Double block and bleed (DBB) is the practice of shutting in a section of pipe on both sides of the valve rather than just one. It means you close the ball valves to block both the upstream and downstream sides of your working area, and then bleed any pressure that remains in the piping and valve.
Double Block and Bleed Valve (DBB Valves)
These valves replace existing traditional techniques employed by pipeline engineers to generate a double block and bleed configuration in the pipeline. Two block valves and a bleed valve are as a unit, or manifold, to be installed for positive isolation. Used for critical process service, DBB valves are for high-pressure systems or toxic/hazardous fluid processes. Applications that use DBB valves include instrument drain, chemical injection connection, chemical seal isolation, and gauge isolation.DBB valves do the work of three separate valves (2 isolations and 1 drain) and require less space and less weight.
The Double Block and Bleed Valve or a DBBV can perform the tasks of 3 separate Valves (2 separate isolations and 1 drain Valve) which apart from being hugely space saving can also save on weight and time due to installation and maintenance practices requiring much less work and the operator being able to locate and operate all 3 Valves in one location.
Double block and bleed Valves operate on the principle that isolation can be achieved from both the upstream and downstream process flow / pressures.
Once isolation has been achieved in one or more of the main process isolation Valves, the cavity that is created between these isolations can be drained. This is useful for flow diverting, sampling, or injection situations, and for maintenance and or integrity check situations where seat leakage can be monitored through the third “bleed” Valve.
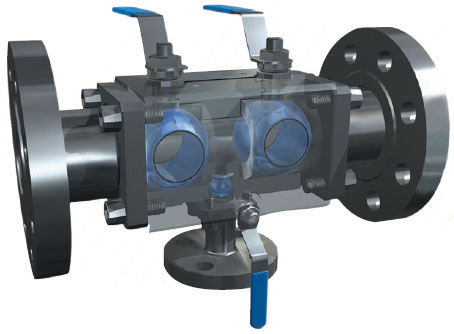
Why use a Double Block and Bleed Valve?
Double Block and Bleed valves have evolved to replace the process of bolting together individual valves to provide dual isolation.
This new assembly provides great savings in weight, space, and installation times, especially in instrument or instrument cage isolation. These savings can be as much as 60% in weight and studies have shown that a 70% installation time saving is also possible. However, the greatest savings are to be seen in the reduction of leak paths to the atmosphere, therefore reducing the risk of the potential hazards this entails.
Dual isolation is a necessary requirement when maintenance is taking place downstream of the first isolation valve. Cavity venting is provided by either a ball or globe vent valve so that trapped pressure between the two isolation valves is safely vented.
These valves have also evolved to encompass the function of chemical injection (using a suitable quill) and sample points. In-built check valves are often integrated into these valves.
All DBB valves are manufactured to EEMUA 182 latest revision.
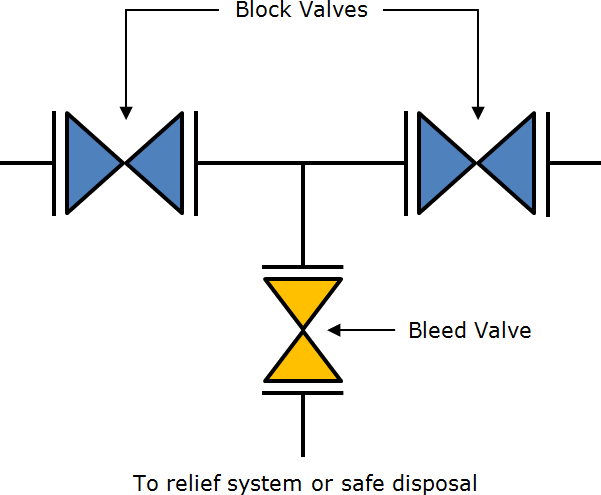
Why use a Double Isolation and Bleed Valve?
Double Isolation and Bleed Valves, as the name implies, are the go-to solution when absolute isolation is needed. For example, in situations such as:
A section of the process is under maintenance and extremely high pressure/temperature fluid is in the upstream flow
In food and beverage industries where shutoff is required, any kind of contamination between upstream and downstream flow must be avoided.
There is an issue to be solved here. The valve body cannot relieve itself of pressure buildup because there is no bleeding function used in the seats. The upstream seat risks damage or leaks, and pressure builds up within the valve body. So, an alternative bleeding method, built into the valve body, is necessary to prevent further pressure buildup and potential valve body damage.
When security is needed in the process shut off, for either safety or product contamination purposes, a DIB valve may be the most efficient solution. That’s why DIBs are often used in food/beverage applications and volatile applications like oil, gas, and steam.
Main Features of Double Block and Bleed Valve
- Fire-safe test approved
- Double Block & Bleed valves are designed in accordance with API 607 & API SPEC 6FA. Double body gasket
- All Double Block & Bleed valves are equipped with two body gaskets. The first body gasket is in soft material and the second in graphite (if not otherwise required), this combination assures the best seal characteristic in whatever corrosive service as well as giving a fire-safe design.
- Anti-Static device
- In order to prevent static electricity which may light the fluid, a static-conduction spring is set between the stem and the ball.
- Anti-blow-out proof stem
- The stem is designed with an integral T-Type shoulder to provide blow-out proof effectively. The design assures that the stem can not be blown out of the valve in the case of the packing being removed while the valve is under pressure.
- Controlled stem & stuffing box finish
- Stem and stuffing box finish machining is a key point of control. The stem is made by cold rolling and the stem surface finish is controlled by Ra=0.4, which can reduce the friction of stem movement and ensure the seal. The stuffing box surface is controlled within Ra=1.6 for better sealing performance.
