What is a High Temperature Solenoid Valve?
High Temperature Solenoid Valve is a pilot direct-acting solenoid valve, its unique shape helps heat dissipation, to prevent high-temperature burn coil. And special coils to make it work in the high-temperature industry. This product is widely used in boiler, marine heavy industry, petroleum industry, heating equipment and other high-temperature industries. Its main function is to regulate and control the medium in the pipeline. Suitable for hot water, hot oil, steam and other media. The operation is quick and sensitive with a minimum aerodynamic pressure of 0.5 bar.
Working Principle Of High Temperature Solenoid Valves
When the solenoid is energized, the connecting rod is lifted, and as the shaft begins to rotate, this movement acts on the pilot valve and opens the main valve; when the power is cut off, the semi-upper pilot valve and the pilot valve are closed under the action of the dead weight of the armature and the return spring, and the main valve is closed by pressure difference.
Normally Closed: When the coil is energized, the pilot Spool is absorbed, the pilot hole is opened, the pressure on the valve is released, the Piston is driven by the pressure of the lower chamber medium, and the solenoid valve is opened; when the coil is powered off, the pilot Spool is reset by the spring, and the pilot hole is closed, the upper chamber of the valve is pressurized by the Piston throttling hole and restores the thrust of the spring. The valve is closed.
Normally Open: When the coil is energized, the pilot hole is closed, the valve upper chamber is pressurized by the Piston throttle hole and the thrust of the reset spring, the solenoid valve is closed. When the coil is cut off, the pilot Spool is reset by spring, the pilot hole is opened, the upper chamber of the valve is unloaded, the Piston is driven by the lower chamber medium pressure, and the solenoid valve is opened.
Features Of High Temperature Solenoid Valves:
- Pilot operated piston construction with low power consumption
- Seal serves longtime at steam ambient
- Used for long-time working in pipeline system
Technical Parameters Of High Temperature Solenoid Valves:
Material | Stainless Steel |
Seal | PTFE |
Size Range | 1/2″ to 2″ |
Suitable Medium | Hot Water, Hot Oil, Steam, etc |
Medium Temperature | -10℃ to 180℃ |
Pressure | 0.5 bar to 16 bar |
Connection Type | Threaded / Flange |
Voltage | DC-12V, 24V; AC-24V, 120V, 240V/60Hz; 110V, 220V/50Hz |
Tolerance | ±10% |
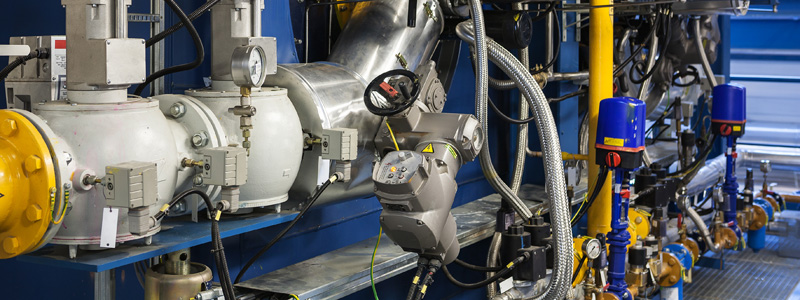
What is a solenoid valve?
The solenoid valve is industrial equipment controlled by electromagnetism. It is an automatic basic element to control the fluid. It belongs to the actuator, but not limits to the hydraulic pressure and pneumatic control. In the industrial control system, the solenoid valve is used to regulate the direction, flow rate, speed and other parameters of the medium. The solenoid valve can coordinate with different circuits to realize the anticipated control, with both control precision and flexibility being guaranteed.
The solenoid valve is constituted by the solenoid coil and magnetic core. It is the valve body containing one or several holes. When the coil is get through or cut off with power, the operation of the magnetic core will result in that the fluid passes through the valve body and is cut off, so as to reach the goal of changing the fluid direction. The electromagnetic component of the solenoid valve is constituted by the fixed iron core, movable iron core, coil and so on. The valve body is constituted by the slide valve core, slide valve harness and spring base. The solenoid coil is installed on the valve body directly while the valve body is enclosed in the seal pipe, so as to constitute a simple and compact combination.
