1. Structure characteristics and technical requirements of ball valve body
Most of the low pressure ball valves and medium pressure ball valves are side mounted ball valves, which are composed of left and right valve bodies. The structure of the left valve body is simple, and the right valve body is complex, as shown in the figure below.
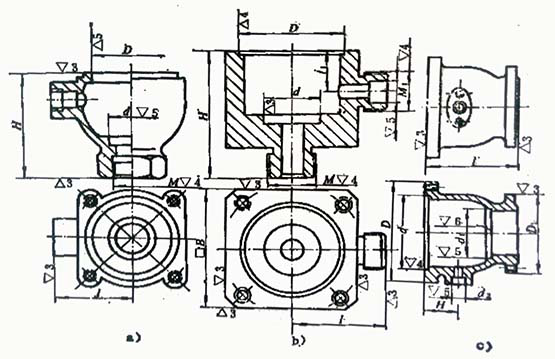
In the inner cavity of the ball valve, there is a high precision inlaid seat hole and a packing hole for installing the valve rod on the side. The right valve body of small size ball valve is connected with the left valve body or with the pipeline by thread, and the right valve body of large and medium size ball valve is connected by flange bolt.
The accuracy of valve seat hole, stop and packing hole is generally grade 6, and the finish is not less than ▽ 5. The accuracy of other machined surfaces is grade 8, and the finish is ▽ 3. There is coaxiality requirement between the stop and the valve seat hole. The perpendicularity of the bolt hole center line on the flange to the end face shall not be greater than 1 °.
According to the use of ball valve, the valve body can be made of gray cast iron, carbon steel, stainless steel or non-metallic materials. Generally casting blanks are used. Only some small-size steel valve body adopts forgings.
2. Machining process of right valve body of ball valve
The main machining surface of the right valve body is the rotating surface, so it can be manufactured by turning machines. Valve bodies below DN150 are produced in large quantities, and each main process is equipped with process equipment. The production capacity of large valve body is very small, which can be processed by marking. The following table shows the typical process of type III valve body in medium and small batch production.
Typical process of A-type ball valve right valve body
Serial number | Process content | Location datum |
1 | Hexagonal end, inner hole and inner thread | Flange outer surface |
2 | Flange end, rabbet and valve seat hole | Hexagonal end and internal thread |
3 | Side end, inner hole and inner thread | Flange end and rabbet |
4 | Drilling flange hole and tapping thread hole |
Typical process of right valve body of B-ball valve
Serial number | Process content | Location datum |
1 | Two ends, side ends and back end | |
2 | Turning small end, drilling, cylindrical, idle stroke, chamfering, external thread | back end and the other side end |
3 | Large end face, drilling, interior hole and valve seat hole | External thread and square end |
4 | Side end, cylindrical, idle stroke, chamfering and external thread, drilling and rabbet | Large end and one side |
5 | Drilling, tapping |
Typical process of right valve body of C-ball valve
Serial number | Process content | Location datum |
1 | End of small end flange, cylindrical, back and chamfer | Cylindrical of large end flange |
2 | End of end flange, inner hole, rabbet and seat hole | Small flange end and cylindrical |
3 | Flange end of side, drilling, packing hole | Large flange end and rabbet |
4 | Draw flange center line | |
5 | Drilling small flange bolt holes | |
6 | Drilling large flange holes and tapping holes |
In mass production, the right valve body can also be processed by automatic line.