Pressure Seal Valves
Pressure seal construction is adopted for Valves for high-pressure service, typically in excess of above 170 bar. The unique feature of the pressure seal Bonnet is that the body-Bonnet joint seals improve as the internal pressure in the Valve increases, compared to other constructions where the increase in internal pressure tends to create leaks in the body-Bonnet joint.
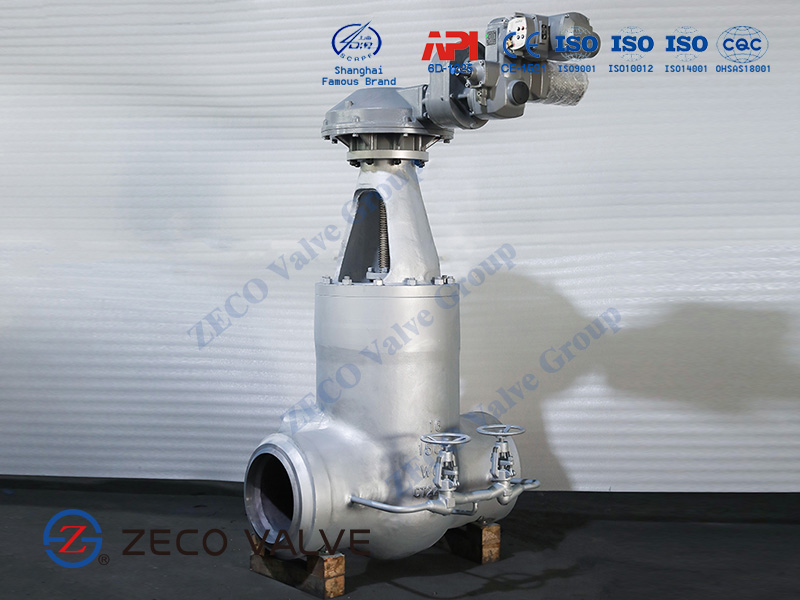
Some other key features of pressure seal valves are as follows:
- No pressure retaining body/bonnet flanges or bolting results in a lighter-weight design compared to the bolted bonnet.
- The differential angle between the bonnet and gasket concentrates the gasket seal force for a better seal at the gasket tip.
- Take-up plate and bolting create initial gasket seal and ensure seal throughout the entire range of working pressures.
- The take-up plate is a separate piece from the yoke arm which allows the removal of the yoke arm without disturbing the pressure seal joint.
- ZECO uses a metal gasket in its standard pressure seal design which is a stronger material with a longer lifetime and lower coefficient of thermal expansion compared to softer gaskets
Pressure Seal Design
Pipeline Valve gate, globe, and check valves are available with pressure seal bonnets in 900 to 2500 class. The pressure seal design is superior to the
bolted design. With the bolted body design, as pressure increases the gasket sealing force reduces, allowing the possibility of a potential leak point.
Whereas with the pressure seal design, increasing fluid pressure increases the gasket sealing force.
The Bonnet bolts affect a seal on the pressure seal joint which forces the bonnet onto the soft metallic gasket which in turn is forced up hard against the outer body. The higher the line pressure, the higher the sealing force against the gasket, further tightening the seal.
The thrust rings are embedded in the body. In smaller forged valves sometimes a ‘breech-lock’ threaded bonnet insert is used instead of a bolt-energized bonnet. Pressure seal bonnets are superior to traditional bolted bonnets and are ideal for high pressures and situations in power plants and refineries where frequent pressure surges, start-ups, and shut-downs occur.
The bonnet gasket is metallic. The gasket is used as its design ensures that pressure acting against it further increases the seal against the surface affecting a self-energized seal. In larger sizes, this gasket is silver plated as silver provides a softer surface to flow the gasket metal into the mating flange surface. Flexible custom-made expanded graphite gaskets are also available. Another superior option for larger sizes is the 316 + Graphite gasket. In very large sizes graphite gaskets can be specified in conjunction with live-loading bonnet bolt washers that can be tightened to ensure a constant force is applied to the bonnet gasket.
