What is a double block and bleed valve?
A double block and bleed valve are like having three valves in one.
API 6D defines a double block and bleed valve as a “single valve with two seating surfaces that, in the closed position, provides a seal against pressure from both ends of the valve with a means of venting/bleeding the cavity between the seating surfaces.”
There are a couple of different styles of double block and bleed valves. One style has two independently seating valves inside, with a bleed or drains valve. This configuration is referred to as double isolation and bleed (DIB). The DIB valve can isolate either side of the valve (bi-directionally) to vent or bleed the cavity and isolate piping.
This trunnion mounted ball valve from Val-Matic provides a double block and bleed in a single valve. This style can isolate piping on both sides of the valve (uni-directionally) to vent/bleed the valve cavity between the seats.
Using a single double block and bleed valve system versus 3 separate valves saves installation time, weight on the piping system, and space. It also cuts down the number of leak paths to the atmosphere, reducing the risk of hazards when transferring liquids dangerous to humans or the environment.
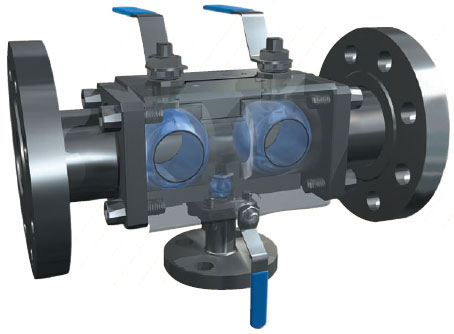
What are the applications of double block and bleed valves?
These types of valves are of high importance in gas and oil factories. But, according to valve manufacturers, this particular type of valve is also used for various other purposes. In situations where the piping which is fitted requires isolation and maintenance, the best choice is a double block and bleed valve.
- Prevent product contamination
- Remove equipment from service for cleaning or repair
- Meter calibration
- Liquid service near waterways or municipalities
- Transmission and storage
- Chemical injection and sampling
- Isolate instrumentation such as pressure indicators and lever gauges
- Primary process steam
How do these double block and bleed valves work?
These types of valves are designed in such a way that one can control the flowing of a liquid in the manifold as desired. The purpose of this double block is that it offers perfect sealing on both sides of the surface to ensure that there is no chance of leakage and that both sides of the surface can endure equal pressure.
Double Positive Isolation
Many people take the term “Double Block & Bleed” (DBB) to mean the same thing as “Double Positive Isolation” (DPI). While this may seem like a small matter, in reality, it means that some users may think they’ve achieved positive isolation when they haven’t. The key to understanding the difference between Double Block & Bleed (DBB) and Double Positive Isolation (DPI) can be found in API 6D. API 6D wasn’t always as clear as it could have been in spelling out the difference between DBB and DPI, but the addition in 2008 of several notes has clarified it.
API 6D defines a Double Block and Bleed Valve (DBB) as a “single valve with two seating surfaces that, in the closed position, provides a seal against pressure from both ends of the valve with a means of venting/bleeding the cavity between the seating surfaces.” The 2008 note points out that this valve does not provide positive double isolation when only one side is under pressure.
API 6D defines a Double Isolation and Bleed Valve (DIB) as a “single valve with two seating surfaces, each of which, in the closed position, provides a seal against pressure from a single source, with a means of venting/bleeding the cavity between the seating surfaces.” The 2008 note adds that this feature can be provided in one direction or in both directions.
The important distinction between the DBB and DIB is, that on a DBB if there is somebody working downstream on the line and the first seal leaks the second seal will not seal in that same direction.
Benefits of using double block and bleed valves
There are times when a machine has two separate liquids which if come in contact with each other can be very risky and cause great damage. Thus, in such a situation, double block and bleed valves are the best as they can properly control both liquids from leaking and mixing with each other. This is why; they are commonly used while handling toxic waste and dangerous chemicals as well.
If you are searching for an alternative with which you can ensure proper and safe venting of liquids from the machine which can pose a great environmental threat, then this type of valve is just best for that purpose.
Wanting to lessen your operation and production costs? If yes, then double block and bleed valves are the solutions for you because the multivalve system installed in the valves ensures better proficiency.
If you are planning to invest in valves then we highly recommend you invest in the double block and bleed valves as they are the best option. However, it is always better and safe to purchase the same from professionals who specialize in manufacturing the same.
How to choose a Double Block and Bleed Valve
Before choosing the type of valve that you require, it is recommended to consider the application, media, pressure, temperature, toxicity, and environment in which it will operate.
As DBB valves are often used in highly critical processes, it is important to test them so that you know they satisfy the requirements.
As an example, ZECO Valve has datasheets for all their DBB valves which detail valve type, rating/pressure, size, connection type, material, and options. To define a part number, all that is required is to use a chart to find the alphanumeric codes that will define the base unit and options. The below chart is a representation of their Flange DBB:
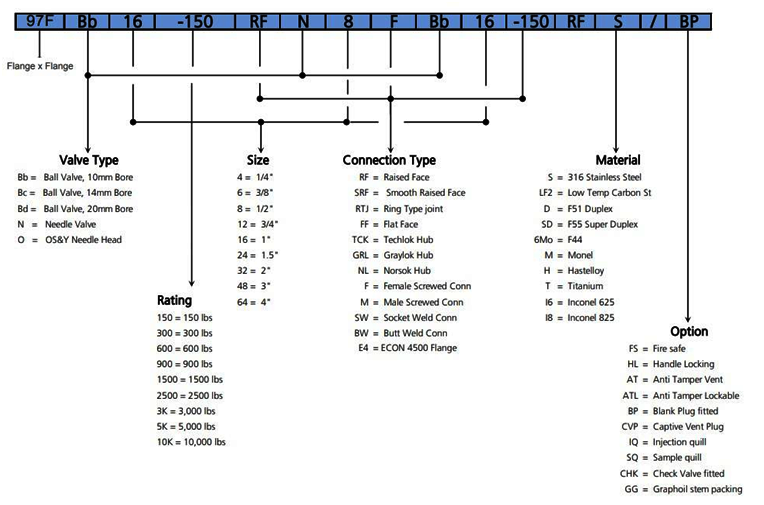
Differences between DIB and DBB
With a DBB valve, there are usually two unidirectional self-relieving seats. These seats do not rely on an outside mechanism to relieve pressure. In contrast, a DIB valve utilizes one or two bidirectional seats. The valve provides double isolation from pressure at both ends of the valve but cannot relieve body cavity pressure past the seats. DIB valves require an external relief system to relieve pressure buildup.
Both valves can provide isolation in both the upstream and downstream directions, even in high-pressure or high-temperature situations. Isolation is important in cases where leakage through a valve could have major consequences. Once the fluid is isolated, the bleed mechanism can drain the area between the two valves or two seating surfaces. This is important for maintenance and integrity check situations where leakage can be monitored.
Related Tags :
Ten articles before and after
Uses of Instrumentation Valves – Zeco VALVES LLP | Industrial valve manufacturer
What are the functions & uses of the needle valve? – Zeco VALVES LLP | Industrial valve manufacturer