valves
Ball check valves are simple and commonly used on small pumps and low-head systems. Ball check valves involve a spring-loaded or free-floating spherical ball clapper to shut at pressures below the cracking pressure. The sealing seat is conically tapered to guide the ball into the seat and create a positive seal. However, these valves can easily wear due to prolonged use and require frequent maintenance.
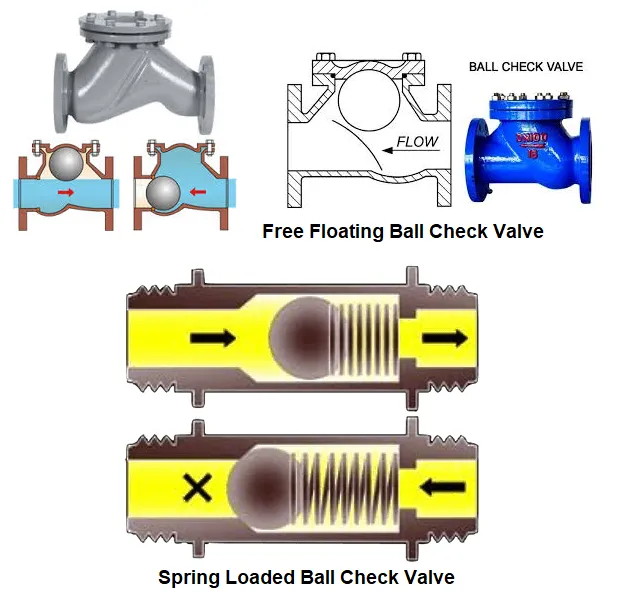
Tilting Disc Check Valves
The tilting disc check valve is similar in appearance to an eccentric butterfly valve. The valve body is double‐flanged and of a short length. The disc is placed via a shaft positioned eccentrically from the body centreline in both the horizontal and vertical axes.
The double eccentricity of the shaft results in the lower section of the disc occupying a greater area in the flow path. Consequently, the disc begins to open at very low flow rates. Therefore, the tilting disc check valve is commonly used in pumping systems with low flow rates and for pulsating flows.
During flow reversal, the disc closes due to gravity. The upper part of the disc above the shaft centreline pushes against the flow, thus acting as a hydraulic brake that cushions the disc as it returns to the closed position. Tilting disc valves can be supplied with optional levers and weights to adjust the closing characteristics of the valve. As such, the tilting disc check valves are well suited to reduce the risk of water hammers.
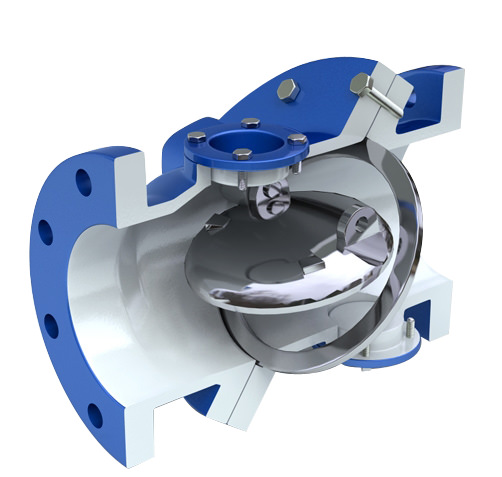
Butterfly Check Valve
A butterfly check valve is a dual plate check valve, folding disc check valve, double-disc, or split disc check valve. As the name suggests, two halves of the disk move towards the centerline with the forward flow, and with reverse flow, two halves open and rest on the seat to close the flow.
These types of check valves are good for low-pressure liquid systems as well as gas piping systems. Its lightweight and compact construction makes it a preferable choice when space and convenience are important. Besides, it is 80 to 90% lighter than the conventional full-body check valve, and the installation and maintenance cost is lower than other types.
Diaphragm Check Valve
Diaphragm check valves consist of rubber flexing diaphragms or self-centering discs for preventing backflow. When the inlet pressure is increased, the diaphragm flexes open, and flow starts. There are two types of diaphragm check valves;
- Free-floating Normally Open Valve
- Fixed Flexing Normally closed Valve
In the case of normally open diaphragm valves, no cracking pressure is required as the self-centering elastomeric diaphragm is free-floating. However, they need back pressure to close the valve. On the other hand, normally closed valves need a certain inlet pressure to overcome the elasticity of the fixed diaphragm.
Stop Check Valve
A stop check valve is two valves built into one body. It can act as a globe valve for isolation or regulation purposes. Again, It can act as a check valve to prevent backflow. Contrary to other check valves, the Stop check valve has an additional external control mechanism in the perpendicular or angular direction. Stop Check valves are popular in steam services like power plants, boiler circulation, steam generators, turbine cooling, and safety systems.