A ball valve is a rotational motion valve that uses a ball-shaped disk to stop or start fluid flow. The ball, shown in Below Figure, performs the same function as the disk in the globe valve.
When the valve handle is turned to open the valve, the ball rotates to a point where the hole through the ball is in line with the valve body inlet and outlet. When the valve is shut, the ball is rotated so that the hole is perpendicular to the flow openings of the valve body and the flow is stopped.
What is Ball Valve?
Most ball valve actuators are of the quick-acting type, which requires a 90° turn of the valve handle to operate the valve. Other ball valve actuators are planetary gear-operated. This type of gearing allows the use of a relatively small handwheel and operating force to operate a fairly large valve.
Some ball valves have been developed with a spherical surface coated plug that is off to one side in the open position and rotates into the flow passage until it blocks the flow path completely.
Seating is accomplished by the eccentric movement of the plug. The valve requires no lubrication and can be used for throttling service.
Ball valves are a type of piping equipment that shuts off or controls the flow in a pipeline by using a hollow sphere and round seats held in a valve body. There are two basic technologies for the design of ball valves, floating ball design and trunnion mounted ball design.
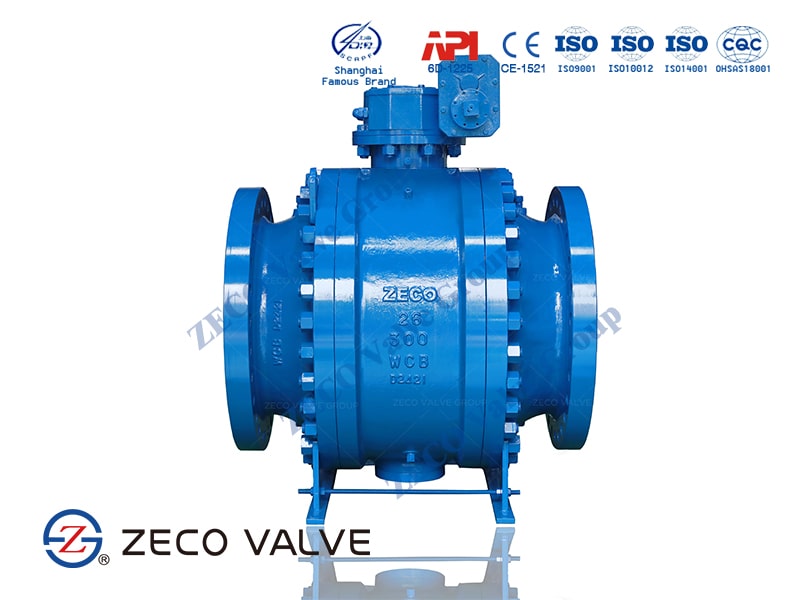
The Major Components of a Ball Valve Include:
Valve body – A pressure vessel that contains the components needed to control or shut off the flow through a pipe. It is designed to connect two or more sections of pipe or tubing to each other.
Ball – A sphere with a flow path (hole or tunnel) through the center of it and a connection point for a shaft to rotate it.
Seats – Round donut-shaped discs that form a seal between the body and ball.
Stem – A shaft that connects the internal ball to the outside of the valve to facilitate rotation of the ball.
Packing – Flexible seals that fit around the shaft and prevent the media traveling through the valve from escaping externally.
Bonnet – The part of the valve body that houses the stem and packing.
Operator or Actuator – An external device designed to rotate the stem of the valve. This can be a lever, a gear, a motor-operated gear (electric actuator), or a pneumatic/hydraulic actuator.
What Types of Ball Valves are Used in Piping?
Ball valves don’t have a complicated mechanism. They are easy to install and simple to use. Their simple design makes them versatile, they can be used in many different industrial applications. There are many types of ball valves depending upon their body construction and function.
Types Based on Body Configuration
Ball valve manufacturers categorize these valves on the basis of their body configuration. There are four types of ball valves based on their construction.
Top Entry Ball Valve
As the name suggests, top entry ball valves allow access to the internal parts of the valve by removing the bonnet cover on the top. These valves can be easily assembled and disassembled. Easy access allows repair and maintenance without having to disengage the ball valve from the pipeline.
End Entry Ball Valve
These ball valves have a single-piece body. The connections on the valve are flanged or screwed. The ball is inserted from one end and is kept in place by a screwed insert. End entry ball valves are usually smaller in size and used for applications requiring less pressure.
