Valves are very important components in utility systems. A gate valve, as the name suggests, is a type of valve used to control the flow of a liquid using a gate or plate. This type of valve is mainly used to stop or start the flow completely and is not used to regulate the flow amount unless specifically designed.
The best industrial valve manufacturers follow stringent standards while manufacturing these valves to ensure quality, durability, and performance. Any sub-standard quality may lead to unwanted damage and economic losses. Efficiency and ease of operation are two very important factors when choosing a valve from the many available valves.
A Sluice valve is called a gate valve; look through it for more information about them.
What is a Sluice Valve?
A gate valve or a Sluice gate valve is described as a valve that uses a gate or wedge shape disk that slides perpendicular to the fluid flow into or out of the pipeline. When the gate valve is fully opened, the disk of the gate valve is completely separated from the flow. This practically gives no opposition to flow. Due to this, very little reduction in pressure is experienced as the fluid moves through the gate valve.
The sluice gate valve is the common type of valve that is used in process plants to handle slurries. In operation, these valves are either fully opened or fully closed.
Sluice gate valves cannot be used for throttling as accuracy cannot be achieved using them. The high flow velocity in the partially open valve can cause disk and seat surface erosion and can also cause vibration and noise.
Sluice Valve Function
Sluice Valve and/or Gate Valve functions strictly to start or stop the flow. Gate valves are used for the water supply system, and sluice valves are used for slurries. The gate valve is opened by lifting the gate/wedge from the water flow, allowing all water to pass without resistance. The top end of the stem (connecting rod/shaft) has a hand wheel or motor to lift and drop the gate, and its bottom end has a gated circular or wedge-shaped to block the water flow. It has a threaded stem; hence the valve has to turn multiple times to go from the open to the closed position, preventing water hammer effects.
Sluice Valve Parts
- Gate
- Available in various designs, the gate is the main part of a gate valve. The main design aspect of it is its sealing capacity for specific applications. A gate valve can be classified as parallel or wedge-shaped based on the gate type. The former can be divided into slab, parallel slide, and parallel expanding gates.
- Seats
- A gate valve has two seats that ensure sealing along with the gate. These seats can be integrated within the valve body or as a seat ring. The latter is threaded or pressed into its position, then sealed and welded to the valve body. In situations where the valve is subject to higher temperatures, seat rings are preferred, as they allow for more variation in design.
- Stem
- The gate in a gate valve is lowered or raised when it spins on a threaded system. This can take place via a manual wheel or an actuator. An actuated gate valve can be controlled remotely. Depending on the step type, the gate valve can be categorized into rising stem and non-rising stem valves. The former is fixed to the gate, whereas the latter is to the actuator and threaded into the gate.
- Bonnets
- Bonnets are valve components that ensure the safe sealing of the passage. It is either bolted or screwed to the valve body so that it can be removed for replacement or maintenance. Based on application, various valve bonnets include bolt bonnets, screw-in bonnets, union bonnets, and pressure seal bonnets.
Types of Sluice Valves
Rising and Non-Rising Stem Designs
Gate valves are classified as rising or non-rising stems. Rising
refers to the stem and if it rises out of the valve bonnet as the valve is opened.
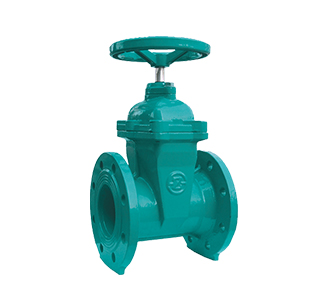
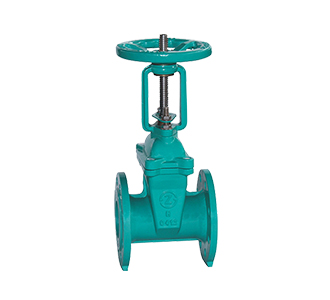
Inclined Disc Designs
Solid Wedge Gate Valves
Solid wedges are the simplest, strongest, and most suitable for many flowing mediums. Solid wedges are often manufactured from a single metal piece, and the disc seat area size matches the valve seat area size.
Flexible Wedge Gate Valves
Flexible wedges are machined around the wedge perimeter to help the disc locate the seating surface more easily. The machined area should not be too large as this reduces the disc’s strength (a thinner disc is weaker).
Split Wedge Gate Valves
Split wedges offer flexible seating on both the suction and discharge side of the wedge. The wedge consists of two separate halves, each able to self-align to sit correctly; this self-aligning feature is made possible due to the flexibility obtained when using two separate halves for one wedge.
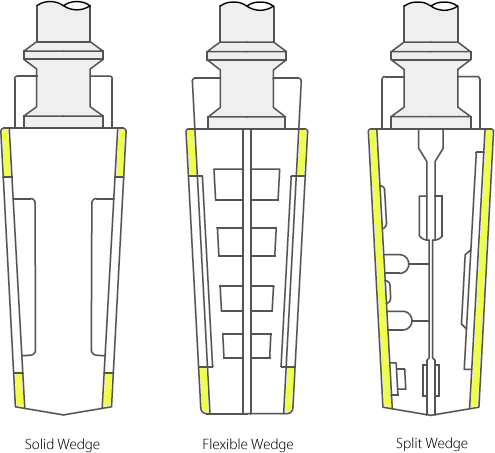
Parallel Disc Gate Valves
Parallel sliding discs utilize a spring placed between the two parallel discs. The spring is held under compression between the parallel discs and thus exerts constant force outwards onto the internal surfaces of the discs. As the valve is lowered into the valve seat, the spring is further compressed and the resultant force exerted by the spring ensures each disc is pressed firmly against the seat.
Sluice Valve Vs Gate Valve
Sluice valves and gate valves are somewhat different in operation and usage. A gate valve can be a good option for in-line sealing and sludge applications. But when it is needed for managing the flow in a sluice or stream, the sluice gate valve is the best option for your application.
Good quality and efficient valves like the ones by ZECO are a great investment as it requires minimal maintenance in the long run, which can save a lot of money. Contact ZECO Valve today for best-in-class valves.