The History of Solenoid Valves
The first solenoid valve was the solenoid control valve, sold and manufactured in 1910 by ASCO Numatics. Then, in the 1950s, manufacturers began distributing plastic molded solenoid valves. The switch to plastic meant that solenoid valves were now more efficient, reliable, corrosion resistant and chemical resistant.
This trend of improvement continued on into the late 20th century. For instance, starting in the 70s, manufacturers began producing automatic shut-off solenoid valves, which were safer and easier to operate than manual control shut-off valves.
In the 1990s, governments around the world, as well as independent organizations, began creating solenoid valve standardizations, which enabled a higher frequency of international trade, easier collaborations between companies and easier maintenance. Today, newer standards also restrict the use of hazardous substances in valve fabrication, so as to improve their environmental friendliness. Today, much of valve fabrication and use innovation is focused on health and sustainability.
Design of Solenoid Valves
Production Process
Manufacturers produce solenoid valves via a variety of processes, such as: CNC machining, laser welding, injection molding and coil winding. Once they’ve fabricated the valve components, they assemble them.
These components include: the solenoid valve coil, the valve, an inlet port, an outlet port, a spring, an orifice and an actuator. Often, solenoid also feature seals.
Materials
Manufacturers have a wide variety of materials available to them with which to construct their solenoid valves. Valves may be made from both plastic and metal materials, such as PVC, natural polypropylene, PTFE, CPVC, stainless steel, bronze, aluminum, and brass. Seals, like viton seals or nbr seals, are usually made from some sort of rubber. Occasionally, manufacturers will make stainless steel seals.
Design and Customization
Solenoid valve manufacturers make choices based on application specifications such as: nature fluid/gas inside pipe (corrosiveness, hazardousness, viscosity, acidity, etc.), environment, frequency with which the pipe will be used and application standard requirements. Based on the specifications, they can choose design aspects like: valve size, valve material, valve type and configuration and number of ports.
Suppliers may customize your solenoid valve system in a number of ways. For instance, they normally create valves with two connection areas and one orifice, but they can also make you valves with three connection areas and two orifices. Likewise, while they usually design valves to run using a 12-volt DC power source, they can also customize them to work with 3-volt, 6-volt or 24-volt power sources. They may also provide you with specialized: pressure levels, spring return, valve size, etc.
How a Solenoid Valve Works
1.Direct-acting solenoid valve
DIRECT-ACTING VALVES
With a direct-acting solenoid valve, the seat seal is attached to the solenoid core. In the de-energized condition, a seat orifice is closed, which opens when the valve is energized
DIRECT-ACTING 2- WAY VALVES
Two-way valves are shut-off valves with one inlet port and one outlet port (Fig. 1). In the de-energized condition, the core spring, assisted by the fluid pressure, holds the valve seal on the valve seat to shut off the flow. When energized, the core and seal are pulled into the solenoid coil and the valve opens. The electro-magnetic force is greater than the combined spring force and the static and dynamic pressure forces of the medium.
DIRECT-ACTING 3-WAY VALVES
Three-way valves have three port connections and two valve seats. One valve seal always remains open and the other closed in the de-energized mode. When the coil is energized, the mode reverses. The 3-way valve shown in Fig. 2 is designed with a plunger type core. Various valve operations can be obtained according to how the fluid medium is connected to the working ports in Fig. 2. The fluid pressure builds up under the valve seat. With the coil de-energized, a conical spring holds the lower core seal tightly against the valve seat and shuts off the fluid flow. Port A is exhausted through R. When the coil is energized the core is pulled in, the valve seat at Port R is sealed off by the spring-loaded upper core seal. The fluid medium now flows from P to A.