Split Ball Valve
In split body ball valves, the body of the valve is divided into two or three pieces that are bolted together like flanges. One part of the body is always larger than the rest and that is what holds the ball. The stuffing box is constructed around the larger body part. Split body ball valves are usually larger in size, though you can find smaller ones as well. They are easy to inspect and maintain.
Welded Ball Valve
In welded body ball valves the bonnet is welded to the body of the valve. This makes the valve safe from any kind of leakages. The valve’s internal parts cannot be accessed or maintained. Welded body valves are suitable for underground applications, submarine pipelines, and regulating the flow of hazardous materials.
Types Based on Ball Movement
Floating Ball Design
A floating design ball valve sandwiches the hollow ball between two or more cupped seats that form a tight seal between the body and the ball at the inlet and outlet ports of the valve body.
The ball is rotated (usually 90 degrees) by a shaft that protrudes outside of the valve body and is connected to some form of operator. For this reason, most ball valves are referred to as quarter-turn valves. This shaft is not rigidly attached to the ball in order for the ball seat to cradle the ball preventing it from moving down in the valve body.
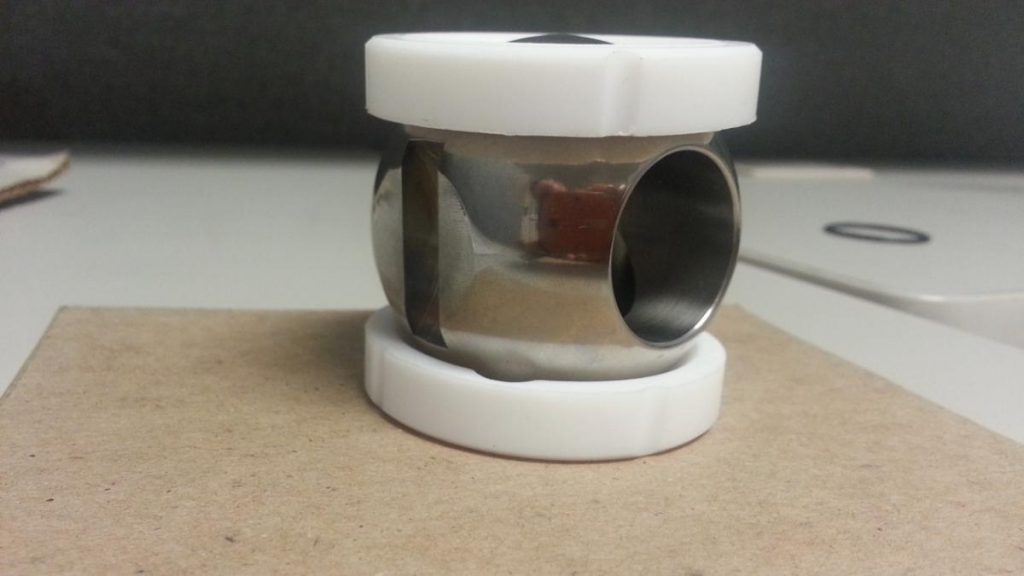
Trunnion Mounted Ball Design
The trunnion design ball valve works nearly the same way as the floating ball except the seats are spring loaded against the ball and the ball does not pivot. The ball only rotates on its axis in this design.
In the trunnion mounted ball valve, the ball utilizes a second shaft and bearing on the bottom of the ball. This stem or “post” holds the bottom of the valve in place. The top of the ball is not slotted and the upper stem is rigidly attached to the ball. This prevents the ball from moving into the downstream seat.
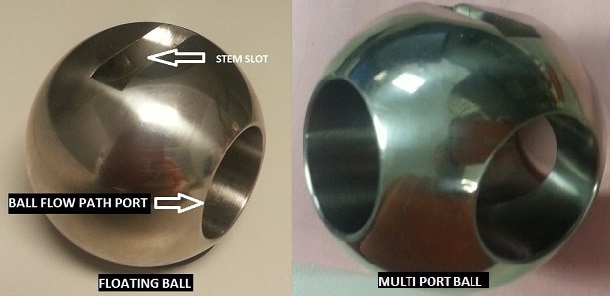
Types Based on Bores
The bore is the internal diameter of the balls used in ball valves. There are three basic types of ball valves based on bores.
Full Port Floating Ball Valve
The full port ball valve is named so because the diameter of the bore in this valve matches the diameter of the connected pipeline. This means there is no restriction to flow through the valve. Full-bore or full-flow ball valves are ideal for situations where pigging may be required. They are used widely in chemical, petrochemical, and refining industries.
Reduced Port Floating Ball Valve
As the name suggests, a reduced port valve has an internal bore diameter that is one or two nominal sizes lower than the internal diameter of the connected pipeline. The flow path is restricted which results in higher energy losses. A reduced port valve is used mostly in the oil and gas industry.
