All water supply systems consist of pipes that transmit water from its source to its destination. In this process, pockets of trapped air can form in the pipelines. Pockets of air and wastewater gases are difficult to detect and will reduce the overall efficiency of the piping system. The air pockets may also cause water hammer problems, full flow stoppage, pipe bursts, system noise, and pipe corrosion. Air in the pipeline can also cause unstable control valves, meters, and equipment operations. To secure a safe and efficient operation, it is therefore critical to remove air and wastewater gases from the water system continually.
What is an Air Valve?
Air valves are an essential part of water supply networks. Whether it be a water distribution line or sewage main, you can find an air valve there.
Main Components of an Air Release Valve
Valve body
The unique ductile Iron valve body is compact and houses the inner floats and upper mechanism. The body is designed so the inlet is completely free of float guides, enabling butterfly valves to be used directly under the air valve without impacting performance. Each valve body has a lower 316SS grade tamper-proof drain valve enabling the valve to be drained and tested quickly and safely.
Inner float assemblies
The inner floats are all manufactured from bar-stock polypropylene, ensuring they can never change their mass or shape. The floats are all guided and kept square to the body by the four guide ribs on the valve body, ensuring they cannot get blown offset to the side.
Air Valve Types
1. Combination Air Valves
It combines the function of automatic air valves and air and vacuum valves. The automatic air release function releases accumulated air from the system while it is under pressure, and the air and vacuum function discharges and admits large volumes of air during the filling or draining of pipelines. Combination air valves are double-orifice air valves, double-acting air valves, and dual-orifice air valves.
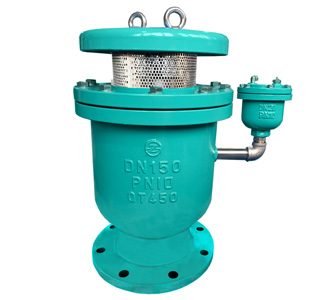
2. Air and Vacuum Valves
It discharges large volumes of air from non-pressurized pipelines and is mainly used when filling a line. Air and vacuum valves make it possible to admit large volumes of air when lines are drained and the pressure suddenly drops. Air and vacuum valves are kinetic air valves, large orifice air valves, vacuum breakers, low-pressure air valves, air relief valves, and single-acting air valves.
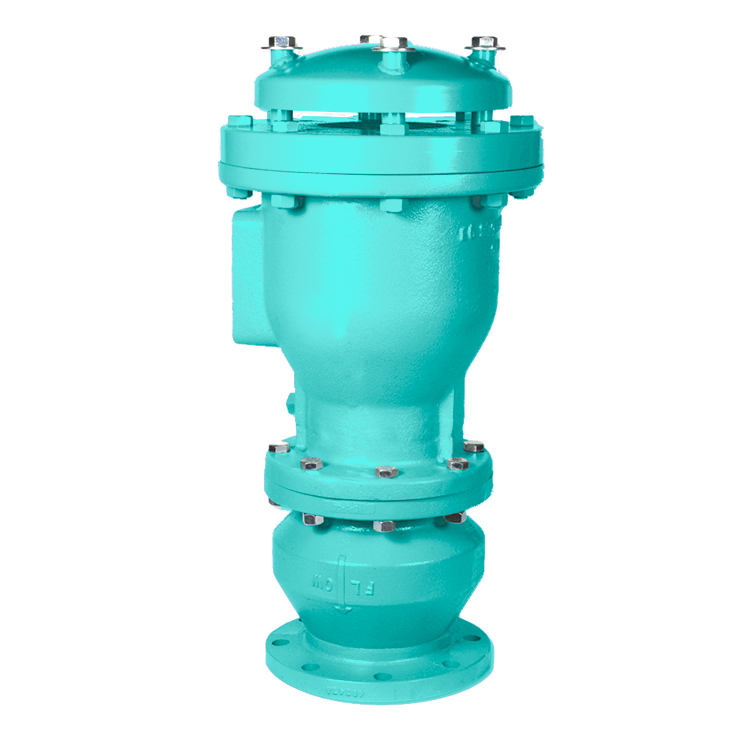
3. Automatic Air Valves
It continuously releases relatively small volumes of air from a pressurized line. Automatic air valves are also known as small orifice and pressure air valves.