2. Pilot-operated solenoid valve
INTERNALLY PILOTED SOLENOID VALVES
With direct-acting valves, the static pressure forces increase with increasing orifice diameter which means that the magnetic forces, required to overcome the pressure forces, become correspondingly larger. Internally piloted solenoid valves are therefore employed for switching higher pressures in conjunction with larger orifice sizes; in this case, the differential fluid pressure performs the main work in opening and closing the valve.
INTERNALLY PILOTED 2-WAY VALVES
Internally piloted solenoid valves are fitted with either a 2- or 3-way pilot solenoid valve. A diaphragm or a piston provides the seal for the main valve seat. The operation of such a valve is indicated in Fig. 4. When the pilot valve is closed, the fluid pressure builds up on both sides of the diaphragm via a bleed orifice. As long as there is a pressure differential between the inlet and outlet ports, a shut-off force is available by virtue of the larger effective area on the top of the diaphragm. When the pilot valve is opened, the pressure is relieved from the upper side of the diaphragm. The greater effective net pressure force from below now raises the diaphragm and opens the valve. In general, internally piloted valves require a minimum pressure differential to ensure satisfactory opening and closing. Omega also offers internally piloted valves, designed with a coupled core and diaphragm that operate at zero pressure differential (Fig. 5).
INTERNALLY PILOTED MULTI-WAY SOLENOID VALVES
Internally piloted 4-way solenoid valves are used mainly in hydraulic and pneumatic applications to actuate double-acting cylinders. These valves have four port connections: a pressure inlet P, two cylinder port connections A and B, and one exhaust port connection R. An internally piloted 4/2-way poppet valve is shown in Fig. 6. When de-energized, the pilot valve opens at the connection from the pressure inlet to the pilot channel. Both poppets in the main valve are now pressurized and switch over. Now port connection P is connected to A, and B can exhaust via a second restrictor through R.
EXTERNALLY PILOTED VALVES
With these types an independent pilot medium is used to actuate the valve. Fig. 7 shows a piston-operated angle-seat valve with closure spring. In the unpressurized condition, the valve seat is closed. A 3-way solenoid valve, which can be mounted on the actuator, controls the independent pilot medium. When the solenoid valve is energized, the piston is raised against the action of the spring and the valve opens. A normally-open valve version can be obtained if the spring is placed on the opposite side of the actuator piston. In these cases, the independent pilot medium is connected to the top of the actuator. Double-acting versions controlled by 4/2-way valves do not contain any spring.
Advantages of Solenoid Valves
There are many beneficial characteristics of solenoid valves that give them advantages over other valve types. For example, since solenoid valves are powered by natural pressure and electromagnetic force, they generally have fewer moving parts than other valves. This is widely considered to be a good design, since moving parts require maintenance.
In addition, solenoid valves can be easily operated by remote devices that activate the solenoid coil, making solenoid valves extremely useful for hazardous applications. Also, solenoid valves can use either hydraulic or pneumatic power because both can be activated or piloted by solenoids. However, pneumatic power is more commonly used because it is considered cleaner and lower maintenance than hydraulic power, due to the absence of degrading fluids which produce waste and must be maintained.
Finally, solenoid valves offer rapid and safe switching, compact design, high reliability and typically long service life.
Related Tags :
Ten articles before and after
News – How To Select A Valve For Gas Industry? | API approved valve manufacturer
News – How To Maintain A Bolier Safety Valve | API approved valve manufacturer
News – Advantages Of Wafer Butterfly Valve | API approved valve manufacturer
News – Zeco Food Grade Valves For Food Processing | API approved valve manufacturer
News – What Is V Port Ball Valves? | API approved valve manufacturer
News – Working Principle Of Air Actuated Butterfly Valves | API approved valve manufacturer
News – 3 Tips For How To Maintain The Electric Actuator Valve | API approved valve manufacturer
News – 2 Steps To Understand Solenoid Valve Working Principle | API approved valve manufacturer
News – 5 Steps To Produce A Valve | API approved valve manufacturer