V Port Floating Ball Valve
The v-port ball valve features either a v-shaped ball or a similarly shaped seat. This ball valve is used in applications where the flow velocity needs to be maintained at a certain level. This is why v ball valve is also called a control valve.
Types Based on Number of Pieces
Ball valves can be housed in one, two, or three-piece structures.
One Piece Floating Ball Valve
This is the cheapest ball valve because it features a single piece of housing that is welded or forged to the body of the valve. One-piece ball valves cannot be opened so cleaning, maintenance, or replacement of parts is impossible. This ball valve is suitable for small-scale industrial applications and materials like gases that do not require valve maintenance.
Two Piece Floating Ball Valve
This ball valve is made of two pieces of housing that are threaded together. Two-piece valves can be disassembled for cleaning and maintenance but that requires the valve to be disengaged from the pipeline.
Three Piece Floating Ball Valve
Three-piece ball valve features three different pieces of housing that are bolted together. The valve can be easily cleaned and maintained. The internal parts can also be replaced without disengaging the valve from the pipeline. Three-piece ball valves are more expensive than the other two types of valves in this category.
Valve Materials
Balls are usually metallic in metallic bodies with trim (seats) produced from elastomeric (elastic materials resembling rubber) materials. Plastic construction is also available.
The resilient seats for ball valves are made from various elastomeric materials. The most common seat materials are Teflon (TFE), filled TFE, Nylon, Buna-N, Neoprene, and combinations of these materials.
Because of the elastomeric materials, these valves cannot be used at elevated temperatures. Care must be used in the selection of the seat material to ensure that it is compatible with the materials being handled by the valve.
Ball Valve Stem Design
The stem in a ball valve is not fastened to the ball. It normally has a rectangular portion at the ball end which fits into a slot cut into the ball. The enlargement permits rotation of the ball as the stem is turned.
Blow-out Proof Stem of Ball Valve
Some ball valve stems have a groove cut in the top face of the stem that shows the flow path through the ball. Observation of the groove position indicates the position of the port through the ball. This feature is particularly advantageous on multiport ball valves.
The blow-out proof stem is one of the basic design features of the ball valve.
Ball valve stem is inserted from the valve body inside with an integral T-type shoulder to provide blow-out proof effectively. It is internally inserted as a function of a backseat to assure stem sealing safety.
To describe it in detail, the stem is sealed by o-rings & packing rings and held in position by the stem housing which is bolted to the valve body. The o-rings & packing rings are compressed and held in position by the gland flange, which is bolted to the stem housing. That means when we replace the packing, the blow-out proof stem feature can prevent the stem from being pushed out by the pressure from the valve inside.
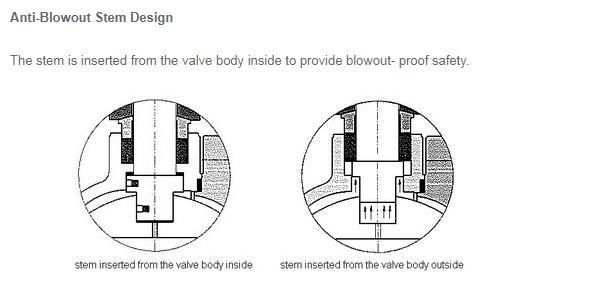
Ball Valve Bonnet Design
A bonnet cap fastens to the body, which holds the stem assembly and ball in place. Adjustment of the bonnet cap permits compression of the packing, which supplies the stem seal.
Packing for ball valve stems is usually in the configuration of die-formed packing rings normally of TFE, TFE-filled, or TFE-impregnated material. Some ball valve stems are sealed by means of O-rings rather than packing.
Ball Valve Position
Some ball valves are equipped with stops that permit only 90° rotation. Others do not have stops and may be rotated 360°. With or without stops, a 90° rotation is all that is required for closing or opening a ball valve.
The handle indicates valve ball position. When the handle lies along the axis of the valve, the valve is open. When the handle lies 90° across the axis of the valve, the valve is closed.
Related Tags :
Ten articles before and after
What affects the sealing performance III
What is anti-static design for ball valve?
What Valves Can Be Used For Throttling? – Zeco Valve
What is the heat treatment of steel | Industrial Valve
What is the difference between 304,304H and 304L?
Industrial Valves: Manufacturing Proces (How Valves are Made) – Zeco
What affects the sealing performance II
What is sealant injection fitting of ball valve?
What affects the valve sealing performance | Industrial Valve