What is a Swing Check Valve?
A swing check valve is mounted with a disc that swings on a hinge or shaft. The disc swings off the seat to allow forward flow and when the flow is stopped, the disc swings back onto the seat to block reverse flow. The weight of the disc and the return flow has an impact on the shut-off characteristics of the valve.
How does a Swing Check Valve work?
The swing check valve adopts a built-in rocker swing structure. All of the valve’s opening and closing parts are installed inside the valve body and do not penetrate the valve body except for the sealing gasket and sealing ring for the middle flange, there is no leakage point as a whole which prevents the possibility of valve leakage. The swing arm connection between the swing check valve and the valve clack adopts a spherical connection structure, so that the valve clack has a certain degree of freedom within the range of 360 degrees, and there is an appropriate trace position compensation. When the medium flows downstream, the medium rushes through the valve flap and opens the valve, the pressure at which the valve opens are called cracking pressure. If the pressure of the medium falls below the cracking pressure the valve automatically shuts. When the medium flows back, the valve flap is sealed with the valve seat by the force of the medium, and the valve is closed.
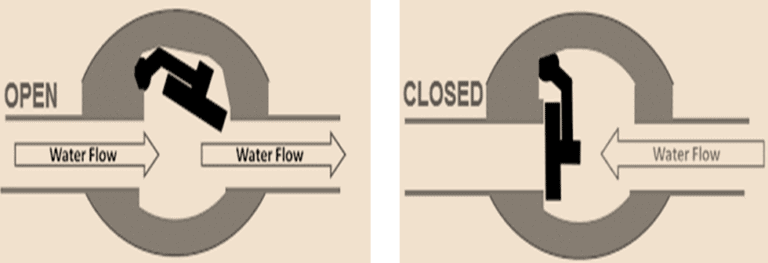
Applications of Swing Check Valves
- Power plants. A variant of the standard swing check valve, silent check valves — also called spring check valves — use a spring to help the valve close with more control. Silent check valves see frequent use in fluid control applications in the power generation sector, such as cooling towers. Of note, it also takes more pressure to open the valve against the spring, so spring check valves are best suited to high-pressure applications.
- Natural gas transmission. Swing check valves help prevent the improper flow of gas that could result in dangerous leaks or fires. These valves see broad usage in gas pipelines, commercial and residential gas meters, gas compressors, and more.
- Oil and gas refineries. Refineries often use specially designed non-slam check valves to mitigate water hammer — the pressure wave created in the system by a slamming valve.
- Horizontal water lines. Swing check valves are ideal for high-volume, consistent-pressure fluid situations. They’re the most common valve used in wastewater treatment and water pumping.
- Custom solutions. Each system is different, and sometimes specific applications require a unique modification or entirely original design to solve a challenging flow issue. It may be as simple as changing the angle of the valve or decreasing the disc’s weight, but your valve manufacturer can help you determine if a customized solution is right for you.
Advantages of Swing Check Valves
- Body and cover: Precision machined castings. Exclusive: Disc shaft does not penetrate body.
- Body and cover joint: Accurately machined, fully-enclosed gasket.
- Disc: Robust one-piece construction to withstand the severe shock of check valve service. Hardfaced with 13Cr, CoCr alloy, SS 316, or Monel, ground and lapped to a mirror finish. Sizes NPS 2–6 (DN 50–150) may have solid CA 15 (13Cr) disc. SS 316 disc with CoCr alloy facing also available.
- Disc assembly: Non-rotating disc is fastened securely to disc hanger with a lock nut and cotter pin. Disc hanger is supported on a sturdy disc carrier hinge pin of excellent bearing qualities. All parts are accessible from top for easy servicing.
- Flanges: ASME Classes 150–300: 1⁄16” raised face. ASME Classes 600–1500: 1⁄4” raised face. Finish 125–250 AARH for all valves.