- Solid ball
- The solid ball used by ZECO provides straight-through flow and real full-port performance characteristics. Hollow balls or cored cavity balls are not used for ZECO products.
- Longevity of life
- Special consideration was devoted to the attainment of enhanced life and operation of our valve throughout the design, development, testing, and manufacturing stages.
- Valve designs combined with the selection of advanced materials are such that long periods of inactivity should not affect the operations of efficiency.
- low Torque output
- Seat designs, stem-bearing systems, and stem seal arrangements ensure consistent minimal torque values.
- Flow capacity
- The valve design allows for high flow capacity in liquid or gas services regardless of whether the media is clean or dirty. Full port valves allow for pigging and ensure maximum flow capacity.
- ISO Flange integrated into the body design
- ISO 5211 mounting is always integrated into the valve as standard design.
- Locking device
- Locking device is supplied as standard in order to prevent unauthorized opening/closing. ZECO locking device can lock the valve in either the open or closed position and cannot be breached by removing the lever
DBB vs DIB
With a DBB valve, there are usually two unidirectional self-relieving seats. These seats do not rely on an outside mechanism to relieve pressure. In contrast, a DIB valve utilizes one or two bidirectional seats. The valve provides double isolation from pressure at both ends of the valve but cannot relieve body cavity pressure past the seats. DIB valves require an external relief system to relieve pressure buildup.
Both valves can provide isolation in both the upstream and downstream directions, even in high-pressure or high-temperature situations. Isolation is important in cases where leakage through a valve could have major consequences. Once the fluid is isolated, the bleed mechanism can drain the area between the two valves or two seating surfaces. This is important for maintenance and integrity check situations where leakage can be monitored.
DBB BALL VALVE
According to the API 6D definition, Section 3.1.10 defines a double-block-and-bleed valve as a: “Single valve with two sealing surfaces that, in the closed position, provides a seal against pressures from both ends of the valve with a means of venting/bleeding the cavity between the seats.”
To achieve this, the valve is equipped with two SPE seats, as we have seen.
The double-block-and-bleed design is the most commonly used for trunnion ball valves, responsible for around 85% of global oil and gas applications. It is a compact, low-weight valve that provides reliable isolation in critical areas, reducing piping requirements. To summarize, a DBB is a valve that seals from either direction with a bleed between the two, if the first seal leaks, the second will not seal in the same direction and it does not require an external mechanism to relieve pressure. A DBB valve implies double security, providing security in two different directions, each with a separate seal. When a DBB valve is in use and the first seal leaks, the second seal will not seal in that same direction.
DIB BALL VALVE
The API 6D definition Section 3.1.11 defines a double-isolation-and-bleed valve as a: “Single valve with two seating surfaces, each of which, in the closed position, provides a seal against pressure from a single source, with a means of venting/bleeding the cavity between the sealing surfaces. This feature can be provided in one direction or in both directions.”
In API’s DBB and DIB definitions the difference is that a double-block-and-bleed valve seals against pressures from both sides of the valve while a double-isolation-and-bleed valve provides an additional seal against pressure building in the valve’s cavity.
Two configurations are available for DIB ball valves — DIB-1 and DIB-2. The DIB-1 configuration features bi-directional seats upstream and downstream. The DIB-2 ball valve design features one bidirectional (DPE) seat and one uni-directional seat (SPE).
DIB-1 BALL VALVE
DIB-1 ball valves have DPE seats both upstream and downstream to provide a seal in both directions. For the DIB-1 configuration, over-pressurization of the cavity is avoided by the use of an external relief valve. With the ball in the closed position and pressure on the upstream side, the cavity pressure will increase in case of upstream seat failure. The cavity pressure will cause a double piston effect on the downstream seat creating a second seal on the ball.
DIB-2 BALL VALVE
For the DIB-2 configuration, one seat SPE and the other DPE, cavity over-pressurization is internally controlled within the line. If the upstream seat leaks, then there is automatic cavity pressure relief on the upstream side and the downstream seat will provide isolation due to the double piston effect.
Advantages and Disadvantages of DBB/DIB-1/DIB-2
The main advantage of the DBB ball valve is that it has self-relieving seats. However, if the upstream seat leak the downstream seat will not provide isolation. On the other hand, the main benefit of the DIB is that even if the upstream seat leak, the second seat will provide the seal and the valve will not leak. It should be noted that the DIB ball valve should have body cavity relief valves. If we want to combine the positive features of both DIB-1 and DBB valves then we should use the DIB-2 valve that has one SPE seat upstream and a DPE seat downstream. If the upstream seat leak in DIB-2, then the cavity pressure can relieve on the upstream side and the downstream seat will provide isolation due to the double piston effect. It should be noted that the installation of the DIB-2 ball valve is critical and the SPE seat should be on the upstream/pressurized side.
Comparison between DBB/DIB-1/DIB-2 Ball valve Structure;(Only for trunnion ball valve construction)
DBB/DIB-1/DIB-2 Structure difference
No | Structure type | Structure name | Exhaust principle | Product application |
1 | DBB | Single piston effect Double blocking and bleeding and middle cavity discharge | Automatic pressure relief in the middle cavity, pressure into the two sides of the channel | The most frequently used structure at present; |
2 | DIB-1 | Double piston effect Double blocking and double bleeding | Pressure relief can only be achieved through an additional relief valve, pressure does not enter through the sides | Use in specific working conditions or customer requirements; |
3 | DIB-2 | Single/Double piston effect Double blocking and Before valve to discharge | Automatic relief in front of the valve, pressure only into the inlet channel | When used to relieve pressure, the pressure must not go into the downstream condition of the pipeline. Valve with the direction of flow, pay attention to the direction of installation; At present, by a lot of owners more accepted; |
Related Tags :
Ten articles before and after