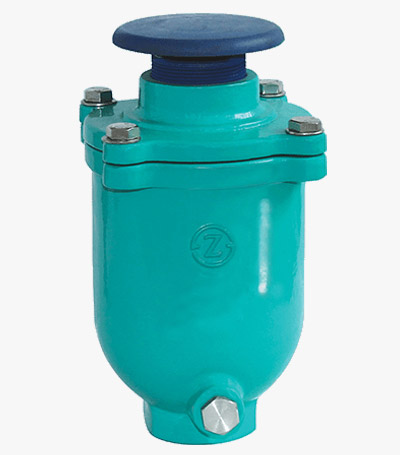
What Causes Air in Water Pipes?
Air and vacuum formed in water mains may lead to serious operating problems and even some dramatic consequences. Air can enter piping systems in several ways:
- Empty Pipelines
Pipelines not in operation are occupied with air. Most of it is evacuated during startup, but some air pockets can remain in the system.
- Air in The Fluid
Liquids like water can contain trapped or dissolved air depending on the temperature and pressure. It separates from the liquid during fluid flow and can become trapped at the system’s high points. Also, in pipelines conveying sewage, the liquid waste can undergo chemical reactions and evolve into gases that can get trapped in the wastewater system.
- Mechanical Equipment
Air can also enter the pipeline through mechanical systems like pumps, pipe joints, valves, etc. Leaks or faulty seals in these components can lead to air infiltrating the piping system.
The function of Air Valves
Air Valves perform two important functions in a piping system. They maintain system design efficiency and provide system protection. System efficiency is maintained by venting air via the air valves from the system, which can restrict flow and increase pumping costs.
Protection is provided by exhausting and admitting air through the air valves during system operations, including start-up, shutdown, and critical conditions such as power failures or line breaks. The exhausting and admitting air during these conditions will reduce the potential for destructive surges and water hammer normally associated with uncontrolled air or a vacuum within the piping system.
How does an Air Valve work?
Automatic air release valves are installed at the highest points in a pipeline where air naturally collects. Air bubbles enter the valve and displace the liquid inside, lowering the liquid level. It drops when the level drops to where it no longer buoys the float. This motion pulls the seat away from the orifice, triggering the valve to open and vent the accumulated air into the atmosphere.
As the air is vented, liquid re-enters the valve, once again buoying the float, lifting it until the seat presses against the orifice, closing the valve. This cycle automatically repeats as often as necessary to maintain an air-free system.
Proper installation is critical to the operation of air-release valves. Because these valves are designed to release air from the piping system, they should be placed where the air is most likely to collect. Install them at system high points vertically with the inlet down. Remember to add a shut-off valve below the valve if servicing is required.
Applications of Air Valves
All fluid transport systems
- Potable
- Sewage
- Residual
- Raw water
- Saltwater (reverse osmosis plants)
- Acids in solution (mining).
Advantages of Air Valves
- Protect pipelines
- Resolve air entrapment issues
- Ensures safe operations of pipelines
- Prevents bubble and air pocket formation
- Low maintenance
- Energy efficiency
Disadvantages of Air Valves in the pipes lines
The control of the presence of air – inside the pipe can cause severe problems:
- The impedance of the flow in pipes or reduction of the effective section:
It increases energy losses. Also, the inadequate water supply to the different areas of the system is due to the obstruction of the flow and the accumulation of localized head losses.
- Inaccurate readings on gauges and hydrometers.
- Serious damage to internal rotating parts of gauges.
- Inadequate water supply due to incorrect meter and hydrometer readings.
- Corrosion and Cavitation problems.