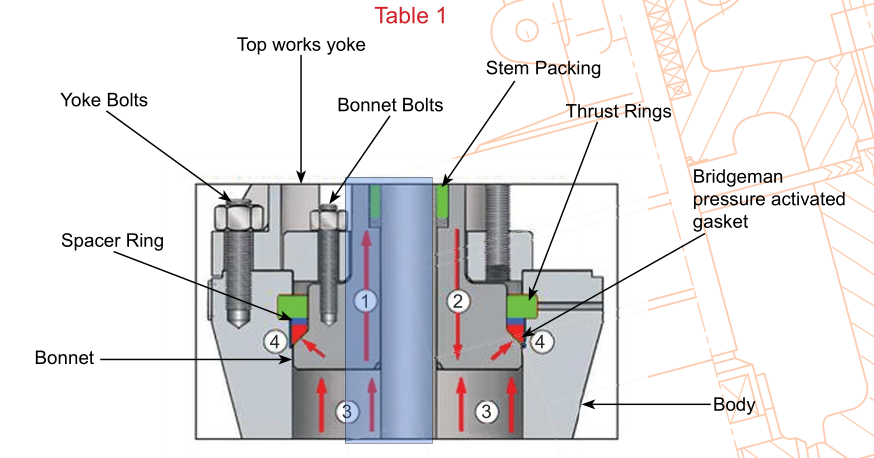
- 1-2 Bonnet tendency to move up or down as pressure changes
- 3 System pressure
- 4 Sealing forces due to pressure
The higher the internal pressure, the greater the sealing force. Easy dismantling is made possible by dropping the Bonnet assembly into the body cavity and driving out the four-segmental thrust rings by means of a push pin.
Relying on fairly simple design principles, pressure seal Valves have proven their capability to handle increasingly demanding fossil and combined-cycle steam isolation applications, as designers continue to push boiler, HRSG, and piping system pressure/temperature envelopes. Pressure seal Valves are typically available in size ranges from 2 inches to 24 inches and ASME B16.34 pressure classes from #600 to #2500, although some manufacturers can accommodate the need for larger diameters and higher ratings for special applications.
Pressure seal Valves are available in many material qualities such as A105 forged and Gr.WCB cast, alloy F22 forged, and Gr.WC9 cast; F11 forged and Gr.WC6 cast, austenitic stainless F316 forged, and Gr.CF8M cast; for over 500°C, F316H forged and suitable austenitic cast grades.
The pressure seal design concept can be traced back to the mid-1900s, when, faced with ever-increasing pressures and temperatures (primarily in power applications), Valve manufacturers began designing alternatives to the traditional bolted-Bonnet approach to sealing the body/Bonnet joint. Along with providing a higher level of pressure boundary sealing integrity, many of the pressure seal Valve designs weighed significantly less than their bolted Bonnet Valve counterparts.
How Does the Pressure Seal Work?
The pressure seal gasket must conform to the ID of the valve body and the clearance between the seal, and the body has to be small. The pressure seal gasket is typically made of malleable iron and then treated with silver to aid in conformance. The structure of the seal consists of a wider top, an angle consisting of 45 degrees or 30 degrees, and a wire-thin toe at the bottom.
The pressure seal gasket is placed just below the keeper ring. With enough force, the metal will move into its correct position and force the toe between the body ID and the bonnet surface. When the system pressure is turned on, the seal becomes a permanent part of the valve until it requires replacement.
The pressure on the gasket in pounds per square inch is enormous. It can be calculated by taking the system pressure times the area of the bonnet, which equals the amount of force generated by the system. For example, for 2,000 pounds per square inch times a 10-inch pipe the load is 157,000 pounds. Considering that the Space Shuttle weighs 292,000 pounds, not much more, in terms of load, would be needed to launch it.
Bolted Bonnets vs Pressure Seals
Bolt Bonnet: The body flange and bonnet flange are joined by studs and nuts, with a gasket of suitable design/material inserted between the flange faces to facilitate sealing.Studs/nuts/bolts are tightened to prescribed torques in a pattern defined by the manufacturer to affect optimal sealing. However, as system pressure increases, the potential for leakage through the body/bonnet joint also increases.
Pressure Seals: Most pressure seal designs incorporate “bonnet take-up bolts” to pull the bonnet up and seal against the pressure seal gasket. This in turn creates a seal between the gasket and the inner(I.D.) of the valve body. A segmented trust ring maintains the load. The beauty of the pressure seal design is that as system pressure builds, so does the load on the bonnet and correspondingly, the pressure seal gasket. Therefore, in pressure seal valves, as system pressure increase, the potential for leakage through the body/bonnet joint decreases.
Related Tags :
Ten articles before and after
Gate Valve Vs Butterfly Valve Comprehensive Compare Guide
How to Measure Butterfly Valves
What is a Double Offset Butterfly Valve
How to Fix a Leaking Butterfly Valve?
valve type – Zeco Valve Company | Professional valve manufacturer
APPLICATIONS – VALVE SEAT/SEAL MATERIALS – Zeco Valve Company | Professional valve manufacturer
MATERIAL SPECIFICATIONS – BALL VALVES – Zeco Valve Company | Professional valve manufacturer
Valve Material Types – Zeco Valve Company | Professional valve manufacturer
COMMON VALVE ABBREVIATIONS – Zeco Valve Company | Professional valve manufacturer